ПНЕВМАТИЧЕСКИЕ И ГИДРАВЛИЧЕСКИЕ ТРАНСПОРТИРУЮЩИЕ УСТРОЙСТВА
План лекции
28.1 Общие сведения
28.2 Принцип действия и расчет пневмотранспортных установок.
28.3Аэроднища и аэрожелоба.
28.4 Гидравлические транспортирующие устройства.
Общие сведения
Пневматическое и гидравлическое транспортирование основано на сообщении сыпучим материалам большой скорости, движущимся потоком воздуха или воды.
Преимущества:
- высокая производительность за счет механизации процесса захвата, транспортировки и разгрузки материала при небольшом числе обслуживающего персонала;
- герметичность трассы перемещения материла;
- возможность перемещения материала в горизонтальном, наклонном и вертикальном направлении;
- удобство монтажа в стесненных условиях;
- возможность совмещения нескольких технологических операций;
- высокая степень автоматизации процесса транспортировки и распределения материала;
- возможность подачи материала одновременно из нескольких пунктов загрузки к нескольким пунктам разгрузки;
- широкий диапазон производительности (до 300 т/ч) и расстояния транспортировки (до 1,5 км).
Недостатки:
- высокий расход энергии на единицу транспортируемого груза (в 8…14 раз выше механических устройств);
- быстрый износ отдельных частей установки, взаимодействующих с грузом;
- необходимость тщательной очистки используемого и отработанного воздуха и воды;
- необходимость тщательного отбора транспортируемого материала с учетом его физико-механических свойств.
|
|
Принцип действия и расчет пневмотранспортных установок
В трубопроводах пневматических транспортирующих устройств (ПТУ) воздушный поток создается искусственным путем.
Различают три системы пневматического транспортирования: всасывающую, нагнетательную и смешанную.
При всасывающей системе материал, подаваемый в транспортный трубопровод, перемещается по нему вследствие разрежения воздуха. В нагнетательной системе перемещение материала происходит под действием нагнетания воздуха в трубопровод. Смешанная система ( всасывающе-нагнетательная) имеет отдельные участки с разрежением и сжатием воздуха.
Рисунок 28.1 – Схема всасывающей системы
Установка всасывающего типа (рисунок 28.1) работает за счет перепада вакуума, создаваемого вакуум-насосом в транспортной магистрали. Материал через всасывающее сопло 1 попадает в транспортный трубопровод 2 и перемещается в виде смеси с воздухом в осадитель (разгружатель) 3. В разгружателе, сечение которого значительно шире трубопровода, скорость воздуха резко падает и крупные частицы материала падают вниз. Более мелкие (пылевидные) частицы задерживаются фильтром 4. Далее через шлюзовый затвор 5, обеспечивающий герметичность трубопровода, материал попадает в хранилище (бункер). Воздух, очищенный в фильтре 4, поступает в вакуум-насос 6, а оттуда – в атмосферу.
|
|
Рисунок 28.2 – Схема нагнетательной системы
Установка нагнетательного типа работают за счет перепада давления воздуха в транспортной магистрали при подаче сжатого воздуха компрессором (рисунок 28.2). Сжатый воздух из компрессора 1, пройдя через масло- и влагоотделитель 2, поступает в смесительную камеру питателя 3, куда принудительно подается материал. В камере материал интенсивно перемешивается с воздухом и через транспортный трубопровод 4 поступает в отделитель (силос) 5, в котором происходит осаждение материала. Отработанный воздух, пройдя фильтр 6, выбрасывается в атмосферу.
В установках всасывающе-нагнетательного действия используются оба способа перемещения материала при помощи общего вакуум-насоса.
В установках всасывающего типа перепад давления воздуха обычно не превышает 0,05 МПа, поэтому транспортирование возможно на короткие расстояния. В установках нагнетательного типа перепад давления доходит до 0,6 МПа, а протяженность транспортирования – до 2 км.
|
|
При расчете пневмотранспортных установок используется понятие массовой концентрации смеси
![]() | (28.1) |
где Q – массовая производительность установки; Qв – массовый расход воздуха.
Так как масса 1 м3 воздуха составляет 1,224 кг, то
![]() | (28.2) |
где Vв – расход воздуха, м3/сек.
Используя эти данные и специальные графики по заданной производительностиQ (т/ч) определяют внутренний диаметр трубопровода, давление воздуха в магистрали, давление и производительность компрессора.
Аэроднища и аэрожелоба
Эти устройства чаще используют для облегчения разгрузки тонкодисперстных, склонных к слеживанию сухих пылевидных материалов, которые быстро насыщаются воздухом и благодаря этому становятся легкоподвижными (текучими) при небольшом уклоне.
Преимущества:
- простота конструкции и низкая стоимость;
- отсутствие быстоизнашивающихся деталей;
- большая производительность;
- низкая энергоемкость и металлоемкость.
Основной недостаток – необходимо использовать только сухойвоздух.
Аэроднища используют в бункерах (силосах) 1, содержащих сухой пылевидный материал 2 (рисунок 28.3, а). В качестве активных элементов применяют аэроплиты 3, которыми покрывают примерно 1/3 площади днища.
|
|
Рисунок 28.3 – Схема использования аэроднища
Сжатый воздух подается от компрессора, аэрирует слой транспортируемого материала и уменьшает трение между его частицами. Материал становится похожим на жидкость и течет под уклон.
Аэроплита (рисунок 28.3, б) состоит из герметичной рамки 4, закрытой пористой керамической плитой 5 с размерами пор до 40 мкм. Внутрь рамки по воздуховоду 6 подается сжатый воздух под давлением 0,1…0,15 МПа.
Аэрожелоба предназначены для транспортирования сухих пылевидных или порошкообразных материалов.
Пневматический желоб состоит из стального нижнего 1 и верхнего 2 корыта толщиной 1…2 мм, а также установленных на замазке пористых керамических перегородок 3 (рисунок 25.4, а). Вместо пористых перегородок часто применяют восьмислойный хлопчатобумажный ремень толщиной 20 мм. Верхнее корыто сообщается с окружающей атмосферой через рамки с байкой 4.
Рисунок 28.4 – Схема пневможелоба
Отфильтрованный воздух подается вентилятором 5 через гибкий рукав 6 в нижнюю полость желоба 1. Проходя через микроотверстия диаметром до 40 мкм в пористой перегородке 3, воздух насыщает (аэрирует) нижний слой материла, который приобретает хорошую текучесть. Под действием силы тяжести за счет наклона желоба (2…50) материал транспортируется вдоль желоба 7. Отработанный воздух выпускается через матерчатые фильтры 8.
Высоту слоя сыпучего груза принимают в пределах 50…60 мм, высоту нижнего корыта 50…100 мм. Ширина желоба 100, 150, 200, 250, 300 и 400 мм. Дальность транспортирования может доходить до 40 м. Удельный расход воздуха 78…90 м3/мин на 1 м2 площади желоба.
Дата добавления: 2018-04-04; просмотров: 2153; Мы поможем в написании вашей работы! |
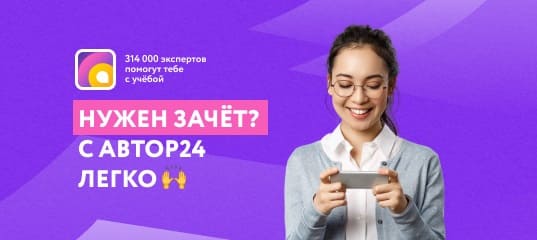
Мы поможем в написании ваших работ!