Глава 8. Выбор смазочных материалов для узлов трения
8.1. Методика выбора смазочных материалов
Смазочные материалы являются, по сути, конструкцион-ными материалами, и от правильного выбора соответствующей марки смазочного материала во многом зависит надежность ма-шин и механизмов.
Освоение методики выбора смазочных материалов позво-ляет не только осуществлять их выбор, но и выявлять как грани-цы их использования, так и область изменения параметров на-гружения, обеспечивающую наибольшую износостойкость узла трения.
Применение того или иного вида смазочного материала в конкретном узле трения зависит от многих факторов: условий внешней среды (температура, влажность и т.д.), удельной на-грузки, скорости смещения контактирующих поверхностей, ха-рактера движения (прерывистое , реверсивное), геометрических характеристик и материала пар трения, твердости поверхност-ных слоев трущихся тел, необходимости использования конкрет-ной системы смазывания, конструктивного исполнения узла тре-ния и др.
Металлургические машины, особенно прокатные станы, ха-рактеризуются широким спектром нагружения, и поэтому даже рекомендуемые заводом-изготовителем марки смазочных мате-риалов не могут охватить всего диапазона изменения силовых и кинематических параметров технологического процесса. Специа-лист, осуществляющий техническую эксплуатацию оборудования, обязан знать границы изменения этого диапазона как для исполь-зуемых марок смазочных материалов, так и для их заменителей.
|
|
В общем случае методика выбора смазочных материалов заключается в следующем:
- выявляются условия работы и технические параметры узла трения;
- осуществляется выбор вида смазочного материала;
- определяется марка смазочного материала.
Основными параметрами, влияющими на выбор смазочно-го материала, являются: удельная нагрузка р и скорость сколь-
123
жения υ, параметр pυ и температура θ , твердость и микро-геометрия трущихся поверхностей, материал трущихся поверх-ностей.
8.2. Выбор вида смазочного материала
8.2.1. Общая характеристика смазочных материалов
В узлах трения металлургических машин наиболее широ-кое распространение получили жидкие, пластичные и твердые смазочные материалы.
В качестве жидких смазочных материалов широко исполь-зуются минеральные масла, способные обеспечить:
- жидкостную смазку;
- интенсивный теплоотвод;
- фильтрацию продуктов изнашивания.
При выборе минеральных масел необходимо учитывать,
что:
- при температуре выше 150°С происходит деструкция ма-
сел;
- при незначительном изменении температуры масла про-исходит значительное изменение его вязкости;
|
|
- требуется эффективная герметизация узлов трения;
- необходимо большое количество единовременно исполь-зуемого масла.
Минеральные масла рекомендуется применять в узлах трения с интенсивным тепловыделением, работающих с доста-точно большими контактными нагрузками и скоростями скольже-ния.
К таким узлам металлургических машин относятся: редук-торы, шестеренные клети, нажимные устройства, подшипники качения и скольжения и др.
Область применения минеральных масел во многом зави-сит от конструктивного исполнения узла трения. Марки мине-ральных масел приведены в табл. 1 прил. В. При невозможности реализации в узле трения жидкостной смазки применяют пла-стичный смазочный материал (ПСМ). Пластичный смазочный материал обеспечивает:
- режим граничной смазки;
- удержание смазочного материала в открытых и слабо-герметизированных узлах трения;
124
- работоспособность узла трения при высоких температу-рах и нагрузках в широком скоростном диапазоне;
- длительный срок службы в герметизированных узлах тре-
ния.
Недостатками в применении ПСМ являются:
- более трудоемкая замена смазочного материала;
|
|
- малый теплоотвод;
- затрудненное удаление продуктов процесса изнашива-
ния.
Наиболее эффективно применение ПСМ для смазывания подшипников качения.
Марки ПСМ приведены в табл. 5 прил. В .
Твердые смазочные материалы (ТСМ) применяют в узлах трения металлургических машин, характеризующихся следую-щими условиями работы:
- высокие контактные напряжения и низкие скорости
скольжения (менее 0,1 м/с); .
- наличие агрессивных сред, разрушающих обычные сма-зочные материалы;
- экстремальные температуры (выше 300 °C и ниже -80
°C )
ТСМ наносят на поверхность трущихся деталей в виде суспензий. После термической обработки на поверхности дета-лей образуются твердые смазочные пленки. Недостаток таких покрытий - малый срок службы.
ТСМ с успехом используются как присадки к жидким и пла-стичным смазочным материалам. В табл. 6 прил. В приведены основные физико-механические свойства ПСМ с добавками.
Особую группу составляют самосмазывающиеся конструк-ционные материалы, физико-механические характеристики кото-рых приведены в табл. 7 прил. В.
Самосмазывающиеся материалы применяют в тех случа-ях, когда применение ЖСМ и ПСМ невозможно или затруднено, требуется длительная работа узла трения с низким трением и высокой износостойкостью (в условиях низких удельных нагру-зок).
|
|
Разработаны конструкционные материалы, основу которых составляют пористые металлы (бронза, железо и др.), пропитан-ные ТСМ или самосмазывающимися материалами.
8.2.2. Выбор вида смазочных материалов для узлов трения
125
Подшипники скольжения
В подшипниках скольжения при скоростях скольжения бо-лее 1 м/с и постоянном направлении относительного скольжения поверхностей наиболее эффективны ЖСМ (минеральные мас-ла).
Применение ПСМ целесообразно при скоростях скольже-ния менее 1 м/с при высоких контактных нагрузках (более 10 МПа), при постоянном изменении направления скольжения по-верхностей, при температурах -50 ... +200 °C .
При температуре выше 250 °C необходимо использование
ТСМ.
