Вторая часть технологического процесса изготовления дисков
(операции №70…160) предусматривают формирование основных рабо-
чих поверхностей. В этой части технологического процесса произво-
дятся фрезерование пазов и скосов на базовых поверхностях диска,
протягивание профиля пазов для установки лопаток, обработка отвер-
стия для фиксации лопаток в диске и др.
На рис. 4.6 представлены основные операции второй части техноло-
гического процесса. Для выполнения используются основные базовые
поверхности: центральное отверстие (поверхность Б), торцы обода дис-
ка, а для углового ориентирования положения заготовки в технологиче-
ской системе – нулевое отверстие диаметром (13,5 +0,035) мм.
На операции №70 осуществляется фрезерование пазов по всей обра-
зующей внутреннего контура (число пазов 30). Для выполнения данной
операции используется вертикально-фрезерный станок с ЧПУ (мод.
МА655СА). Обработка ведется при следующих режимах: n = 220 мин-1
(V = 7 м/мин.) и подаче Sм = 70 мм/мин., режущий инструмент выпол-
няется из инструментального сплава Р9К5.
159
Рис. 4.6. Вторая часть технологического процесса
Изготовления дисков первой ступени турбины
160
|
Данная операция выполняется на настроенном станке по разрабо-
танной программе концевой фрезой диаметром 11…9 мм. Режущий ин-
струмент врезается на глубину 5,5 мм и осуществляет круговое движе-
ние на диаметре 529 мм. При достижении ширины паза равной 58 мм
|
|
фреза отводится от заготовки. После этого осуществляется перемеще-
ние фрезы на холостом ходу (Sм = 250 мм/мин) в рабочее положение
для обработки второго паза и т.д.
Этой же фрезой осуществляется обработка трех пазов на усиленном
пояске диска. При обработке данных пазов выполняются операционные
размеры (на рис. 4.6. не показан) и (12±0,5 мм).
На операции № 75 производится фрезерование пазов с другой сто-
роны диска. При этом также используется станок с ЧПУ мод.
МА655СА.
Контроль выполнения геометрических параметров в этой части тех-
нологического процесса производится периодически с помощью уни-
версального и специального контрольно-измерительного инструмента,
так как расположение контура пазов обеспечивается технологически за
счет применения специального станочного приспособления и управ-
ляющей программы станка. Станочное приспособление периодически
контролируется и паспортизуется.
Операция №80 - фрезерование 12 пазов, расположенных на конус-
ной образующей диска, на горизонтально-фрезерном станке мод.
FV-40В. При выполнении этой операции используется специальное по-
воротное приспособление, ось которого повернута в пространстве. Это
|
|
приспособление позволяет обеспечить необходимое угловое располо-
жение пазов на диске.
Слесарная обработка (операция №85) заключается в зачистке острых
кромок и скруглении радиусов переходов различных поверхностей. Для
выполнения этой операции используются инструментальные шарошки,
шлифовальные круги и шлифовальные шкурки. Для создания движения
инструмента применяются высокоскоростные пнемошлифовальные
головки.
Операция №100 – протягивание пазов наиболее важная операция
данной части технологического процесса (рис. 4.6.). От качества вы-
полнения данной операции зависят основные показатели работы диска
и всего колеса турбины. Надежность исполнения параметров пазов в
заготовке на этой операции определяются режущим инструментом,
применяемым оборудованием и назначенными режимами протягива-
ния.
161
Эта операция выполняется на горизонтально-протяжном станке мод.
7Б56У. При протягивании применяется специальное поворотное при-
способление с пневмогидравлическим закреплением заготовки и под-
вижной частью этого приспособления. Протягивание проводится сбор-
ными фасонными протяжками, которые устанавливаются и точно ори-
ентируются в технологической системе. Перемещение протяжек вы-
|
|
полняется по специальным направляющим корпуса станочного приспо-
собления.
Перед выполнением этой операции производится протягивание паза
на технологическом образце (операция №90), который подвергается
тщательному контролю всех геометрических параметров и качества
обработанных поверхностей.
На основании полученных результатов контроля технического об-
рзца, дается заключение о соответствии качества с заданным. Это за-
ключение определяет возможность проведения операции №100 на ра-
бочем диске турбины.
