Обработка отверстий абразивным инструментом
Обработка наружных цилиндрических поверхностей. 2 Методы получистовой и чистовой обработки валов 3 Обработка длинных ступенчатых валов (отношение длины к диаметру >10)
Обработка отверстий
Обработка отверстий абразивным инструментом
Обработка отверстий без снятия стружки
Обработка систем отверстий со взаимно параллельными осями
Обработка плоских поверхностей
Обработка пазов, методы их обработки.Обработка шпоночных пазов
Обработка конических и фасонных поверхностей
Особенности обработки резьбы на станках токарной группы
Особенности фрезерования резьб гребенчатыми и дисковыми фрезами, вихревой метод нарезания резьбы. Технологические возможности методов
Шлифование резьбы
Методы пластического деформирования резьбы
Обработка червяков
Обработка шлицевых поверхностей
Обработка зубчатых колёс
Фрезерование по методу копирования, долбление, протягивания зубчатых колес
Фрезерование по методу обката, долбление, зуботочение
Нарезания зубьев колёс рейками
Зубошевингование
Кромочное шевингование
Отделочная обработка зубчатых колес после термообработки
Способы нарезания прямозубых конических колёс
Обработка конических зубчатых колес
Пластическое деформирование зубчатых колес и шлицев
|
|
Особенности методов и их возможности
Обработка на токарных автоматах
Обработка на агрегатных и с ЧПУ
Изготовление шпинделей
Обработка коленчатых валов
Обработка корпусных деталей
Типовой технологический процесс обработки корпусной детали
Обработка наружных плоскостей корпусных деталей
Обработка отверстий в корпусных деталях
Обработка станин
Обработка составных станин
Резание с наложением вибраций
Резание с нагревом
Электроэрозионная обработка
Электрохимическая обработка
Анодная механическая обработка
Высокоскоростные методы обработки
Обработка электронным лучом
1 Обработка наружных цилиндрических поверхностей.
Наружные цилиндрические поверхности можно обработать:
1. точением;
2. зенкерованием;
3. фрезерованием;
4. протягиванием;
5. шлифованием;
6. суперфинишированием;
7. притиранием (лопингование);
8. полированием;
9. пластическим деформированием;
10. электрофизическими методами.
Точение
Это самый дешевый, распространенный способ обработки. Применяется от единичного до массового производства, точность обработки – 14-7 квалитет, шероховатость - 3-7 класс. Производится на станках токарной группы, агрегатных и специальных станках.
|
|
Обработка точением в единичном производстве осуществляется на токарно-винторезных станках,токарно-карусельных и лоботокарных; в серийном – на токарно-револьверных и с ЧПУ; в крупносерийном и массовом производствах – на токарных автоматах и полуавтоматах (одно- и многошпиндельных).
Зенкерование –процесс черновой и получистовой обработки небольших по размеру цилиндр. поверхностей типа бобышек, цапф .
Обработка на агрегатных станках или автоматных линиях.
Наружный диаметр обрабатывается по 10IT, шероховатость – 5 класс.
Если деталь большая, то применяется не цельный зенкер, а сборный.
Фрезерование
Процесс черновой и получистовой обработки цилиндрических, конических и фасонных поверхностей на специальных станках, полуавтоматах и автоматах. Это метод Рото-Фло. Обработка идет при вращающейся детали, установленной в центрах. Станки применяются в крупно-серийном и массовом производстве для обработки обычно сложных деталей, имеющих цил., кон. и фасон поверхности. Точность обработки – 10 квалитет, шероховатость – 5 класс.
|
|
2 Методы получистовой и чистовой обработки валов
Протягивание
При черновой, чистовой и отделочной обработке цилиндрических поверхностей призматическими или круглыми протяжками. Протяжки сборные, оснащены твердым сплавом. Применяются только в массовом производстве, н-р для обработки коленвала. Обработка идет при вращающейся детали со скоростью круговой подачи. Поверхность м.б. конической или фасонной.
Точность обработки – 7 квалитет, шероховатость – 7-8 класс.
С внутренними зубьями
Шлифование
Производится на круглошлифовальных станках методом продольной подачи, поперечной подачи и косой подачи. В единичном и мелкосер производстве на универс. ст.; в крупносер и массовом – полуавтоматы и автоматы.
