Глава 5. Подбор материалов для узлов трения
Узлы трения обобщенно можно подразделить на сопряже-ния, в которых реализуется сила трения покоя (посадки с натягом, крепежные соединения) и подвижные сопряжения.
При подборе материалов для узлов трения покоя необходи-мо руководствоваться следующими рекомендациями:
- в узле трения должно реализовываться внешнее трение, опреде-ляемое условием:
p ≤ | 0,125 ⋅ HB | − | 6τ | n | 2 | |||
1 | , | (5.1) | ||||||
c | ∆2 |
| HB | |||||
где HB - твердость по Бринеллю менее твердого тела, МПа; ∆ - комплексная характеристика шероховатости;
τn=τ0+β ·HB,
где τ0, β - фрикционные характеристики (табл. 5.1);
pc -контурное давление,МПа,определяемое из зависимости:
p | = | ∆Н | ; | (5.2) | ||||
c | d ⋅c | |||||||
2 | d | |||||||
c = | (1 − k22 )⋅ E | ; | k 2= | 2 | , | |||
d |
где ∆Н -натяг в соединении, м; d -диаметр вала,м;
d2-наружный диаметр ступицы,м;
- для предотвращения заедания поверхностей при разборке со-единения шероховатость более твердой поверхности должна со-ответствовать условию
∆ = 2,7 ⋅ HB2 ⋅θ 2 ⋅ | HB | , | (5.3) |
p | |||
c |
где θ=(1-µ2)/E;
|
|
µ - коэффициент Пуассона;
E - модуль упругости, МПа;
- избегать контурных давлений, соответствующих переходу упру-гопластических деформаций в пластические:
85
p >7,5 ·∆-2 | ·HB5 ·θ4; | (5.4) |
c |
- учитывать возможность схватывания материалов в парах трения: полное схватывание
Al-Cu, Fe-Cu, Pb-Cu, Al-Ag;
частичное схватывание
Al-Fe, Fe-Ti, Al-Ni, Zn-Al, Cu-Ag;
не происходит схватывания
Fe-Pb, Fe-Аg.
Таблица 5.1 | ||||
Фрикционные характеристики материалов | ||||
Материал | τ0, МПа | β | HB, МПа | |
Сталь 40Х | 184 | 0,055 | 3410 | |
Сталь 45 | 204 | 0,044 | 2700 | |
Сталь45 (закалка) | 130 | 0,072 | 3240 | |
БрА10ЖЗМц1,5 | 20 | 0,1 | 1200 | |
Медь | 17 | 0,08 | 850 | |
Алюминий | 15 | 0,116 | 600 | |
Капролон | 2 | 0,06 | 130 | |
Фторопласт-4 | 3,4 | 0,017 | 30 | |
Для подвижных соединений к материалам пар трения предъявляются следующие требования:
- стойкость к задирам;
- хорошая прирабатываемость;
- минимальный коэффициент трения;
- высокая износостойкость;
- недефицитность.
86
Таблица 5.2 Триботехнические и физико-механические свойства антифрикционных материалов
Материал | Рс, | V, | [pv], | f | НВ, | Е, | σт, | Примечания
| ||||||||
МПа | м/с | МН/(м ·с) | МПа | МПа | МПа | |||||||||||
Баббиты | Для работы в условиях жидкост- | |||||||||||||||
ГОСТ 1320-74 | 0,35 ·105 | ной или полужидкостной смазки | ||||||||||||||
Б-16 | 5-10 | 5-50 | 10-50 | 0,006 | 320 | 86 | и в паре с деталью твердостью | |||||||||
Б-83 | 5-10 | 5-50 | 10-50 | 0,005 | 300 | 0,48 ·105 | 82 | HRC>50 | ||||||||
БН | 10 | 15 | 30 | 0,006 | 280 | 0,4 ·105 | 72 | |||||||||
Бронзы | Для работы в условиях полужид- | |||||||||||||||
ГОСТ 613-79 | 0,9 ·105 | костной смазки. Хорошие анти- | ||||||||||||||
Бр05Ц5С5 | 8 | 3 | 12 | 0,009 | 600 | 100 | фрикционные свойства | |||||||||
Бр010Ф1 | 15 | 10 | 7 | 0,008-0,15 | 600-900 | 0,75 ·105 | 100 | |||||||||
ГОСТ 493-79 | 1,12 ·105 | В условиях граничной смазки при | ||||||||||||||
Бр А4Ж4Л | 15 | 4 | 12 | 0,012-0,04 | 980 | 400 | высоких нагрузках и низких ско- | |||||||||
87 | Бр А10Ж4Н4Л | 15 | 4 | 12 | 0,006-0,012 | 1400-1600 | 1,15 ·105 | 600 | ростях скольжения в паре с де-