При протягивании пазов заготовка ориентируется в технологической
системе по основным базовым поверхностям. Протягивание всех (83)
пазов производится предварительной протяжкой, затем протяжками
2,3,4. Последняя протяжка формирует окончательный профиль пазов в
диске. На этом этапе обеспечиваются:
1) базовая плоскость паза (см. рис. 4.1) и ее положение относитель-
но технологических установочных поверхностей;
2) угол профиля впадины замка φ (52°30′±5′);
3) угол расположения профиля паза относительно базовой плоско-
сти (α = 7°30′±5′);
4) шаг зубьев паза h1 = (3,15±0,01) мм, h2 = (6,3±0,01) мм,
h3 = (9,45±0,01) мм, h4 = (12,6±0,01) мм;
|
|
5) ширина пазов В1 = (14,19+0,12) мм, В2 = (12,56+0,12) мм,
В3 = (10,93+0,12) мм, В4 = (9,3+0,12) мм;
6) угол расположения паза относительно оси диска 8°±10′;
7) точность расположения левой и правой части паза относительно
друг друга в осевом направлении 0,02 мм.
Поворотное делительное приспособление и сборная протяжка обес-
печивают также точность расположения пазов относительно техноло-
гически базовых поверхностей в осевом и радиальном направлении и
относительно друг друга. Расстояние базовой плоскости (рис. 4.1, 4.6)
до оси диска (334,4±0,15) мм. На этой операции выполняется располо-
162
жение пазов относительно друг друга и относительно оси диска. Вели-
чина допустимого смещения при этом должна быть не более 0,08 мм.
С целью обеспечения этих заданных значений показателей качества
заготовок перед выполнением операции №100 производится тщатель-
ная выверка и контроль станочного приспособления.
Протягивание пазов производится при скорости протяжки
v = 1,2 м/мин. Для достижения высоких показателей по шероховатости
поверхностей (Ra = 2,5мкм) при протягивании обеспечивается обильное
охлаждение и смазывание поверхностей, подвергающихся обработке. В
процессе протягивания осуществляется тщательный контроль над уда-
лением стружки из зоны обработки.
На рис. 4.7 представлена схема протягивания пазов в дисках турби-
ны. Приспособление 2 (рис. 4.7,а) устанавливается и закрепляется на
корпусе станины 1 протяжного станка. Корпус 3 поворотной части ста-
ночного приспособления развернут к оси паза диска турбины на угол α.
Заготовка 6 центрируется в технологической системе по пояску ц и
фиксируется по отверстию ф (рис. 4.7,б).
Опорная поверхность заготовки размещается в непосредственной
близости от места приложения силы протягивания Рпр. Делительный
диск 5 приспособления и заготовка 6 после протягивания паза произво-
дят поворот на шаг. Перед этим выполняется подъем заготовки совме-
стно с делительным диском на высоту Н и перемещение протяжки 7 в
крайнее правое положение. Поворот делительного диска фиксируется
специальным устройством 4. Подъем и поворот заготовки выполняются
в полуавтоматическом режиме специальной гидравлической системой.
После протягивания всех пазов в диске турбины осуществляется
смена сборной протяжки 7.
В направляющие элементы 8 станочного приспособления 2 устанав-
ливается следующая сборная протяжка. Последняя, чистовая протяжка
формирует основные показатели профиля паза.
От качества заточки, настройки сборной протяжки, от режимов об-
работки, величины удаляемого слоя металла при протягивании, от сте-
пени охлаждения зоны обработки и других факторов зависят качест-
венные показатели паза.
163
Рис. 4.7. Схема протягивания пазов в дисках турбины
164
|
Точность расположения паза диска относительно оси установоч-
ной поверхности ц зависит от составляющих производственных по-
грешностей. На представленной схеме (рис. 4.7,в) суммарный вектор
смещения Ä ∑см этих осей относительно друг друга определяется сум-
мой составляющих векторов:
Ä ∑см= Ä0 + Ä1 + Ä2 + Ä3 + Ä4 ,
где Ä 0 – вектор смещения оси паза диска, относительно оси установоч-
ного базового элемента приспособления. Эта погрешность обработки
определяется процессом резания металла при протягивании; Ä 1 – век-
тор смещения оси режущих элементов протяжки относительно устано-
вочных поверхностей подвижного блока сборной протяжки. Эта по-
грешность возникает в процессе изготовления или переточки сборной
протяжки; Ä 2 – вектор смещения оси подвижного блока протяжки от-
носительно направляющих элементов станочного приспособления. Это
смещение определяется возможным зазором между направляющими
элементами станочного приспособления и сборной протяжки; Ä 3 –
вектор смещения направляющих элементов станочного приспособле-
ния относительно установочного (центрирующего) элемента этого при-
способления; Ä 4 – вектор смещения установочной поверхности заго-
товки относительно установочного элемента станочного приспособле-
ния. Погрешность установки заготовки на станочном приспособлении
определяется возможным зазором между заготовкой и установочным
элементом приспособления.
