Механизированные способы сварки и наплавки
Вопрос (не будет) 2 вопрос Моральный износ – это несовершенство данной машины по сравнению с вновь создающимися того же назначения. Физический износ машин — результат изменения начальных свойств, нарушения конструктивных связей и нормального функционирования их элементов. В связи с износом ухудшаются эксплуатационные и эргономические характеристики машин, они теряют работоспособность и перестают отвечать своему назначению.
Механическое изнашивание
Механическое изнашивание наблюдается при механическом взаимодействии материалов изделия;
Механическое изнашиваниеподразделяют на абразивное, усталостное, кавитационное и изнашивание при заедании..
Абразивное изнашивание оказывает наиболее разрушительное действие на детали, оно наблюдается в тех случаях, когда трущиеся поверхности загрязняются мелкими абразивными и металлическими частицами.
Усталостное изнашивание является результатом воздействия на деталь переменных нагрузок, вызывающих усталость материала детали и его разрушение (возникновение трещин и отделение с поверхностного слоя частиц материала).
Кавитационное изнашивание-это разрушение материала от соприкосновения его с движущейся жидкостью, в которой нарушается сплошность ее объема из-за образования полостей, заполненных паром, газом или их смесью.
Изнашивание при заедании или износ схватыванием (Молекулярно-механическое изнашивание) происходит в результате механического взаимодействия материалов и одновременного воздействия молекулярных или атомарных сил;
|
|
Обычно он возникает при трении скольжения с относительно малыми скоростями перемещения трущихся поверхностей (менее одного метра в секунду) и большом удельном давлении при котором две сопрягаемые поверхности сближаются настолько плотно, что между ними начинают действовать молекулярные силы, приводящие их к схватыванию.
2 Коррозионно-механическое изнашивание
Коррозионно-механичесое изнашивание происходит в результате механического воздействия, сопровождаемого химическим или электрическим взаимодействием материала со средой. Он возникает под влиянием коррозии и механических факторов.
3 Эрозионное изнашивание- ото механическое изнашивание поверхности в результате воздействия на нее потока жидкости и (или)газа.
3вопросТиповой системой технического обслуживания и ремонта называется совокупность взаимосвязанных положений и норм, определяющих организацию и выполнение работ по техническому обслуживанию и ремонту оборудования с целью сохранения в течение обусловленного времени при заданных условиях эксплуатации производительности, точности и других показателей, гарантированных в сопроводительной технической документации.
|
|
Типовой системой регламентируется 2 вида работ:
а) техническое обслуживание, к которому относят работы по поддержанию работоспособности станков и машин при хранении, транспортировании, подготовке к использованию и использовании.
б) ремонт, к которому относят работы по поддержанию и восстановлению работоспособности и исправности оборудования.
По способу организации ТО различают плановое ТО и неплановое.
В состав планового ТО входит:
- плановый осмотр(О);
- ежесменный осмотр (Ое);
- периодический частичный осмотр (Оч);
- ежесменное поддержание чистоты оборудования и помещений (Че);
- ежесменное смазывание (Се);
- пополнение смазочных материалов (Сп);
- замена смазочных материалов (Сз);
- промывка механизмов и смазочных систем (П);
- регулирование механизмов, устройств, элементов, замена быстроизнашивающихся деталей и подтяжка крепежных деталей (Р);
- проверка геометрической и технологической точности (Пр);
- консервация (Ск).
При неплановом ТО проводят замену случайно отказавших деталей или восстановление их работоспособности и восстановление случайных нарушений регулировки
|
|
По способу организации ТС предусматривает два вида ремонтов:
а) плановый ремонт (ПР) – это ремонт, предусмотренный ТС и выполненный через установленное нормами этой системы число часов оперативного времени, отработанных оборудованием или при достижении установленного нормами технического состояния.
б) неплановый ремонт (НР) – это ремонт, предусмотренный ТС, но осуществляемый в неплановом порядке, по потребности, т.е. ремонт вызванный аварией оборудования
По составу работ предусматривается три вида плановых ремонтов: текущий, средний и капитальный.
Текущий ремонт (ТР) – это ремонт выполняемый для обеспечения или восстановления роботоспособности оборудования и состоящий в замене и (или) восстановлении отдельных частей.
Средний ремонт (СР) – это ремонт, выполняемый для восстановления исправности и частичного восстановления исправности и частичного восстановления ресурса оборудования с заменой или восстановлением составных частей ограниченной номенклатуры и контролем технического состояния составных частей, выполняемых в объеме, установленном в нормативно- технической документации.
|
|
Капитальный ремонт (КР) – этот ремонт, выполняемый для восстановления исправности и полного или близкого к полному восстановлению ресурса изделия с заменой или восстановлением любых его частей, включая базовые.
