ПРОЕКТИРОВАНИЕ ОТДЕЛЕНИЙ И УЧАСТКОВ
ПРИЕМА, ХРАНЕНИЯ И ПОДГОТОВКИ СЫРЬЯ
Основное и дополнительное сырье для производства хлеба, хлебобулочных, бараночных, сухарных и других изделий хранится в отведенных для этого складских помещениях в таре (в мешках, ящиках, бочках) и бестарно (в силосах, бункерах, цистернах, танках).
Механизация процессов подготовки муки и дополнительного сырья имеет большое значение для повышения качества продукции и эффективности производства, а также экономии сырья.
Отделение приема, хранения и подготовки муки
При проектировании хлебозавода или пекарни, как правило, предусматривается склад бестарного хранения муки с помещением для тарного ее хранения в количестве суточной потребности.
В составе этого отделения проектируются приемные устройства для автомуковозов и рампа для разгрузки мешков с мукой; силосы или бункера для бестарного хранения, кладовые для хранения мешков с мукой; участки для просеивания, взвешивания и подачи муки в производственные емкости.
Технологическая схема приема, хранения
И подготовки муки
Склад бестарного хранения муки (БХМ).Нормами технологического проектирования предприятий хлебопекарной промышленности рекомендуется хранить муку в силосах или бункерах.
Бестарная доставка муки на хлебозаводы осуществляется автомуковозами, которые при въезде на территорию предприятия должны быть взвешены на автомобильных весах. Грузоподъемность весов и длину их платформы подбирают при проектировании в зависимости от типа и грузоподъемности автомуковоза. Наиболее распространенный автомуковоз К4-АМГ грузоподъемностью (9000±200) кг взвешивают на автомобильных весах грузоподъемностью 30 т при длине платформы 12 м. Используются также автомуковозы К-1040-Э и полуприцепы-цистерны ТЦ-25,5; ТЦ-20 и ТЦ-21,2 грузоподъемностью 8,5; 11 и 16 т соответственно.
|
|
Наиболее удачным следует признать размещение и совмещение автомобильных весов с проходной предприятия на въезде-выезде.
После взвешивания автомуковоз подается к складу бестарного хранения, где разгрузочный патрубок или рукав, например марки М-127, присоединяют к одному из индивидуальных загрузочных мукопроводов посредством гибкого шланга (рис. 2.1). По этим индивидуальным для каждого из установленных силосов или бункеров мукопроводам аэрозольтранспортом подается мука.
Емкости для хранения муки пронумеровывают и закрепляют за определенными сортами.
В бестарных складах хранение муки осуществляют в силосах и бункерах, что имеет и технологические преимущества: муку легко перемещать из одного силоса в другой, аэрировать, подсортировывать, просушивать, быстро прогревать, используя теплые потоки воздуха.
|
|
Надо учитывать, что минимальное число бункеров для одного сорта муки должно быть не менее двух.
Это требование связано с принятой организацией работы складов БХМ и учетом ее, так как расход муки на производство необходимо осуществлять из одного бункера, а прием из автомуковоза – в полностью освободившийся другой бункер.
Для 6-7-суточного хранения муки используется следующее оборудование (табл. 2.1).
Таблица 2.1 - Оборудование для БХМ
Марка оборудования | Рабочий объем, м3 |
Силосы: | |
ХЕ-160А | 50,7 |
А2-Х2-Е-160А | 51,0 |
А2-Х3-Е-160А | 48,0 |
А2-Х3-Е-160Б | 34,0 |
Бункера: | |
БР | 9,0 |
М-111 | 28,1 |
М-118 | 57,8 |
Установки: | |
М-135 (включает 3 бункера) | 78,4 (единицы оборудования) |
М-137 (включает 12 бункеров) | 45,0-64,0 (единицы оборудования) |
LM (включает 1-8 силосов) | 45,0 (единицы оборудования) |
Рисунок 2.1 - Склад бестарного хранения муки открытого типа с легкими ограждающими конструкциями: 1 – присоединительное устройство; 2 – компрессор; 3 – ресивер; 4 – питательный шнек (винтовой конвейер); 5 – роторный питатель; 6 – просеиватель муки; 7 – бункер-накопитель просеивателя; 8 – винтовые разгрузители; 9 – цепной конвейер; 10 – бункера для бестарного хранения муки; 11 – вентилятор; 12 – фильтр-циклон
|
|
Выбор при проектировании типа и марки емкости для приема и хранения муки зависит от многих факторов, в том числе:
– от общей вместимости склада и распределения муки по сортам;
– от габаритных размеров помещения склада;
– от типа склада (открытый или закрытый);
– от эксплуатационных свойств бункеров и силосов, в том числе эффективности разгрузки муки из емкостей, очистки от мучных вредителей, аспирации и т. д.;
– от необходимости и возможности перспективного увеличения вместимости силосов или бункеров;
– от возможности применения механического или пневматического транспорта муки;
– от учета муки в силосах и бункерах;
– от технологичности сборки и монтажа.
