ТРЕБОВАНИЯ К ВЫПОЛНЕНИЮ ВИЗУАЛЬНОГО И КОНТРОЛЯ
ПОДГОТОВКА РАБОЧЕГО МЕСТА
3.1.1. Визуальный и визуально-оптический контроль, как правило, должен выполняется на стационарных участках, которые должны быть оборудованы столами, стендами, роликоопорами и др. средствами, обеспечивающими удобство выполнения работ.
3.1.2. Визуальный и визуально-оптический контроль при монтаже и ремонте оборудования, конструкции и трубопроводов, а также при техническом диагностировании изделий выполняется непосредственно по месту Монтажа (ремонта) или расположения изделия. В этом случае, должен быть обеспечен подход к месту производства контрольных работ, созданы условия для безопасного производства работ, в т.ч. оборудованы леса. ограждения, подмости, а также обеспечена возможность подключения ламп местного освещения напряжением 12 вольт.
3.1.3. Участки контроля, особенно стационарные, следует располагать на наиболее освещенных местах цеха. имеющих естественное освещение. Не зависимо от наличия естественного освещения участки контроля должны быть также оборудованы искусственным освещением, в т.ч розетками переменного тока для подключения переносных осветительных приборов Освещенность контролируемых поверхностей должна быть достаточной для надежного выявления дефектов и соответствовать требования ГОСТ 23479, но в любом случае должна быть не менее 300 Лк.
Окраску поверхностей стен, потолков, рабочих столов и стендов на участках визуального и визуально-оптического контроля рекомендуется выполнять в светлых тонах (белый голубой, желтый, светло-зеленый, светло-серый) для увеличения контрастности контролируемых поверхностей деталей, повышения контрастной чувствительности глаз и снижения-общего утомления специалиста.
|
|
ПОДГОТОВКА ОБЪЕКТА К КОНТРОЛЮ
3.2 1. Подготовка объекта к визуальному и визуально-оптическому контролю производится подразделениями предприятия (организации), выполняющими изготовление, монтаж или ремонт.
Подготовка объекта к техническому диагностированию выполняется службами Заказчика.
Подготовка изделий к контролю в обязанности специалиста по контролю не входит.
3.2.2 Паровые и водогрейные котлы, сосуды и трубопроводы, подлежащие визуальному и визуально-оптическому контролю при техническом диагностировании, должны быть выведены из работы, охлаждены, дренированы, отключены от соседних котлов и трубопроводов. Внутренние устройства сосудов в случае необходимости должны быть удалены, а тепловая изоляция и обмуровка, препятствующие контролю технического состояния основного металла и сварных соединений должны быть частично или полностью удалены в местах, оговоренных программой работ по техническому диагностированию.
|
|
3.2.3. Перед проведением визуального и визуально-оптического контроля поверхность объекта в зоне контроля подлежит зачистке до чистого металла от ржавчины, окалины, грязи, краски, масла, шлака, брызг расплавленного металла, продуктов коррозии и других загрязнений, препятствующих проведение контроля. Зона зачистки должна определяться НД на вид работ или на изготовление изделия. При отсутствии требования а НД зона зачистки деталей и сварных швов должна составлять;
- при зачистке кромок деталей под дуговую и газовую сварку - не менее 20 мм с наружной стороны и не менее 10 мм с внутренней стороны от кромок разделки детали;
- при зачистке кромок деталей под электрошлаковую сварку - не менее 50 мм;
- при зачистке кромок деталей при угловых соединения труб (вварка штуцера в коллектор, трубу или барабан) - зачистке подлежат: поверхность вокруг отверстия в трубе (коллекторе, барабане) на расстоянии 15-20 мм, поверхность "очка" - на всю глубину и поверхность привариваемого штуцера - на расстоянии не менее 20 мм от кромки разделки;
- при зачистке стального подкладного остающегося кольца или расплавляемой проволочной вставки - вся наружная поверхность подкладного кольца и вся поверхности расплавляемой вставки:.
|
|
- при зачистке сварного шва деталей - шов и прилегающие " нему участки основного материала деталей; ширина зона зачистки основного материала должна составлять не менее 20 мм в каждую сторону от шва при всех видах дуговой и газовой сварки и не менее 100 мм - при электрошлаковой сварке.
3.2.4 Зачистка поверхностей деталей (изделий) и сварных соединений перед контролем производится металлическими щетками, напильником или абразивным кругом.
При зачистке деталей и сварных швов из аустенитных сталей и высоконикелевых сплавов должны применяться щетки, изготовленные из нержавеющей нагартованной проволоки.
3.2.5. Шероховатость зачищенных под контроль поверхностейдеталей (сварных соединений) должна составлять не более Ra 12.5 (Rz 80).
3.2.6. Шероховатость поверхностей изделий и сварных соединений для проведения последующих видов контроля неразрушающими методами зависит от метода контроля и должна быть не более:
Ra 3,2 (Rz 20) при капиллярных видах контроля;
Ra 10 (Rz 63) - при магнитопорошковом методе контроле;
Ra 6.3 (Rz 40) - при ультразвуковых видах контроля.
Для других методов неразрушающего контроля шероховатость контролируемых поверхностей изделий устанавливается конструкторской и технологической документацией.
3.2.7 Шероховатость поверхностей разделки кромок деталей (сборочных единиц, изделий), подготовленных под сварку, должна быть не более Ra 12,5 (Rz 80).
Дата добавления: 2018-04-15; просмотров: 357; Мы поможем в написании вашей работы! |
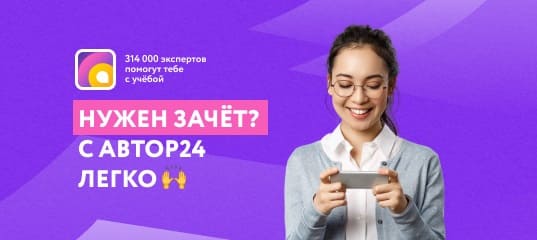
Мы поможем в написании ваших работ!