Четвертый принцип TQM. Определение. Методы «Дзидока», «Пока-ёка», методика «8D»
Процессный подход в управлении - подход, определяющий рассмотрение деятельности любой компании как сети бизнес-процессов, связанных с целями и миссией этой компании.
Процесс – совокупность взаимосвязанных видов деятельности, преобразующих входы в выходы.
Владелец – лицо, несущее полную ответственность за процесс и наделенный полномочиями в его отношении.
Уровни управления процессом: - стратегический
- тактический
- операционный
Цель процесса – создание ценности.
Методология процессного подхода.
1. Входы и результаты четко измеряются
2. Определение потребителей каждого процесса и идентификация их требований. Изучается их удовлетворенность
3. Устанавливается взаимодействие данного процесса с функциями предприятия.
4. Каждый процесс управляется и устанавливает полномочия, права и ответственность.
5. При проектировании процесса определяют его ресурсное обеспечение.
Успешное применение принципа дает преимущества:
1. Для формулировки политики и стратегии.
2. Для установления целей и показателей.
3. Для оперативного управления.
4. Для оправления людскими ресурсами.
МЕТОД «ДЗИДОКА»
Цель
Увеличение добавленной стоимости и устранение непроизводительных затрат посредством выявления и исправления нарушений, которые возни - кают в процессе производства.
|
|
Суть
Дзидока ( автономизация ) – привнесение человеческого интеллекта в автоматические устройства , способные самостоятельно обнаруживать дефект, после чего сразу останавливать производственную линию и сигнализировать о том, что нужна помощь. Дзидока является одним из основных принципов в разработке политики производственной системы предприятия.
План действий.
Процесс автономизации включает в себя следующие этапы:
1. Автономный контроль за ходом процесса производства и выявление нарушений.
2. Остановка производства, требующая вмешательства.
3. Немедленное определение причины нарушений и исправление положения.
4. Анализ возможных причин нарушений, их оценка и модернизация процесса, исключающая повторение тех же ошибок.
Результат:
Устранение непроизводительных затрат во внутренних процессах предприятия и повышение конкурентоспособности производства.
Достоинства:
Автономизация препятствует производству дефектных изделий, исключает перепроизводство, сосредоточивает внимание на понимании проблемы и обеспечивает недопущение повторения тех же ошибок.
Недостатки:
Дзидока (автономизация) требует высокого уровня владения навыками и опытом для решения технических, организационных и поведенческих проблем.
|
|
Дзидока (автономизация) один из двух основных принципов произ - водственной системы Тоуо ta.
Дзидока, или автономизация, может быть охарактеризована как «автоматизация со свойственным человеку интеллектом». Дзидока передает уровень человеческого интеллекта автоматизированному оборудованию и позволяет при возникновении нарушений в процессе производства немед - ленно останавливать работу и выявлять причины нарушений . Это, в свою очередь, ведет к совершенствованию процесса , обеспечивая встраивание качества в ходе осуществления операций в каждом процессе, что позволяет ликвидировать глубинные причины возникновения дефектов.
Слово «автономизация» («дзидока») следует понимать как организацию и контроль за нарушением процесса посредством установления на производственной линии устройств автоматического останова, использование автономных устройств было распространено также и на производственные линии, где применяется ручном труд. В общем автономизация представляет собой механизм, который позволяет автономно обнаруживать отклонения в производственном процессе.
|
|
МЕТОД «ПОКА-ЁКА»
В основе бездефектного производства лежит, как известно, метод защиты от ошибок, получивший название покэ-ёка.
Дефекты в производстве по большей части возникают из-за увеличения вариабельности характеристик процесса, разброс которых, в свою очередь, может быть следствием:
· некорректно разработанных стандартов или документированных процедур;
· использования некачественного или устаревшего оборудования;
· применения неподходящих материалов;
· изношенности инструментов;
· ошибок операторов.
Устранение первых четырех причин дефектов может быть осуществлено с помощью корректирующих и предупреждающих действий. Предотвратить же ошибки операторов достаточно трудно.
Известно, что совершать ошибки в процессе работы для людей – естественно, и это не является показателем непрофессионализма оператора. Цель покэ-ёка – найти способы защиты от непреднамеренных ошибок.