Размещение силосов и бункеров в помещении склада или на открытой площадке должно соответствовать требованиям нормальной и безопасной их эксплуатации:
– проходы между рядами силосов или бункеров следует принимать не менее 0,7 м;
– расстояние между силосами (бункерами) и стеной – не менее 0,7 м на высоту прохода 2,0 м, а выше – не менее 0,5 м;
– расстояние между двумя смежными в ряду бункерами или силосами круглого сечения – не менее 0,25 м;
|
|
– высота помещения над силосами (бункерами) должна быть не менее 1 м при расположении обслуживающей площадки ниже крышек силосов (бункеров), при этом расстояние от площадки до конструкций – не менее 2 м и при расположении площадки на одном уровне с крышками силосов (бункеров) – также не менее 2 м.
Источником воздуха для аэрозольтранспорта является либо компрессор, установленный на автомуковозе, либо стационарный источник сжатого воздуха на хлебозаводе; однако в ряде проектов хлебозаводов и цехов малой мощности с небольшими трассами подачи муки применяют роторные компрессоры (газодувки).
Актуальным для проектировщика является выбор системы аспирации бункеров. Очистка транспортирующего муку воздуха длительное время проектировалась путем установки на крышках бункеров (силосов) встряхивающихся фильтров ХЕ-161 и ХЕ-162, а также самодельных фильтров в виде рукава из фильтровальной ткани. Однако ни один из этих фильтров не обеспечивает удовлетворительной очистки воздуха в силу ряда конструктивных и эксплуатационных недостатков.
Наиболее радикальным решением аспирации бункеров (силосов) является использование современных фильтров-циклонов типа РЦИЭ. Подбор их осуществляется по объему очищаемого воздуха. Возможно проектирование центральной системы аспирации, когда в помещении склада БХМ для одного из сортов муки устанавливается фильтр-циклон, к которому присоединяют воздуховоды от ряда бункеров этого сорта муки. При такой компоновке оборудования следует предусматривать возврат муки из циклона в один из бункеров.
Удачным вариантом представляется установка индивидуальных фильтров-циклонов непосредственно на крышке бункера (силоса). Такое решение позволяет собранную в циклоне муку через шлюзовой затвор возвращать в бункер, исключая систему пневмотранспорта.
Во всех упомянутых вариантах компрессор и ресивер для продувки могут быть установлены в любом удобном месте склада БХМ.
Загрузку муки в бункера из автомуковозов следует проектировать индивидуальными мукопроводами диаметром 1 м, соответствующим диаметру гибкого рукава соединительного устройства для присоединения автомуковоза. При такой схеме разводки несколько увеличивается расход труб, однако это компенсируется отсутствием переключателей. Кроме того, практически исключается возможность ошибки при подаче муки в бункера из-за отказа переключателя или ошибки оператора.
При проектировании трассы загрузочного мукопровода от автомуковоза до бункера следует стремиться к минимальному количеству отводов, так как каждый поворот на трассе мукопровода – это дополнительное сопротивление.
Мука из бункеров аэрозольтранспортом через роторные питатели марок РП, Д3-ХПШ, М-122, шлюзовые затворы (Р3-БШМ), виброразгрузочное устройство (Ш2-ХМГ-200) или механическим транспортом (возможна комбинация механического и аэрозольтранспорта) подается на просеивательные линии, состоящие из бункера-разгрузителя с фильтром, просеивательной машины марки Ш2-ХМ2-В, Ш2-ХМЕ или Бурат, автоматических порционных весов АД-50НК, подвесового бункера, из которого подготовленная к производству мука аэрозольтранспортом или посредством шнекового питателя, например, ПШМ-1, направляется в производственные бункера тестомесильного отделения, отделение приготовления жидких дрожжей или заквасок и другим потребителям муки.
