Раздел 2. Повышение надежности
Глава 1. Пути повышения безотказности
Обеспечение работоспособности машин в межремонтный период - одна из важнейших задач ремонтного и эксплуатационно-го персонала.
Знание положений теории надежности позволяет находить пути решения этой задачи.
Как было установлено ранее наработки металлургических машин могут быть описаны экспоненциальным, нормальным, Вей-булла распределениями и соответственно определены показатели безотказности. Как известно, вероятность безотказной работы в момент t окончания межремонтного периода может быть найдена из следующих зависимостей для:
экспоненциального распределения
P(t)=e-λt ; | (1.1) |
нормального распределения | |
P(t)=0,5-Φ((t-µ)/σ); | (1.2) |
распределения Вейбулла | |
P(t)=exp(-t/a)b; a=µ*Γ(1+1/b). | (1.3) |
73
Анализ данных зависимостей показывает, что повышение вероятности безотказной работы достигается сокращением вре-мени t межремонтного периода.
Этот путь повышения безотказности ведет к сокращению расходов на аварийные восстановления за счет снижения числа отказов и возрастанию затрат на плановые восстановления рабо-тоспособного состояния в связи с их увеличением.
Повышение безотказности за счет сокращения времени межремонтного периода требует экономического обоснования.
Снижение затрат на аварийные восстановления и повыше-ние расходов на плановые восстановления при уменьшении меж-ремонтного периода предполагает существование оптимального межремонтного периода, которому будет соответствовать мини-мум затрат и, следовательно, этот путь имеет ограничение. Мето-дика определения оптимального межремонтного периода рассмот-рена в ч. 2, гл.3. Другой путь повышения безотказности связан с параметрами распределений λ, µ, характеризующимися средней наработкой, и σ, b, характеризующимися среднеквадратичным от-клонением от средней наработки.
|
|
В этом случае повышение безотказности достигается за счет увеличения средней наработки и снижения величины среднеквад-ратичного отклонения.
Повышение средней наработки объекта является непростой технической задачей , для решения которой необходимо устано-вить причину отказов и выработать пути их устранения.
Для установления причин отказов необходимо:
- проанализировать характер нагружения и кинематику уз-лов, в которых происходят отказы;
- проанализировать влияние внешних факторов окружающей
среды;
- проанализировать соблюдение эксплуатационным и ре-монтным персоналом правил технической эксплуатации (ПТЭ) оборудования;
- установить вид повреждения;
|
|
- изучить физику отказов.
При установлении причины отказа оборудования важную информацию несет характер повреждения детали.
Повышение средней наработки при установленной причине отказа основывается на конструктивных решениях, повышении прочностных характеристик материала, повышения износостойко-сти узлов трения, организационных мероприятиях.
Мероприятия по снижению величины среднеквадратичного отклонения связаны, в основном, с соблюдением технологического
74
процесса производства деталей и материала для них, с ужесточе-нием допусков в процессе их производства , с соблюдением ПТЭ оборудования и технологии ремонта машин.
Такими мероприятиями являются повышение квалификации эксплуатационного и ремонтного персонала и ужесточение требо-ваний за соблюдением технологической дисциплины на всех опе-рациях процесса изготовления и эксплуатации машин.
Наиболее приемлемыми уровнями вероятности безотказной работы в межремонтный период с учетом экономической целесо-образности являются для:
- машин P(t)=0,8...0,9;
- механизмов (узлов) P(t)=0,85...0,95;
- деталей P(t)=0,9...0,99.
Для металлургических машин межремонтный период узлов и деталей должен быть кратным межремонтному периоду машины.
|
|
Глава 2. Повреждения деталей металлургических машин
Повреждения деталей металлургических машин являются неотъемлемой частью процесса эксплуатации как следствие раз-вития процессов старения и нарушений правил технической экс-плуатации оборудования.
Повреждения деталей машин по характеру воздействий, приводящих к отказу оборудования, подразделяют на:
- механические (остаточная деформация, вязкий излом, хрупкий излом, усталостное выкрашивание);
- термические (терморазупрочнение, термическая уста-
лость);
- коррозионные (коррозия, коррозионная усталость, коррози-онное растрескивание);
- эрозионные;
- кавитационные;
- износовые (изнашивание - адгезионное, абразивное, уста-лостное, окислительное, водородное, коррозионно-механическое, фреттинг-коррозия)
2.1. Механические повреждения
75
Механические повреждения возникают под воздействием внешней нагрузки и проявляются в виде:
- остаточной деформации (изгиб, скручивание, смятие);
- вязкого излома;
- хрупкого излома;
- усталостного выкрашивания.
Остаточная деформация есть следствие перегрузок, дли-тельного действия переменных контактных, растягивающих или сжимающих напряжений, повышенных температур.
|
|
Устраняется:
- обучением эксплуатационного персонала и повышением требований за соблюдением правил технической эксплуатации (ПТЭ) оборудования;
- заменой на материал с повышенными механическими ха-рактеристиками;
- повышением твердости поверхностного слоя;
- изменением конструкции узла.
Вязкий излом возникает под воздействием нагрузок, превы-шающих допустимые значения и являющихся следствием наруше-ния ПТЭ. Характерным признаком вязкого излома является нали-чие участка текучести в месте излома.
Устраняется такими же мерами, как и в случае остаточной деформации.
Хрупкий излом является следствием значительных ударных нагрузок, длительного воздействия знакопеременной нагрузки, низкого качества материала с повышенным содержанием P, S, H, некачественной термообработки, наличия концентраторов напря-жений. Характерным признаком хрупкого излома является кри-сталлическая структура места излома и сглаженная поверхность мест зарождения усталостной трещины.
