Глава 7. Смазка и смазочные материалы
7.1. Виды смазки
Наиболее эффективным средством снижения величины коэффициента трения и износа в узлах трения машин является применение специальных материалов, получивших название
“Смазочные материалы”.
При введении смазочного материала между трущимися поверхностями реализуются различные механизмы взаимодей-ствия, определяемые свойствами смазочного материала, свой-ствами трущихся поверхностей, кинематическими и силовыми условиями на контакте.
Действие смазочного материала на поверхности трения, приводящее к снижению трения и скорости изнашивания обозна-чается термином “смазка”.
Различают два вида:
- жидкостная смазка;
- граничная смазка.
Синонимами этих терминов являются жидкостное трение
и граничное трение.
При одновременном возникновении между трущимися по-верхностями жидкостной смазки и граничной смазки действие смазочного материала определяют термином “смешанная смаз-
ка”.
Жидкостная смазка имеет несколько режимов:
- гидродинамический;
- гидростатический,
- эластогидродинамический.
99
При обозначении режимов жидкостной смазки допускается опускать термин “жидкостная”, т.е. гидродинамическая смазка, гидростатическая смазка, эластогидродинамическая смазка.
Внешнее различие режимов смазки может определяться толщиной пленки смазочного материала, разделяющегося тру-щиеся поверхности. С этой целью введен так называемый ко-
|
|
эффициент толщины пленки λ .
λ = | h | , | ||
R 2 | + R2 | |||
а1 | а2 |
где h - толщина пленки смазочного материала, Rа1, Rа2-шероховатости поверхностей.
При λ ≤1 - наиболее вероятна граничная смазка; λ ≤5-смешанная смазка;
1 ≤ λ ≤10 | - эластогидродинамическая смазка; |
5 ≤ λ ≤ 100 | - гидродинамическая и гидростатическая |
смазка.
Сравнительные толщины пленок смазочного материала при различных видах смазки приведены на рис7.1.
допуски
шероховатость
ГД - пленка
ЭГД - пленка
МЭГД - пленка
слой окислов
предельный слой смазочного материала диаметр молекулы окисла
10-10 | 10 | 10 | 10 | 10 | 10-5 | 10-4 | 10-3 М |
100
Рис 7.1. Сравнительная толщина пленки смазочного материала при различных режимах смазки
Известно, что различные режимы трения характеризуются различной величиной коэффициента трения.
f | ||||
I | II | III | ηω | |
ρ | ||||
Рис. 7.2 Кривая Штрибека.Зависимость коэффициента трения от параметра Герси:
|
|
I - зона сухого и граничного трения; II - зона смешанного трения;
III - зона жидкостного трения
На рис.7.2 приведена кривая Штрибека, характеризующая зависимость величины коэффициента трения f от безразмер-
ного параметра | η ⋅ω | , | ||
p |
где η - динамическая вязкость смазочного материала, Па⋅с ;
ω -частота вращения, с−1; p -удельная нагрузка, Па.
7.2. Гидродинамическая жидкостная смазка
Условием реализации жидкостной смазки является полное разделение трущихся поверхностей слоем жидкого смазочного материала. Обеспечить такое разделение можно, зная законо-
101
мерности механизма взаимодействия смазочного материала и трущихся поверхностей.
Один из таких механизмов реализуется в подшипниках скольжения при смещении трущихся поверхностей – это режим гидродинамической смазки.
На рис.7.3 и 7.4 представлены схемы поведения деталей подшипника скольжения при изменении скорости вращения вала.
Ρ Ρ
∆
H min
Рис. 7.3. Схема возникновения несущего масляного слоя в подшипнике:
а – отсутствие вращения вала; б – вращающийся вал
|
|
Ρ Ρ
![]() | l / d = ∞ | ε | ||
δ | 0,9 | |||
1.0 | ||||
0.7 | ||||
0.5 | 0,7 | |||
δ | в | 0.3 | 0,5 | |
ϕ | α | 0,3 | ||
h min | ||||
0,1 | ||||
а | б | в0 |
δ |
Рис. 7.4. Положение вала в подшипнике:
a - момент трогания; б - установившийся режим;
в - изменение положения центра вала в подшипнике (полукруг Гюмбе-
ля)
Исходное положение вала в подшипнике скольжения (рис.7.3,а) определяется диаметральным зазором ∆ и ради-альным зазором δ = ∆/ 2. В момент трогания вал накатывается на подшипник, и ось вала отклоняется на угол ϕ (рис.7.4,а), а
при последующем проворачивании вала осуществляется захват смазочного материала.