| |||||||
Бр А9Мц2Л | 20 | 5 | 12 | 0,012 | 800-1000 | 1,2 ·105 | 300 | талью твердостью HRC>50 | ||||||||
ГОСТ 18175-78 | 1,12 ·105 | Используется | как наплавочный | |||||||||||||
Бр КЗМц-1 | 5 | 3 | 7 | 0,015 | 900 | 500 | материал | для | восстановления | |||||||
изношенной поверхности | ||||||||||||||||
Полимеры | Хорошая | износостойкость | при | |||||||||||||
Фторопласт-4 | 1,0 | 0,5 | 0,04 | 0,03-0,1 | 30-60 | 500-600 | 24,0 | частичном | проникновении | абра- | ||||||
ГОСТ 1007-80 | зивной среды. Необходим высо- | |||||||||||||||
Капрон ТУ | 3 | 0,2 | 0,15 | 0,11-0,15 | 80-120 | 1500 | 65 | кий класс | чистоты | обработки | ||||||
6-06-309-70 | сопряженной детали | (8 | класс | |||||||||||||
Капролон В ТУ | 4 | 0,2 | 0,2 | 0,12 | 140-150 | 2000-300 | 70 | чистоты обработки поверхности | ||||||||
6-05-211-950-74 | и выше) | |||||||||||||||
Текстолит Б | (0,02-0,1) ·105
| В условиях работы без смазоч- | ||||||||||||||
ГОСТ 5-78 | 5 | 1 | 2 | 0,2-0,3 | 280 | 50 | ного материала (с.м.) и со сма- | |||||||||
(без с.м.) | 10 | 2 | 4 | 0,05-0,1 | 280 | 50 | зыванием водой | |||||||||
(со с.м.) |
В подвижных соединениях реализуются как прямые, так и обратные пары трения. В прямой паре деталь с большей по-верхностью трения имеет и большую твердость. В обратной паре деталь с большей поверхностью трения имеет меньшую твер-дость. Более износостойкой является прямая пара трения.
Менее твердое тело должно изготавливаться из антифрик-ционных материалов.
При невозможности использования в узле трения смазоч-ного материала или при недостаточном его количестве необхо-димо использовать антифрикционные материалы с низкими зна-чениями фрикционных характеристик τ0 и β.
Но, как правило, такие материалы обладают низкими проч-ностными свойствами и при их деформации возрастают потери энергии на трение, что ведет к интенсивному нагреванию по-верхностных слоев. Разогрев поверхностных слоев вызывает их размягчение, что ведет к росту силы трения и увеличению ин-тенсивности изнашивания. Поэтому такие материалы (например, фторопласт-4) используют в виде тонких покрытий или наполни-телей.
Триботехнические и физико-механические свойства наи-более широко используемых антифрикционных материалов при-ведены в табл. 5.2.
Из металлических антифрикционных материалов наи-большее распространение в подшипниках скольжения получили баббиты и бронзы.
Баббиты используют в подшипниках скольжения, рабо-тающих в режиме жидкостной смазки.
В узлах трения, работающих при небольших окружных ско-ростях и высоких нагрузках, используют бронзы.
Твердость валов, контактирующих с бронзовыми вклады-шами, должна быть не ниже HRC 50.
Глава 6. Виды изнашивания
6.1. Характеристики нагруженности узла трения
Основным фактором, определяющим срок службы узла трения, является интенсивность изнашивания.
Факторы, влияющие на ее величину, рассмотрены в гл. 3. Одними из важнейших внешних факторов являются контурное давление на контакте и скорость смещения трущихся поверхно-стей.
88
В дальнейшем, рассматривая способы повышения износо-стойкости при различных видах изнашивания, будут использо-ваться термины "низкая" и "высокая" нагрузки, "малые" и "боль-шие" скорости скольжения.
