Испытание под нагрузкой и в работе.
Под нагрузкой отремонтированный и собранный станок испытывают путём обработки деталей-образцов на различных скоростях в соответствии с техническими данными паспорта станка. Испытание ведут с нагружением станка до величины номинальной мощности привода, снимая стружку всё большего сечения. Допускается кратковременная перегрузка до 25% сверх номинальной мощности в течение 30 мин.
Все механизмы станка при его испытании под нагрузкой должны работать исправно, допустимо лишь незначительное повышение шума в зубчатых передачах. Устройства, предохраняющие станок от перегрузки, должны действовать надёжно; легко и плавно должна включаться пластинчатая фрикционная муфта.
4 Испытание на точность После обкатки станка на холостом ходу и испытания под нагрузкой должно быть проверено соответствие нормам точности, т.е. измерены геометрическая точность самого станка и точность изделий, обрабатываемых на станке.
В процессе этого испытания производят:
- проверку прямолинейности и правильности плоскостей;
- проверку взаимной параллельности поверхностей;
- проверку взаимной перпендикулярности поверхностей;
- проверку соосности осей узлов.
Испытание на получение требуемой шероховатости обработанной поверхности производится точением образца при определённых режимах резания. (на обработанных поверхностях не должно быть следов дробления).
Результаты испытания на точность заносятся в акт сдачи станка из ремонта.
|
|
5 Испытание на жесткость Внедрение контроля жёсткости станков даёт возможность обеспечить устойчивую их работу. Показателем жёсткости является степень деформации испытываемых сборочных единиц относительно станины под действием определённой внешней силы. Проверяют жёсткость динамометром и индикатором, применяя при необходимости оправки и упоры.
По результатам всех испытаний и проверок, предусмотренных техническими условиями, комиссия в составе представителей цеха-заказчика, цеха , производившего ремонт, и отдела технического контроля вносит в акт приемки станка из ремонта заключение о пригодности его к эксплуатации.
Вопрос 20 (не будет)
Вопрос 21 Ремонт корпусных деталей
К корпусным деталям относят корпуса коробок скоростей, коробок подач, редукторов, бабок и т.п. Основной материал корпусных деталей - чугун, в некоторых случаях применяются сварные корпуса.
Основные дефекты корпусных деталей:
Трещины.
Ремонт производится:
а) с помощью штифтов в следующей последовательности:
Рисунок 4.5- Заделка трещин штифтами
- границы трещины определяют керосиновой пробой;
- размечают отверстия на расстоянии 1.5 диаметра друг от друга и сверлят сверлом диаметром 4-5 мм;
|
|
- нарезают резьбу в отверстиях;
- вворачивают в резьбовые отверстия штифты из меди или мягкой стали;
- отрезают концы штифтов так, чтобы они выступали над поверхностью детали на 1-2 мм;
- засверливают отверстия между штифтами с перекрытием не менее чем на ¼ диаметра;
- нарезать в них резьбу и ввернуть штифты, концы срезать;
- расчеканить и запилить выступающие концы штифтов;
- проверить герметичность шва под давлением 0.3-0.4 МПа.
б) стяжками
-просверлить и развернуть 2 отверстия в корпусе, запрессовать в них штифты;
-изготовить стальную пластину-стяжку;
-просверлить 2 отверстия на расстоянии несколько меньше расстояния между штифтами;
-нагреть пластину-стяжку и установить её на штифты (охлаждаясь пластина стянет трещину)
Рисунок 4.6 – Установка стяжек
в) установкой накладок на винтах с расчеканкой краев
- зачистить ремонтируемое место стальной щеткой или шлифовальной шкуркой;
-на концах трещины просверлить сквозные отверстия диаметром 4-5 мм;
- из мягкой стали вырезать накладку больше чем трещина или пробоина на 15 мм и более;
- вырезать прокладку из картона или свинца по размеру стальной прокладки;
|
|
-просверлить в корпусе отверстия на расстоянии 10-15 мм и 10мм от края накладки, нарезать резьбу М5-М6;
-просверлить сквозные отверстия под винты с потайными головками в прокладке и накладке;
-прокладку и накладку смазывают суриком (герметиком) и закрепляют винтами, края расчеканивают;
- герметичность проверяют под давлением 0,2-0,3 МПа
г) заваркой с последующей механической обработкой (при необходимости)
Пробоины и сколы.
