Например D-8x42x48H8/h7x8F10/h9
Способы центрирования прямобочных шлицевых соединений:
а) по наружному диаметру
б)по внутреннему диаметру
в) по боковым сторонам
При сборке шлицевых соединений их пригоняют в следующем порядке:
- шлицы вала пригоняют по пазам одной из ступиц, а затем все остальные детали сидящие на валу пригоняют по шлицам вала ;
- в случае если вал не подвергался ремонту, то шлицевые отверстия в ступицах пригоняют по валу.
Сборка прессовых соединений
Запрессовка, в зависимости от требуемого усилия, производится вручную молотком или же механизированным способом. Вручную запрессовывают небольшие детали - шпонки, клинья, штифты. При этом пользуются медными или свинцовыми молотками, а также молотками из дерева твердых пород. Допускается использование и стальных молотков, но при условии нанесения ударов. Через мягкую прокладку.
Удары при запрессовке должны быть сначала легкими, пока деталь не вошла в отверстие. Убедившись, что деталь вошла в отверстие без перекосов, увеличивают силу ударов. Заканчивают запрессовку резкими заключительным ударом, чтобы деталь плотно села на свое место.
Механизированная запрессовка производится специальными приспособлениями или на прессах- ручных, гидравлических, пневматических.
Для получения прессовых посадок применяют сборку с нагревом охватывающей детали или охлаждением охватываемой. Этот способ основан на явлении расширения деталей под нагревом и уменьшения объема при охлаждении.
|
|
Нагрев производится в кипящей воде или масле с температурой 85-900С, в нагревательных печах, газовыми горелками или электрическим током. Охлаждают детали в жидком воздухе, жидком кислороде или сжиженном азоте, а также в твердой углекислоте (сухой лед).
Сборка штифтовых соединений
Штифты фиксируют взаимное положение двух соединенных деталей и разгружают болты от поперечных усилий.
Сборка штифтовых соединений :
- по имеющемуся отверстию в одной детали после фиксации положения соединяемых деталей засверливают отверстие в другой детали ( для конического штифта диаметр сверла равен диаметру штифта).
- для гладких штифтов ( без насечек) оба отверстия совместно развертывают цилиндрической или конической разверткой;
- в полученное отверстие загоняют штифт.
Сборка подшипниковых узлов
При сборке подшипников качения в первую очередь подготавливают и проверяют посадочные места на валу и в корпусе. Предназначенные для сборки подшипники вынимают из упаковки, тщательно промывают и измеряют. Устанавливают подшипники на вал и в корпус, обеспечивая их соосность. Контролируют качество монтажа подшипников ( не защемлены ли тела качения, прижаты ли подшипники к заплечникам вала и корпуса).
|
|
Подшипники качения могут устанавливаться:
- с натягом вала;
- с натягом в корпусе;
- с натягом на вал и в корпусе.
Для облегчения монтажа подшипники подвергают нагреву в масляных или водяных банях и затем охлаждают в жидком азоте. Подшипники запрессовывают на вал при помощи ручного или гидравлического прессов. Если пресс отсутствует, то посадку подшипника на вал можно производить при помощи монтажной трубы и молотка.
Сборка зубчатых колес
При сборке зубчатых колёс необходимо, чтобы строго выдерживалось:
а) для передач с цилиндрическими зубчатыми колёсами:
параллельность осей и межосевое расстояние ( при износе шеек валов, подшипников качения это расстояние обычно изменяется, как правило, в сторону увеличения) , радиальные и боковые зазоры;
Проверку правильности зацепления определяют при сборке мягким щупом или по краске. Щуп- свинцовая лента шириной, примерно равной высоте зубьев проверяемых колес. Толщина ленты 0,1-0,2 мм. Ленту закладывают между зубьями колес и проворачивают. По оттиску судят о правильности контакта зубьев. Краску наносят на зубья ведущего колеса. Пятно должно занимать 70-80% поверхности зуба.
|
|
б) для конических передач:
пересечение и взаимная перпендикулярность осей конических колёс;
Если пара колес собрана правильно, пятно касания не должно доходить до края меньшего торца зуба и до верхней кромки его боковой поверхности. Пятно должно быть 60%.
в) для червячных передач:
совпадение осей червяка и средней плоскости червячного колеса.
Для этого на винтовую поверхность червяка наносят тонкий слой краски, вводят червяк в зацепление с червячным колесом и проворачивают червяк несколько раз до получения отпечатков . Если зацепление правильное, пятно касания размещается по центру колеса в направлении его вращения, занимая на поверхности зуба не менее 75% его длины. Смещение отпечатка свидетельствует о плохом зацеплении и о необходимости его регулирования.
Сборка ременной передачи.