К низким нагрузкам будем относить нагрузки, под воздей-ствием которых в паре трения реализуется упругий или упруго-пластический контакт, к высоким нагрузкам – когда реализуется пластический контакт.
Условиями реализации различных видов контакта являются следующие неравенства:
Ненасыщенный упругий контакт (ННУК) | |
p <5 , 4⋅∆−2⋅ HB5⋅θ 4 . | (6.1) |
c | |
Упругопластический контакт (УПК) | |
5 , 4 ⋅∆− 2 ⋅ HB5 ⋅θ 4 < pc <14,5 ⋅∆−2 ⋅ HB5 ⋅θ . | (6.2) |
Ненасыщенный пластический контакт (ННПК) | |
14,5 ⋅∆−2 ⋅ HB5 ⋅θ 4 < pc < 0,06 ⋅ HB . | (6.3) |
Насыщенный пластический контакт (НПК) | |
0,06 HB < pc < 0,32HB , | (6.4) |
где pc - контурное давление, МПа;
∆ -комплексная характеристика шероховатости для болеетвердого из контактирующих тел (таб.4.2, 4.3);
1 − µ2 | -1 | |
θ = E | - упругая постоянная, МПа ; | |
Е – модуль упругости менее твердого тела, МПа; HB – твердость менее твердого тела, МПа.
Величина контурного давления pc для различных соедине-ний может быть найдена из следующих зависимостей.
Шариковый подшипник качения: | |||||||||
N | 13 | ||||||||
p | = 0 , 578 |
| . | (6.5) | |||||
2 | |||||||||
c | ⋅ r | 2 | |||||||
θΣ |
Роликовый подшипник качения:
89
pc =0,564 | N | 0 ,5 | , | (6.6) | ||||
|
| |||||||
θ Σ | ||||||||
⋅ r ⋅l |
где N - нагрузки, МН;
θΣ = θ1+θ2;
θ1−θ2-упругие постоянные контактирующих тел,МПа-1;
r – радиус шара, цилиндра, м;
l – длина контакта вдоль продольной оси цилиндра, м.
Посадки с натягом: | |||||||||||||
∆ | H | 1 + K 2 | ⋅ E−1 , | ||||||||||
p | c | = | ; | C = | 1 | + | 2 |
| (6.7) | ||||
d | ⋅c | 2 | |||||||||||
1 − K2 |
где ∆H - величина натяга, м; d – диаметр вала, м.
K2 = dd2 ; d2–диаметр ступицы насаженной детали,м.
Плоские поверхности:
1,5 | ||||||||||||
0,42 |
| H |
| |||||||||
B | 3+δ | δ | ||||||||||
|
| 3+δ | ||||||||||
pc = K | 2R ⋅θ | ⋅ pa | , , | (6.8) | ||||||||
2 | ||||||||||||
B | Σ |
|
где pa - номинальное давление, МПа;
HB, RB –высота и радиус волны волнистой поверхности,мкм
(табл. 6.1);
K, δ -коэффициенты(табл. 6.2).
Таблица 6.1 | |||
Ориентировочные значения параметров волнистости | |||
Метод | Rа, | HB , | RB , |
обработки | мкм | мкм | мкм |
Круглое шлифование | 1,25 … 0,16 | 0,8 … 3 | 20 … 160 |
Плоское шлифование | 5,0 … 0,16 | 1,2 … 12 | 25 … 90 |
Растачивание | 5,0 … 0,32 | 2 … 3,5 | 25 … 100 |
Полирование | 0,63 … 0,08 | 0,3 … 1,5 | 20 … 160 |
90
Таблица 6.2
Значения коэффициентов К и δ
Деформа- | 1 | Коэф- | Rmax | H B | |||||||
ция |
| фици- | |||||||||
θΣ HB | |||||||||||
0,1 | 0,2 | 0,4 | 0,8 | 1,6 | 3,2 | ||||||
выступов | ент | ||||||||||
50 | К | 1,05 | 1,1 | 1,2 | 1,35 | 1,55 | 2,1 | ||||
Пластиче- | δ | 0,6 | 0,7 | 0,85 | 1,15 | 1,5 | 2,3 | ||||
100 | К | 1,1 | 1,17 | 1,28 | 1,43 | 1,75 | 2,6 | ||||
ская | δ | 0,65 | 0,8 | 1,0 | 1,3 | 1,65 | 2,0 | ||||
200 | К | 1,13 | 1,2 | 1,35 | 1,55 | 2,1 | 3,5 | ||||
δ | 0,7 | 0,85 | 1,1 | 1,5 | 2,35 | 2,0 | |||||
Упругая | - | К | 1,05 | 1,06 | 1,14 | 1,25 | 1,5 | 2,1 | |||
δ | 0,65 | 0,8 | 1,05 | 1,4 | 1,95 | 2,4 |
Шлицевое соединение (зубчатые муфты):
pc = 0,75 | E ⋅ϕ ⋅l | ; | (6.9) | |
H | ||||
где ϕ - угол перекоса соединяемых валов; Н –высота контакта зубьев,м;
l –длина сопряжения,м.