102
|
hmin |
При достижении номинальной скорости вал занимает по-ложение, соответствующее рис. 7.3,б и 7.4,б. Между валом и подшипником скольжения формируется слой смазочного мате-
риала с толщиной hmin в месте максимального сближения. Раз-ность между радиальным зазором δ и минимальной толщиной
|
|
слоя смазочного материала определяет эксцентриситет
e оси вала относительно оси подшипника.Величина эксцентри-ситета зависит от величины Р нагрузки на подшипник и частоты вращения вала ω . Для характеристики подшипника скольжения
используется относительный эксцентриситет ε = δe .
В слое смазочного материала возникают напряжения, эпю-ры которых представлены на рис.7.4,в.
Величина номинального давления находится из зависимо-
сти
pа = | Ρ | , | (7.1) | |
d ⋅l | ||||
где d и l - диаметр и длинна подшипника. Величина максимального напряжения
pmax≅(2..3) pа
Величина слоя смазочного материала hmin в соответствии
с гидродинамической теорией жидкостной смазки зависит от:
- частоты вращения вала ω ;
- номинального давления pа ;
- относительного диаметрального зазора ψ = ∆d ;
- вязкости смазочного материала η .
Положение центра вала определяется безразмерным па-
раметром η ⋅pω . С ростом этого параметра центр вала переме-
щается к центру подшипника по траектории, близкой к полуок-ружности диаметром, равным радиальному зазору δ (полукруг Гюмбеля). На рис. 7.4,в в качестве величины диаметра исполь-зована относительная величина – относительная толщина мас-ляного слоя
103
ξ = | hmin | . | (7.2) | |||
δ | η ⋅ω | |||||
При бесконечно большой величине параметра | центр | |||||
p |
вала совпадает с центром подшипника. При этом hmin = δ , кли-
новидность зазора исчезает, а давление в масляном клине должно быть равным нулю. Такое состояние может наступить при отсутствии внешней нагрузки.
С уменьшением параметра | η ⋅ω | толщина масляного слоя | ||
p |
hminуменьшается,вытекание масла,нагнетаемого в эту область
насосным действием вала, затрудняется, давление в масляном слое повышается, теоретически до бесконечности. Реально от-клонение от цилиндричности, шероховатость, наличие загрязне-ния в смазочном материале ограничивают несущую способность подшипника.
При гидродинамической смазке относительный эксцентри-
ситет ε и относительная минимальная толщина ξ =1−ε | явля- | |||
ются функциями безразмерного числа Зоммерфельда | ||||
So = | η ⋅ω | . | (7.3) | |
p ⋅ψ 2 |
Существует оптимальное значение, ξ = 0.3...0.35 , при ко-
тором режим гидродинамической жидкостной смазки наиболее устойчив.
Выше этого значения небольшие изменения нагрузки ведут к значительному смещению центра вала (полукруг Гюмбеля), которые легко переходят в циклические вихревые движения.
Взаимосвязь между числом Зоммерфельда и относитель-ной минимальной толщиной смазочного слоя может быть выра-жена следующими зависимостями для различных значений от-
ношения длины к диаметру подшипника | l | d | : | ||||||||
ξ | |||||||||||
l | d | = 0.75..1.0 | So = | ; | (7.4) | ||||||
0.8 l | d | − 0.24 | |||||||||
104
l | d | =1.0..2.0 | So = | ξ | . | (7.5) | ||||||
0.43 l | d | + 0.24 | ||||||||||
Для этих случаев оптимальный относительный зазор | ||||||||||||
ψопт =1.5⋅ | η ⋅ω | ⋅ l | d | . | (7.6) | |||||||
p |
Предельное значение относительного зазора, при котором еще реализуется гидродинамическая жидкостная смазка:
ψmax=3⋅ | η ⋅ω | ⋅3 l | d | . | (7.7) | |
p |
Ограничение на реализацию режима гидродинамической смазки накладывает и величина безразмерного параметра Рей-нольдса
Re = u ⋅hvmin ,
где hmin - минимальный слой смазочного материала, мм;
u - средняя скорость жидкостной пленки, мм/с;
v - кинематическая вязкость смазочного материала, мм2/с. При Re > 1900 ламинарное течение смазочного материала
переходит в турбулентное, что ведет к нарушению режима жид-костной смазки.
7.3. Гидростатическая жидкостная смазка
Разделение трущихся поверхностей в подшипнике сколь-жения можно осуществить не только в динамике (при вращении вала), но и в статике, когда вал неподвижен. Это очень важно в момент трогания вала. Это можно обеспечить, подавая в зону контакта вала с подшипником жидкий смазочный материал под высоким давлением, создаваемым установленным вне подшип-ника насосом. Такой режим разделения трущихся поверхностей получил название «гидростатическая жидкостная смазка», а подшипник, в котором реализуется этот режим, – «гидростатиче-ский подшипник жидкостного трения».
Для гидростатической смазки требуется давление масла порядка 20…30 МПа.
