ПОРЯДОК ВЫПОЛНЕНИЯ ВИЗУАЛЬНОГО КОНТРОЛЯ СВАРНЫХ СОЕДИНЕНИЙ (НАПЛАВОК)
3.5.1. Визуальный контроль сварных соединений выполняется при производстве сварочных работ (послойный контроль в процессе сварки с фиксацией результатов контроля) и на стадии приемо-сдаточного контроля готовых сварных соединений.
Послойный контроль в процессе сварки выполняется в случаях, например, невозможности проведения неразрушающих методов контроля или в случаях, оговоренных в рабочих чертежах при согласовании с Заказчиком и головной материаловедческой организацией (последнее - для объектов атомной энергетики).
3.5.2. Визуальный послойный контроль в процессе сварки соединений выполняется с целью подтверждения отсутствия недопустимых поверхностных дефектов (трещин, пер, включений, западаний между валиками, наплывов) в каждом слое (валике) шва.
Выявленные при контроле дефекты подлежат исправлению перед началом сварки последующего слоя (валика) шва.
Сварные соединения, выполненные с послойным визуальным контролем, подлежат дополнительно контролю капиллярным или магнитопорошковым методом на доступных участках.
3.5.3. При визуальном контроле сварного соединения (наплавки) проверяется:
- отсутствие (наличие) поверхностных трещинвсех видов и направлений;
- отсутствие (наличие) на поверхности сварных соединений и наплавок дефектов (пор, включений, скоплений пор и включений, отслоений. прожогов, свищей, наплывов, усадочных раковин, подрезов, не проваров, брызг расплавленного металла, а также мест касания сварочной дугой поверхности основного материала):
|
|
- наличие зачистки металла в местах приварки временных технологических креплений, гребенок индуктора и бобышек крепления термоэлектрических преобразователей (термопар), а также отсутствие поверхностных дефектов в местах зачистки;
- наличие зачистки поверхности сварного соединения изделия (сварно, о шва и прилегающих участков основного металла) под следующий контроль неразрушающими методами;
- наличие маркировки (клеймения) шва (наплавки) и правильности ее выполнения.
3.5.4. В сварном соединении необходимо измерить;
- размеры поверхностных дефектов (поры, включения и др.). выявленных при визуальном контроле:
- высоту и ширину шва, а также вогнутость и выпуклость обратной стороны шва в случае доступности обратной стороны шва для контроля;
- высоту (глубину) углублений между валиками (западания межвалико-вые) и чешуйчатости поверхности шва;
- размеры подрезов основного материала;
- протяженность не сплавления (не провары) с наружной и внутренней стороны шва.
Требования к выполнению измерений при контроле сварных швов приведены на рис.9 и в таблице 8.
|
|
Таблица 8 - Требования к измерениям сварных швов
Контролируемые па-. раметры | Условное обозначение (рис.9) | Номер Рисунка | Средства измерений. Требования к измерениям |
1 | 2 | 3 | 4 |
1. Ширина шва | е,е1 | 9а.б | Штангенциркуль ШЦ-1 или шаблон универсальный. Измерение - см. п. 3.5.5 |
2. Высота шва | g, g1 | 9а.б | То же |
3. Выпуклость обратной стороны шва | g1 | 9а | Штангенциркуль ШЦ-1. Измерение согласно п. 3.5.5. |
4. Вогнутость обратной стороны шва | g2 | 9б | Штангенциркуль ШЦ-1, в т.ч. модернизированный (рис.10). Измерения в 2-3 местах в зоне максимальной величины |
5. Глубина подреза (неполного заполнения разделки) | b2, bЗ | 9г | Штангенциркуль ШЦ-1, в т.ч. модернизированный (рис.10). Измерения согласно п.3.5.5. |
в. Катет углового шва | К.К1 | 1г,д | Штангенциркуль ШЦ-1 или шаблон. Измерение- согласно п.3.5.5, |
7. Чешуйчатость шва | Δ1 | 1ж | Штангенциркуль ШЦ-1, в т.ч. модернизированный (рис.10). Измерения не менее, чем в 4 точках по длине шва |
8. Глубина западаний между валиками | Δ 2 | 1з | Тоже |
9. Размеры (диаметр, длина, ширина) одиночных несплошностей | dg. lg. bg | 1и | Лупа измерительная. Измерению подлежит каждая несплошность |
|
|
Рисунок 9 - Размеры сварною шва. подлежащие измерению.
а) и б) размеры (ширина, высота) стыкового одностороннего шва с наружной и внутренней стороны: в) то же двухстороннего сварного шва; г) подрез или неполное заполнение разделкикромок; д) чешуйчатость (Δ1) шва и западание между валиками шва (Δ2); е) размеры поверхностных включений (диаметр - dg. длина - Ig, ширина – bg, включения): ж) размеры катета шва таврового (углового, нахлесточного) соединения.
3.5.5. Высота и ширина сварного шва должна определяться не реже, чем через один метр по длине соединения, но не менее, чем в трех сечениях равномерно расположенных по длине шва.