К комплексу работ по восстановлению работоспособности оборудования относится также аварийный ремонт.
Аварийный ремонт (АР) – это неплановый ремонт, вызванный дефектами конструкции или изготовления оборудования, дефектами ремонта и нарушением правил технической эксплуатации.
Вопрос 4 . Все работы по плановому техническому обслуживанию и ремонту выполняются в определенной последовательности, образуя повторяющиеся циклы.
Ремонтный цикл (Цр)- это повторяющаяся совокупность различных видов планового ремонта, выполняемых в определенной последовательности через установленные равные числа часов оперативной работы оборудования, называемые межремонтными периодами. ИЛИ Ремонтный цикл - это время работы оборудования от начала ее эксплуатации до первого капитального ремонта или между двумя капитальными ремонтами.
Ремонтный цикл определяется структурой и продолжительностью и завершается капитальным ремонтом.
Структура ремонтного цикла -это перечень ремонтов, входящих в его состав, расположенных в последовательности их выполнения. Например, структуру ремонтного цикла, состоящего из 4-х текущих, 1-го среднего и 1-го капитального ремонта, записывают так: КР-ТР-ТР-СР-ТР-ТР-КР.
Продолжительность ремонтного цикла (Тцр) - это число часов оперативного времени работы оборудования, на протяжении которого производятся все ремонтные работы, входящие в состав цикла.
Продолжительность ремонтного цикла изображают размерной линией между обозначениями капитальных ремонтов, которыми начинается и завершается цикл. Над размерной линией указывают продолжительность ремонтного цикла, в часах.
КР-ТР-ТР-СР-ТР-ТР-КР
Межремонтный период (Тмр) - это период оперативного времени работы оборудования между двумя последовательно выполняемыми видами ремонта.
Продолжительность межремонтного периода равна продолжительности ремонтного цикла, деленной на число внутрицикловых ремонтов плюс 1.
Период между двумя последовательными плановыми осмотрами называется межосмотровым периодом.
Рекомендуемые структуры ремонтного цикла для различых металлорежущих станков и другого оборудования приведены в таблице 1.3 /1/.
Цикл технического обслуживания (Цо) - это повторяющаяся совокупность операций различных видов планового технического обслуживания, осуществляемых через установленные для каждого вида оборудования числа часов оперативного времени работы, называемые межоперационными периодами (Тмо).
Цикл ТО определяется структурой и продолжительностью.
Структука цикла ТО - это перечень операций планового технического обслуживания, входящих в состав цикла, с коэффициентам, показывающими число операций каждого вида в цикле.
Структуру цикла ТО изображают в виде суммы входящих в него операций. Для обозначения числа операций, которые выполняются ежедневно, в качестве коэффициента ставят букву Е.
Например: ЕОе+4Сп+Сз+Оч+2Р,
где ЕОе - ежесменный осмотр;
4Сп - 4 пополнения смазочного материала;
Сз - замена смазочного материала;
Оч - частичный осмотр;
2Р - две профилактические регулировки.
Продолжительность цикла технического обслуживания (Тцо) и продолжительность межремонтного периода (Тмр) равны между собой, т.к. все операции планового технического обслуживания выполняются между двумя последовательными плановыми ремонтами.
Межоперационный период обслуживания (Тмо) - это период оперативной работы оборудования между двумя одноименными операциями планового технического обслуживания.
Для различных видов оборудования и различных условий эксплуатации однотипного оборудования Типовой системой определены разные по структуре и продолжительности ремонтные циклы и числа плановых осмотров в циклах ТО. Структуры циклов ТО устанавливают по данным карт планового технического обслуживания.
Зависимости для определения продолжительности ремонтного цикла, межремонтного периода, межосмотрового периода для различного оборудования приведена в таблице 1.4 /1/.
5 вопрос При выборе способа восстановления деталей и сборочных единиц за основу принимают экономическую целесообразность восстановления, наличие на предприятии необходимого оборудования и материалов, технологические и конструктивные особенности деталей, величину и характер их износа и др.
Целесообразность способа восстановления и упрочнения деталей зависит от многих факторов: от условий их работы, характера сопряжения, нагрузок скорости перемещения подвижных деталей, смазка и т.д.