Метод покэ-ёка базируется на семи принципах:
1. для создания эффективных процессов используйте робастное проекти-рование;
2. работайте в командах: только так можно максимально полно использо-вать знания сотрудников;
3. устраняйте ошибки, также используя робастное проектирование: это позволит приблизить число ошибок к нулю;
|
|
4. устраняйте коренные причины появления дефектов, применяя метод
5. «5 Why» («Пять почему»);
6. действуйте сразу, используйте все возможные ресурсы;
7. устраняйте деятельность, не добавляющую ценность;
8. внедряйте улучшения и сразу задумывайтесь над дальнейшими улуч-шениями.
Применяя метод покэ-ёка, не полагаются на то, что операторы сами най-дут ошибку. Поэтому при выполнении работ используются сенсорные датчики другие устройства. Это помогает эффективно выявлять дефекты, пропущен-ные операторами.
Метод покэ-ёка следует применять как при входном контроле, так и в хо-де всего процесса. Эффект от его внедрения зависит от того, на каком именно этапе процесса – входном контроле или контроле в ходе процесса – этот метод был использован.
Последовательное применение метода покэ-ёка позволяет значительно сократить число ошибок, допускаемых операторами, что способствует снижению затрат и повышению удовлетворенности потребителей.
МЕТОДИКА 8 «D»
8D (EIGHT DISCIPLINE) - высокоэффективное средство для определения коренных причин несоответствий и внедрения корректирующих действий.
8D (EIGHT DISCIPLINE) – это ”методика восьми дисциплин”, созданная для разрешения проблем, связанных с недостаточным уровнем качества в производственном процессе, методологическим и аналитическим путем. Это высокоэффективное средство для определения коренных причин несоответствий, разработки и внедрения корректирующих действий.
В рамках 8D проводится доскональное изучение системы, в которой возникло несоответствие, и предотвращение возникновения подобного явления в будущем - повторяемости.
Основные преимущества данного метода работы над несоответствиями:
- Большая глубина изучения проблемы возникновения несоответствия;
- Вовлечение руководства предприятия в работу по устранению несоответствия;
- Корректирующие мероприятия становятся коллективной работой.
Каждый шаг 8D методики имеет в своем наименовании букву D, что означает discipline (дисциплина). Каждая из восьми дисциплин имеет свои входные и выходные информационные потоки. Типовой бланк 8D имеет восемь секций, каждая из которых определяет свою дисциплину.
ОСНОВНЫЕ ЭТАПЫ 8D
- D0 - Подготовка. Раздел посвященный подготовке к выполнению 8 D.
- D1 - Команда. Раздел посвященный созданию команды людей, которые будут выполнять 8 D.
- D2 - Описание проблемы. Самый обширный и трудоемкий раздел.
- D3 - Определение временных мероприятий
- D4 - Диагноз проблемы. Определение коренной причины.
- D5 - Выбор и верификация корректирующих действий для коренной причины
- D6 - Внедрение и валидация корректирующих действий.
- D7 - Выбор предупреждающих действий.
- D8 - Закрытие 8D.
Дисциплина - D0. Подготовка
Основная задача на этом шаге - определить величину проблемы (несоответствия) и необходимость введения действий, направленных на предотвращение поступления некачественной продукции заказчику. Заказчик должен быть всегда защищен.
Дисциплина – D1. Команда
Команда (многофункциональная) людей для выполнения 8D должна состоять из представителей разных отделов, как правило, это:
Дата добавления: 2018-04-04; просмотров: 1320; Мы поможем в написании вашей работы! |
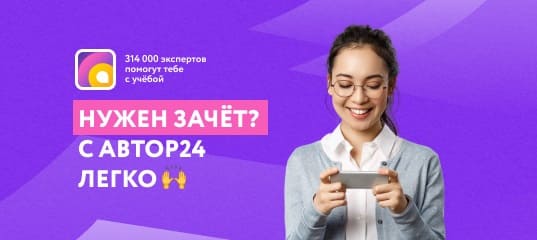
Мы поможем в написании ваших работ!