Подшипники качения
В подшипниках качения наилучшим смазочным материа-лом являются минеральные масла. Но их использование услож-няет конструкцию подшипникового узла. При использовании ПСМ упрощается конструктивное исполнение и во многих случаях об-легчается его эксплуатация.
Минеральные масла рекомендуется использовать в под-шипниках качения при частоте вращения менее 5 - 10 об/мин и окружной скорости более 5 м/с.
Исходя из условий технической эксплуатации подшипнико-вых узлов наиболее предпочтительным является применение в них ПСМ. На сегодняшний день подшипники качения являются основными потребителями ПСМ.
Наиболее эффективно применение ПСМ в герметизиро-ванных подшипниковых узлах и в подшипниках, подверженных ударным нагрузкам.
Как правило, ограничением на применение ПСМ является окружная скорость, лимитируемая через параметр (d ·n) (d - внутренний диаметр подшипника, мм; n - частота вращения, об/мин).
При значении параметра d ·n, не превышающем допусти-мое значение [d ·n] целесообразно использовать ПСМ.
Допустимые значения параметра [d ·n], в зависимости от типа подшипника при среднем нагружении (нормальные контакт-ные напряжения не более 2 ·103 МПа) следующие:
Тип подшипника | [d ·n] |
Радиальный шариковый | 5 ·105 |
126
Радиально-упорный шариковый | 4 ·105 | |
Цилиндрический роликовый | 4 ·105 | |
Конический роликовый | 2 ·105 | |
Цилиндрический роликовый двухрядный | 5 ·105 | |
Упорный шариковый | n·( dh )1 / 2=0 , 810·5 | |
Игольчатый подшипник | n·dH =2 , 510·5 | |
Примечание: h - высота подшипника, мм; dH | - | наружный диаметр, оги- |
бающий иглы, мм. |
Величина допустимых значений [d ·n] снижается на:
- для тяжелонагруженных подшипников (контактные напря-жения до 5 ·103 МПа) – 25%;
- при вертикальном расположении подшипников – 25%;
- при вращении внешнего кольца – 50%;
- при спаренных подшипниках – 25%;
Контактные нормальные напряжения можно определять из зависимостей для:
шарикоподшипников | ||||||
R | 1 | 3 | ||||
σ k |
|
| ; | (8.1) | ||
= 1810 ⋅ | ||||||
Z ⋅ Dw |
роликоподшипников
σ k = 425 ⋅ | R ⋅∑ ρ | 0,5 | ; | |||
i ⋅ z ⋅l ⋅cos | α | |||||
где R – радиальная нагрузка, МН;
i - количество рядов тел качения; z - количество тел качения в ряду; Dw -диаметр ролика,м.;
l - длина ролика, м;
α - угол наклона роликов;
∑ ρ -сумма кривизны ролика и кольца.
∑ ρ = 2 / Dw(1 − γ ); γ = Dw / D0 *cos α;
D0 = (d + D) / 2 - средний диаметр подшипника.
Зубчатые зацепления
(8.2)
(8.3)
127
Основным смазочным материалом для зубчатых зацепле-ний являются минеральные масла. И только для открытых и ти-хоходных зубчатых передач (υ < 0,5 м/с) возможно использова-ние ПСМ. ТСМ для зубчатых зацеплений применяются в экстре-мальных условиях при температурах, превышающих 300 °С.
Для открытых зубчатых передач рекомендуется применять битумные композиции и ПСМ, характеристики которых приведе-ны в табл. 5, 6 прил. В.
Зубчатые муфты
В зубчатых муфтах наиболее эффективно применение вы-соковязких минеральных масел, но трудности по обеспечению герметичности в процессе эксплуатации зубчатых муфт побуж-дают применять ПСМ , а также битумные композиции, рекомен-дуемые для открытых зубчатых передач (например, 03П-1).
Направляющие скольжения
Наиболее эффективным и широко используемым видом смазочного материала являются минеральные масла.
8.3. Выбор марки минерального масла
8.3.1. Выбор марки минерального масла для подшипников скольжения
Основным свойством минеральных масел, определяю-щим возможность реализации режима жидкостной смазки, яв-ляется вязкость. Поэтому выбор марки минерального масла основывается на расчете требуемой вязкости при рабочей температуре узла трения.
Для практики эксплуатации подшипников скольжения необ-ходимую вязкость можно определять из зависимости (7.3)
ηt = Sо⋅ paω⋅ψ 2,
где ηt - динамическая вязкость при рабочей температуре, Па ·с; So -безразмерная величина,число Зоммерфельда;
pa -номинальное давление,Па;
128
ω - частота вращения вала, c−1 ;
ψ = ∆ / d - относительный диаметральный зазор;
d - диаметр вала.
Значение числа Зоммерфельда So находится из зависи-
мостей (7.3), (7.4) при подстановке в них оптимального значения относительной минимальной толщины масляной пленки ξ=0,35.
Для конструируемого подшипника скольжения величина относительно зазора ψ находится из соотношения
ψ =ψср =(∆min+ ∆max) / 2d ,
где ∆min , ∆max - минимальный и максимальный зазоры в поле до-
пуска принятой посадки.
Средняя рабочая температура масла в подшипнике сколь-жения определяется из зависимости:
t p = t вх + a* Р / 2d 2 , | (8.4) |
где tвx - температура масла, входящего в подшипник. Принима-
ется равной 40 - 60 °С | в зависимости от возможности теплоот- | |||||||
вода и нагруженности узла трения. | ||||||||
P -нагрузка на подшипник,МН; | ||||||||
d -диаметр вала,м; | ||||||||
a -коэффициент при давлении масла0,3МПа. | ||||||||
l −1,8 | l | −1 | ||||||
a =11,26⋅ |
| ⋅ 2,8 − |
| ; | (8.5) | |||
d | d |
При износе подшипника давление масла падает, и при его снижении менее 0,1 МПа значение коэффициента a возрастает в 1,5 раза, что ведет к снижению вязкости минерального масла.