Зубчатые зацепления:
Для зубчатых зацеплений контурные давления можно оп-ределять по зависимостям (8.10)-(8.12).
Критерии «больших» и «малых» скоростей
Критерием больших скоростей является соотношение, м/с: V > 4 ·a/r;
критерием малых скоростей - соотношение
V < 4a/25r,
где a - коэффициент температуропроводности, м2/с;
а=0,11*10 - 4 - для стали; а=1,15*10 - 4 - для меди;
а=0,6*10 - 4 - для бронзы;
r - радиус микронеровностей, м.
91
Таблица 6.3
Ориентировочные значения малых и больших скоростей для пар трения сталь-бронза, сталь-сталь
Пара | Способ обработки | |||||||||||
тре- | Скорость, | Точение, шлифование | Полирование | |||||||||
ния | м/с |
| ||||||||||
Шероховатость Ra, | мкм | |||||||||||
1,25…2,5 | 0,63…,25 | 0,32…0,63 | 0,32…0,63 | 0,16…0,32 | 0,08…0,16 | |||||||
Сталь-бронза | Малая | 0,5 | 0,27 | 0,18 | 0,04 | 0,02 | 0,015 | |||||
Большая | 12 | 6,8 | 4,4 | 1,0 | 0,5 | 0,36 | ||||||
-сталь | Малая | 0,09 | 0,05 | 0,033 | 0,007 | 0,004 | 0,003 | |||||
Сталь | Большая | 2,2 | 1,25 | 0,8 | 0,18 | 0,09 | 0,07 | |||||
6.2. Адгезионное изнашивание
Характерно для высоконагруженных сопряжений при раз-рушении смазочного слоя и сопровождается схватыванием тру-щихся поверхностей. При скоростях скольжения 2,5 ·10-3... 0,5 м/с, высоких контактных нагрузках и вибрациях наблюдается схватывание I рода, сопровождающееся образованием на по-верхностях трения углублений и наростов со значительным из-менением шероховатости. При скоростях 1...5 м/с и малых на-грузках развивается процесс схватывания II рода. В этом случае поверхность становится грубошероховатой с отчетливыми сле-дами течения и размазывания материала.
Для предотвращения схватывания применяют:
- поверхностное пластическое деформирование (ППД);
- поверхностную закалку;
- сульфидирование;
- введение в смазочный материал присадок, содержащих
S, Cl, P.
92
6.3. Абразивное изнашивание
Возникает при давлении абразивных частиц (подвижных и неподвижно закрепленных) на материал под воздействием внешних сил и характеризуется высокой интенсивностью изна-шивания.
При абразивном изнашивании неподвижно закрепленными абразивными частицами износостойкость узла трения зависит от соотношения твердостей абразива Hа и металла Нм.
Если Нм<(0,8...0,6)Hа, то износ не зависит от разности твер-достей абразива и металла.
Если Нм=(0,8...1,5)Hа, износостойкость возрастает с ростом твердости металла.
Износостойкость существенно повышается при Нм>=1,6Hа. При наличии свободных абразивных частиц износостой-
кость И пропорциональна разности твердостей трущихся тел И=K ·(H1-H2).
Следовательно, для повышения износостойкости узлов трения в условиях абразивного изнашивания необходимо приме-нение сталей, подвергнутых упрочняющей технологии (табл. 4.4, ч.II), и высокотвердых сплавов (табл. 6.4).