105
7.4. Эластогидродинамическая смазка
Этот режим смазки реализуется в подшипниках качения и зубчатых зацеплениях. Предпосылкой для возникновения пленки смазочного материала служат высокие контактные нагрузки, приводящие к упругим деформациям соприкасающихся тел и к росту вязкости смазочного материала в соответствии с зависи-мостью
η =η0⋅eαp , | (7.8) |
где η0 - вязкость смазочного материала при | p = 0, Па⋅c ; |
p - давление на контакте, МПа ;
α - пьезокоэффициент вязкости, МПа−1 , для минеральных масел, 0.01 <α < 0.04 .
Эпюра давлений в смазочном слое и вид контакта пред-ставлен на рис.7.5, т.е. на выходе имеется сужающаяся щель и соответствующий сужению всплеск давления.
r
III | III | ||
II | |||
I | I | ||
Х1 | Х2 | ||
P | 3 | ||
4 | |||
Д | |||
A | O | B | |
II | Д | ||
2 | 1 |
Рис. 7.5. Эпюра распределения скоростей , форма зазора между контактирующими при качении цилиндрами
и ориентировочная эпюра распределения в нем давления масла:
1 - контактирующие поверхности; 2 - масло; 3 – эпюра давле-ния масла; 4 - распределение давления по Герцу для несмазанных по-
верхностей; x1, x2 - координаты концов смазочного слоя
В наиболее узком месте увеличивается скорость течения и растет вязкость масла под действием давления. При выходе из зазора вязкость масла резко падает.
106
Наибольшее влияние на распределение максимума дав-
− | ||||||
ления оказывает параметр скорости U . | ||||||
− | η | 0 | ⋅u | |||
U = | , | (7.9) | ||||
E1 | ⋅ R | |||||
где η0 - вязкость смазочного материала, МПа⋅c ; u -скорость скольжения на контакте, мс ;
E1-эквивалентный модуль продольной упругости,Па; R -эквивалентный радиус кривизны,м.
Минимальная толщина масляной пленки также зависит от параметра скорости, т.е. возрастает с его ростом.
Сила трения, возникающая при эластогидродинамической смазке при чистом качении, изменяется с изменением параметра скорости и в первом приближении прямо пропорциональна тол-щине пленки смазочного материала.
Существенное влияние на режим эластогидродинамиче-ской смазки оказывает шероховатость контактирующих поверх-ностей. Условной мерой реализации эластогидродинамической смазки является коэффициент толщины пленки λ.
При λ > 3 топография поверхности не оказывает влияние на свойства пленки;
при 2< λ <3 увеличение поперечной шероховатости приво-дит к росту толщины пленки;
при 1< λ <2 на толщину пленки превалирующее влияние оказывает продольная разнотолщинность, что характерно для реальных режимов трения;
при λ ≅ 0,8 возникает смешанное трение с небольшой до-лей нагрузки, приходящейся на микронеровности;
при λ =1,5..2,5 возникают только отдельные контакты, ко-
торые исчезают при λ > 2,5, обеспечивая режим гидродинамиче-ской жидкостной смазки.
После приработки толщина пленки смазочного материала, необходимая для обеспечения жидкостного трения, уменьшается
в некоторых случаях до 10 раз.
7.5. Граничная смазка
107
В соответствии с международным стандартом ИСО 4378/3 под граничной смазкой понимается такой вид смазки, которому не могут быть приписаны объемные вязкостные свойства сма-зочного материала и который определяется свойствами гранич-ных слоев, возникающих при взаимодействии материала поверх-ности трения и смазочного материала в результате физической адсорбции или химической реакции.
Объемные свойства жидкого смазочного материала не проявляются при толщине пленки менее 0,02…0,1 мкм. Наибо-лее прочные адсорбционные слои на металлах образуют по-верхностно-активные вещества (ПАВ), такие как жирные кислоты, их спирты и эфиры, животные и растительные жиры.
Так, например, при толщине монослоя олеиновой кисло-
o
ты, равным 19,02 A , слой смазочного материала может вклю-чать 10…50 таких монослоев. Адсорбционные пленки образуют-ся на металлических поверхностях под действием ориентацион-ных сил притяжения Ван дер Ваальса. Молекулы, ориентирован-ные в силовом поле твердой поверхности, занимают стоячее по-ложение (рис. 7.6).
108
+ | - | + | + | ||
- | |||||
+ | - | - | - | ||
- | + | + | |||
+ | - | + | |||
+
-
-
- +
-
+
+- -
Рис.7.6. Схема формирования адсорбционного слоя
Затем под действием дисперсионных сил образуются сле-дующие слои. Молекулы между собой по всей длине находятся под действием поперечных (дисперсионных) сил. Таким образом, мультимолекулярный слой приобретает квазикристаллическую структуру комплекса жидких криталлов, обладающего свойства-ми квазитвердого тела с высоким модулем упругости рис.7.7.