Определив необходимую вязкость при рабочей темпера-туре, находим вязкость при эталонной температуре 40 или 50 °С для маловязких масел, или при 100 °С для высоковязких мине-ральных масел.
t | p | n | ||||
; | (8.6) | |||||
ηtэ = ηtp ⋅ | ||||||
tэ | ||||||
значение коэффициента n находим из зависимости
n = | 1 + lg | ν p | , | (8.7) | |
2 , 8 − lg | t p |
гдеν р - кинематическая вязкость масла при рабочей температу-ре;
129
tр - рабочая температура масла.
Выбрав необходимую марку смазочного материала из табл.1 прил. В, возможно найти характеристики подшипника скольжения (коэффициент надежности, максимально возможный диаметральный зазор, коэффициент трения и др.).
Пример 8.1.
Подобрать марку минерального масла для подшипников
скольжения | шестеренной | реверсивной | клети | кварто | ||
800/1400х2800. | ||||||
Исходные условия: | ||||||
момент прокатки | - | 2 МН ·м; | ||||
частота вращения валков | - 50 – 120 об/мин; | |||||
длина подшипника | - | 0,82 м; | ||||
диаметр подшипника | - | 0,6 м; | ||||
межцентровое расстояние | - | 1000 мм; | ||||
материал вала | - | сталь 40 ХН; | ||||
твердость поверхности вала | - | 50 - НRС; | ||||
материал подшипника | - | Б 16; | ||||
температура масла, входящего в подшипник - 50 °С; | ||||||
посадка подшипника | - | H8/e8. |
Решение Определим необходимую величину вязкости минерального
масла при рабочей температуре из зависимости (7.3)
ηt =60= So( pa / ω )ϕ2=0 , 44( 3⋅106 / 8,4 )⋅( 3,9⋅10−4 )2== 24 ⋅10−3 Па⋅с = 24 мПа⋅с.
Находим значения входящих в зависимость величин для l / d= 0,82 / 0,6 = 1,37
So =0 ,35( 0,43l / d +0, 24 )−1=0,35( 0,43⋅1,37+0, 24 )−1=0,44.
Номинальное давление в подшипнике
pa = (М· k) / dш ·d ·l ·cosα ) =(2 ·0,7) / (1 ·0,6 ·0,82 ·cos20) = 3
МПа, где М - момент прокатки, МН;
dш -диаметр шестеренного валка,м;α - угол зацепления, α=20°;
130
k - коэффициент перераспределения момента, передавае-мого через зубчатое зацепление (изменяется в пределах 0,5
...1,0).
ω = π * n / 30= π *80 / 30=8,34 c−1.
Среднее значение относительного диаметрального зазора для посадки ∅600 H8/e8
ψ = ( 0,329+0,135 ) / 2 ·600 = 3,9 ·10−4.
Определяем рабочую температуру по зависимости (8.4) t p = tbx + a ⋅ p / 2 d 2=50+4,47⋅1,48 / 2⋅0,62=60°C.
Из зависимости (8.5)
a =11,26(1,37)−1.8* (2,8−1,37)−1=4,47.
Нагрузка на подшипник
P = pa ⋅d ⋅l =3⋅0,82⋅0,6=1,48 МН.
Находим кинематическую вязкость минерального масла при эталонных температурах 40, 50 °С:
ν t=60 =ηt=60 / ρ = 24 / 0,9 = 26,7 мм2 / с;
ν 50 =ν60 *(60/50) n = 26,7(60 / 50)2,37 = 41,1 мм2 / c;
n = (1 + lgν) / (2,8 – lg t0 ) = (1 + lg 26,7) / (2,8 – lg 60) = 2,37;
ν40 = 26,7(60 / 40)2,37 = 75 мм2 / с.
Из табл. 1 прил. В выбираем И - 40 А или в соответствии с ГОСТ 17479.4 - 87 И-Г-А - 68.
8.3.2. Выбор марки минерального масла для подшипников качения
При выборе марки минерального масла для подшипнико-вого узла необходимо учитывать размеры подшипника и частоту его вращения, величину нагрузки, действующей на подшипник, рабочую температуру подшипникового узла и состояние окру-жающей среды.
Выбор необходимой вязкости минерального масла осуще-ствляется по номограммам на рис. 8.1. Марка минерального масла находится из табл. 1 прил. В.
Пример 8.2. Подобрать марку минерального масла для подшипников качения шестеренной клети стана 1700 горячей про-катки.
131
Исходные условия:
Частота вращения шестеренных валков - 500 об/мин; под-шипник -№ 97172; рабочая температура подшипника – 60 °С.
Решение.
Подшипник № 97172 роликовый, радиально-упорный, ко-нический, двухрядный с наружным диаметром D = 540 мм. Тогда средний диаметр Do = (d+D) / 2 = (360+540) / 2 = 450 мм.
По номограмме «а» на рис. 8.1 из точки, соответствующей Do = 450 мм проводим вертикаль до пересечения с наклонной линией n = 500 об /мин. Из точки пересечения проводим горизон-тальную линию до пересечения с осью ординат. Получаем
νt=60 = 12 мм2 / c.
По номограмме «б» рис. 8.1 находим вязкость минерально-го масла при эталонной температуре (40, 50 или 100 °С)
Из точки на оси ординат, равной 12 мм2/с, проводим гори-зонталь до пересечения с вертикалью, проведенной из точки 60 °С.
Из точки пересечения проводим прямую, параллельную ближайшей наклонной прямой, до пересечения с вертикалью, проведенной из точки (40, 50 или 100 °С).