Схема разводки муки по потребителям выполняется таким образом, чтобы с любой просеивательной линии мука могла быть подана практически во все приемники – производственные бункера. Такая схема позволяет обеспечить непрерывный цикл производства в случае планового ремонта или непредвиденных остановок оборудования. Следовательно, аэрозольтранспорт муки, несомненно, предпочтительнее механического.
Склад БХМ следует проектировать открытого или частично открытого типа (рис. 2.1) с закрытой подсилосной обслуживаемой зоной в условиях со средней температурой наиболее холодного периода до минус 30 оС; склады закрытого типа – со средней температурой ниже минус 30 оС.
При проектировании складов БХМ необходимо размещать их как можно ближе к местам потребления муки и учитывать также, что эти склады по взрыво- и пожароопасности относятся к категории Б.
Аналогичные аспекты следует учитывать и при размещении в здании хлебозавода или цеха источников сжатого воздуха для систем аэрозольтранспорта муки. Максимально возможное приближение компрессорных станций сжатого воздуха к складам БХМ позволит уменьшить его потери. Этот фактор важен при имеющейся тенденции демонтажа с автомуковозов компрессоров сжатого воздуха и использования для этого стационарных источников воздуха хлебопекарных предприятий.
При проектировании складов БХМ следует обратить внимание на создание безопасных и удобных для обслуживающего персонала условий труда. Достаточное внимание должно быть уделено площадкам обслуживания люков и лазов, переключателей, питателей, фланцев и муфт на мукопроводах, запорной арматуре, приборам контроля и управления. Следует учитывать необходимость периодической санитарной очистки оборудования.
При проектировании складов БХМ используется техническая документация, в которой отражены многие из этих проблем:
– инструкция по обеспечению взрыво- и пожаробезопасности в установках бестарной приемки, хранения и внутризаводского транспортирования муки на предприятиях хлебопекарной промышленности;
– инструкция по эксплуатации складов БХМ на предприятиях хлебопекарной промышленности;
– инструкция по санитарной очистке бункеров склада БХМ на хлебозаводах;
– нормы технологического проектирования предприятий хлебопекарной промышленности.
Проектировщик должен учитывать позитивные и негативные стороны открытых складов БХМ:
– при отсутствии здания склада экономятся денежные средства;
– снижается взрыво- и пожароопасность и исключаются соответствующие мероприятия в проекте;
– ухудшаются условия труда для обслуживающего персонала, в том числе ремонтников, особенно в зимнее время;
– зимой при низких температурах требуется добавление антифриза в смазочные масла (для редукторов, подшипников);
– более тщательно должна осуществляться осушка сжатого воздуха системы аэрозольтранспорта муки.
Для предотвращения попадания осадков и их быстрого удаления с поверхности силосов (бункеров) крышки должны быть выполнены с уклоном, люки и фланцы тщательно загерметизированы, фильтры закрыты защитными кожухами с жалюзийными решетками.
Оптимальным вариантом являются склады частично закрытого типа. В этом случае нижняя часть бункеров с лазовыми люками, роторными питателями или цепными транспортерами, кранами или переключателями находится в помещении с дежурным отоплением, а верхняя часть, например, цилиндрическая при круглом сечении бункеров, – в открытом пространстве. Такое компоновочное решение требует тщательной герметизации участка примыкания кровли к поверхности силосов (бункеров).
Возможен вариант размещения склада БХМ на открытой площадке с ограждениями из легких конструкций. В этом случае внутреннее пространство его не отапливается, только защищено от атмосферных осадков.
В соответствии с требованиями ВНТП 02-92 расстояние от производственных помещений до отдельно стоящего склада бестарного хранения муки открытого типа должно быть не менее 12 м. Можно размещать открытый склад и у стены хлебозавода, цеха или другого сооружения, но при этом надо учитывать взрыво- и пожароопасность установки БХМ.
Важное место для складов БХМ занимают выбор и проектирование источников сжатого воздуха для систем аэрозольтранспорта муки. Это может быть компрессорная станция со стационарными компрессорами, фильтрами, влагомаслоотделителями, ресиверами, системой оборотной воды для охлаждения или компрессоры шестеренчатые типа 2АФ (ЗАФ) с фильтрами и глушителями.
Решение о выборе источника сжатого воздуха принимается на основе аэродинамического расчета материалопровода (мукопровода). Воздуходувную машину подбирают по расходу воздуха и давлению, развиваемому машиной. Эти параметры определяются аэродинамическим расчетом, исходными данными для которого являются производительность, длина и конфигурация линии, концентрация аэросмеси. Следует также принимать во внимание, что к компрессорной станции и к ее помещению, предъявляются повышенные требования, изложенные в «Правилах устройства и безопасной эксплуатации стационарных компрессорных установок, воздуховодов и газопроводов».