6.4. Окислительное изнашивание
Протекает при нормальных и повышенных температурах при трении без смазочного материала или недостаточном его количестве в диапазоне скоростей скольжения 0,5...1 м/с.
Повышение износостойкости достигается созданием по-верхностей трения с высокой твердостью.
Способы повышения твердости:
- процессы ППД (для низкоуглеродистых сталей);
- цементация (для малоуглеродистых сталей - сталь 20ХГС, сталь 40, сталь 45 и др.);
- азотирование (для нержавеющих марок сталей);
- хромирование (для средне- и высокоуглеродистых ста-
лей);
- нитроцементация (для углеродистых сталей в условиях интенсивного изнашивания);
- электромеханическая обработка (для сталей с содержа-нием углерода менее 0,7%);
93
- закалка ТВЧ (для сталей, содержащих углерода не менее
0,6%);
- металлизация (при работе узла трения со смазочным ма-териалом).
Таблица 6.4
Износостойкая наплавка.
Марка | Наплавленный | Твердость | Примечание | |||
металл | HRC | |||||
ЭЛЕКТРОДЫ | ДЛЯ РУЧНОЙ ДУГОВОЙ НАПЛАВКИ по ГОСТ 10051-75 | |||||
| ||||||
У340П/Б | Э-10Г3 | 28...35 | Наплавка | деталей, | ||
О3Н-400У | Э-15Г5 | 40...44 | испытывающих | кон- | ||
НР-70 | Э-30Г2ХМ | 31...41 | тактные (ударные) на- | |||
грузки: оси, валы, | ||||||
рельсовые крестовины | ||||||
и др. | ||||||
ОМГ-Н | Э-65Х11Н3 | 25...33 | Наплавка | деталей из | ||
стали Г13Л (Гатфиль- | ||||||
12АН/ЛИВТ | 25...32 | да) | ||||
Э-95Х7Г5С | Наплавка | деталей, | ||||
ТКЗ-Н | Э-30Х5В2Г2СМ | 50...60 | испытывающих интен- | |||
сивные | ударные | на- | ||||
грузки с | абразивным | |||||
изнашиванием. | ||||||
Наплавка | деталей, | |||||
Т-620 | Э-320Х23С2ГТР | 55...62 | подверженных | абра- | ||
Т-590 | Э-320Х25С2ГР | 57...63 | зивному изнашиванию | |||
Наплавка | деталей, | |||||
испытывающих | абра- | |||||
ЦС-1 | Э-300Х28Н4С4 | 48...54 | зивное изнашивание с | |||
ВСН-6 | 175Б6Х6СТ | 52...57 | ударными нагрузками | |||
НАПЛАВОЧНАЯ ПРОВОЛОКА по ГОСТ10543-82
Нn-40Х3Г2МФ | 38...44 | |||
Нn-50ХФА | 43...50 | |||
Нn-40Х13 | 45...52 | |||
НВ(МПа) | ||||
Нn-30 | 1600...2200 | Наплавка | деталей, | |
Нn-40 | 1600...2200 | подверженных абра- | ||
Нn-50 | 1800...2400 | зивному изнашиванию: | ||
Нn-80 | 2600...3400 | оси, шпиндели, колеса, | ||
Нn-50Г | 2000...2700 | опорные катки, ролики |
94
Нn-65Г | 2300...3100 | ||||||||
Нn-30ХГСА | 2200...3000 | ||||||||
Продолжение табл. 6.4 | |||||||||
Марка | Наплавленный | Твердость | Примечание | ||||||
металл | НВ(МПа) | ||||||||
Нn-Х15Н60 | 2000...2200 | Наплавка деталей, ра- | |||||||
Нn-Х20Н80 | 2000...2200 | ботающих при высокой | |||||||
температуре | с интен- | ||||||||
сивным окислением | |||||||||
Проволока | порошковая | наплавочная по ГОСТ 26101-84 | |||||||
ПП-Нn-30Х5Г2СМ-Т(D)-C(У)-2,5 | 50...56HRC | Наплавка | деталей об- | ||||||
ПП-Нn-30Х4Г2М-Т-С(Ф)-2,0 | 42...48HRC | щего назначения | |||||||
НВ(МПа) | |||||||||
ПП-Нn-14СТ-Т-С-3,0 | 2400...2600 | ||||||||
ПП-Нn-19СТ-Т-С-3,0 | 3000...3400 | ||||||||
ПП-Нn-50Х3СТ-Т-С-3,0 | 4600...5100 | ||||||||
ПП-Нn-18Х1Г1М-Т-Ф-3,5 | 3200...3800 | ||||||||
ПОРОШКОВЫЕ ЛЕНТЫ | |||||||||