а) накладками
б) установкой ввертыша
- рассверлить пробоину и нарезать в ней резьбу;
- смазать резьбу суриком;
- в отверстие ввертывают пробку;
-пробку стопорят винтом и расчеканивают.
в) установкой пробки
- небольшие сколы засверлить и развернуть;
- в отверстие запрессовать пробку, опиленную по форме ремонтируемой поверхности.
г) установкой вставки
- сколотое место запилить или фрезеровать;
- по форме паза изготовить вставку;
- запрессовать вставку в паз;
- можно дополнительно вставку закрепить винтами.закрепить
Вопрос 22Ремонт валов и осей.
Вал - это деталь машины, передающая крутящий момент и поддерживающая вращающиеся детали.
Ось - вращающаяся или неподвижная деталь машины и механизма, служащая для поддержания вращающихся частей, но не передающая крутящего момента.
|
|
Ремонт
1 Очищенный от грязи и смазки вал (ось) сначала выправляют от изгиба
2 Все основные операции механической обработки валов производятся обычно в центрах. Центровые отверстия служат базой при изготовлении вала и ремонтных работах. Поэтому центровые отверстия должны быть правильно засверлены, содержаться в исправном состоянии.
Именно поэтому, после предварительной правки деталей у них зачищают центровые отверстия. Эту операцию осуществляют на токарном станке выглаживанием с помощью специального центра.
Размеры центровых отверстий выбирают в зависимости от размера заготовок валов по ГОСТ .
3 Шейки валов (осей) ремонтируются различными способами, выбор которых зависит от величины их износа.
1) У деталей со значительным износом шейки протачивают и шлифуют под очередной ремонтный размер ( уменьшение диаметра на 5-10%) или запрессовывают на них компенсационное кольцо, которое обтачивают и шлифуют на номинальный размер.
2) При износе шейки детали до 0,15 мм на диаметр, исходный размер восстанавливают хромированием, предварительно выполнив операцию шлифования для вывода рисок и нецилиндричности шейки. (Гальванические способы эффективны при массовом восстановлении однотипных деталей)
3) Шейки с износом более 0,2 мм на сторону восстанавливают вибродуговой наплавкой, осталиванием, электромеханическим способом, ферромагнитными порошками.
4) При износе шеек более 0,3 мм на сторону применяют наплавку, металлизацию или осталивание.
5) при износе более 0,5мм преимущественно используют следующие виды наплавки: в среде углекислого газа, вибродуговая, под флюсом и в природном газе.
4Шпоночные пазы на валах обычно разбиваются и изменяют свою форму, что является следствием неправильного монтажа, перегрузки соединений, а также вибраций и прочих динамических нагрузок.
Шпоночные пазы у валов и осей восстанавливают следующими способами:
- фрезеруют под следующий ремонтный размер при износе менее чем 15% или под нестандартную ступенчатую шпонку;
- заваривают, затем поворачивают деталь вокруг оси на 90° и фрезеруют новый паз с номинальными размерами, если это позволяет конструкция ;
- наплавляют с последующей обработкой под номинальный размер (для неответственных соединений).
5 Шлицы изнашиваются по боковым поверхностям, впадинам, вершинам или торцам шлиц. В зависимости от вида износа различают следующие способы восстановления шлицевых валов:
При износе и смятии шлицев производят:
а) электродуговую наплавку с последующей механической обработкой (при незначительной ширине 4-5 мм и больших износах);
-очистить;
-наплавить;
-проточить вал после наплавки;
-фрезеровать зубья с припуском на шлифование;
-термическая обработка (закалка и отпуск);
-шлифовать наружные и боковые поверхности.
б) при износе по ширине паза до 0,5-1 мм и при центрировании шлицевого соединения по внутреннему диаметру шлицы ремонтируют раздачей отожженного вала
-отжечь вал;
-выполнить зубилом канавки и раздать зубья в продольном направлении, доводя ширину каждого зуба до размера, превышающего номинальный на величину припуска на 0,1-0,2 мм для механической обработки;
-заварить полученные канавки;
-проточить вал по наружному диаметру до заданного размера;
-фрезеровать зубья;
-закалка и отпуск;
-шлифовать поверхность зубьев.
в) при небольших износах ( 0,1-0,2 мм) шлицы восстанавливают наращиванием хромированием с последующим шлифованием.