Шлифование, как правило, применяется при обработке закаленных поверхностей с твердостью больше 40HRC. Можно шлифовать и незакаленные стали и цветные металлы. Шлифование обеспечивает 6-9 квалитет точности, 6-9 класс шероховатости. Осуществляется при использовании СОТС (эмульсии).
Недостатки: высокие температуры на поверхности резания, что приводит к появлению прижогов, низкая производительность, ограниченная длина заготовок(не >80).
|
|
Интенсивно разрабатываются способы снижения температуры в зоне резания:
1) подача СОТС при давлении 5 и более атмосфер;
2) подача СОТС через поры круга (способ практически не применяется);
3) импульсное шлифование, когда контакт абразивного круга с деталью прерывистый. – профилированные круги.
Импульсное шлифование позволяет исключить возможность прижогов, повысить режимы резания, производительность. Износ круга больше на 15-20%, чем у обычных кругов.
Интенсификация проц шлифования:1. Ув ск рез 30-40 м/c, до 50 – скоростное, 60-150 – высокоскоростное – 10-14 класс шерох.
Суперфиниширование
Процесс отделочной обработки поверхности, предварительно полученной шлифованием или тонким точением.
Обработка на специальных станках для суперфиниширования абразивными брусками, установленными в головке, движущимися с продольной подачей (0,2-0,5 мм/об) вдоль оси детали и совершающими колебательные движения (до 1000 колебаний/мин). Деталь вращается со скоростью до 10-30 м/мин и более. Примен СОЖ.
Применяется в крупносерийном и массовом производстве при обработке наиболее ответственных поверхностей (шейки коленчатого вала). Припуск под суперфиниширование в пределах допуска. Точность размера повышается незначительно, точность взаимного расположения не повышается. Повышается только класс шероховатости (10-12 класс).
Притирание
Процесс отделочной обработки поверхности абразивными порошками или пастами, нанесенными на притиры, которые могут быть из чугуна (СЧ20). Порошки: окись кремния, нитрид бора, карбиды металлов и др.
Процесс притирания применяется в единичном и мелкосерийном производствах на модифицированных токарных станках. В крупносерийном и массовом производствах – на притирочных станках, в которых детали типа роликов, плунжеров устанавливаются в кассеты, ось вращения которых эксцентрична по отношению к оси вращения притиров. Притирание обеспечивает повышение точности обработки до 6-4 квалитета, шероховатость – до 10-14 класса.
Притираемая поверхность должна быть предварительно обработана тонким точением или шлифованием. Припуск под притирание – 10-50 мкм.
Расположение детали на сепораторе под углом и эксцентриситет осей позвол получиттьслож траекторию движения абразивного зерна по поверхности деталей – высокая точность. Точность взаим полож не повыш.
Полирование
В единичном и мелкосерийном производстве на модернизированных токарных станках мягкими кругами (войлочными или фетровыми), на которые наносятся абразивные порошки или пасты. СОТС – керосин с маслом.
В крупносерийном и массовом производствах применяются специальные станки, на которых обработка производится мягкими абразивными кругами на вулканитовой основе, абразивными лентами, которыми можно полировать поверхности, отличающиеся от цилиндрических.
Полирование труднообрабатываемых материалов, твердых сплавов, спецсталей хорошо зарекомендовало себя способом магнитно-абразивной обработки, когда абразивные зерна (магнитопроводящие) прижимаются к поверхности детали магнитным постоянным полем. Источником энергии, прижимающим абразивные зерна к поверхности детали, могут быть центробежные силы, жидкость или сжатый воздух под давлением и др. источники. Полирование не повышает точности размера и формы, но повышает класс шероховатости до 10-14.
Пластическое деформирование
Осуществляется шариками или роликами, установленными в специальные раскатники. При этом приложение нагрузки к шарикам и роликам может быть статическим или динамическим (наложение ультразвука).
На модернизированных токарных станках или специальных раскатных станках с помощью специальных твердосплавных или алмазных (алмазное выглаживание) накатников.
Поверхность детали должна быть предварительно обработана не ниже 4 класса шероховатости.
Применяется для низко- и среднеуглеродистых сталей после операции нормализации или улучшения, для цветных металлов.
Пластическое деформирование позволяет наклепать поверхностный слой, т.е. повысить его прочность (ΔНВ до 40%).
