Подготовка деталей к хромирования
1) предварительная механическая обработка (шлифование и при необходимости полирование) изношенной поверхности детали с целью придания этой поверхности правильной геометрической формы и доведения ее до нужных размеров с учетом припуска на хромовое покрытие; шероховатость не должна превышать Ra=0,8 (1,6) мкм;
2) очистка деталей от окислов шлифовальной шкуркой и предварительное обезжиривание промывкой в растворителях;
3) изоляция мест, не подлежащих хромированию, покрытием этих мест цапон-лаком в смеси с нитроэмалью в соотношении 1:2, либо нанесением пленки из полихлорвинилового пластика толщиной 0,3—0,5 мм, либо применением клея БФ, цапонлаком 9-32 и др.;
4) установка детали в подвесном приспособлении с целью правильного базирования ее относительно анода и для соединения с контактами токопроводящих шин;
5) окончательное обезжиривание детали (эта операция должна выполняться весьма тщательно, так как тончайшая жировая пленка изолирует поверхность детали от электролита. Наилучшие результаты обеспечивает электрохимическое обезжиривание с подвеской детали на катоде.
6) анодная обработка (декапирование), выполняемая с целью удаления с поверхности детали тончайших пленок окислов (эта операция осуществляется путем погружения детали вместе с подвеской в ванну для хромирования, но при включении обратного тока, т. е. анодом служит деталь. Процесс сводится к электролитическому растворению металла и одновременно к механическому отрыву окислов выделяющимся кислородом. После завешивания детали в ванну ее предварительно прогревают без тока 1—2 мин, а затем ведут анодную обработку в течение 30—45 с при плотности тока 30—35 А/дм2).
|
|
После анодной обработки деталь, не вынимая из ванны, переключают на катод и наносят покрытие.
Хромирование.
Практически хромирование деталей осуществляется в ваннах, наполненных растворами хромовой кислоты, в которые на определённом расстоянии друг от друга погружены деталь, контактируемая с отрицательным полюсом и называемая катодом и свинцовая пластина, контактируемая с положительным полюсом и называемая анодом. Площадь пластин должна быть в 2-2.5 раза больше, чем покрываемая хромом деталь. Раствор подогревают до температуры 40-60°С. Если через цепь свинцовая пластина - раствор хромовой кислоты - покрываемая деталь или, что тоже самое анод - электролит - катод, пропустить постоянный электрический ток определённой силы и напряжения ( U=8-12 В), то на поверхности детали будет осаждаться слой металлического хрома, за счёт которого изменится её размер.
3 Обработка деталей после хромирования:
- промывка в дистиллированной воде; Промывка детали вместе с подвеской в ванне с дистиллированной водой с целью сбора дорогостоящего хромового ангидрида
|
|
- промывка деталей в проточной воде;
- погружение на 0,5—1 мин в ванну с 3—5 %-ным раствором кальцинированной соды для нейтрализации остатков электролита
- демонтаж подвесок, удаление изоляции;
- сушка при температуре 120—130 °С;
- контроль качества хромированных поверхностей;
- контроль размеров хромированных поверхностей с целью определения припуска на механическую обработку;
- механическая обработка (шлифование и полирование). Припуск на шлифование оставляют 0,08— 0,1 мм. . Хромовые покрытия, нанесенные с декоративной целью, подвергаются полированию с применением паст ГОИ.
Хромирование широко применяют в ремонтной практике для восстановления рабочих поверхностей валов, шпинделей и других подобных деталей с износом до 0,1 мм.
Покрытие хромом имеет следующие достоинства:
- высокая твёрдость;
- низкий коэффициент трения;
- высокая коррозионная стойкость;
- значительная износостойкость;( превышающей в 2—3 раза износостойкость закаленной стали 45)
- высокая жаростойкость и кислотоустойчивость;
- хорошей сцепляемостью почти с любыми металлами;
|
|
- возможность одновременного восстановления большого количества деталей.