Из полученной точки проводим горизонталь до пересече-ния с осью ординат. Находим:
ν50 =18 мм2 / c; ν40 = 28 мм2 / c.
Из табл. 1 прил. В выбираем марку минерального масла И–20 А ГОСТ 20799 – 88.
132
1000 | n | |||||||||||||||||||||||||
= | о | |||||||||||||||||||||||||
2 | ||||||||||||||||||||||||||
б/ | ||||||||||||||||||||||||||
м | ||||||||||||||||||||||||||
и | ||||||||||||||||||||||||||
500 | н | |||||||||||||||||||||||||
5 | ||||||||||||||||||||||||||
Up | 1 | |||||||||||||||||||||||||
200 | 2 | 0 | ||||||||||||||||||||||||
0 | ||||||||||||||||||||||||||
5 | ||||||||||||||||||||||||||
100 | 0 | |||||||||||||||||||||||||
1 | ||||||||||||||||||||||||||
0 | ||||||||||||||||||||||||||
50 | 2 | 0 | ||||||||||||||||||||||||
00 | ||||||||||||||||||||||||||
5 | ||||||||||||||||||||||||||
0 | ||||||||||||||||||||||||||
20 | 1 | 1 | 0 | |||||||||||||||||||||||
5 | ||||||||||||||||||||||||||
0 | 0 | |||||||||||||||||||||||||
3 | 0 | 0 | ||||||||||||||||||||||||
0 | ||||||||||||||||||||||||||
0 | 2 | |||||||||||||||||||||||||
0 | ||||||||||||||||||||||||||
0 | 0 | |||||||||||||||||||||||||
1 | 0 | |||||||||||||||||||||||||
5 | 0 | |||||||||||||||||||||||||
10 | 0 | |||||||||||||||||||||||||
00 | 00 | |||||||||||||||||||||||||
0 | 0 | |||||||||||||||||||||||||
2 | ||||||||||||||||||||||||||
0 | ||||||||||||||||||||||||||
0 | ||||||||||||||||||||||||||
5 | 5 | 0 | ||||||||||||||||||||||||
0 | ||||||||||||||||||||||||||
0 | ||||||||||||||||||||||||||
0 | ||||||||||||||||||||||||||
0 | ||||||||||||||||||||||||||
0 | ||||||||||||||||||||||||||
3 10 | 20 | 50 | 100 | 200 | 5001000 | |||||||||||||||||||||
n=100000 об/мин | D0, мм | |||||||||||||||||||||||||
а | ||||||||||||||||||||||||||
450 | ||||||||||||||||||||||||||
260 | ||||||||||||||||||||||||||
170 | ||||||||||||||||||||||||||
100 | ||||||||||||||||||||||||||
70 | ||||||||||||||||||||||||||
50 | ||||||||||||||||||||||||||
40 | ||||||||||||||||||||||||||
Up | 30 | |||||||||||||||||||||||||
20 | ||||||||||||||||||||||||||
10 | ||||||||||||||||||||||||||
9 | ||||||||||||||||||||||||||
8 | ||||||||||||||||||||||||||
7 | ||||||||||||||||||||||||||
6 | ||||||||||||||||||||||||||
5 | 30 | 40 | 50 | 60 | 70 | 80 | 90 | 100 | 110 | 120 | ||||||||||||||||
20 | ||||||||||||||||||||||||||
б | t,0C | |||||||||||||||||||||||||
а | б | |||||||||||||||||||||||||
Рис.8.1. Номограммы для выбора масла с вязкостью, соответствующей заданным условиям эксплуатации
8.3.3. Выбор марки минерального масла для зубчатых зацеплений
133
На выбор марки минерального масла для зубчатых пере-дач оказывают влияние: температурный режим (50 – 130 °С), ок-ружная скорость, нормальные контактные напряжения в зоне контакта, твердость и состояние контактирующих поверхностей.
Как правило, для легко- и средненагруженных зубчатых передач применяют индустриальные масла без присадок.
В легконагруженных зубчатых зацеплениях нормальные контактные напряжения не превышают 800 МПа при окружной скорости до 100 м/с, в средненагруженных зубчатых зацеплени-ях соответственно 1200 МПа и 10 - 15 м/с. Для более тяжелых условий работы используют индустриальные масла с противоиз-носными и противозадирными присадками табл. 2 прил. В.
Определение необходимой вязкости минерального масла для стальных зубчатых передач производится по графику на рис. 8.2. в зависимости от параметра x
HV ⋅ p2
x = max ; (8.8)
υ ⋅105
где HV - твердость по Виккерсу, МПа;
pmax-максимальное нормальное контактное напряжение,МПа;
υ - окружная скорость,м/с.
Для нахождения твердости по Виккерсу, зная значение
твердости по Роквеллу, можно пользоваться зависимостью:
HV = 1,86 ⋅106 ⋅(110 − HRC)−2 ; | (8.9) | |||||||||
Наибольшее нормальное контактное напряжение для: | ||||||||||
цилиндрических прямозубых зацеплений | ||||||||||
p2 | = 9,5 ⋅104 | (u +1)3 ⋅ K ⋅M k | ; | (8.10) | ||||||
max | u2⋅ A2⋅b | |||||||||
цилиндрических косозубых и шевронных зацеплений | ||||||||||
p2 | = 7,5 ⋅104 | (u +1)3 ⋅ K ⋅M k | ; | (8.11) | ||||||
| ||||||||||
max | u2⋅ A2⋅b | |||||||||
конических зацеплений | ||||||||||
p2 | = 5 , 3 ⋅106 | u ⋅ K ⋅ M k | , | (8.12) | ||||||
max | d 3 | |||||||||
ek | ||||||||||
где u - передаточное число;
134
A - межцентровое расстояние, м; b - ширина зубчатого венца, м;
dek - диаметр внешней делительной окружности (на допол-
нительном конусе), м;
k - коэффициент, равный 1,3...1,5 (меньшие значения следу-ет выбирать при расположении колес на валах, близком к сим-метричному; большие значения - при несимметричном располо-жении колеса);
Mk - крутящий момент на колесе, МН ·м.