Устраняется:
- заменой на материал с повышенной ударной вязкостью;
- недопущением концентраторов напряжений на поверхности детали;
- изменением конструкции узла;
- предотвращением появления повышенных зазоров в линии привода, приводящих к появлению повышенных динамических на-грузок.
Усталостное выкрашивание(питтинг) проявляется при вы-соких контактных нагрузках и пониженной контактной прочности материала.
Устраняется:
76
- повышением механических характеристик материала с од-новременным повышением поверхностной твердости;
- повышением класса чистоты обработки поверхности.
2.2. Термические повреждения
Наиболее распространенным видом термических поврежде-ний металлургических машин является термическая усталость как следствие одновременно действующих механических нагрузок и циклических, с большим перепадом (до 8000С и более) темпера-тур. Этому виду повреждения подвержены рабочие валки и ролики рольгангов станов горячей прокатки, ролики МНЛЗ, хоботы зава-лочных машин и др. Характерным признаком повреждения являет-ся так называемая "сетка разгара".
Повышенным сопротивлением термической усталости обла-дают следующие марки стали - сталь 60С2, сталь 30ХГСА, сталь Х18Н9Т (закалка с высоким отпуском).
2.3. Коррозионные повреждения
Коррозия металлов и сплавов представляет процесс разру-шения стали вследствие химического или электрохимического воздействия внешней среды.
По характеру воздействия внешней среды различают атмо-сферную, газовую и электрохимическую коррозию.
Атмосферная коррозия возникает при влажности среды бо-лее 70% за счет конденсации влаги и взаимодействия с кислоро-дом воздуха.
Устраняется:
- заменой материала с повышенными антикоррозийными свойствами;
- пассивацией поверхности;
- применением защитных покрытий.
Газовая коррозия возникает при температурах 300-6000С. При температуре выше 6000С наблюдается скачок в окалинообра-зовании.
Предотвращается заменой материала с повышенной окали-ностойкостью и применением защитных покрытий.
Электрохимическая коррозия развивается в водной среде с растворенным кислородом за счет электрохимических процессов, связанных с неоднородностью металла, в трещинах, в щелях меж-ду металлами. При наличии бактерий, восстанавливающих серно-
77
кислые соли, коррозия возможна при отсутствии кислорода. При-мером может служить контакт стали с деревом из дуба, каштана.
Устраняется:
- ограничением или предотвращением доступа кислорода к поверхности металла;
- применением однородных материалов;
- устранением условий возникновения электрохимических процессов.
Коррозионное растрескивание возникает под действием ста-тических нагрузок и весьма агрессивной (по отношению к данному металлу) коррозионной среды.
Большая опасность коррозионного растрескивания состоит в том, что при отсутствии видимых повреждений на поверхности мо-жет произойти внезапное разрушение детали, находящейся под нагрузкой, не превышающей допустимые значения. Коррозионное растрескивание является следствием пониженной коррозионной стойкости границ зерен и их наводораживанием, сопровождаю-щимся развитием значительных давлений по границам зерен. Это ведет к снижению межкристаллитной прочности и последующему разрушению детали.
Устраняется заменой материала и исключением возможно-сти наводораживания.
Коррозионная усталость представляет процесс разрушения металлов при одновременном действии коррозионной среды и циклических напряжений. Основными факторами, вызывающими коррозионную усталость, являются активность коррозионной сре-ды, уровень действующих циклических напряжений, число циклов нагружения в единицу времени, прочность и коррозионная стой-кость сплава.
Предотвращается защитой деталей от коррозионной среды
и применением низколегированных марок сталей.
2.4. Эрозионные повреждения
Эрозионные повреждения возникают при действии на ме-талл с большой скоростью потоков жидкости или газа.
Интенсивность разрушения поверхности возрастает с повы-шением температуры потока и его запыленности.
Устраняются:
- повышением сопротивления металла окислению в данной среде;
- повышением поверхностной твердости;
- наплавкой твердосплавных материалов (табл.6.1 гл.6).
78
2.5. Кавитационные повреждения
Кавитационные повреждения на поверхности металла воз-никают под воздействием гидравлических ударов. Гидравлические удары есть следствие образования в жидкости каверн (при пони-жении давления в потоке жидкости) и последующего их схлопыва-ния или разрыва. Кавитационные повреждения интенсифицируют процесс коррозии и наоборот.
Интенсивность кавитационных повреждений можно снизить:
- введением веществ, снижающих поверхностное натяжение;
- применением углеродистых сталей с повышенным содер-жанием углерода (до 0,8%);
- применением никель- и хромсодержащих сталей (напри-мер, 38ХМЮА);
- применением низколегированного чугуна с шаровидным графитом;
- применением упрочняющей технологии (процессов пласти-ческого деформирования - ППД, закалка ТВЧ, азотирование, це-ментация);
- наплавкой и металлизацией высокотвердыми материалами;
- применением высокоэластичных материалов;
- повышением давления в зоне кавитации.
Дата добавления: 2018-05-12; просмотров: 355; Мы поможем в написании вашей работы! |
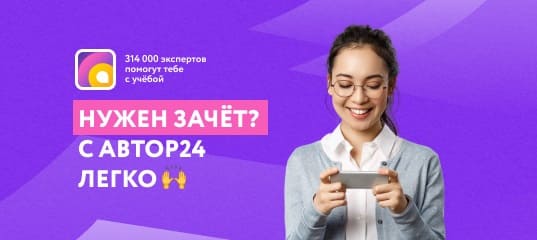
Мы поможем в написании ваших работ!