Основным показателем оценки экономической эффективности восстановления и определения целесообразности того или иного способа восстановления и упрочнения служит относительная себестоимость, т.е. себестоимость восстановления детали отнесённая к её сроку службы после ремонта. Выгодным является тот метод, который полностью восстанавливает техническую характеристику детали и при этом стоимость восстановления ниже стоимости изготовления новой детали, а сроки восстановления короче. Показатель относительной себестоимости является комплексным показателем, так как отражает не только все элементы затрат, но и износостойкость деталей после их восстановления. Однако немаловажное значение имеют продолжительность и трудоёмкость процесса, а так же дефицитность применяемых материалов.
Сущность метода ремонтных размеров заключается в том, что восстанавливают геометрическую форму ремонтируемой сопрягаемой детали снятием минимального слоя металла с её изношенных поверхностей до удаления следов износа без сохранения первоначальных размеров детали. У более дорогостоящей детали сопряжения неравномерный износ устраняют механической обработкой, а менее дорогостоящую деталь заменяют новой, имеющей измененный (ремонтный) размер. Сопряжение деталей затем восстанавливается с помощью детали компенсатора. Этот способ носит название способ ремонтных размеров.
Ремонтным размером называют размер, до которого производится обработка изношенной поверхности при восстановлении детали. Для валов ремонтные размеры будут меньше номинальных размеров новой детали, а для отверстий - больше. Наиболее часто этот способ применяют для сопрягаемых деталей типа "вал-втулка".
Новый ремонтный размер будет равен номинальному размеру детали минус сумма величины износа и припуска на обработку.
Ремонтные размеры делятся на свободные и регламентированные.
Свободным называется размер, величина которого не устанавливается заранее, а получается непосредственно в процессе обработки. Их ещё называют пригоночными, т.е. установленные с учётом припуска на пригонку детали "по месту". К полученному свободному ремонтному размеру подгоняют соответствующий размер сопрягаемой детали методом индивидуальной пригонки.
Регламентированный ремонтный размер - это заранее установленный размер, до которого ведут обработку изношенной поверхности при её исправлении. Регламентированные ремонтные размеры называют также категорийными.
Вопрос
Сварка применяется как способ неразъёмного соединения деталей, а также для восстановления изношенных деталей с изломами, трещинами, сколами и др. дефектами.
Наплавкой, являющейся разновидностью сварки, металлические детали или части не соединяют в одно целое, а наращивают, наплавляя на основной металл присадочный материал газовой сваркой или электросваркой. Наплавкой восстанавливают изношенные поверхности деталей, посадочные размеры которых затем получают механической обработкой на станках. В качестве наплавочных материалов применяют литые и порошковые твёрдые сплавы содержащие карбиды марганца, хрома, вольфрама, титана и др. наплавку выполняют теми же способами, что и сварку.
Достоинства сварки и наплавки:
- быстрота выполнения операций;
- относительная несложность используемого оборудования;
- экономичность процессов.
Однако сварка и наплавка имеют ряд недостатков:
-изменение структуры основного металла в зоне термического влияния и появление местных напряжений, приводящее к короблению деталей, снижению усталостной прочности и даже появлению трещин; при сварке и наплавке происходит нагрев восстанавливаемой детали, вызывающий деформации и возникновение внутренних напряжений, для ликвидации которых необходимо осуществлять термическую обработку, которая в свою очередь может быть причиной деформации деталей.
- затруднения при сварке и наплавке деталей из высокоуглеродистых и легированных сталей и изготовленных из чугуна.
При ремонте технологического оборудования наибольшее распространение получили дуговая и газовая сварка и наплавка деталей.
Дуговая сварка и наплавка.
Осуществляется угольными и металлическими электродами путём расплавления электрода и металла теплом электрической дуги, таким образом в месте контакта образуется ванночка с жидким металлом, который охлаждаясь соединяет края свариваемых деталей.
Для защиты жидкого металла от вредного воздействия окружающей атмосферы электроды покрывают специальными обмазками или процесс выполняют в защитных средах (углекислый газ, аргон, азот или их комбинации). Когда защитной средой является сыпучая смесь (флюсы), процесс называют сваркой под слоем флюса.
Источники питания сварочной дуги. Для дуговой сварки и наплавки используют источники переменного или постоянного тока. Источники переменного тока — сварочные трансформаторы
Шире применяется сварка на переменном токе, т.к. меньше расход электроэнергии, меньше стоимость оборудования и легче осуществлять его обслуживание.