Верхний предел вязкости (рис. 8.2) принимается при сле-дующих условиях:
- изготовление обеих зацепляющихся шестерен из одной марки или хотя бы одной из шестерен из никелевой или хромо-никелевой стали со сквозной закалкой;
- работа передачи с ударными нагрузками;
- температура окружающего воздуха выше 25 °C.
Нижний предел (меньшее значение вязкости) при:
- высокой точности обработки шестерен (не менее 6-й сте-пени точности);
- температуре окружающего воздуха ниже 10 °C;
- фосфатированной или сульфидированной шестерни;
- параметре x > 100.
Пример 8.3. Подобрать марку минерального масла для зубчатого зацепления шестеренной клети кварто 800 / 1400 х 2800.
Исходные данные: | ||||
момент прокатки | - | 2 МН ·м; | ||
межцентровое расстояние | - | 1000 мм; | ||
частота вращения | - | 50-120 об/мин; | ||
длина шестеренного валка | - | 1700 мм; | ||
материал шестеренных валков | - | сталь 40 ХН; | ||
твердость поверхности зубъев | - | HRC 50. | ||
Решение. | ||||
Определяем параметр x | ||||
x = HV ⋅ Pmax2 | 5 | = 517 ⋅ 4 ,6 ⋅105 | 5 = 907. | |
υ ⋅10 | 2,62 ⋅10 |
HV =1,86⋅106 (110− HRC )−2=1,86⋅106(110−50 )−2=517.
Для шевронных зацеплений
135
P 2 | =7 ,5⋅104 ( u +1 )3⋅ k ⋅ Mk | 2 | 2 | = 7 ,5 ⋅104 23 ⋅ 1, 3 ⋅1 | 2 | = 4,6 ⋅105. | |||||||||
max | u | ⋅ | A | ⋅b | 2 | ⋅1,7 | |||||||||
1 | ⋅1 | ||||||||||||||
υ = πdn / 60= ( 3,14⋅1⋅50 ) / 60=2,6 м / с. | |||||||||||||||
Так как шестеренные валки изготовлены из хромоникеле- | |||||||||||||||
вой стали, то значение вязкости находим по верхней кривой . | |||||||||||||||
Значению параметра x =907 соответствует значение кине- | |||||||||||||||
матической вязкости ν50 =190 | мм2 / c. | ||||||||||||||
Найдем значения кинематической вязкости при эталонных | |||||||||||||||
температурах 100 и 40 °С. | |||||||||||||||
ν 100= ν 50( 50 / 100 )n | =190 ⋅0,52 ,91 = 25 | мм2 / с; | |||||||||||||
n = ( 1+ lgν p ) /( 2,8− lg tp ) = (1+ lg190 ) /( 2,8− lg 50 ) =2,91; | |||||||||||||||
ν 40= ν 50( 50 / 40 )n | =190 ⋅1,252 ,91 = 364 | мм2 / c. | |||||||||||||
Так | как | контактные | нормальные | напряжения |
Pmax =4 , 610·5=678МПа< 800МПа,то выбираем минеральноемасло без присадок П-28 ГОСТ 6480 –78 или ИГП-182 ТУ 38 101413-78. По новой классификации И-Т-А- 460 или И-Т-С- 320.
136
137 |
Рис.8.2. Зависимость вязкости минерального масла от параметра x
8.3.4. Выбор марки минерального масла для червячных передач
Необходимую вязкость минерального масла для червяч-ных передач определяют по номограмме на рис. 8.3 в зависимо-
сти от отношения Ks / ν , определяемого из зависимости:
Ks | = | M | ; | (8.13) | |
ν | A3⋅n |
где М - крутящий момент на червячном колесе, Н ·м; А - межосевое расстояние, м;
n - частота вращения червяка, мин−1 .
По найденному значению вязкости ν40 при t = 40 °С выби-
рают марку минерального масла. Как правило, вязкость высоко-вязких минеральных масел в таблицах приводится при t = 100 °С. Поэтому вязкость νt =100 находят из зависимостей (7.12) и (7.13), а
затем из табл. 3,4 прил.В выбирают марку минерального масла.
V мм2/с | |||||
4p | |||||
1200 | |||||
800 | |||||
400 | |||||
0 | 102 | 103 | 104 | 105 | |
10 | |||||
K fv, H*мин/м2 | |||||
1 |
Рис. 8.3. Определение вязкости минерального масла для червячных передач
Пример 8.4. Подобрать марку минерального масла для червячного редуктора механизма подъема штабелировочного
стола. | ||
Исходные данные: | ||
крутящий момент на червячном колесе - | 50 кН ·м; | |
межосевое расстояние | - | 0,625 м; |
138
частота вращения червяка | - 560 мин−1 . |
Решение. | |
Определяем параметр K s / ν | |
K s / ν = M / A3 n =50⋅103 / 0,6253⋅560=4023. | |
По номограмме рис. 8.З находим | ν40=570 мм2 / c. |
Для высоковязких минеральных масел в таблице значения вязкости даны при эталонной температуре tэт=100°С
Находим
ν 100= ν 40( 40 / 100 )n =570⋅( 40 / 100 )3 ,14=32 мм2 / c. n = (1+ lgν40 ) /( 2,8− lg 40 ) =3,14.
Из табл. 3 прил. В выбираем минеральное масло цилинд-
ровое - 38 ГОСТ 6411 - 76.
