Технологическая схема производства, ее обоснование и описание
В пищевой отрасли производство глазированных сырков осуществляется в строгом соответствии с действующими нормативными документами.
Технологическая схема производства - это сочетание отдельных технологических операций, при последовательном выполнении которых сырье превращается в готовую продукцию.
Технологический процесс производства сырков глазированных включает в себя следующие этапы (рис.1).
Приемка, начальная и предварительная обработка сырья. Цель операции - приемка и начальная обработка сырья. При приемке производят оценку качества молока и его взвешивание. Начальная обработка молока - очистка, охлаждение до температуры (4±2) ºС, промежуточное хранение, продолжительность которого не должна превышать 6 часов. При производственной необходимости более длительного срока хранения молока его после приемке подвергают термической обработке - нагрев до температуры (70±2) ºС с выдержкой (8±2) с или (87±2) ºС с выдержкой (18±2) с, после чего охлаждают и направляют на промежуточное хранение до 18ч. [20, 184].
Предварительная обработка - подогревание, сепарирование, тепловая обработка молока и смесей, охлаждение и нормализация.
Блок схема производства.
Рис.1. Технологическая схема производства глазированных сырков
При запуске процесса производства продуктов детского питания молоко из резервуара хранения подогревается в секции регенерации пастеризационно-охладительной установки до температуры (45±2) ºС, после чего поступает в сепаратор-сливкоотделитель, откуда обезжиренное молоко возвращается в установку, а сливки направляются в пастеризатор, где подвергаются тепловой обработке при температуре (88±3) ºС, охлаждаются до (4±2) ºС и используются для нормализации смеси или в дальнейшем производстве. Обезжиренное молоко после пастеризации при температуре (70±2) ºС с выдержкой (8±2) с или (87±2) ºС с выдержкой (18±2) с, охлаждают до (4±2) с и направляют в резервуар для нормализации молока. Для нормализации подают обезжиренное молоко и сливки. Для нормализации подается цельное молоко из резервуара промежуточного хранения, обезжиренное молоко и сливки. В отдельных случаях для нормализации используется восстановленное молоко.
|
|
Перед использованием масло выдерживают при комнатной температуре не более двух суток.
Орехи перебирают на столах с заграждениями, удаляя механические примеси, не допускается использование ядер орехов, пораженных плесенью. Ядра орехов освобождают от скорлупы, затем дробят на ореходробилке и обжаривают в жарочном шкафу при температуре 130-140°С в течение 20 - 40 минут.
Сухие фрукты без косточек (изюм, курага, чернослив и т.п.) перебирают, освобождают от плодоножек. Затем их тщательно промывают в перфорированной тележке проточной водой с температурой (20±2)°С, дают возможность стечь воде. Курагу, чернослив обсушивают воздухом и дробят на электромясорубке. Изюм пропаривают в течение 20 минут в тележке, накрытой крышкой.
|
|
Мармелад перед использованием дробят на электромясорубке.
Красители используют в виде водного раствора. Раствор приготавливают в специально промаркированной ёмкости, используя питьевую воду с температурой (60 ± 5)°С.
Ванилин перед употреблением смешать вручную в специально промаркированной ёмкости с сахарным песком для лучшего распределения в смеси. Ароматизаторы, красители и ванилин хранятся в отдельном помещении.
Глазурь шоколадную вручную переливают в ванну, которая имеет подвод холодной воды и пара. Температура воды в межстенном пространстве указана на температурном датчике и должна быть не более (58 ± 2)°С.
Жир закладывают в маслоплавитель, расплавляют, сливают во фляги и транспортируют в сырковый цех, где помещают фляги в печь.
Сепарирование и пастеризация молока. Цель операции - уничтожение вегетативных форм микроорганизмов; инактивация ферментов; обеспечение условий для формирования необходимой консистенции готового продукта.
|
|
Часть молока нагревают до температуры (37 ± 3)°С и подают на сепаратор-сливкоотделитель.
В процессе тепловой обработки меняются основные компоненты молока (белки, соли, ферменты, витамины). Казеин обладает высокой термоустойчивостью, он термостабилен, при пастеризации молока не происходит его коагуляции, а сывороточные белки термолабильны и начинают свертываться в молоке при температуре 69ºС. В процессе тепловой обработки молока изменяется в первую очередь состав солей кальция. В плазме молока нарушается соотношение форм фосфатов Са; фосфорнокислые соли кальция, находящиеся в виде истинного раствора, переходят в коллоидный фосфат кальция, который агрегирует и осаждается на мицеллах казеина. При этом происходит необратимая минерализация казеинат кальций фосфатного комплекса, что приводит к нарушению структуры мицелл и снижению термоустойчивостью молока.