Следует учитывать относительно высокое энергопотребление стационарных компрессоров, необходимость обслуживания квалифицированным персоналом, создание оборотной системы охлаждающей воды, экологические факторы.
На хлебопекарных предприятиях, где относительно небольшие трассы продуктопроводов (мукопроводов), возможно применение шестеренчатых компрессоров (газодувки, воздуходувки).
Проектировщик должен предусмотреть фильтрацию забираемого воздуха, установку глушителя (при размещении вне звукоизолированного помещения), обратного клапана на нагнетающей линии непосредственно после компрессора. Воздух желательно забирать с улицы через фильтры, в качестве которых можно использовать батареи автомобильных масляных фильтров. Для предотвращения попадания аэрозольной смеси муки в нагнетательную камеру компрессора при отключении электродвигателя необходим обратный клапан.
При проектировании следует также предусмотреть «мягкое» присоединение всасывающей и нагнетательной линий компрессора с помощью гибкого резинотканевого рукава, так как металлические трубопроводы и арматура, «висящие» на компрессоре, могут вызвать его разбалансировку и ухудшение условий работы. Шестеренчатые компрессоры создают повышенный шум и вибрацию, что препятствует их установке непосредственно на производстве.
Тарные склады муки.Тарные склады проектируются и при бестарном хранении муки. Тарные склады следует размещать как можно ближе к местам потребления муки. Для разгрузки муки в мешках необходимо предусмотреть в проекте площадку (рампу) с навесом. Расстояние от нее до места складирования и от склада до места растаривания должно быть минимальным.
Тарные склады должны иметь оборудование, исключающее применение тяжелого физического труда.
Различают два вида складских помещений: производственный склад и склад для сменного запаса.
Производственный склад должен вмещать 7-суточный запас муки.
Склад для сменного запаса предназначен для муки и дополнительного сырья, выдаваемого производству на смену; расположен в отдельном изолированном помещении, имеющем сообщение с производственным складом и производством. Склад сменного запаса должен быть отделен от склада перегородкой, которая может быть выполнена из легкой металлической сетки высотой не менее 2,0 м.
В плане склада намечают укладку поддонов со штабелями муки по сортам, расстановку оборудования, рабочие места, проезды, проходы. На предприятиях средней и большой мощности следует транспортировать мешки с мукой на поддоне с помощью вилочных электропогрузчиков. На предприятиях малой мощности необходимо проектировать перемещение мешков с мукой средствами малой механизации с укладкой штабелей по высоте в восемь рядов. При механизированной укладке допускается укладка мешков на поддоне в четыре ряда, установка поддонов в три яруса по высоте.
Проезды должны равняться диагонали погрузчика со штабелем плюс 0,4 м; в местах, где требуется разворот и заезд для укладки – 4 м. Проходы между группами штабелей должны иметь ширину 0,75 м, от штабелей до стены – 0,5 м; расстояние между проходами не более 12 м.
Высота склада от пола до нижней поверхности перекрытия принимается 3,6 м, а при установке в высоту двух поддонов – 4,8 м.
Размеры штабелей для муки в плане – 1,25´1 м. Мешки укладываются в 6-8 рядов по высоте по три мешка в ряду (в перевязку); размеры мешков: длина – 0,77-0,80 м, ширина – 0,47-0,53 м, толщина –0,27-0,28 м. Средняя масса мешка – 50 кг. Высота штабеля – 1,88 м. Для удобства расстановки и снятия между штабелями оставляют зазор – 0,1 м.
Загрузочные двери при использовании электропогрузчиков должны быть шириной 2 м, высотой – 2,4 м (в чистоте). Проемы оборудуются тепловыми завесами, в холодных районах устраиваются тамбуры.
У мест поступления муки делаются платформы с навесом, увязанные с габаритами транспорта. Платформы для железнодорожного транспорта устраивают на одном уровне с полом вагона и мучного склада: на высоте 1,1 м над уровнем головки рельсов; при доставке муки автотранспортом и наличии автопогрузчиков это требование необязательно.
В помещении производственного запаса муки целесообразно устанавливать приемник муки из мешков типа ХМП-М. В конструкцию этого приемника входит опрокидывающее устройство, а также система пневматической очистки мешков от пыли. От этого приемника мука может направляться на просеивательную линию или в бункер для бестарного хранения.