, , высокой ю и теплостойкостью.
При значительных преимуществах хромирование имеет и недостатки:
- высокая стоимость;
- ограничение толщины покрытия (до 0,3 мм) так как при большей толщине слой хрома возможно отслоение хрома и он теряет износостойкие свойства;
- большая продолжительность процесса (от 6 до 16 часов в зависимости от режима хромирования); относительно низкую производительность процесса (до 0,03 мм/ч) из-за малых значений выхода металла по току;
- уменьшается усталостная прочность до 20% (т.е. нельзя хромировать детали работающие с ударной нагрузкой или с усилием выше 0,75 кН);
- хрупкость;
- ограниченная смачиваемость, т.е нельзя восстанавливать детали работающие на износ при больших удельных давлениях .
Для неподвижных соединений применяют гладкое хромирование. Слой хрома не должен превышать 0,15 мм (после шлифования). . Он характеризуется слабой смачивающей способностью по отношению к маслу и плохой прирабатываемостью.
Для восстановления трущихся поверхностей и повышения износостойкости деталей рекомендуется применять так называемое пористое хромирование, при котором слой хрома получится пористым, что способствует удержанию смазки.
|
|
Вопрос 8 Осталивание- это процесс гальванического осаждения слоя железа до 2 мм из водных растворов его солей при прохождении через электролит тока низкого напряжения. Осталивание применяют для наращивания поверхностей деталей под неподвижные посадки, для восстановления деталей с большим износом (до 2—3 мм), а также с целью получения подслоя в 1—3 мм для тонкого хромового покрытия (0,02—0,03 мм). Детали после осталивания можно подвергать термической и термодиффузионной обработке.
Осталивание ведётся либо в ваннах из фаолита, керамики, либо в металлических с кислотостойким покрытием. Электролит подогревается до температуры 85-1000С. Из двух групп электролитов, предназначенных для осталивания сернокислых (200-300 НВ) и хлористых (100-400 НВ), используют хлористые
Электролитами здесь являются водные растворы солей железа, в качестве анодов - стальные растворимые пластины из низкоуглеродистой сталь марки 08 или 10., катодом является осталиваемая деталь.
Технологический процесс осталивания мало чем отличается от хромирования. При подготовке детали к осталиванию не всегда требуется предварительное ее шлифование: при наращивании значительного слоя деталь обычно не шлифуют. Другие подготовительные операции (обезжиривание, изоляция мест, не подлежащих осталиванию, вторичное обезжиривание, анодная обработка) принципиально те же, что и при хромировании.
Преимущества:
- производительнее хромирования в 15-20 раз;
- можно наносить более толстый слой металла чем при хромировании; Твёрдость 160-180 НВ, можно цементировать 500-600 НВ.
- высокая прочность сцепления покрытия с основным материалом (слой, нанесённый при осталивании, по своим физико-механическим свойствам напоминает серо-углеродистые стали);
- простота и экономичность ( низкая стоимость компонентов входящих в состав электролита);
- не деформируется деталь;
- можно подвергать механической обработке;
- выход металла по току 85—90 %,.
Недостатки:
- возникновение трещин на покрытии, если оно выполнено с твёрдостью свыше 38-40 HRCэ.
- износостойкость таких деталей после ремонта на 25-30% ниже по сравнению с новыми или хромированными.
Вопрос 10 (не будет)
Вопрос 12 1 Восстановление деталей методами изменения её конструкции.
1 Надевание "рубашек".
Нарушение сопряжения можно восстановить путём надевания на изношенную поверхность детали так называемых "рубашек".
Если из условий прочности это допустимо, то изношенная поверхность протачивается на меньший размер и на эту поверхность насаживается втулка - "рубашка", изготавливаемая обычно из стали. Толщина стенки "рубашки" и натяги должны быть такими, чтобы при насадке не оставались остаточные деформации. Крепление "рубашек" осуществляется либо путём установки болтов и штифтов, либо обваркой её с торцов. Допустимо приклеивание "рубашек". После износа втулка снимается и заменяется новой.