109
В
Б
А
Рис.7.7. Схема структуры граничного смазочного слоя на поверхности металла:
А - поликристаллическая поверхность металла;
Б - поликристаллическая зона граничного слоя; В - монокристаллическая зона граничного слоя
Так , модуль упругости молекул жирных кислот достигает Е=3,5…5 ·105 МПа, а мультимолекулярные слои выдерживают нагрузку до 100 МПа.
С другой стороны, монослои связаны между собой слабы-ми дисперсионными силами Ван дер Ваальса, что является при-чиной легкого скольжения между контактирующими адсорбцион-ными пленками при граничном трении (рис.7.8).
Рис.7.8. Схема скольжения граничных слоев, построенных из цепных макромолекул
110
В результате химических реакций жирных кислот с метал-лической поверхностью образуются мыла, снижающие трение. Наиболее активны медь, кадмий, цинк, магний, в меньшей степе-ни железо, алюминий.
Прилегающий к твердому телу монослой образует химиче-ские связи с поверхностью металла с образованием химически модифицированных слоев при наличии таких химически актив-ных элементов, как S, Cl, P. В этом случае образуются модифи-цированные слои, состоящие из соединений железа с S, Cl, P. Модифицированные слои не только обеспечивают снижение трения, но и являются более активными адсорбентами.
Модифицированные слои повышают износостойкость, так как в процессе трения разрушается не сам металл, а менее прочный модифицированный слой, существенную долю в кото-ром составляет активный элемент присадки. В результате этого вместо интенсивного изнашивания металла происходит потеря массы присадки, воспроизводимой из смазочного материала.
Эффективность присадок, содержащих Cl, начинает прояв-ляться при температуре 100…150°С. Сульфидные пленки эффек-тивны при более высоких температурах, но коэффициент трения несколько выше. Самый высокий коэффициент трения имеют фос-фидные пленки, но они обладают высокой износостойкостью. По-верхностно-активные вещества в результате миграции по поверх-ности могут проникать в микротрещины, вызывая адсорбционное пластифицирование (эффект Ребиндера) и, как следствие, разру-шение тонкого поверхностного слоя. Если такой процесс локализу-ется на микронеровностях, то происходит их сглаживание, идет процесс приработки и улучшения смазывания поверхностей.
Q F Q
Рис. 7.9. Схема адсорбционно-расклинивающего действия полярных молекул смазочного материала:
F – давление адсорбированого слоя; Q – расклинивающие силы
111
При высоких нагрузках процесс разрушения поверхностей проникает на большую глубину и граничные слои ведут себя не как смазочные, а скорее как режущие.
При граничной смазке проявляется еще один эффект – “эффект Дерягина”, когда ориентированные граничные слои спо-собны оказывать расклинивающее действие, выражающееся в сопротивлении слоя смазочного материала утоньшению под действием нагрузки (рис.7.9).
Значительное влияние на прочность граничного слоя ока-зывает температура. Повышение температуры приводит к рез-кому возрастанию силы трения и повреждению поверхностей, свидетельствующее о разрушении граничного смазочного слоя, т.е. о дезориентации и десорбции молекул ПАВ.
Повышение температуры в присутствии химически актив-ных добавок в смазочном материале интенсифицирует процесс образования химически модифицированных слоев, обеспечи-вающих снижение трения и износ. Дальнейший рост температу-ры ведет к разрушению модифицированных слоев, следствием чего является адгезионное изнашивание.
Разрушение граничного слоя может вызываться и пласти-ческой деформацией поверхностей в сопряженном контакте.
7.6. Смазочные материалы
7.6.1. Общая характеристика
Для снижения трения и скорости изнашивания широкое распространение получили смазочные материалы. Различают несколько видов смазочных материалов:
- жидкие смазочные материалы (ЖСМ);
- пластичные смазочные материалы (ПСМ);
- твердые смазочные материалы (ТСМ);
- газообразные смазочные материалы (ГСМ); По происхождению ЖСМ подразделяются на:
- минеральные (нефтяные и сланцевые);
- жировые (растительные и животные);
- синтетические.
Минеральные масла представляют сложную смесь угле-водородов (парафиновых, нафтеновых, ароматических). В них присутствуют сернистые соединения, смолы, нафтеновые кисло-ты.
112
Чистые нефтяные масла работоспособны в диапазоне тем-ператур -40°С…+50°С. Эксплуатационные свойства масел улучшают путем введения присадок. Эти масла наиболее широ-ко используются для смазывания узлов трения механизмов ме-таллургических машин.