Предельное суммарное поле рассеяния модуля вектора смещения
±ρ∑см оси паза относительно оси диска определяется суммой полей рас-
сеивания составляющих элементов:
±ρ∑см= ±( ρ0+ ρ1+ ρ2+ ρ3+ ρ4).
В примере эта величина не должна превышать заданного смещения
паза относительно оси диска ±0,08 мм.
Определим вероятные ожидаемые значения суммарного поля рас-
сеивания модуля вектора ±ρ∑см [10,14,15].
По известным предельным значениям составляющих векторов, при-
нятым в соответствии с чертежной сборной протяжки и станочного
приспособления, учитывая используемые в операции методы проверки
положения детали в технологической системе, определим наиболее ве-
165
роятные ожидаемые значения смещений осей пазов диска относительно
номинального положения.
Известны: ρ0=(0 ±0,01) мм; ρ1=(0± 0,01) мм; ρ2=(0 ±0,015) мм;
ρ3=(0 ±0,01) мм; ρ4=(0 ±0,025) мм;
Тогда предельная величина смещения
±ρ∑см = ±0,01±0,01±0,015±0,01±0,025 = ±0,07 мм.
Коэффициент теоретико-вероятностного суммирования К производ-
ственных погрешностей позволяет определить наиболее вероятное зна-
чение ожидаемого смещения осей по формуле (3.1):
Вер±ρ∑см = К ∑ i =1 ñi .
Принимая количество составляющих звеньев n= 5; отношение макси-
мального поля рассеивания модуля вектора к минимальному полю рас-
севания с = 2,5; коэффициент, определяющий соотношение систематиче-
ской и случайной составляющих производственных погрешностей
η= 0,5; процент производственного риска р=0,5% в соответствии с прил.
2, получим коэффициент К = 0,6. Тогда Вер±ρ∑см = 0,6·0,07 = ± 0,042 мм.
Это наиболее вероятное ожидаемое значение имеет запас точности
по отношению к заданному предельному допустимому смещению
(±0,08 мм) осей. Коэффициент точности для данного важного парамет-
ра диска турбины К = 0,042/0,08 = 0,525 показывает, что процесс протя-
гивания пазов в диске турбины для данного анализируемого параметра
выполняется с достаточной точностью.
После выполнения операции №100 производится вторичное протя-
гивание технологического образца (операция №105).Технологический
образец после протягивания подвергается тщательному контролю (опе-
рация №110) всех заданных геометрических параметров паза. По ре-
зультатам измерения образца дается заключение о возможности даль-
нейшего использования комплекта протяжек.
После выполнения указанных операций диск турбины подвергается
слесарной обработке и промывке.
Обработка отверстий для подачи воздуха во внутреннюю полость
лопатки производится на вертикально-сверлильном станке моделей
2110, 2125 и др. с использованием специального поворотного кондук-
тора.
Операция №130 – обработка отверстий для фиксации лопаток в
пазах диска также осуществляется на вертикально-сверлильном станке
166
|
с использованием специального поворотного приспособления-
кондуктора.
После выполнения слесарной обработки острых кромок и радиусов
скругления (операция №140), промывки диска (операция №145), он
подвергается полированию (операция №155). Предусматриваются от-
делка полотна диска с двух сторон и полирование радиусов перехода
для плоских, цилиндрических и конических поверхностей. При поли-
ровании используют специальное станочное приспособление, шлифо-
вальные круги 24А16СТК, абразивные порошки (зерно 24А) и шлифо-
вальные шкурки. Полирование используются пневмо-шлифовальные
головки ПШТ-2. Выполнение данной операции сопровождается тща-
тельным контролем состояния поверхностей и поверхностного слоя
(прижоги при обработке на поверхности не допускаются).