2 Гильзование. Геометрическую форму и размеры изношенных цилиндрических отверстий в деталях восстанавливают растачиванием с последующей установкой гильз (втулок). Этот метод применяется тогда, когда толщина стенки детали достаточна для растачивания без нарушения прочности и жёсткости её. Втулки могут быть изготовлены из стали, чугуна и цветных металлов. Они закрепляются стопорными винтами, ставятся на клей или выполняются на резьбе. После износа гильза заменяется новой.
3 Применение накладок. Для компенсации износа трущихся поверхностей применяют накладки. Для этого ремонтируемую поверхность обрабатывают на размер, компенсирующий износ и минимальную толщину накладки. В качестве накладок могут быть использованы различные материалы: текстолит, капрон, бронза, баббит, чугун. Накладки могут крепиться винтами или приклеиваться. Накладки являются компенсаторами износа, поэтому очередной ремонт узла упрощается. Кроме того, накладки применяются в качестве крепящих деталей, когда необходимо связать воедино деталь, получившую трещину, или деталь у которой отломилась какая-то часть. В ряде случаев механическое крепление накладкой или планкой восстанавливают на длительное время работоспособность дорогой детали.
4 Вмонтирование хвостовиков. В процессе эксплуатации у некоторых деталей отламываются хвостовики. Такие детали, могут быть восстановлены путём вставки новых хвостовиков, которые или запрессовывают и обваривают электросваркой, или завинчивают на резьбе.
5 Восстановление резьб. В чугунных деталях восстановление крепёжных резьб можно производить только заменой данной резьбы, другой, большей по размеру. При этом если новая резьба имеет тот же шаг что и исправляемая, отверстие иногда не рассверливают, а лишь нарезают резьбу метчиком следующего размера. Если же шаг резьбы не совпадает, отверстие приходится рассверливать а затем нарезать новую резьбу.
В стальных деталях резьба не выкрашивается, а растягивается, поэтому её часто исправляют прорезкой с помощью метчика того же размера. Если этого не достаточно, применяют такие же методы, что и для чугунных, или заваривают отверстие электросваркой, а затем просверливают новое отверстие и нарезают резьбу. Если все эти методы на приемлемы, приходится сверлить отверстие и нарезать резьбу в новых местах.
2 Восстановление деталей пластическим деформированием.
Обработка пластическим деформированием относится к числу прогрессивных технологических процессов восстановления, отделки и упрочнения поверхностей деталей ремонтируемого оборудования. К этим методам относятся: осадка, обжатие, раздача, вдавливание, вытяжка, растяжка, правка, накатка.
Вопрос 11 Правка.
Правка играет большую роль в восстановлении негодных деталей оборудования. Правильно применённая правка может полностью восстановить деталь, вернув ей первоначальные качества. Правка может осуществляться в холодном состоянии, с подогревом и путём термического воздействия. Обычно при ремонте правят полностью обработанные детали, поэтому подогревать их следует только в исключительных случаях, так как возможны нежелательные деформации и окисление.
Правка в холодном состоянии и с подогревом выполняется посредством приложения усилий вызывающих остаточную деформацию. Холодная правка ниже 0°С не производится, т.к. может привести к поломке деталей. Если выправить деталь в холодном состоянии невозможно, её подогревают до температуры ковки. Подогрев детали делает её более эластичной и позволяет теми же усилиями выправить детали больших сечений. Править в интервале температур 150-450°С не рекомендуется, т.к. при этих температурах в стальных деталях могут образовываться трещины. Правка деталей обычно производится на винтовых и гидравлических прессах. Проверку результатов правки валов производят в центрах. Правку не очень жёстких деталей часто выполняют на токарном станке с помощью ручного пресса, однако она применима лишь для валов небольших сечений.