Шкивы насаживают на вал, выдерживая тугую или напряженную посадку, при этом пригоняют шпонку по пазам в валу и ступице. При сборке располагают шкивы передачи в одной плоскости. При опробовании ременной передачи ремень может оказаться на краю обода.. Возможные причины: оси шкивов расположены не параллельно, не совмещены торцы, большое биение, ремень слабо натянут. Косо сшит.
|
|
При сборке ременных передач выполняются следующие ТУ:
- допустимое радиальное биение шкива диаметром до 300мм – 0,10мм; свыше 300мм-0,15мм;
- шкивы диаметром свыше200мм должны подвергаться балансировке;
- шкивы должны быть одной ширины;
- торцы должны лежать в одной плоскости;
- валы должны быть параллельны.
Сборка цепной передачи
При сборке необходимо руководствоваться следующими техническими требованиями:
- оси валиков параллельны;
- звездочки находятся в одной плоскости;
-цепь должна работать при определенной величине натяжения;
- передача должна работать плавно без стука.
Сборка производится в следующей последовательности:
- установить шпонки в пазы валов;
-напрессовать звездочки;
- зафиксировать;
-проверить радиальное и торцовое биение;
- проверить расположение звездочек в одной плоскости;
-надеть цепь на звездочки;
-замерить с помощью линейки, накладываемой на ведомую ветвь, величину провисания цепи;
-при недостаточном или чрезмерном провисании регулировать межосевое расстояние звездочек.
Вопрос 20
Выпускаемый из капитального и среднего станка станок должен быть подвергнут приемочным испытаниям, выполняющимся в приведенной ниже последовательности.
1Внешний осмотр. При этом проверяются:
-комплектность станка;
- соответствие внешнего вида станка требованиям к качеству отделки;
- обработка и отделка поверхностей деталей, доступных осмотру при открытых крышках (профиль зубьев, шлицы валиков, окраска полостей корпусных деталей и т.д.)
- соответствие монтажа электропроводки и электроаппаратуры;
- качество сборки, доступное проверке без включения станка ( отсутствие качки рукояток, фиксация переключаемых элементов, плотность затяжки соединений и т.д.)
-отсутствие в полостях корпусных деталей, нишах и т.д. посторонних предметов
2 Обкатка (испытание на холостом ходу). Целью обкатки является выявление возможных дефектов сборки и приработка сопрягаемых поверхностей. К ней приступают, убедившись, что все сборочные единицы и механизмы закреплены и обеспечена их доброкачественная смазка.
Перед пуском станка проверяют работу механизмов, проворачивая соответствующие сборочные единицы вручную. Одновременно следят, как поступает масло к трущимся поверхностям. Сначала обкатку ведут на холостом ходу и на самых малых скоростях, а затем при последовательном включении всех его рабочих скоростей - от наименьшей до наибольшей. На самой большой скорости станок должен работать не менее 1ч без перерыва.
При испытании необходимо убедится в следующем:
- температуру нагрева подшипников не выше 50-60°С, заедание шпинделя и валов отсутствует;
- зубчатые передачи работают плавно, без толчков, стука и сотрясений
- все механизмы работают плавно, без толчков и вибраций, а их пуск и реверсирование - осуществляться легко и не сопровождаться рывками или ударами;
-все органы управления сблокированы таким образом, чтобы при включении исполнительных органов перемещения и подачи происходили строго согласованно во времени и полностью исключается возможность самопроизвольного движения даже на самое малое расстояние каких-либо деталей механизмов или частей агрегата.;
- системы смазки и охлаждения подают к соответствующим местам достаточное количество масла и охлаждающей жидкости;
- электрооборудование работает безотказно при всех режимах работы станка, пуске и остановке. В рубильниках, переключателях, реостатах и других аналогичных устройств и аппаратах не допускаются даже малейшие неисправности. Недостаточно быстрое включение или выключение электроаппаратуры, чрезмерный нагрев пускового реостата, гудение реле и другие неполадки в электрооборудовании, обнаруженные при обкатке станка, свидетельствуют о дефектах сборки или ремонта. Их устраняют соответствующими регулировками, а в случае необходимости полностью разбирают те или иные механизмы.
- в станках с гидроприводом проверяют исправность гидросистемы, отсутствие резкого шума и утечек масла.
Дата добавления: 2018-05-02; просмотров: 713; Мы поможем в написании вашей работы! |
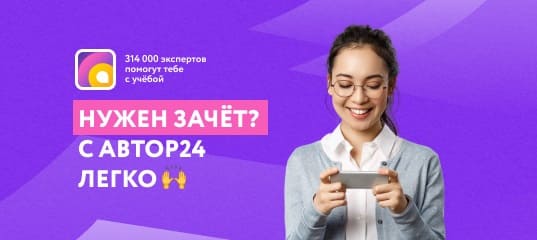
Мы поможем в написании ваших работ!