В поверхностном слое создаются положительные напряжения сжатия, обеспечивающие повышение долговечности работы детали, сопротивляемости поверхности знакопеременным циклическим нагрузкам.
Для ответственных дет в авиастр, ракет технике.
3 Обработка длинных ступенчатых валов (отношение длины к диаметру >10)
Валы являются не жесткими, поэтому нужно применять люнеты, вибрагасители или повышать жесткость самой детали операцией улучшения (закалка+в.о.) В единичном и мелкосерийном производствах производится на токарных универсальных станках по шаблону с использованием двух подач вручную или по упорам(16IT).
В серийном производстве обработка производится по копиру с использованием гидросуппорта, устанавливаемого на токарно-винторезный станок.
В крупносерийном и массовом производствах применяются специальные станки полуавтоматы, многорезцовые(10IT) и гидрокопировальные (9IT),имеющие 2 суппорта (продольный и поперечный).
На многорезцовых станках каждый инструмент обрабатывает свою поверхность. С поперечного суппорта подрезают торцы, точат фаски, канавки (выдерживаем линейные размеры).
На гидрокопировальных станках обработка всех ступеней производится 1 резцом, управляемым от копира (диаметральные размеры по IT9-8). Многорезцовые станки применяются для черновой и получистовой обработки (диаметральные размеры по IT10).
В среднесерийном производстве используют гидрокопировальные станки полуавтоматы с цикловым программным управлением. Станки позволяют выполнять многопроходную обработку.
Автоматизацией обработки на токарных станках в мелко- и среднесерийном производстве является обработка на станках с ЧПУ, которые обеспечивают точность чистовой обработки до 8 квалитета.
Процесс обработки
На многорезцовых станках
На станках ЧПУ
Обработка отверстий
Отверстия можно обрабатывать:
1. сверлением;
2. зенкерованием;
3. развертыванием;
4. фрезерованием;
5. растачиванием;
6. протягиванием;
7. шлифованием;
8. хонингованием;
9. притиранием;
10. полированием;
11. обработка без снятия стружки.
Сверление
Сверление – самый распространенный способ обработки отверстий, единственно возможный способ получения отверстий в сплошном материале.
В зависимости от конструкции сверла и его особенностей сверла могут быть однокромочными (ружейное, пушечное), двухкромочными (перовое, спиральное), многокромочные (трубчатые, кольцевые).
Наибольшее распространение получили спиральные сверла, которые выпускают Ø0,2-55 мм. Экономически выгодно сверлить отверстие в сплошном материале диаметром Ø≤25 мм. Отверстия Ø >25 мм необходимо зенкеровать или растачивать. Предпочтение отдают зенкерованию, так как зенкер имеет большее число режущих кромок (более 3).
Сверление отверстий малых размеров Ø≤10…12 мм по кондукторным втулкам обеспечивает точность 10 квалитет, шероховатость до 5 класса, точность межцентрового+/- 0,2…0,1 Обычное сверление обеспечивает 12 квалитет, шероховатость 4 класс.
Спиральными сверлами обычной конструкции экономически выгодно сверлить отверстия длиной l (l/d < 5 - 6мм). Специальными шнековыми сверлами с подводом СОЖ через тело сверла можно сверлить отверстия глубиной l (l/d<15-20мм), а в массовом при l/d<5, а также для мягких материалов Ружейными и пушечными сверлами сверлят глубокие отверстия (20<l/d<300мм). Для повышения точности оси отверстия (прямолинейности) обработка идет при вращающейся детали. Желательно все глубокие отверстия (l/d>10мм) сверлить при вращающейся детали (то есть на токарном станке), т.к. в случае увода сверла появл силы, стрем вернуть сверло в прмолин полож
Обработка ружейными сверлами возможна по целому металлу. Минимальный диаметр сверления Ø = 3 мм.
Пушечные сверла применяются только при рассверливании. Точность обработки ружейными и пушечными сверлами 9-10 квалитет, шероховатость 5-6 класс.
В процессе обработки сверло направляется по обрабатываемой поверхности и выглаживает ее. СОЖ при резании подается под давлением 20…80 атмосфер. Первичное направление сверла происходит по кондукторной втулке.
Зенкерование
Зенкерование – процесс черновой и получистовой обработки отверстий режущим инструментом – зенкером, который может работать как по черному отверстию, то есть полученному литьем или штамповкой, так и по предварительно обработанному сверлением.