Пл-АН101 | 300Х25Н3С3 | 50...55HRC | Конуса и чаши засып- | ||||||
Пл-АН102 | 250Х20С3Р3 | 52...56HRC | ных аппаратов домен- | ||||||
Пл-АН111 | Никель- | 48...55HRC | ных печей, | броневые | |||||
Карбидхрома | плиты | ||||||||
Пл-АН126 | 20Х2Г2МТ | 33...45HRC | Детали общего назна- | ||||||
чения | |||||||||
Спеченные ленты по ГОСТ 22366-77 | |||||||||
ЛС-100Х7Р1 | 54...58HRC | Детали, | испытываю- | ||||||
щие интенсивное абра- | |||||||||
зивное изнашивание | |||||||||
ЛС-10Х14М3 | 46...50HRC | Плунжеры | гидропро- | ||||||
цессов, крановые ко- | |||||||||
ЛС-20Х10Г10Т | 38...42HRC | лёса | |||||||
|
|
| |||||||
Порошки для наплавки ГОСТ 21448-75 | |||||||||
ПГ-С27 | Для наплавки деталей, | ||||||||
400Х28Н2С2ВМ | >53HRC | работающих в услови- | |||||||
ях абразивного изна- | |||||||||
шивания при темпера- | |||||||||
туре до 500°C. | |||||||||
ПГ-С1 | >51HRC | Для наплавки деталей, | |||||||
подвергающихся абра- | |||||||||
300Х28Н4С4 | зивному | (газоабразив- | |||||||
ПГ-УС25 | >55HRC | ному) изнашиванию |
95
500Х38Н
Окончание табл.6.4
Марка | Наплавленный | Твердость | Примечание | ||||
металл | |||||||
Прутки для наплавки ГОСТ21448 -75 | |||||||
Пр-С27 | 52HRC | Для | наплавки дета- | ||||
450Х28Н2СВМ | лей, | испытывающих | |||||
абразивное | изнаши- | ||||||
вание с умеренными | |||||||
ударами | при | темпе- | |||||
ратуре до 500°C. | |||||||
Пр-С1 | То же при нормаль- | ||||||
50HRC | ной температуре | ||||||
300Х28Н4С3 | То же со значитель- | ||||||
Пр-С2 | 44HRC | ными | ударными на- | ||||
200Х17Н2 | грузками | ||||||
Пр-В3К | 40HRC | Для | наплавки дета- | ||||
лей, | испытывающих | ||||||
100Х29К63В5 | абразивное | изнаши- | |||||
вание при нагреве до | |||||||
750°С, | воздействии | ||||||
агрессивных | сред и | ||||||
ударных нагрузок |
6.5. Усталостное изнашивание
Проявляется при качении в виде местных очагов разруше-ния (питтинг) и в отделении микрообъемов поверхности при тре-нии скольжения за счет усталости поверхностных слоев.
На усталостную прочность σ, характеризующуюся количе-ством циклов нагружения, существенное влияние оказывает удельная нагрузка на контакте p, связанные соотношением из
теории подобия
p3σ=idem,
где idem – условие подобия модели и натуры.
То есть незначительное повышение нагрузки ведет к сни-жению количества циклов нагружения, при котором происходит разрушение поверхности.
Повышение износостойкости в условиях усталостного из-нашивания достигается снижением удельной нагрузки на контак-те, выбором материала с повышенным сопротивлением устало-
96
сти, повышением класса чистоты обработки, применением жид-ких смазочных материалов с высоким классом чистоты.
6.6. Фреттинг-коррозия
Этот вид изнашивания проявляется в соединениях ( под-вижных и неподвижных) при колебаниях контактирующих по-верхностей с малыми амплитудами 0,025...2,5 мм. Наиболее ин-тенсивное изнашивание соответствует амплитудам в пределах 0,1...0,15 мм. Распространен на посадочных поверхностях полу-муфт, зубчатых колес, подшипников качения, в деталях криво-шипно-шатунных механизмов.