Детали, изготовленные из листа, следует править в правильных вальцах. При их отсутствии правят вручную ударами молотка, нанося удары не по выпуклости, а по соседним с выпуклостями участкам. Если деталь имеет выпуклость в середине, удары следует наносить, начиная с краев к середине. При ручной правке применяют молотки из меди, латуни, свинца, а для тонкого материала - из дерева. Результаты правки проверяют на плите с помощью щупа или "на краску".
Суть правки заключается в укорочении участка детали (вогнутости), ранее удлинившегося вследствие каких-либо причин, и в удлинении участка детали (вогнутости), ранее изогнувшейся. Деталь, подвергаемая правке, укладывается на две опоры или ставится в центры выпуклостью кверху. Под точку наибольшей вогнутости ставится индикатор, по показаниям которого контролируют ход процесса. Нагрев обычно ведут сварочной горелкой, место наивысшего перегиба ограничивают накладками из мокрого листового асбеста.
Кроме ручной правки, погнутый металл и готовые детали правят механическим способом на правильных станках, прессах и с помощью специальных приспособлений.
Валы, не имеющие большого износа в рабочих местах, но погнутые от напряжений или по другим причинам, не следует заменять новыми. Целесообразно и выгодно такие валы восстанавливать правкой. Правят погнутые валы на токарном станке с применением пневматического приспособления, которое устанавливается на направляющие станины под заднюю бабку и перемещается по ним на роликах. Установленный в центрах вал проверяют индикатором на биение. Когда определено место наибольшего прогиба, его выравнивают бойком приспособления, действующего под давлением сжатого воздуха.
Вопрос13 Шабрение.
Обработка поверхности, выполняемая путём соскабливания тонкой стружки, называется шабрением. Толщина стружки при шабрении колеблется от 0,05 до 0,0005 мм. Шабрение чаще всего применяется как доводочная операция при обработке плоских и внутренних цилиндрических поверхностей. Шабрение производится при помощи специальных инструментов, называемых шаберами. Шаберам придают разнообразные формы и размеры применительно к обрабатываемым поверхностям. Шаберы изготавливаются из инструментальных сталей У10, У12 и закаливаются до 56-60 HRC. После заточки режущую кромку шабера следует периодически доводить путём притирки на чугунной плите.
Пришабривание чаще всего производится "по краске". Для этого на рабочую поверхность поверочного инструмента или детали, по которой ведётся пригонка (эталонная деталь или предварительно исправленная), наносится тонкий слой разведённой на машинном масле краски. Затем поверочный инструмент или деталь накладывают на подлежащую поверке поверхность и перемещают по ней. В результате перемещения в местах контакта остаются следы краски, отмечающие выступающие участки поверхности, подлежащие снятию шабером. Частота расположения закрашенных пятен определяет степень приближения точности обрабатываемой поверхности к эталонной.
При шабрении внутренней цилиндрической поверхности краска наносится на вал, которому затем сообщается качательное движение. Когда шабрением должна быть обеспечена особо высокая точность поверхности, краска на эталон не наносится, а шабрение ведут по блестящим пятнам (точкам), остающимся на шабруемой поверхности в результате контакта её с поверочным инструментом или сопряжённой деталью.
Припуски на шабрение должны быть минимальными, не более 0,1-0,2мм.
Качество шабрения определяется по числу пятен приходящихся на квадрат 25Х25 мм. Для различных поверхностей установленное число пятен различно от 6 до 20.
Притирка.
Обработка поверхностей с помощью порошков или паст для получения наиболее полного прилегания данной поверхности к эталонной или к поверхности сопрягаемой детали называется притиркой. Притирка применяется для создания плотных или герметичных соединений, а также доводки поверхностей. Припуск на притирку даётся в пределах 0,01-0,02мм.
Рисунок 27– Материалы, применяемые для притирки и доводки поверхностей.