5При износе резьбы изношенную резьбу срезают и нарезают новую, обрабатывая её до ближайшего диаметра по стандарту, либо на деталь насаживают втулку или бандаж с резьбой, при значительном износе профиля резьбовую часть наплавляют с последующей обточкой шеек и нарезанием резьбы требуемого размера.
6 Трещины на валах и поломанные валы, возможно восстанавливать электрической и газовой сваркой, однако следует помнить, что прочность восстановленного вала на участке сварки обычно не превышает 60 процентов прочности целого вала. Поэтому поломанные валы ответственных и сильно нагруженных машин не восстанавливают, а заменяют новыми.
Ремонт шпинделей
Шпиндель - вращающийся вал станков с устройством для закрепления заготовок или режущего инструмента.
Шпиндель одна из ответственных деталей станка от точности и жёсткости которого зависит качество выполняемых на станке операций. Отклонения от формы и размеров поверхностей шпинделя допускаются в очень узком диапазоне, поэтому к ремонту шпинделей предъявляются повышенные требования.
Изготовление нового шпинделя является сложной и дорогостоящей операцией. Однако в тех случаях, когда его ремонт влечёт за собой также ремонт или изготовление сопрягающихся с ним деталей, замена изношенного шпинделя новым может оказаться более экономичной.
Концы шпинделя стандартизированы и служат базой для технологической оснастки. Поэтому при ремонте стремятся восстановить его в начальных размерах.
Ремонт шпинделя заключается в восстановлении подшипниковых шеек, переднего конуса, канавок, резьбы, шпоночных пазов.
Выбор способа восстановления основных поверхностей шпинделя производят в зависимости от величины их износа.
1 Если износ по диаметру 0,01-0,02мм - ремонтируют притиркой на токарном станке, выполняя на токарном станке специальным инструментом - жимком (кольцо-хомутик, винт, втулка-притир). На шейку накладывают смесь из мелкого наждачного порошка и масла, после чего надевают жимок и слегка заворачивают винт. Включают станок скоростью 10-20м/мин и равномерно водят жимком вдоль шейки. Промывают керосином, наносят тонкий слой доводочной пасты и завершают обработку.
2 При износе поверхностей шпинделя до 0,05мм на сторону выполняют:
- предварительное шлифование для восстановления геометрической формы поверхности;
- хромирование;
- окончательное шлифование, снимая до 0,03мм на сторону.
3 При износе более 0,05мм на сторону поверхности шпинделя подвергают наращиванию металлом одним из известных способов, затем механической обработкой.
4 Шейки шпинделя под подшипники скольжения восстанавливают установкой на клее тонкостенных компенсационных наделок или вставок.
5 Коническое отверстие на конце шпинделя при восстановлении обычно - шлифуют, затем торец шпинделя подрезают по конусному калибру.
При значительном износе конического отверстия его растачивают, запрессовывают втулку и вновь обрабатывают внутренний конус.
-расточить коническое отверстие;
-изготовить ремонтную втулку с толщиной стенок не менее 2мм , отверстие закалить до 59-61HRCэ;
-установить втулку на клей и выдержать не менее 24 ч;
-шлифовать коническое отверстие;
- проверить отверстие с помощью конического калибра.
6 Для восстановления изношенной резьбы на шпинделе необходимо прорезать её, с последующим изготовлением по месту новых сопрягаемых гаек. Производить наварку резьбы не рекомендуется, т.к. при её нарезании редко удаётся получить хорошую поверхность.
7 Шпоночные пазы делают шире и ставят нестандартную шпонку, или если это допускает конструкция можно изготовить паз на новом месте.
Установку шпинделя при ремонте внутренней поверхности осуществляют при помощи трёхкулачкового патрона и люнета.
При обработке наружных поверхностей применяют специальную оправку.
Дата добавления: 2018-05-02; просмотров: 885; Мы поможем в написании вашей работы! |
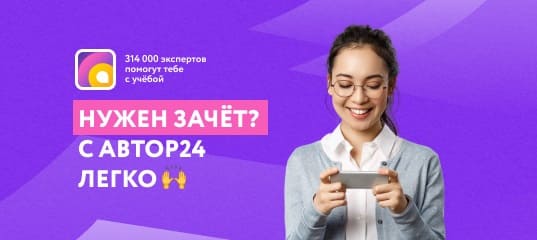
Мы поможем в написании ваших работ!