Для механизации приема муки в таре можно применять мешко-опрокидыватели типа БЭТА или устройства для подъема мешков с бункером для ссыпания муки, входящие в комплект установки типа УХМ-Ф-9 оборудования пекарен малой мощности А2-ХПО. Для очистки мешков от мучной пыли и тестовой корки в отдельном помещении должен устанавливаться комплекс Г4-БОК-200.
Просеивательное отделение.Мука, поступающая со склада, должна быть просеяна, очищена от ферропримесей и взвешена. Число просеивательных линий зависит от расхода муки, количества её сортов, производительности и режима работы отделения. На предприятиях средней и большой мощности следует предусмотреть одну резервную просеивательную линию.
В качестве мукопроводов применяют стальные холоднокатаные трубы (56´2; 80´2 мм).
Аэрозольная смесь, попадая в фильтр-разгрузитель или приемное устройство для муки с фильтром, разделяется. Воздух уходит через фильтрующее или аспирационное устройство, а мука накапливается в бункере приемного устройства над просеивателем. В качестве такого приемного устройства может быть применен фильтр-разгрузитель марки М-104.
Для предотвращения попадания воздуха в просеиватель (что возможно при недостаточной пропускной способности фильтра-разгрузителя), атакже с целью упорядочения подачи муки на просеивание между разгрузителями и просеивателем следует устанавливать шлюзовой затвор либо питательный шнек, который будет играть роль дозирующего и запорного устройства. Можно применять просеиватели муки марок Ш2-XMB, Ш2-ХМЕ, Бурат (ПБ-1,5; ПБ-2,85), РЗ-ХМП, А2-ХПГ.
При использовании муки в мешках можно установить просеиватели П2-П, Пиорат-2М, ПМ-900 и мешкоопрокидыватели БЭТА.
В комплект оборудования пекарни малой мощности типа А2-ХПО входит просеиватель центробежный горизонтальный, имеющий в корпусе на проходе муки магнитную защиту. В этом случае просеиватель установлен под автоматическим взвешивающим устройством, одновременно являющимся циклоном-разгрузителем. Проектом должны быть обеспечены свободный и удобный доступ к ситам и магнитам, сбор и удаление схода.
Весовое отделение.Проектирование просеивательного и весового отделений осуществляется по схеме взвешивания после просеивания, так как конструктивные особенности применяемых весовых устройств позволяют обеспечить стабильность их работы только на просеянной муке. В качестве весового устройства в последнее время применяется автоматический дозатор АД-50НК для муки.
Для обеспечения заданной производительности (3,5-15 т/ч) между просеивателем и весами проектируется промежуточный (надвесовой) бункер, в котором должен находиться запас муки не менее установленной максимальной дозы (70 кг). С этой же целью под весами проектируется накопительная емкость для отмеренной дозы муки, так называемый «подвесовой бункер» вместимостью, достаточной для обеспечения непрерывной работы, как весового устройства, так и системы, подающей муку на производство.
В конструкции весового дозатора имеется счетчик отвесов, по которому ведется учет отпускаемой муки. Показания счетчика дублируются на пульте управления оператора склада БХМ. Так как эти весовые устройства порционного принципа действия и отмеренная, достаточно большая (до 70 кг) доза муки сбрасывается единовременно в подвесовую емкость, следует уделить повышенное внимание герметизации оборудования весового отделения и аспирации. Размещение аспирационного оборудования следует проектировать в соседнем помещении.
При компоновке оборудования, подающего муку на производство (роторные или шнековые питатели), непосредственно после подвесового бункера проектируется установка питательного шнека. Это необходимо для предотвращения возможного прорыва воздуха из питателя в подвесовой бункер и весы, что может быть дополнительным источником пыли в этом взрыво- и пожароопасном помещении. Над выходным патрубком шнека устанавливается рукавный матерчатый фильтр на проволочном каркасе.
Таким образом мука подается в производственные силосы марки ХЕ-63В, рассчитанные на 6-7-часовой сменный запас.
Расчет технологического оборудования для хранения, подготовки и подачи муки на производство. Необходимый запас муки рассчитывается на основании данных о суточной производительности предприятия по каждому виду изделий и суточной потребности в каждом сорте муки.
Суточная потребность муки для отдельного вида изделий, кг:
(2.1)
где Рс– суточная производительность предприятия по отдельному виду изделий, кг; Вх – выход хлебных изделий, %.