Жировые масла обладают лучшими антифрикционнымисвойствами, чем чисто нефтяные масла, но являются менее ста-бильными в эксплуатации, быстро окисляются, особенно при по-вышенной температуре. Работоспособны при температурах - 20°С…+100°С. В чистом виде используются в основном в про-цессе холодной прокатки полос, в качестве присадок к нефтяным маслам и при производстве ПСМ.
Синтетические масла пока не используются в узлах тре-ния металлургических машин из-за их высокой стоимости.
Они работоспособны в диапазоне температур -60 – +400°С.
Применение ЖСМ обеспечивает в узлах трения:
- режим жидкостной смазки;
- интенсивный теплоотвод;
- фильтрацию продуктов износа.
Пластичный смазочный материал (ПСМ) представляет со-бой систему, состоящую из жидкой среды, которая удерживается в структурном каркасе загустителя. В качестве жидкой среды ис-пользуются ЖСМ (от 70 до 95% по массе), преимущественно ми-неральные масла. В качестве загустителя используются мыла жирных кислот, твердые углеводороды, пигменты, силикагель, бентонитовые глины . Для улучшения эксплуатационных свойств вводятся присадки и наполнители (до 10% по объему).
Применение ПСМ обеспечивает в узлах трения:
- режим граничной смазки;
- избирательный перенос;
- защиту от коррозии;
- снижение вибрации;
- снижение трения и износа;
- уплотнение зазоров в сопряжениях.
Твердые смазочные материалы (ТСМ) и твердые анти-фрикционные покрытия применяются тогда, когда не могут при-меняться ЖСМ и ПСМ, т.е . при температурах застывания этих материалов и при высоких температурах, когда эти материалы разлагаются и испаряются.
113
Твердые смазочные материалы подразделяются на неор-ганические и органические . Из неорганических твердых смазоч-ных материалов наиболее широкое распространение получили:
графит, дисульфид молибдена MoS2 , дисульфид вольфрама WS2.Из органических ТСМ наиболее широко используются по-
литетрафторэтилен (ПТФЭ), полиамиды.
Газовые смазочные материалы используются в высокоско-ростных узлах трения при n >10000 об мин.
7.6.2. Классификация минеральных масел
В зависимости от способа получения нефтяные масла раз-
личают:
- дистиллятные (полученные из масляных дистиллятов по-сле вакуумной перегонки мазута);
- остаточные (полученные из гудрона); - компаундированные (путем смешивания базовых дистил-
лятных и остаточных масел); - загущенные (с полимерными присадками).
По назначению масла подразделяются на: - индустриальные; - трансмиссионные; - моторные;
- энергетические (турбинные, трансформаторные, электро-изоляционные, конденсаторные, кабельные, компрессорные, для выключателей);
- технологические; - теплоносители;
- специальные (пропиточные, парфюмерные, медицинские, для цепей туннельных печей и др.).
В узлах трения металлургических машин в основном ис-пользуются индустриальные и трансмиссионные масла.
В соответствии со стандартом ГОСТ 17479.4-87 “Смазоч-ные материалы индустриальные”, разработанном на основании международного стандарта ИСО 3448-75, индустриальные масла подразделяются по вязкости на 18 классов с кинематической
вязкостью v40 = 2...1500 мм2 с при температуре t =400 C .
114
По прежней классификации значение вязкости в обозначе-нии марки минерального масла приводилось для эталонных
температур 500 C и 1000 C .
Пример обозначения индустриальных масел по прежней и действующей классификациям
Эталонная температура t, °С
50 | 40 | 100 | 40 |
И-12 H | И-Л-А-22 | Цилиндровое-11 | И-Т-А-100 |
ИГП-14 | И-Л-С-22 | МС-14 | И-Т-А-220 |
И-20 А | И-Г-А-32 | МС-20 | И-Т-А-320 |
ИСП-40 | И-Т-D-68 | П-28 | И-Т-А-460 |
И-50 А | И-Г-А-100 | Цилиндровое-24 | И-Т-А-460 |
ИГП-72 | И-Г-С-100 | Цилиндровое-38 | И-Т-А-680 |
ИТП-200 | И-Т-D-460 | П-40 | И-Т-А-680 |
ИТП-300 | И-Т-D-680 | Цилиндровое-52 | И-Т-А-1000 |
В обозначение индустриальных масел входят символы, отражающие область применения, эксплуатационные свойства и класс вязкости.