Задачи
Каждая задача имеет 4 варианта (1, 2, 3, 4). Первый вариант (1.1) - исходные условия задачи.
Второй вариант (1.2) - в исходных условиях скорость сколь-жения или частота вращения принимаются меньшими в 2 раза.
Третий вариант (1.3) - в исходных условиях скорость сколь-жения или частота вращения принимаются меньшими в 1,5 раза, а нагрузка в контакте - в 1,5 раза большей.
Четвертый вариант (1.4) - в исходных условиях скорость скольжения или частота вращения принимается меньшими в 3 раза.
Задача1. Подобрать смазочный материал для подшипниковскольжения клети Дуо сортового стана «350».
Исходные данные: | ||
давление металла на валки | - 0,7 МН; | |
частота вращения валков | - | 600 об./мин; |
внутренний диаметр подшипника | - | 250 мм; |
длина подшипника | - | 200 мм; |
посадка подшипника | - E9/h8. |
Задача2. Подобрать смазочный материал для подшипниковкачения валков №777752 клети кварто 500/1300×1200.
Исходные данные:
139
давление металла на валки | - 20 МН; |
скорость прокатки | - 30 м/с; |
смещение оси рабочих валков | |
относительно опорных | - 10 мм. |
Задача3. Подобрать смазочный материал для ПЖТ опорныхвалков со следующими параметрами: d = 900 мм, l = 700 мм, по-садка подшипника E8/h8.
Исходные данные задачи 2.
Задача4. Подобрать смазочный материал для ПЖТ валковклети Дуо 250 проволочного стана «250».
Исходные данные: | |
давление металла на валки | - 0,4 МН; |
скорость прокатки | - 40 м/с; |
внутренний диаметр втулки | - 180 мм; |
длина подшипника | - 150 мм; |
посадка подшипника | - E9/h8. |
Задача5. Подобрать смазочный материал для двухступен-чатой цилиндрической передачи нажимного механизма клети кварто 800/1500 × 2800.
Исходные данные: | |
передаваемая мощность | - 100 кВт; |
частота вращения шестерни I ступени | - 730 об/мин; |
межцентровое расстояние I ступени | - 190,9 мм; |
межцентровое расстояние II ступени | - 1092 мм; |
передаточное число I ступени | - 5.35; |
передаточное число II ступени | - 2.15; |
ширина зубчатого венца I ступени | - 195 мм; |
ширина зубчатого венца II ступени | - 280 мм; |
материал зубчатых колес | - Сталь 40ХН. |
Задача6. Подобрать смазочный материал для комбиниро-ванного редуктора шестеренной клети дрессировочного стана кварто 600/1500 × 2500.
Исходные данные:
передаваемая мощность - 260 кВт; наибольший крутящий момент на
140
выходных шестеренных валках - 2×25 кН ·м;
I ступень - z1 = 37, z2 = 104, mН = 7 мм, mS =7,07 мм,
β =8°06′34″;
II ступень - z1 = 35, z2 = 124, mН = 10 мм, mS =10,1 мм,
β =8°06′34″;
Шестеренная пара - z1 = z2 = 25, mS =20 мм, β =30°;
скорость прокатки - 2,5 м/с;
ширина зубчатого венца I ступени - 200 мм;
ширина зубчатого венца II ступени - 320 мм;
ширина зубчатого венца III ступени - 400 мм;
I ступень
материал шестерни - Сталь 40ХН;
материал колеса - Сталь 30
ХГСН.
II ступень
материал шестерни - Сталь 40ХН;
материал колеса - Сталь 30
ХГСН.
III ступень
материал шестеренных валков - Сталь 40ХН.
Задача7. Подобрать смазочный материал для подшипниковскольжения эксцентрикового вала ножниц усилием 20 МН сля-
бинга «1150».
Исходные данные: | ||
число полных ходов в минуту | - 12; | |
диаметр подшипника | - 1200 мм; | |
длина подшипника | - | 450 мм; |
температура подшипника | - | 80°С. |
Задача8. Подобрать смазочный материал для подшипни-ков качения № 2097152 барабана летучих ножниц 0,25 - 0,6 × 1000 мм.
Исходные данные:
скорость разрезаемой полосы - 1,5 - 5,0 м/с;
диаметр окружности режущей части ножей - 500 мм.
Задача9. Подобрать смазочный материал для подшипниковкачения № 777/620 рабочих валков клети кварто 1100/1600 × 3200.
141
Исходные данные:
давление металла на валки - 30 МН;
скорость прокатки - 1 м/с;
температура подшипника - 70°С;
смещение оси рабочих валков
относительно опорных - 10 мм.
Задача10. Подобрать смазочный материал для подшипни-
ков качения № 77788 клети Дуо 850 × 2000.
Исходные данные:
давление металла на валки - 7 МН;
скорость прокатки - 1 м/с;
Задача11. Подобрать смазочный материал для ПЖТ опор-ных валков клети кварто 1100/1600 × 3200.
Исходные данные:
давление металла на валки - 30 МН;
скорость прокатки - 1 м/с;
внутренний диаметр втулки подшипника - 1000 мм;
длина подшипника - 750 мм;
посадка подшипника - E9/h8.
Задача12. Подобрать смазочный материал для подшипни-ков качения № 771/500 валков вертикальной клети широкополос-ного стана «1700».
Исходные данные:
давление металла на валки - 2 МН;
частота вращения валков - 20 об/мин;
температура подшипника - 70°С.
Задача13. Подобрать смазочный материал для подшипни-ков качения № 1077756 рабочих валков клети кварто 600/1500 × 2500 холодной прокатки.