В качества притирочных порошков применяются карборунд, корунд, наждак, толчёное стекло, окиси железа (корпусы), венская известь, окиси хрома и т.д. Порошки выбираются в зависимости от твёрдости материала притираемых деталей. Для притирки стальных деталей применяются корундовые и наждачные порошки; для притирки чугунных и бронзовых деталей - наждачный порошок и толчёное стекло. Порошки различаются по величине зерна. ГОСТ устанавливает номера зернистости, в зависимости от которых дроблённые абразивные материалы делятся на шлифзерно, шлифпорошки и микропорошки.
Притирка производится двумя способами: притирка деталей одна по другой и притирка деталей по эталонной поверхности. Первый способ при ремонте оборудования применяется чаще. При притирке тел вращения, если от соединения требуется герметичность, притираемой детали сообщают колебательные движения, вращая её на 30-45° попеременно то в одну, то в другую сторону.
Притирку начинают с более грубых порошков (паст) переходя постепенно к более тонким. Механизируют процесс притирки, применяя коловороты, дрели, ручные сверлильные машины.
В настоящее время широкое применение нашли алмазные порошки и алмазные пасты. Они позволяют вести притирку очень твёрдых поверхностей и обеспечивают более высокий класс чистоты. Применение абразивных паст позволяет повысить производительность процесса притирки.
Вопрос 14 Восстановление деталей клеевым методом.( 2 часа)
Клеевой метод широко используют при ремонте оборудования для восстановления неподвижных соединений. Он отличается простотой технологии, низкой себестоимостью и обеспечивает прочность и достаточную надёжность соединения.
Клеевым способом выполняют многие виды работ:
- заделывают трещины в корпусных деталях и накладывают заплаты;
- ликвидируют забоины и задиры на направляющих поверхностях оборудования;
- устанавливают детали-компенсаторы износа цапф, валов, шеек шпинделей, а также тонкостенные втулки в конусные отверстия шпинделей и пинолей задних бабок;
- восстанавливают резьбовые соединения и изношенные отверстия шкивов и маховиков;
- ремонтируют колодочные и конусные фрикционные муфты.
Достоинства:
- возможность соединения разнородных материалов при весьма малой их толщине;
- клеевой шов практически непроницаем для многих веществ и не разрушается от воздействия кислорода, воды, минеральных масел;
- склеенные поверхности можно обрабатывать на металлорежущих станках с применением СОЖ и всухую.
Недостатки:
- относительно низкая прочность на односторонний отрыв;
- меньшая долговечность по сравнению со сварными и клепанными соединениями;
- низкая теплостойкость.
Эпоксидный клей.
В настоящее время широкое распространение получил эпоксидный клей ЭД-5, ЭД-6. Основными составляющими клея являются эпоксидная смола (80-100%) и отвердитель - полиэтиленполиамин (7-16%). Для уменьшения хрупкости, повышения ударной вязкости и эластичности в состав клея вводят 10-16% пластификатора. Механическая прочность клеевого слоя повышается, если ввести в его состав 20-60% какого-либо наполнителя (уменьшается усадка, коэффициент термического расширения, регулируется вязкость клея), в качестве которого используют: металлические порошки из чугуна, стали, алюминия, бронзы, а также цемент, фарфоровую или кварцевую муку, графит и др.
Эпоксидная смола быстро (25-40 мин.) затвердевает при введении в неё отвердителя, а смесь смолы с пластификатором и наполнителем (без отвердителя) может хранится в закрытом состоянии в течении года. Готовый клей затвердевает за 24 ч при температуре 20-300, а при 60°С - 4 ч, при 120°С - 2 ч. Приготовленный клей нужно наносить на тщательно подготовленные поверхности.
Эпоксидными клеями склеивают изделия из однородных и разнородных металлов, пластмасс, фарфора, стекла и других материалов. Их используют для контровки болтов, заделки пороков литья, их применяют в клеесварных, клеезаклепочных и клеерезьбовых соединениях.
Карбинольный клей
Карбинольный клей применяют для склеивания металлов, стекла, пластмассы и др. материалов, а также для заделки пороков литья.Клей стоек к действию минеральных масел, но обладает недостаточной морозо- и влагостойкостью, теплостойкость не выше 600С, ограниченно вибростоек.