Газовая сварка и наплавка
Широко применяется в ремонтном производстве и заключается в плавлении металла теплом горящего газа (ацетилен при t=3300°С, пропан-бутан, метан и др) в струе чистого кислорода. Газовая сварка позволяет использовать почти любой присадочный материал, поэтому она нашла широкое применение для восстановления деталей изготовленных из различных материалов. В ремонтном производстве наибольшее распространение получила ацетилено-кислородная сварка и наплавка. Используя ацетилено-кислородное пламя, выполняют следующие работы: сварку черных и цветных металлов и сплавов, наплавку твердых сплавов, резку металлов, поверхностную закалку, пайку твердыми припоями, сварку пластмасс.
Для уменьшения влияния кислорода, азота и водорода на качество наплавляемого металла применяют флюсы.
Механизированные способы сварки и наплавки
На ремонтных предприятиях широкое распространение получили:
- сварка и наплавка под слоем флюса;
- вибродуговая наплавка;
- сварка и наплавка в среде защитных газов;
- сварка и наплавка порошковой проволокой;
- и др.
Сварка и наплавка деталей под слоем флюса. Суть автоматической сварки (наплавки) в том, что электрод-проволока 3 подаётся к месту образования дуги автоматически, зона дуги 1, также автоматически, прикрывается подающимся порошковым флюсом 2 , который создает шлаковую защиту 7. Сварочная дуга, возникающая между электродом и наплавляемой деталью, горит под жидким слоем расплавленного флюса в пространстве 4, которое образовано парами и газами, выделяемые в стволе дуги. Расплавленный металл 5, предохранен от соприкосновения с кислородом и азотом воздуха, что улучшает качество формирования шва.
Вибродуговая наплавка.
Разновидность дуговой наплавки плавящимся металлическим электродом.
Суть вибродуговой наплавки состоит в том, что электроду при сварке сообщаются колебания частотой 50-100 Гц с помощью электромагнитного или механического устройства. В результате непрерывная дуга превращается в прерывистую - металл, наплавляющий поверхность, подаётся на неё небольшими порциями. На суппорте токарного станка закрепляют наплавочную головку ( ОКС-6569 или ОКС -1252) Для питания используют источники постоянного тока ( генераторы АНД-500/250, выпрямители ВС-300 и ВС-600, преобразователи ПД-305 и ПСГ-500)
Наплавка может вестись в один или несколько слоёв. За один приём можно нарастить слой металла до 4 мм. Восстановление валов, фланцев и других деталей типа тел вращения вибродуговой наплавкой возможно на токарном станке, на суппорт которого устанавливается виброголовка (получающая продольную или поперечную подачу), а в центрах или патроне закрепляется деталь.
Автоматическая и полуавтоматическая сварка и наплавка в среде защитных газов Используется в тех случаях, когда невозможно или трудно применить автоматическую сварку под слоем флюса. Широко применяется для ремонтных работ. Состоит в том, что в зону горения электрической дуги 4 под давлением через газоэлектрическую горелку 2, подается защитный газ 3, благодаря которому столб дуги, а также сварочная ванна изолируется от кислорода и азота воздуха. Для создания защитной атмосферы используется обычная углекислота, сварочный углекислый газ или аргон. Сварка может производится плавящимися и неплавящимися электродами 1. При сварке неплавящимися –дуга горит между угольным или вольфрамовым электродом и деталью (дуга плавит металл детали или присадочный материал), а при сварке плавящимся –между электродной проволокой и изделием ( плавится проволока и основной металл) .
Технологическая последовательность сварки и наплавки:
- подготовка деталей к сварке или наплавке (очистка; промывка; обезжиривание, разделка шва ( для сварки));
- сварка или наплавка;
- контроль качества покрытия;
- механическая обработка .
При механической обработке деталей после наплавки в виду наличия неравномерных припусков, неоднородности свойств наплавленного металла механическая обработка наплавленного слоя в зависимости от твердости и требований качества поверхности применяют обработку на токарных и шлифовальных станках. При твердости до HRC40 возможна токарная обработка.
7 вопрос Нанесение расплавленного металла на поверхность детали струей сжатого воздуха называется металлизацией.
Сущность процесса состоит в том, что расплавленный в специальном приборе-металлизаторе каким-либо источником тепла металл подхватывается струёй воздуха или газа и мельчайшими частицами переносится на предварительно подготовленную поверхность детали.
Металлизация широко применяется в ремонтной практике, т.к. позволяет наносить слой покрытия толщиной до 10 мм на любой металл и другие различные материалы (дерево, резина, пластмасса).
3 Типовой маршрутный техпроцесс металлизации.