Исходные данные: | |
давление металла на валки | - 35 МН; |
скорость прокатки | - 21 м/с; |
смещение оси рабочих валков | |
относительно опорных | - 6 мм; |
142
температура подшипника | - 60°С. |
Задача14. Подобрать смазочный материал для подшипни-ков качения № 777/660 валков клети кварто 500/130 × 1700.
Исходные данные:
давление металла на валки - 18 МН;
скорость прокатки - 7 м/с;
температура подшипника - 60°С.
Задача15 . Подобрать смазочный материал для подшипни-ка скольжения в устройстве уравновешивания шпинделей чисто-
вой клети широкополосного стана «2000». | |
Исходные данные: | |
масса шпинделя | - 15850 кг; |
расстояние от оси головки шпинделя со стороны | |
шестеренной клети до опорного подшипника | - 3200 мм; |
длина шпинделя | - 8000 мм; |
частота вращения шпинделя | - 120 об/мин; |
внутренний диаметр втулки подшипника | - 470 мм; |
посадка подшипника | - E9/h8; |
коэффициент переуравновешивания шпинделей | - 1,2. |
Задача16. Подобрать смазочный материал для вкладышейголовки шпинделей чистовой клети широкополосного стана
«2000». | |
Исходные данные: | |
передаваемый крутящий момент | - 2 кН ·м; |
максимальный угол наклона шпинделя | - 1°20′; |
длина шпинделя | - 8000 мм; |
длина контактной поверхности вкладышей | - 250 мм; |
диаметр контактной поверхности вкладышей | - 550 мм; |
ширина вкладышей | - 300 мм; |
материал вкладышей | - БрАЖМц 10-3- |
1,5. |
Задача17. Подобрать смазочный материал для подшипни-ков качения №1097992 шестеренной клети с межосевым рас-стоянием А= 700 мм.
Исходные данные:
передаваемый крутящий момент - 0,5 кН ·м;
143
частота вращения | - 400 |
об/мин; |
Задача18. Подобрать смазочный материал для подшипниковкачения № 97172 шестеренной клети А = 650 мм клети кварто
660/1300 × 1700.
Исходные данные: | |
максимальный крутящий момент | |
на приводном валу | - 100 кН ·м; |
частота вращения | - 500 |
об/мин; | |
длина шестеренного валка | - 1400 мм; |
материал шестеренных валков | - Сталь |
60Х2МФ. |
Задача19. Подобрать смазочный материал для зубчатого заце-пления шестеренной клети А = 650 мм рабочей клети кварто
660/1300 × 1700.
Исходные данные:
максимальный крутящий момент
на приводном валу - 100 кН ·м;
частота вращения - 500 об/мин;
длина шестеренного валка - 1500 мм;
материал шестеренных валков - Сталь
30Х2ГМТ.
Задача20. Подобрать смазочный материал для цилиндрическо-го двухступенчатого редуктора ЦД-4000.
Исходные данные: | ||
крутящий момент на ведущем валу | - 100 кН ·м; | |
частота вращения | - 500 | |
об/мин; | ||
I ступень - z1 = 32, z2 = 168, mS = 16, mН = 14; | ||
II ступень - z1 = 36, z2 = 164, mН = 24; β =30°; | - 600 мм; | |
ширина зубчатого венца I ступени | ||
ширина зубчатого венца II ступени | - 950 мм. |
144
Задача21. Подобрать смазочный материал для вкладышейуниверсального шпинделя клети кварто 600/1500 × 2500 стана холодной прокатки.
Исходные данные: | ||
передаваемый крутящий момент | - 200 кН ·м; | |
частота вращения шпинделя | - 800 | |
об/мин; | - 0°21′; | |
максимальный угол наклона шпинделя | ||
длина контактной поверхности вкладышей | - 150 мм; | |
диаметр контактной поверхности вкладышей | - 230 мм; | |
ширина контактной поверхности вкладышей | - 160 мм. |
Задача22. Подобрать смазочный материал для подшипни-ков качения № 7616 универсального шпинделя дрессировочного стана кварто 600/1500 × 2500.
Исходные данные: | |
передаваемый крутящий момент | - 50 кН ·м; |
частота вращения шпинделя | - 800 |
об/мин; | |
расстояние между подшипниками вилки | - 240 мм; |
максимальный угол наклона шпинделя | - 8°; |
температура подшипника | - 50°С. |
Задача23. Подобрать смазочный материал для зубчатогозацепления шестеренной клети с межцентровым расстоянием А
= 1000 мм.
Исходные данные: | |
крутящий момент со стороны электродвигателя | - 100 кН ·м; |
частота вращения | - 50-120 |
об/мин; | |
длина шестеренного валка | - 1700 мм; |
материал шестеренных валков | - Сталь |
40ХН. |
Задача24. Подобрать смазочный материал для зубчатойцилиндрической передачи нажимного механизма блюминга
«1150».
Исходные данные:
145
передаваемая мощность | - 270 кВт; |
частота вращения шестерни I ступени | - 500 об/мин; |
межцентровое расстояние I ступени | - 667 мм; |
межцентровое расстояние II ступени | - 1092 мм; |
передаточное число I ступени | - 4,5; |
передаточное число II ступени | - 1,0; |
ширина зубчатого венца I ступени | - 95 мм; |
ширина зубчатого венца II ступени | - 190 мм; |
материал зубчатых колес | - Сталь |
35ХНВ. |
Задача25. Подобрать смазочный материал для подшипникакачения № 2097152 ролика приемного рольганга слябинга
«1150». | |
Исходные данные: | |
масса слитка | - 30 т; |
окружная скорость роликов | - 1,5 м/с; |
температура подшипников | - 90°С. |
Задача26. Подобрать смазочный материал для двухступен-чатой цилиндрической передачи привода роликов рольганга хо-
лодильника. | |
Исходные данные: | |
передаваемая мощность | - 45 кВт; |
частота вращения ведущего вала I ступени | - 580 |
об/мин; | |
I ступень | |
межцентровое расстояние | - 450 мм; |
передаточное число | - 3,74; |
ширина зубчатого венца | - 180 мм; |
материал | - Сталь |
40ХН; | |
II ступень | |
межцентровое расстояние | - 480 мм; |
передаточное число | - 1,61; |
ширина зубчатого венца | - 200 мм; |
материал | - Сталь |
40ХН. |
146
Задача27. Подобрать марку минерального масла для чер-вячного редуктора механизма опрокидывания люльки слитково-за.