Основным составляющим является карбинол - бесцветная жидкость в виде сиропа со специфическим запахом, а также перекись бензоила. Для склеивания металлов обычно применяют чистый карбинол, доведенный до состояния густой массы, что необходимо для ускорения затвердения, так как жидкий клей затвердевает около 2 месяцев. Чугунные и стальные детали склеивают карбинолом с наполнителями, которые увеличивают механическую прочность.
Применяется для склеивания в различных сочетаниях стали, чугуна, алюминия, стекла, текстолита и др., а в виде клея-цемента - для заделки раковин и трещин.
Клей БФ
Наряду с карбинольным применяют универсальный клей БФ, представляющий спиртовой раствор различных термореактивных смол. Применяют следующие марки клея: БФ2, БФ4, БФ6. Их теплостойкость не выше 80 °С, предел прочности при сдвиге 40—60 МПа..
При помощи этих клеев могут быть склеены металлы пластмассы, керамика, дерево, фанера, фибра, эбонит, бумага и т.д. На поверхность детали клеи БФ наносят в два или три слоя с помощью кисти или шпателя с промежуточным просушиванием в течение 10—20 мин. Толщина клеевого слоя должна быть в пределах 0,1—0,2 мм. При большей толщине слоя силы сцепления молекул клея уменьшаются в 1,5—2 раза. После нанесения клеевого слоя детали стягивают струбцинами или специальными приспособлениями до получения давления 0,5—1 МПа и в таком виде просушивают при температуре 140—150 СС в течение 30— 60 мин. Эти клеи затвердевают быстрее карбинольного, однако для полного затвердения детали должны быть подогреты. При этом прочность соединений несколько ниже, чем полученных карбинольным клеем. Эксплуатация деталей после склеивания допускается после трёх суток.
Технологический процесс склеивания
1 Подготовка поверхности перед склеиванием (необходима для хорошегосцепления клеевого состава с материалом детали).:
- механическая обработка поверхности;
- очистка от грязи и окислов (Металлические поверхности зачищают наждачными кругами);
- обезжиривание авиационным бензином, ацетоном или спиртом;
- высушить поверхность.
Подготовку поверхности можно проконтролировать при помощи капли воды. Если она растекается, а не скатывается, то поверхность подготовлена удовлетворительно. Шероховатость должна соответствовать Ra=3.2
2 Подготовка клея.
3 Нанесение клея на склеиваемые поверхности (толщина до 0,1мм).
Те участки поверхностей, которые не подлежат склеиванию, покрывают разделительным слоем резинового клея, воска или мыла.
4 Совмещение склеиваемых поверхностей.
Оно должно быть таким, чтобы обеспечивалось не только точное наложение их друг на друга, но также вытеснение пузырьков воздуха из пространства между склеиваемыми поверхностями, равномерное распределение клея по шву, исключение самопроизвольного смещения одной детали относительно другой во время затвердения. До отвердения клея поверхности должны выдерживаться под давлением 0.3-1 МПа.
5 Удаление излишков клея с деталей.
6 Выдержка при определённом режиме. Процесс склеивания может выполняться как с подогревом с помощью различных нагревателей, так и без подогрева.
7 Контроль качества шва. Испытание на прочность или герметичность.
8 Обработка деталей после склеивания.
Дата добавления: 2018-05-02; просмотров: 1417; Мы поможем в написании вашей работы! |
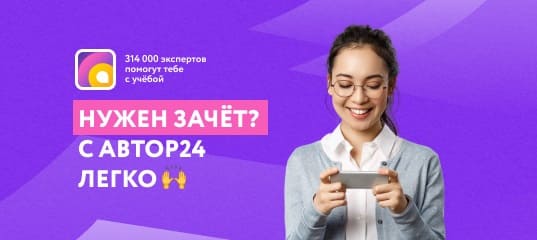
Мы поможем в написании ваших работ!