Порядок символов. Характеристика символов
[1-2-3-4] | |||||||||
| | | | | | | значение вязкости в мм2 с | . | |||||
| | | | | | | 2,3,5,7,10,15,22,46,68,100,150,220,460,680,1000,1500 | ||||||
| | | | | | |||||||
| | | | | эксплуатационные свойства | . | ||||||
| | | | | | А - масла без присадок | ||||||
| | | | | В→А+антиокислительные, антикоррозионные присадки | |||||||
| | | | | С→В+противоизносные | |||||||
| | | | | D→С+противозадирные | |||||||
| | | | | Е→D+противоскачковые | |||||||
| | | | ||||||||
| | | область применения | . | |||||||
| | | | Л(F)-легконагруженные узлы трения | |||||||
| | | Г(Н)-для гидравлических систем | ||||||||
| | | Н(G)-для направляющих скольжения | ||||||||
| | | Т(С)-тяжелонагруженные узлы трения |
115
| И – индустриальные масла
7.6.3. Показатели физических свойств минеральных масел
Вязкость
При подборе минеральных масел значение вязкости явля-ется определяющей величиной. Различают вязкость динамиче-скую – η и кинематическую – ν . В системе СИ за единицу дина-
мической вязкости принята Паскаль ·секунда (Па ·с), за единицу кинематической вязкости – м2/с. Для характеристики вязкости минеральных масел используются более мелкие единицы изме-рения – мПа ·с и мм2/с. Соотношение между динамической и ки-нематической вязкостью определяется зависимостью:
ν = | η | , | (7.11) |
ρ |
где ρ – плотность минерального масла.
На вязкость существенное влияние оказывает температу-ра. В инженерных расчетах значение вязкости в зависимости от температуры можно определить по формуле Прокофьева:
t | э | n | |||||
νt | = νtэ ⋅ |
| , | (7.12) | |||
t |
где νtэ – значение динамической вязкости при эталонной темпе-
ратуре (40, 50, 100оС);
t – температура , при которой определяется вязкость смазоч-ного материала, как правило рабочая температура;
n – коэффициент, определяемый из зависимости:
n = | 1+ lg(νt ) | ||
2 , 8 −lg( t ) . | (7.13) |
Для характеристики изменения вязкости в зависимости от температуры существует так называемый индекс вязкости – ИВ. Если ИВ находится в пределах 85…95, то минеральное масло име-ет удовлетворительную вязкостно-температурную характеристику. Чем выше ИВ, тем с меньшей интенсивностью изменяется вязкость
116
с изменением температуры, тем надежнее реализуется режим жид-костной смазки в более широком температурном диапазоне.
Температура застывания
Температурой застывания условно считается та темпера-тура, при которой масло, помещенное в пробирку, не меняет по-ложение мениска (на глаз) при повороте пробирки из вертикаль-ного положения в наклонное под углом 45о.
Температура вспышки
Температура, при которой мгновенно вспыхивают нако-пившиеся газообразные углеводороды при приближении откры-того пламени. Чем выше температура вспышки, тем более ста-бильно минеральное масло.
Кислотное число
Кислотное число характеризует количество щелочи КОН в мг, необходимой для нейтрализации кислот, находящихся в 1 г. масла. Присутствие кислот, особенно низкомолекулярных, вызы-вает интенсивную коррозию металлов. Повышение кислотного числа характеризует старение минерального масла.
Анилиновая точка
Это температура, при которой равные объемы минераль-ного масла и анилина разделяются на две фазы. Чем выше тем-пература разделения смеси, тем больше в масле ароматических соединений, тем ниже ИВ.
Противозадирные свойства
Характеризуются индексом задира – Из и нагрузкой за-
едания – Pкр .
Из = Р0d⋅иdг ,
где Р0 – нагрузка прижатия верхнего шара к нижним в четырех-шариковой машине трения;
117
dг –диаметр площадки упругой деформации шаров; dи –диаметр пятна износа.
Более износостойкими являются остаточные масла. Для них dи =0,6…0,8 мм при нагрузке 196 Н по ГОСТ 9490-75. Для
дистиллятных масел dи =0,8…1,1 мм.
7.6.4. Фильтрация масел
Любая система смазывания и гидравлическая система за-грязнены уже до начала эксплуатации (остатки материала, обра-зовавшиеся при изготовлении, частицы, попавшие в момент сбор-ки).
Степень загрязнения системы увеличивается вследствие износа за счет попадания загрязнений через вентиляционные отверстия, уплотнения, в процессе проведения ремонтов. При этом в одном литре масла может находиться до 100 млн. частиц размером более 1 мкм.
До 80% отказов в смазочных и гидравлических системах вызваны загрязнениями (заклинивание, более длительный рабо-чий цикл за счет износа сопряжений, вибрация подшипников, от-сутствие необходимого давления, повышение температуры мас-ла). Поэтому необходима соответствующая постоянная фильт-рация масла. С этой целью используют защитные фильтры гру-бой очистки и рабочие фильтры сверхтонкой очистки. Первые задерживают крупные частицы, размеры которых значительно больше зазоров. Рабочие фильтры удаляют частицы до 5 мкм и сводят износ до минимума. Решающее влияние на износ узлов трения наряду с размерами частиц оказывает и их количество.