Вторая часть технологического процесса завершается проведением
термической обработки диска (операция №160). При выполнении тер-
мической операции производится отжиг и последующий отпуск на воз-
духе.
Третья часть технологического процесса (операции №165-185)
предусматривает абразивно-жидкостную обработку основных поверх-
ностей диска окончательное формирование конструкторских и рабочих
поверхностей, отделку отверстий под призонные болты и проведение
окончательной слесарной обработки.
Операция №165 - гидроабразивная струйная обработка (ГАО) ос-
новных поверхностей диска сокращает трудоемкость слесарно– зачист-
ных и слесарно-полировальных работ, которые при изготовлении ГТД
составляют до 40% общей трудоемкости изделия [34]. Применение
струйной гидроабразивной обработки обеспечивает повышения качест-
венных показателей параметров поверхностей и поверхностного слоя.
Это приводит к увеличению ресурса и надежности работы изделия.
Применяемый метод обработки обладает высокими технологиче-
скими возможностями и применяется:
для скругления острых кромок и сопряжения радиусов, полирования
и шлифования сложных поверхностей;
удаления заусенцев;
снятия со всех поверхностей дефектного слоя;
снятия небольшого припуска с целью снижения шероховатости и
удаления различных повреждений с поверхности детали.
Данный процесс использует эффект удара абразивных частиц об об-
рабатываемую поверхность заготовки [35]. Процесс гидроабразивной
167
струйной обработки заключается в направлении струи суспензии, со-
стоящей из воды и частиц абразивных материалов, на обрабатываемую
поверхность заготовки. Струя подвергается воздействию потока сжато-
го воздуха, который увеличивает скорость истечения суспензии из со-
пла. Действие режущей кромки абразивных частиц на обрабатываемую
поверхность непродолжительно и имеет ударный характер. Количество
ударов в 1 с абразивных частиц колеблется в зависимости от условий
обработки от 2 · 106 до 25 · 106.
Струйная гидроабразивная обработка не создает направленной ше-
роховатости, обеспечивает упрочнение обрабатываемой поверхности,
вследствие чего повышается усталостная прочность обрабатываемых
деталей.
Основными геометрическими параметрами струйного аппарата с
сужающимся смесительным соплом являются [34]:
диаметр смесительного сопла dс;
диаметр активного сопла (жиклера) dа.
отношение площадей смесительного и активных сопел Fс/Fа;
расстояние между входным сечением активного сопла и выходным
сечением смесительного сопла а;
длины смесительного сопла lс;
длины цилиндрической части смесительного сопла lу;
угол сходимости конусной части смесительного сопла G(рис. 4.8).
Суспензия подается в струйный аппарат при помощи насоса. Управ-
ление установкой электропневматическое. Основными узлами установ-
ки являются камера 2 с ребристым днищем, в которой устанавливается
обрабатываемая заготовка 9, и струйный аппарат 7. Нижняя часть ка-
меры служит емкостью для гидроабразивной суспензии, здесь же раз-
мещены пневматические барбатеры 1 для взвешивания абразивных
частиц в жидкости. Для настройки струйного аппарата установлены
механизмы 4 и 6.
При вращении маховика 5 осуществляется перемещение струйного
аппарата в вертикальной плоскости. В зависимости от положения ма-
ховика 3 струйный аппарат может перемещаться в горизонтальной
плоскости и поворачиваться вокруг горизонтальной оси на угол 90°.
168
Рис. 4.8. Схема гидроабразивной струйной обработки (ГАО)
диска турбины ГТД и изменение остаточных напряжений σост
Дата добавления: 2018-05-12; просмотров: 680; Мы поможем в написании вашей работы! |
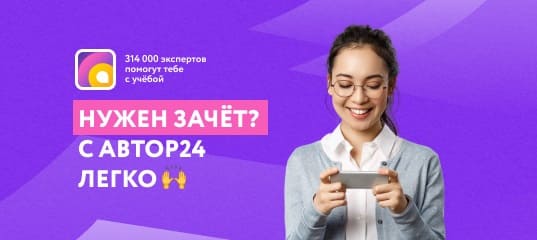
Мы поможем в написании ваших работ!