Исходные данные: | |
крутящий момент на червячном колесе | - 220 кН ·м; |
межосевое расстояние | - 0,6 м; |
частота вращения червяка | - 300 мин -1. |
Задача28. Подобрать марку минерального масла для гло-боидного редуктора нажимного механизма блюминга «1500».
Исходные данные: | |
крутящий момент на глобоидном колесе | - 6 МН ·м; |
межосевое расстояние | - 0,9 м; |
частота вращения глобоидного червяка | - 100 мин - |
1. |
147
Библиографический список
1. Байхельт Ф., Фринкен П. Надежность и техническое обслужи-вание. Математический подход: Пер. с нем. М.: Радио и связь, 1985.
2. Белевский Л.С., Жиркин Ю.В., Анцупов В.П. Основы трибо-техники и методы упрочения деталей металлургического обо-рудования: Учеб. пособие. Магнитогорск: МГМИ, 1989. 94 с.
3. Временное положение о техническом обслуживании и ремон-тах (ТО и Р) механического оборудования предприятий сис-темы Министерства черной металлургии СССР. Тула. 1983, 389 с.
4. Гребеник В.М., Цапко В.К. Надежность металлургического оборудования (оценка эксплуатационной надежности): Спра-вочник. М: Металлургия, 1980. 344 с.
5. Гребеник В.М., Гордиенко А.В., Цапко В.К. Повышение на-дежности металлургического оборудования: Справочник. М.: Металлургия, 1988. 688 с.
6. Жиркин Ю.В. Сборник задач и упражнений по курсу «Надеж-ность, ремонт и монтаж металлургических машин»: Учеб. по-собие. Свердловск.: УПИ, 1986. 85 с.
7. Жиркин Ю.В. Надежность металлургических машин. Ч.1: Ос-
новы теории надежности: Учеб. пособие. Магнитогорск:
МГМИ, 1994. 52 с
8. Жиркин Ю.В. Надежность металлургических машин. Ч.2: Экс-плуатационная надежность. Оценивание показателей безот-казности: Учеб. пособие. Магнитогорск: МГМА, 1995. 60 с.
9. Жиркин Ю.В. Надежность металлургических машин. Ч.3: Тех-ническое обслуживание и ремонт: Учеб. пособие. Магнито-горск: МГМА, 1996. 60 с.
10. Жиркин Ю.В. К расчету осевых усилий в валковой системе прокатных клетей кварто // Изв. вузов. Черная металлургия. 1981. № 10. С. 156-158.
11. Жиркин Ю.В. Технология и особенности монтажа металлур-гических машин. Свердловск: УПИ, 1985. 90 с.
12. Жиркин Ю.В. Надежность, эксплуатация, техническое обслу-живание и ремонт металлургических машин. Магнитогорск:
МГТУ, 1998. 331 с.
13. Капур К., Ламберсон Л. Надежность и проектирование сис-тем: Пер. с англ.. М.: Мир, 1980. 604 с.
14. Надежность и эффективность в технике: Справочник: В 10 т./ Ред. совет: B.C. Авдуевский (пред.) и др. М.: Машинострое-ние, 1987. Т.2.: Математические методы в теории надежности
148
и эффективности / Под ред. Б.В. Гнеденко. 260 с.
15. Надежность и эффективность в технике: Справочник: В 10 т./ Ред. совет: B.C. Авдуевский (пред.) и др. М.: Машинострое-ние, 1989. Т.6.: Эксплуатация и ремонт / Под ред. В. И. Кузне-цова и К.Ю. Барзиловича. 320 с.
16. Надежность машиностроительной продукции: Практическое руководство по нормированию, подтверждению и обеспече-нию. М.: Изд-во стандартов, 1990. 328 с.
17. Надежность технических систем: Справочник / Ю.К. Беляев, В.Н. Богатырев, В.В. Блотин и др.; Под ред. И.А. Ушакова М.: Радио и связь, 1985. 608 с.
18. Орлов П.И. Основы конструирования: Справочно-методическое пособие: В 2 кн./ Под ред. П.Н. Усачева. 3-е изд., испр. М.: Машиностроение, 1985. 544 с.
19. Проников А.С. Надежность машин. М.: Машиностроение, 1978. 542 с.
20. Трение, изнашивание и смазка: Справочник: В 2 кн./ Под ред. И.В.Крагельского, В.В. Алисина. М.: Машиностроение, 1978.
Кн. 1. 400 с.
149
150
Приложение А
Дата добавления: 2018-05-12; просмотров: 3282; Мы поможем в написании вашей работы! |
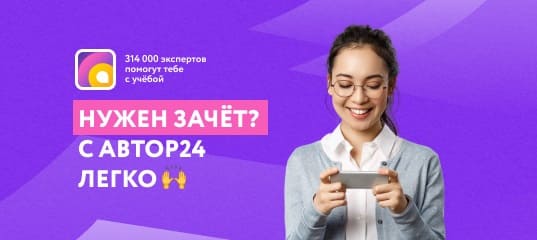
Мы поможем в написании ваших работ!