Разработан международный стандарт ИСО 4406 на чисто-ту масла. По этому стандарту определяется количество частиц размером более 5 мкм и частиц размером более 15 мкм в 100 мл жидкости.
Обычные фильтры задерживают частицы размером более 25 мкм, что определяет невысокий срок службы узлов трения, работающих в режиме эластогидродинамической смазки. Суще-ственно повышается срок службы таких узлов при фильтрации частиц менее 10 мкм.
В процессе эксплуатации необходимо удалять не только час-тицы загрязняющих веществ, но и воду, проникающую в систему. Вода способствует кавитации, коррозии, ускоренному старению масла, особенно при наличии частиц железа или меди, которые являются катализаторами старения масла при наличии воды. На-
118
ряду с этим вода способствует осаждению присадок, уменьшению толщины смазочной пленки, ускоренному износу шестеренчатого насоса.
7.6.5. Регенерация минеральных масел
Продукты окисления, загрязнения и другие примеси, нака-пливающиеся в масле в процессе эксплуатации, резко снижают его качество. Для восстановления первоначальных свойств ма-сел или существенного снижения количества продуктов окисле-ния и воды разработаны различные способы регенерации. Про - стейшими технологическими процессами регенерации являются:
- отстой и фильтрация;
- отстой, адсорбционная очистка, фильтрация;
- отстой, обработка щелочью, адсорбционная очистка, фильтрация;
- отстой, обработка кислотой, адсорбционная очистка, фильтрация;
- отстой, обработка кислотой и щелочью, адсорбционная
очистка, фильтрация.
Отстой отработавших масел от механических примесей и воды наиболее эффективен при 80о…90оС. Время отстоя 24…48 ча-сов.
Для фильтрации масла применяют металлические сетки, плотные ткани, бумагу, картон, отбеливающие земли.
Малозагрязненные и малообводненные масла (до 0,3%) в циркуляционных смазочных системах очищают сепараторами при подогреве масла до 60…70оС.
Серно-кислотную очистку применяют для глубоко окислен-ных отработавших масел.
Обработка щелочью служит для удаления из масла орга-нических кислот и остатка свободной серной кислоты.
Наиболее эффективным способом удаления из масла ас-фальтосмолистых веществ является адсорбция. В качестве ад-сорбентов применяется активированный уголь и отбеливающие земли. Наиболее глубокую очистку минеральных масел, практи-чески полное восстановление исходных свойств можно получить на специальных регенерационных установках. В этом случае технологический процесс включает следующие процессы:
- осаждение (грубое удаление воды и механических при-месей);
119
- атмосферная перегонка (удаление низкокипящих фрак-ций и воды);
- серно-кислотная очистка с последующей нейтрализаци-ей известью (удаление продуктов окисления и приса-док);
- фильтрование (удаление кислого гудрона);
- вакуумная перегонка (разделение на один или два ма-ловязких и средневязких дистиллята и остаток);
- очистка отбеливающими глинами;
- компаудирование и введение присадок.
7.6.6. Пластичные смазочные материалы и их свойства
При подборе ПСМ решающее значение имеют их эксплуа-тационные характеристики, наиболее важными являются:
- объемно-механические свойства;
- стабильность, как коллоидных систем;
- триботехнические свойства.
К объемно-механическим свойствам относятся: предел прочности на сдвиг и разрыв, вязкость, механическая стабиль-ность, термоупрочнение, пенетрация. Предел прочности на сдвиг определяет каркас загустителя. Для большей части ПСМ в ин-тервале температур t=20…120оС предел прочности составляет
σр = 0,1…2 кПа. При меньших значениях смазочный материал
вытекает из узла трения, при больших значениях затрудняется его доступ к смазываемой поверхности.
Вязкость определяет возможность подачи и заправки ПСМ в узлы трения при низких температурах. Существующими нагне-тателями можно подавать ПСМ вязкостью не более 5…10 кПа ·с. В централизованных смазочных системах вязкость ПСМ не должна превышать 80 Па ·с.
После разрушения структурного каркаса ПСМ начинает течь подобно жидкости. С увеличением скорости течения (скоро-сти деформации ) до 10 с-1 вязкость смазочного материала пони-жается в сотни и тысячи раз.
В результате интенсивного и длительного сдвига изменя-ется предел прочности. Изменение предела прочности на сдвиг под воздействием механического нагружения есть механическая стабильность, которая характеризуется индексом разрушения – Кр и индексом восстановления – Кв.
120
Кр = | σи −σ р | ⋅100%; Кв = | σв −σ р | ⋅100%, | |||
σ и | σ р | ||||||
где σи - исходный предел прочности на сдвиг; σр - предел прочности после разрушения;
σв - предел прочности через трое суток после окончания раз-
рушения.
