Глава 7. Ремонтопригодность машин
Затраты на поддержание оборудования в работоспособном состоянии во многом зависят от его надежности, одним из свойств которой является ремонтопригодность.
Ремонтопригодностью определяется свойство машин, кото-рое способствует предупреждению и обнаружению причин возник-
60
новения отказов, восстановлению работоспособного состояния путем проведения технического обслуживания и ремонтов.
Ремонтопригодность, как свойство машины, закладывается при конструировании. Уже на стадии конструирования в машину должны быть заложены возможности по предупреждению и обна-ружению отказов (системы технической диагностики, системы кон-троля параметров, определяющих работоспособность оборудова-ния), а также обеспечена возможность минимальных затрат вре-мени и трудовых ресурсов на восстановление работоспособности машины.
Таким образом, мерой ремонтопригодности являются время
и затраты на восстановление работоспособного состояния.
К сожалению, во многих конструкциях металлургических ма-шин вопросы их ремонтопригодности проработаны очень слабо и имеют низкие показатели.
Ремонтопригодность характеризуется как единичными, так и комплексными показателями.
Единичные показатели:
1. Среднее время восстановления работоспособного со-стояния (математическое ожидание времени восстановления ра-
ботоспособного состояния) – TВ .
|
|
2. Вероятность восстановления работоспособного состоя-ния - P(t )= P(tВ < t)(вероятность того, что время восстановления
работоспособного состояния не превысит заданного - аналогия вероятности отказа).
3. Средние затраты на восстановление работоспособного состояния - QВ .
Комплексные показатели:
1. Коэффициент готовности - КГ . Вероятность того, что
объект окажется в работоспособном состоянии в произвольный момент времени, кроме планируемых периодов, в течение которых применение объекта по назначению не предусматривается.
КГ = | T | , | (7.1) | |
T +T | ||||
В |
где Т - средняя наработка на отказ.
2. Коэффициент оперативной готовности - КОГ . Вероят-ность безотказной работы объекта в течение заданного времени t,
61
начиная с произвольного, достаточно удаленного момента време-ни t∞.
Оценкой КОГ является отношение
КОГ = | n [t∞ ,t ∞+ t] | , | (7.2) | |
N | ||||
т.е. отношение числа объектов, исправных в произвольный, дос-таточно удаленный момент времени и проработавших затем без-отказно в течение заданного времени t, к общему числу объектов.
|
|
3. Коэффициент технического использования - КТИ .
КТИ = | T | . | (7.3) | ||
T +T +T | |||||
В | р |
Отношение средней наработки на отказ за некоторый пери-од эксплуатации к сумме средних наработок на отказ, длительно-сти плановых ремонтов и аварийных простоев оборудования.
Этими показателями оценивается ремонтопригодность ма-шин в процессе их эксплуатации.
Для оценивания же ремонтопригодности машин на стадии проектирования используются относительные показатели ремон-топригодности:
• | коэффициент взаимозаменяемости КВ | |||||||||
КВ | = | Sдм | ; | (7.4) | ||||||
Sдм + SП | ||||||||||
• | коэффициент доступности | Кд | ||||||||
K ∂= | S0 | , | (7.5) | |||||||
S 0+ SB | ||||||||||
где Sдм - трудоемкость демонтажно-монтажных работ, чел.-ч/ед. наработки;
SП -трудоемкость пригоночных работ,чел.-ч/ед.наработки; SО -трудоемкость основных операций,чел.-ч/ед.наработки;
62
SВ -трудоемкость вспомогательных операций,чел.-ч/ед.на-работки;
|
|
• | коэффициент унификации | Ку | ||||||
Ку = | N у | ; | (7.6) | |||||
N | ||||||||
• | коэффициент стандартизации | КСТ | ||||||
КСТ | = | NСТ |
| , | (7.7) | |||
| ||||||||
N | ||||||||
где N у , NСТ - число соответственно унифицированных и стан-
дартных сборочных единиц или деталей, не вошедших в состав сборочных единиц;
N - общее число составных частей.
При оценке ремонтопригодности новых конструкций машин используется и качественная или экспертная оценка. При эксперт-ной оценке ремонтопригодности выделяют параметры, опреде-ляющие трудоемкость и длительность восстановления.
Такими параметрами могут являться:
• количество сборочных единиц;
• количество предварительно снимаемых элементов для доступа к месту отказа;
• технологичность процесса сборки;
• рабочие позы ремонтников;
• возможность использования средств механизации;
• наличие средств контроля и систем технической диагностики;
• организация технического обслуживания и ремонтов.
|
|
Оценивание параметров может осуществляться либо в бал-лах, либо словами: «лучше», «хуже», «без изменений». Во втором случае более высокая ремонтопригодность будет характеризовать конструкцию, для которой количество параметров, оцененных словом «лучше», будет больше.
Анализ надежности металлургических машин часто показы-вает их низкую ремонтопригодность. Так, например, для демонта-жа 1 т отказавшего оборудования требуется предварительно де-
63
монтировать до 20 т исправного оборудования. Отсутствуют сред-ства контроля и технической диагностики; низкий уровень механи-зации слесарно-сборочных работ; неудобные позы ремонтников; существующие сроки плановых ремонтов оборудования не явля-ются оптимальными с точки зрения минимума затрат на восста-новление работоспособности и потерь, связанных с простоем обо-рудования.
Существующая система технического обслуживания и ре-монта (ТОиР) не отвечает условиям оптимальности. Поэтому не-обходимо рассматривать различные возможные стратегии восста-новлений и на основе математического подхода устанавливать оптимальные сроки замены оборудования.
Дата добавления: 2018-05-12; просмотров: 327; Мы поможем в написании вашей работы! |
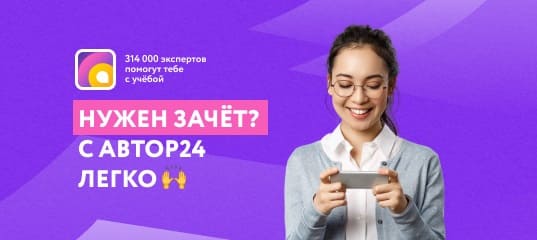
Мы поможем в написании ваших работ!