При всех способах ремонта деталей металлизацией технологический процесс состоит из подготовки детали к металлизации, нанесения покрытия и обработки детали после металлизации.
1. Подготовка поверхности следует выполнять непосредственно перед нанесением покрытия. Разрыв времени между этими операциями должен быть минимальным ( не более 1 часа)
а) очистка от загрязнений .
б) обезжиривание Промывка растворителями, обработка в моечных машинах.
в)механическая обработка детали для придания правильной геометрической формы (При металлизации тел вращения), устранение неровностей, задиров . При нанесение покрытия на плохо сцепляющийся материал и на детали, где нежелательна механическая обработка наносят молибден, который хорошо сцепляется со всеми материалами и полированными поверхностями.
г) создания на поверхности детали шероховатой поверхности с целью улучшения сцепления покрытия с основным металлом. Для дополнительного крепления слоя наплавляют сваркой или оставляют при механической обработке буртики или прорезают канавки, кромки которых перед металлизацией слегка закатывают. Нарезание рваной резьбы д) нанесение промежуточного слоя из смеси никеля с алюминием;
е) изолирование неметаллизируемых поверхностей специальной пастой, бумагой, картоном, а отверстий-деревянными или резиновыми пробками.
2. Нанесение покрытия:
При металлизации тел вращения деталь закрепляют в центрах токарного станка, а металлизатор устанавливают на суппорте. При металлизации плоских поверхностей напыление осуществляют при помощи металлизатора вручную. Толщина покрытия должна обеспечивать устранение износа и припуск на обработку: 0,6-1мм под обтачивание и 0,4-0,6мм под шлифование.
3. Механическая обработка точением или шлифованием (не менее чем через 24ч, из-за усадки поверхности).
В зависимости от припуска на обработку, твердости и требований качества поверхности напыленного слоя выполняют токарную обработку или шлифование. При точении напыленных покрытий применяют резцы из сплава Т15К6 с пониженными режимами резания: глубина резания 0,1—0,3 мм, подача 0,1—0,15 мм/об.
4. Контроль качества.
В зависимости от источника расплавления металла различают следующие виды металлизации: газопламенную, дуговую, высокочастотную, плазменную.
Вопрос
Процесс нанесения металла на поверхность детали путем кристаллизации его из водного раствора солей при прохождении электрического тока (электролитическим способом) называется гальваническим покрытием.
В электролитическую ванну вносят два электрода. Деталь, расположенная на специальных подвесках, обычно является отрицательным электродом-катодом, а положительным электродом-анодом является либо металл, соль которого находится в растворе, либо металл, который нерастворим в электролите. При пропускании через электролит постоянного тока молекулы раствора расщепляются на положительно заряженные частицы — катионы, которые перемещаются к отрицательному электроду (катоду), где осаждаются, превращаясь в нейтральные атомы, и отрицательно заряженные частицы — анионы, перемещающиеся к положительному электроду (аноду), где также теряют свой заряд и превращаются в нейтральные атомы.
При пропускании постоянного тока через электролит на поверхности детали осаждается необходимый металл.
В качестве анода применяют пластины из меди, свинца, цинка и др. металлов. Применяют растворимые и нерастворимые аноды. В основном применяют растворимые аноды, а нерастворимые – свинцовые применяют только при хромировании.
Рисунок 12– Металлы для электрохимических и химических покрытий
1.1 Хромирование - это процесс электролитического наращивания хрома на поверхность ремонтируемых деталей. (слой до 0,2 мм)
Хромовые покрытия применяют для восстановления размеров изношенных деталей, а также в качестве антикоррозионного и декоративного покрытия.
Перед хромированием деталь очищают от грязи затем шлифуют (снимают минимальный слой металла для удаления следов износа и придания им правильной геометрической формы), полируют, обезжиривают протравливают для удаления оксидных плёнок.
Технологическая последовательность при хромировании:
Хромирование слагается из подготовительных операций, собственно хромирования и заключительных операций после наложения хрома.
Дата добавления: 2018-05-02; просмотров: 645; Мы поможем в написании вашей работы! |
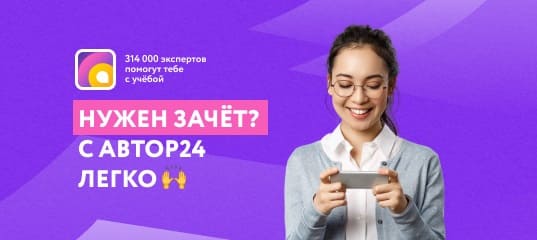
Мы поможем в написании ваших работ!