При контроле стыковых сварных соединений труб с наружным диаметром до 89 мм включительно и с числом однотипных соединений более 50 на. одном изделии допускается определение размеров шва на 10-20% соединений в одном или двух сечениях, при условии, что при визуальном контроле, которому подвергают асе соединения, не возникло сомнений а части размеров (ширина, высота)шва.
3.5.6. Измерение толщины наплавленного антикоррозионного покрытия на цилиндрических поверхностях проводится не реже. чем через 0,5 м в осевом направлении и через каждые 60° по окружности при ручной наплавке и 90° при автоматической наплавке..
|
|
При автоматической наплавке на плоских и сферических поверхностях проводят не менее одного измерения на каждом участке размером 0,5м х 0,5м (длина х ширина)
3.5.7. При контроле сварных угловых соединений определяют катеты сварного шва. Определение высоты, выпуклости и вогнутости углового шва выполняется только в тех случаях, когда это требование заложено в рабочих чертежах. Измерение выпуклости и вогнутости производится с помощью специальных шаблонов, а определение высоты углового шва расчетным путем.
3.5.8. Измерение глубины западаний между валиками при условии, что высоты валиков отличаются друг от друга, должно выполняться относительно валика. имеющего меньшую высоту. Аналогично определяют и глубину чешуйчатости валика (по меньшей высоте двух соединений чешуек).
3.5.9. Измерение размеров, указанных в п.3.5.5 • 3.5.8 и таблице 8 выполняют а первую очередь на участках шва, вызывающих сомнение в части размеров по результатам визуального контроля.
3.5.10. Выпуклость (вогнутость) стыкового шва оценивается по максимальной высоте (глубине) расположения поверхности шва от уровня расположения наружной поверхности деталей. В том случае, когда уровень поверхности деталей одного типоразмера (диаметр, толщина) отличаются друг от друга, измерения следует проводить относительно уровня поверхности детали, расположенной выше уровня поверхности другой детали (рис.11).
В том случае, когда выполняется сварка деталей с различной толщиной стенки и уровень поверхности одной детали превышает уровень поверхности второй детали, оценку выпуклости (вогнутости) поверхности шва выполнять относительно линии, ссоединяющей края поверхности шва а одном сечении (рис.12) с помощью специального шаблона.
1 - штангенциркуль ГОСТ 166
2 - опора
Рисунок 10 • Штангенциркуль типа ШЦ-1 с опорой
Рисунок 11 - Схема измерения высоты шва стыкового соединения при различном уровне наружных поверхностей деталей, вызванном смещением при сборке соединения.
3.5.11. Выпуклость (вогнутость) углового шва оценивается по максимальной высоте (глубине) расположения поверхности шва от линии, соединяющей края поверхности шва в одном поперечном сечении (рис.13).
3.5.12. Размеры выпуклости (вогнутости) стыкового (рис.12) и углового (рис.13) шва определяются специальными шаблонами,
Рисунок 12 - Схема измерения высоты шва стыкового соединения при различном уровне наружных поверхностей деталей, вызванном разницей в толщине стенок.
Рисунок 13 - Схема измерения выпуклости (д) и вогнутости (д2) наружной поверхности и высоты (h) углового шва.
Рисунок 14 - Схема измерения выпуклости (д1) и вогнутости (д2) обратной стороны стыкового одностороннего шва.
3.5.13. Выпуклость (вогнутость) корня шва оценивается по максимальной высоте (глубине) расположения поверхности корня шва от уровня расположения внутренних поверхностей сварных деталей.
В том случае, когда уровни внутренних поверхностей разные, измерения следует проводить согласно схемы, приведенной на рис.14.
3.5.14 Схемы измерения отдельных размеров Сварного соединения с помощью шаблона универсального типа УШС приведены на рис. 15.
а)
в)
Рисунок 15 - Схема измерения размеров сварного i с помощью талона УШС
а» измерение высоты шва и глубины подреза;
б) измерение ширины шва;
в) измерение западаний между валиками
3.5.15. Измерения чешуйчатости и западаний между валиками шва, глубины и высоты углублений (выпуклостей) в сварном шве и основная металле, s т.ч. при техническом диагностировании, разрешается определять по слепку снятому с контролируемого участка. Материалом для слепка могут служить пластилин, воск, гипс и другие материалы. Измерения проводят с помощью измерительной лупы или на микроскопе после разрез»» слепка механическим путем.
3.5.16. Измерения перелома осей цилиндрических элементов и угловое смещение плоскостей плоских деталей, а также несимметричности штуцера выполнять при контроле сварных узлов и деталей (см. п. 3.6.9 и 3.6.10).
Дата добавления: 2018-04-15; просмотров: 1739; Мы поможем в написании вашей работы! |
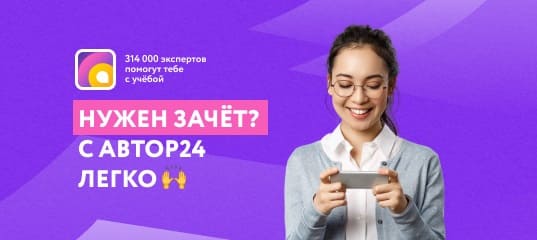
Мы поможем в написании ваших работ!