Черновое зенкерование обеспечивает точность обработки 12 квалитет, шероховатость поверхности 4 класс (Rz40). Чистовое зенкерование после чернового обеспечивает 10 квалитет точности, шероховатость поверхности – до 5 класса.
Применяются зенкеры диаметром более 13 мм.
Процесс зенкерования широко применяется при обработке на агрегатных станках, токарных многошпиндельных, специальных и других в среднесерийном – массовом производстве.
Широко применяются многоступенчатые зенкеры, а также комбинированный режущий инструмент (зенкер, зенковка, сверло, развертка).
Разновидностью процесса зенкерования является зенкование под головки винтов или цекование.
Для обеспечения точного межцентрового расстояния между отверстиями зенкерование производится с использованием направляющих элементов. При этом направление может быть переднее (впереди режущей части), заднее (за режущей частью) и комбинированное. Это позволяет обеспечить точность межцентрового расстояния при зенкеровании отверстий ±(0,10…0,15) мм.
Развертывание
Развертывание – это процесс чистовой и отделочной обработки отверстий многокромочными или однокромочными развертками. Минимальный диаметр однокромочной развертки Ø3 мм, минимальный диаметр многокромочной развертки Ø2 мм.
Развертывают отверстия диаметром Ø (4…500) мм. Припуск на развертывание 0,03…0,30 мм. В процессе развертывания с обрабатываемой поверхности снимается минимальный равномерный припуск по окружности, что обеспечивается плавающим креплением режущего инструмента. Развертывание не повышает точность взаимного расположения
Черновое развертывание отверстий после сверления или зенкерования обеспечивает точность обработки 9 квалитет, шероховатость поверхности 6 класс. Чистовое развертывание обеспечивает точность обработки 7 квалитет, шероховатость поверхности 7 класс.
Однолезвийные развертки обеспечивает лучшее качество поверхности на 1-2 квалитета.
Отверстия Ø≤12 мм развертывают сразу после сверления, отверстия Ø≥12 мм – после зенкерования.
При обработке точных отверстий малых размеров (Ø≤5…6 мм) с точным межцентровым расстоянием (±0,05 мм) выполняют координатное развертывание, то есть черновое развертывание по кондукторным втулкам. Чистовое развертывание может быть по кондукторным втулкам или без них.
При обработке глубоких отверстий зенкерованием и развертыванием используется схема обработки с обратной подачей.
2Z = 0,25D
t≤0,125D
Растачивание
Растачивание – процесс черновой, чистовой, окончательной, отделочной обработки, выполняемый на станках токарной группы, расточных станках, агрегатных и специальных станках. Растачивание – самый универсальный способ обработки, обеспечивающий точность обработки от 12 квалитета до 7 квалитета (отделочная обработка – до 6 квалитета). Тонкое растачивание производится с малыми глубинами резания t=(0,03…0,10) мм и малыми подачами S=0,03…0,05 мм/об при высокой жесткости и отсутствием вибраций.
Протягивание
Протягивание – процесс черновой, чистовой, отделочной обработки отверстий за один проход. Протягивать можно отверстие после сверления, зенкерования или растачивания. При этом желательно, чтобы точность отверстия была не грубее 10 (9) квалитета.
Чем меньше зазор между направляющими и отверстием. Тем равномернее снимаемый припуск. Протягивание небольших по размерам деталей производится на горизонтально-протяжных станках; большие корпусные детали – на вертикально-протяжных станках. Форма протяжки в поперечном сечении соответствует форме получаемого отверстия. В зависимости от вида обработки (черновая, чистовая, окончательная) используют различные схемы резания. Последние режущие зубья протяжки работают по профильной схеме Sz = (0,03…0,05) мм/зуб.
Очень часто последние зубья протяжки выполняют выглаживающими, что позволяет повысить класс шероховатости отверстия до 8-9 класса.
Точность взаимного положения при протягивание не повышается.
Фрезерование
Прнименяетс редко. Обычно на ст с ЧПУ черновая обработка отв больши диаметра в корпусных деталях концевыми фрезами по программе. Точность до 10 IT, шероховатость до 5 кл.