На интенсивность процесса изнашивания существенное влияние оказывает количество циклов нагружения.
Характерным признаком процесса фреттинг-коррозии в подвижных соединениях является наличие темных полос по гра-ницам сопряжения. В соединениях с натягом в месте контакта появляются продукты окисления от светло-красно-коричневого до темно-коричневого цвета.
Повреждения поверхностей вследствие фреттинг-коррозии служат концентраторами напряжений и снижают предел вынос-ливости. В случае усталостного разрушения на фреттинг-коррозию как первопричину указывает характерный язычок ме-талла.
Предотвратить или замедлить развитие процесса фрет-тинг-коррозии возможно путем:
- нанесения на поверхность контакта слоя меди, кадмия, ПТФЭ (политетрофторэтилен);
- повышения твердости одной из деталей;
- увеличения натяга соединения;
- увеличения шероховатости поверхности, если устраняет-ся проскальзывание;
- фосфатирования поверхности и покрытия ее парафином;
- покрытия поверхности свинцовыми белилами или их сме-сью с MoS2;
- смазывания контактирующих поверхностей маслами с
противоизносными присадками.
6.7. Избирательный перенос
Избирательный перенос (ИП) - это процесс, заключающий-ся в формировании при трении на трущихся поверхностях так называемой сервовитной пленки. Сервовитная пленка, как пра-
97
вило, формируется из бронзы или медьсодержащих химических соединений и представляет собой очень активную медную плен-ку толщиной 1…2 мкм , свободную от окисных пленок. Сервовит-ная пленка покрывает трущиеся поверхности обоих контактируе-мых тел (рис. 6.1).
V 1
2
3
Рис. 6.1. Избирательный перенос:
1 - металлополимерный слой; 2 - сервовитная пленка меди; 3 - сталь
Одновременно с формированием сервовитной пленки об-разуются полимеры трения, дополнительно разделяющие пары трения, поверхностно-активные вещества (ПАВ), выделяется свободный водород, восстанавливающий окисные пленки на медном сплаве и стали. Это положительные факторы, стабили-зирующие эффект безизносности .
Но при повышении температуры более 65°С интенсифици-руется выделение водорода и насыщения им поверхности стали. Поверхность стали в виде порошка переходит на поверхность бронзы. Режим избирательного переноса переходит в режим во-дородного изнашивания.
Наибольшая вероятность реализации ИП в парах трения сталь-бронза при наличии смазочного материала с ПАВ (напри-мер, ЦИАТИМ-201, ЛКС-металлургическая, АМ-10 и др.) или сталь-сталь с использованием смазочных материалов, вклю-чающих медьсодержащие порошки или химические соединения. Порошки вводятся в количестве 10% от объема. А использова-ние в качестве присадки до 3% серно-кислой меди обеспечивает работу пары сталь -сталь с такими же триботехническими харак-теристиками, как и пары трения сталь-бронза.
Наиболее стабилен процесс ИП с циклическим знакопере-менным изменением направления смещения контактирующих поверхностей:
98
- со скоростью скольжения в пределах υmax >υск >10−2 м/с (υ max - максимальная величина скорости скольжения, огра-ниченна температурными свойствами смазочного материала);
- имеющих шероховатость более твердой детали в пределах
0.3…0.63 Ra;
- работающих при удельных нагрузках более 20 МПа;
- со смазочными материалами, содержащими ПАВ (динатрие-вая соль этилдиаминтетрауксусной кислоты, олеиновая ки-слота, сульфополиамидные производные) в количестве 0.5…3% от массы смазочного материала.
Дата добавления: 2018-05-12; просмотров: 1900; Мы поможем в написании вашей работы! |
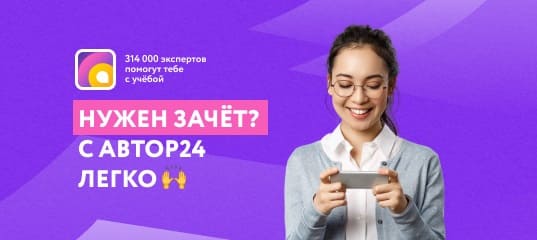
Мы поможем в написании ваших работ!