Запас муки, кг:
(2.2)
где п – срок хранения муки, сут (по действующим нормам проектирования 6-7 сут).
Если изделие готовится из смеси разных сортов муки, потребность в каждом сорте рассчитывают, исходя из его содержания в смеси, кг:
(2.3)
где Рм –содержание муки данного сорта в смеси, %.
Вместимость силосов для хранения каждого сорта муки, м3:
(2.4)
где р – объемная масса муки, т/м3 (р = 0,55).
Общий объем силосов для хранения муки, м3:
(2.5)
где Мз – запас муки, кг; р – объемная масса муки, т/м3 (р = 0,55).
Общее число силосов для хранения муки:
(2.6)
где Vc – вместимость силоса, т.
После расчета по формуле (2.6) дробные числа округляют до целых максимальных величин.
Склады тарного хранения муки рассчитывают так же, как и бестарные.
Для транспортирования на производство, взвешивания, просеивания, очищения от металлических примесей и хранения на предприятии проектируют мучные линии, производительность которых определяется производительностью просеивателя, т/ч:
Qпр = F f, (2.7)
где F – рабочая поверхность сита, м2; f – производительность 1 м2 сита, т/ч (при просеивании ржаной муки f = 1,5-2, пшеничной – 2-3 т/ч).
Производительность просеивателя с пирамидальным барабаном (частота вращения 60 об/мин, поверхность сита 1,5 м2) при расходе ржаной муки составляет 3 т/ч, пшеничной – 3,75 т/ч.
Количество мучных линий:
(2.8)
где Мч – потребность в муке, т/ч; Qч – производительность мучной линии, т/ч (проверяют по просеивателю).
Количество производственных силосов принимается из расчета подачи муки из двух силосов на тестоприготовительную линию. Отдельно предусматриваются силосы для дрожжевого, кондитерского и других цехов.
Количество муки в силосах определяется в зависимости от производительности линии. Минимальный запас муки рассчитывается на 2-часовой ее расход, а желательно, чтобы запас муки составлял ее сменный расход.
Для контроля количества муки в силосах (например, при сдаче остатков одной сменой другой) необходимо внедрять тензометрические способы учета муки.
Массу муки в силосе ориентировочно можно определить подсчетом, кг:
Mсил = V r, (2.9)
где V – объем, занимаемый мукой, м3; r – насыпная плотность муки, кг/м3.
Объем муки в силосе равен 1,8 м3; масса муки 1000 кг; объем муки в силосе составляет 2,9 м3, а масса муки – 1500 кг.
Необходимый для производства запас муки в силосах для отдельного сорта муки, кг:
åG = åМч Т, (2.10)
где åМч – суммарный расход муки отдельного сорта, кг/ч; Т – срок запаса муки (проверяется по графику), ч.
Расчет загрузки силосов. Продолжительность заполнения одного силоса мукой, с:
(2.11)
где G – вместимость силоса, кг; Q – производительность мучной линии, кг/ч.
Продолжительность расхода муки из одного силоса, с:
(2.12)
Размеры склада зависят от количества муки, находящейся на хранении, и средней нагрузки на 1 м2.
Площадь склада при укладке муки в мешках, м2:
(2.13)
где åМ – количество муки в складе, кг; qср – средняя нагрузка на 1 м2, кг.
При приеме и хранении муки в штабелях площадь рассчитывается, м2:
(2.14)
где g– масса мешка, кг (g = 50); K – количество мешков в штабеле (в тройнике 18-24 шт.); f – площадь штабеля, м2 (тройника 1,25´1,0); m – коэффициент, учитывающий проезды, проходы (для муки 1,85, для прочего сырья 1,5).
Площадь склада при бестарном хранении муки рассчитывается по формуле (2.15), м2:
(2.15)
где Мз – запас муки на срок хранения, т; Vс – средний объем склада на 1 т (Vс = 7), м3; h – высота склада, м.
Дата добавления: 2018-02-28; просмотров: 3782; Мы поможем в написании вашей работы! |
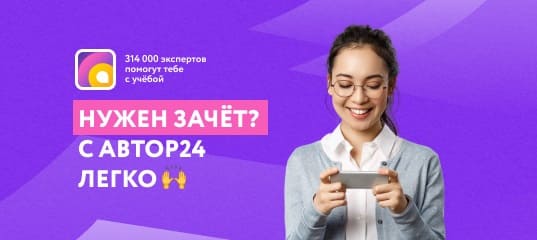
Мы поможем в написании ваших работ!