Обработка отверстий абразивным инструментом
Хонингование
Хонингование – процесс отделочной обработки отверстия абразивными брусками, установленными в специальные головки. Абразивные бруски направляются по обрабатываемой поверхности благодаря плавающему креплению, снимая с поверхности минимальный равномерный припуск. Повышается точность размера и формы. Точность взаим полож не повыш.
Процесс хонингования производится на специальных станках, которые могут быть универсальными или станками полуавтоматами и автоматами.
Минимальный диаметр хонингуемых отверстий в серийном и крупносерийном производствах Ø7 мм, в единичном – Ø5 мм.
Модели станков:
3М82 – диаметр обрабатываемого отверстия D = Ø(20…80) мм;
382 – D = Ø(30…105) мм, ход шпиндельной головки h = (35…500) мм;
3А84 – D = Ø(65…200) мм, h = (75…1200) мм;
385 – D = Ø(125…500) мм, h = 1750 мм;
ОФ-52 – D = Ø(7…25) мм;
ОФ-385 – D = Ø(10…20) мм, h = 295 мм.
Хонингование обеспечивает точность обработки 5-6 квалитет, шероховатость поверхности – 10-11 класс.
Vхон.гол. = 40…80 м/мин
Zmin = 0,02…0,10 мм
Шлифование
В единичном производстве может выполняться на модернизированном токарном станке, у которого вместо резцедержателя ставится шлифовальная головка.
Начиная от мелкосерийного до массового производства шлифование отверстий производится на внутришлифовальных станках. При этом обработка деталей (тел вращения: стаканы, втулки, гильзы) производится при вращающейся детали. Съем припуска происходит за несколько десятков двойных ходов головки. После каждого двойного хода круг врезается в радиальном направлении на величину глубины резания в пределах 2-5 мкм.
Vш.к. = 25…30 м/с
Vдет = 16…20м/мин
Dш.к. = (0,80…0,85)Dотв
Z = 0,05…0,50 мм
Шлифование обеспечивает точность обработки 6-7 квалитет, шероховатость поверхности 7-9 класс.
Большинство внутришлифовальных станков имеют систему автоматического слежения за выполняемым размером, то есть станок автоматически выключается. Особо точные отверстия шлифуют в два приема: черновое шлифование, правка круга, чистовое шлифование. Все выполняется в автоматическом режиме.
Многие станки имеют две шлифовальных головки, позволяющие обрабатывать не только отверстия, но и торец. Торец шлифуется чашечным кругом.
На внутришлифовальном станке с ЧПУ можно шлифовать не только отверстие, но и оба торца с одной установки детали благодаря специальной заправке абразивного круга (торец не более 5 мм).
Отверстия в корпусных деталях шлифуют при неподвижной детали, используя схему планетарного шлифования. Шлифование повышает точность взаимного расположения отверстий и размеров.
В массовом производстве при обработке беговых дорожек колец шарикоподшипника применяется схема бесцентрового шлифования. Точность взаимного расположения улучшается не более, чем на 5 мкм.
Притирание
Притирание используется в единичном, мелкосерийном производстве взамен операции шлифования, в крупносерийном и массовом производстве - для обеспечения высокой точности обработки (5 квалитет и точнее), шероховатость поверхности 10-14 класс.
Обработка производится на специальных притирочных станках чугунными притирами с нанесенными на них абразивными пастами или порошками. Процесс идет с СОЖ (керосин с маслом). ОФ26А. Повышается точность размера и формы. Точность взаим полож не повыш.
Полирование
Процес идет на спец станках и модернезированных токарных. М производится мягкими кругами (войлок, фетр) или мягк абразив кругами, а также спец ленточными, основой которых явл шкурка или лента, закрепл на круге. Шерох 10-14 класс. Точность размеров и формы не повышаются. Припуск под шлифование не оставляется.
Дата добавления: 2018-05-12; просмотров: 109; Мы поможем в написании вашей работы! |
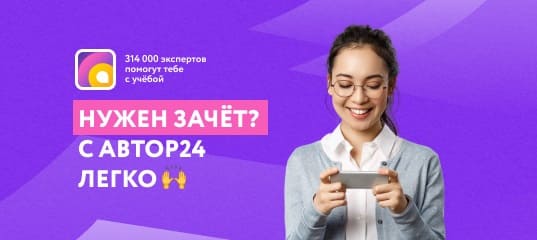
Мы поможем в написании ваших работ!