Термоупрочнение характеризует изменение предела проч-ности на сдвиг ПСМ при нагреве выше 100оС и последующем охлаждении.
Степень консистенции ПСМ характеризуется числом пе-нетрации. Число пенетрации выражает глубину погружения в мм, умноженную на число 10, стандартного конуса массой 150 г под действием собственного веса в течение 5 с.
ПСМ должны сохранять стабильность как коллоидные сис-темы, неизменность состава, стойкость против окисления, инертность к воде и агрессивным средам. Проявлением наруше-ния коллоидной стабильности является выделение жидкой фазы (минерального масла) в процессе хранения и под воздействием одностороннего приложенного давления.
ПСМ обеспечивают реализацию граничной смазки и по-этому имеют лучшие антифрикционные характеристики, чем ми-неральные масла, на которых они изготовлены.
Противоизносные и противозадирные свойства ПСМ ха-рактеризуются нагрузкой заедания – Ркр и нагрузкой сваривания
– Рс.
Присутствие в ПСМ свободных щелочей и воды существенно ухудшает их смазочное действие, усиливается коррозионный износ.
Наиболее эффективно для снижения износа является вве-дение в ПСМ роданида меди, этиленгликоля.
Для улучшения триботехнических свойств в ПСМ вводят различные наполнители в виде порошков графита, Мо S2, слюды, Sn, Cu, Pb. Введение в ПСМ соли однойодистой меди и соли ме-ди ацетилсалициловой кислоты реализует эффект безизносно-сти. В качестве полимерных наполнителей используют полиэти-лен, полипропилен, ПТФЭ в виде порошков дисперсностью до 10 мкм.
7.6.7. Твердые смазочные материалы
121
Наиболее часто в узлах трения металлургических машин при невозможности применения ЖСМ и ПСМ применяются гра-фит, дисульфид молибдена, мягкие металлы (Pb, Sn), ПТФЭ (фторопласт).
Графит обладает хорошими антифрикционными свойства-ми в атмосферных условиях до температуры t=400оС, которые теряются в вакууме, инертном газе, сухом воздухе.
Дисульфид молибдена MoS2 имеет структуру, подобную графиту, но его антифрикционные свойства ухудшаются при ад-сорбции кислорода, паров воды и других веществ, вступающих в химическое взаимодействие с серой. В вакууме MoS2 работоспо - собен до температуры t=1000…1300оС, а на воздухе до t=350оС.
Мягкие металлы (металлы с низкой температурой плавле-
ния: Jn – 165оC, Pb –327оС, Sn – 238оС, Cd – 321оС) используют-
ся в качестве основы или компонентов покрытий на твердых кон-струкционных материалах. Их антифрикционность определяется малым сопротивлением срезу в тонком слое мягкого покрытия при относительном движении поверхностей под нагрузкой. По-рошки мягких металлов вводят в качестве наполнителей в ПСМ и композиционные антифрикционные материалы.
Из органических полимерных материалов наиболее эф-фективен политетрафторэтилен (ПТФЭ) или фторопласт (зару-бежное название - тефлон). ПТФЭ имеет смешанную кристалли-ческую и аморфную структуру (степень кристалличности до 90%). Взаимодействие между молекулами и кристаллами ПТФЭ осуществляется слабыми ван-дер-ваальсовыми силами, что и обеспечивает его высокую антифрикционность. ПТФЭ инертен, не горит, не смачивается большинством жидкостей, работоспо-собен при температурах t=-269…+270оС. Основные характери-стики:
- температура плавления кристаллов 327оС;
- твердость 30…40 HB(МПа);
- предел прочности на растяжение σр =14…31 МПа;
- модуль упругости при изгибе 0,43…0,85 ГПа;
- температурный коэффициент линейного расширения –
24 ·10-5;
- допустимые нагрузки и скорости скольжения [p]=0,2 МПа, [v]=2м/с.
ПТФЭ в узлах трения применяется в виде тонких покрытий, в композиционных материалах и в качестве наполнителя ПСМ.
Этот материал требует осторожного обращения при нагре-ве. При температуре выше 400…500оС начинается разложение
122
фторопласта с выделением токсичного газа перфторизобутиле-на, который в 50 раз токсичнее фосгена.
Дата добавления: 2018-05-12; просмотров: 458; Мы поможем в написании вашей работы! |
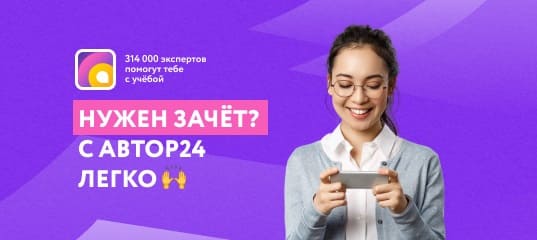
Мы поможем в написании ваших работ!