В процессе высокотемпературной пастеризации молока происходит изомеризация лактозы (образование лактулозы) и ее взаимодействие с аминокислотами (реакция меланоидинообразования). В результате образования меланоидинов изменяется вкус и цвет молока.
|
|
Молочный жир под воздействием высоких температур подвергается незначительному гидролизу. При этом увеличивается количество в молоке диглециридов и снижается на 2-3% содержание в триглицеридах ненасыщенных жирных кислот. Более существенно изменяется состав оболочек жировых шариков: денатурируется их белковый компонент, и часть веществ оболочки переходит в плазму молока. В результате снижается механическая прочность оболочек и наступает частичная дестабилизация жировой эмульсии - происходит слияние некоторых жировых шариков и вытапливание жира.
Тепловая обработка молока приводит к разрушению части витаминов и потере активности почти всех ферментов. В большей степени разрушаются водорастворимые витамины (тиамин, В12, С1), количество жирорастворимых витаминов изменяется мало.
При всех видах тепловой обработки стремятся максимально сохранить исходные данные молока, его пищевую и биологическую ценность, так как длительное воздействие высоких температур может вызвать необратимое изменение структуры и свойств белка и прочих составных частей молока. Пастеризацию молока проводят при температуре 85-87 ºС с выдержкой в течение 5-10 минут или при 90-2 ºС с выдержкой 2-3 минуты.
Заквашивание и сквашивание молока. Цель операции - заквашивание молока. При производстве сырков применяют сухой закваской мезофильных молочнокислых стрептококков.
После внесения закваски в смесь добавляют хлористый кальций из расчёта 400 г безводного хлористого кальция на 1 т заквашиваемой смеси.
Хлористый кальций вносят в виде водного раствора с массовой долей хлористого кальция от 30 до 40 %. Приготавливают раствор хлористого кальция в специально промаркированной ёмкости, для чего используют воду с температурой (85 ± 5)°С из расчёта 1,5 дм на 1 кг хлористого кальция. Раствор отстаивается и становится бесцветным и прозрачным. Готовый к применению раствор хранится в специально промаркированной закрытой таре.
После внесения раствора хлористого кальция в смесь вводят 1 % раствор молокосвёртывающего препарата, который готовится за (25 ± 5) мин до использования.
Сычужный порошок (ферментные препараты) растворяют в пастеризованной и охлаждённой до (34 ± 2)°С питьевой воде из расчёта 2,5 г препарата на (150 ± 50) см воды, используя специально промаркированные ёмкости.
Закваску, растворы хлористого кальция и фермента вносят при непрерывном перемешивании молока.
После заквашивания молоко тщательно перемешивают в течение 10-15 минут и оставляют в покое до образования сгустка кислотностью (65±3)°Т. Продолжительность сквашивания составляет (9 ± 3) ч. После окончания сквашивания продукт охлаждают.
Обработка сгустка. Цель операции - разрезка сгустка, отделение сыворотки и разлив сгустка. Готовый сгусток размешивают и оставляют в покое для выделения сыворотки на (45 ±15) мин. Выделившуюся сыворотку выпускают из в промежуточный бачок, откуда насосом подают на пластинчатый охладитель где сыворотка охлаждается до температуры (4 ± 2)°С и подаётся в ёмкости для накопления и хранения. Сгусток разливают вручную в бязевые или лавсановые мешки, заполняя их не менее, чем на 3/4.
Самопрессование сгустка, прессование и охлаждение творога. Мешки со сгустком завязывают и укладывают в охладитель, в котором происходит самопрессование и охлаждение сгустка в течение от 1 до 4 часов в зависимости от качества полученного сгустка и от хладоносителя (ледяная вода). После самопрессования мешки с творогом помещают в тележки для творога, перевозят их в прессовую творожного участка, где температура воздуха не более 6°С. Мешки с творогом помещают в пневматические пресса, кладут на них деревянные прижимные круги и опускают прижимные тарелки пресса. Прессование продолжается не более 10 часов до достижения творога массовой доли влаги, требуемой рецептурой. Для ускорения отделения сыворотки мешки с творогом периодически встряхивают. Отпрессованный творог высыпают из мешков в тележки для творога, накрывают их крышками и помещают в холодильную камеру, где он охлаждается до температуры (12 ± 3)°С.
Приготовление сырковой массы. Цель операции - создание соответствующего наполнения продукта, внесение компонентов. Сырьё, предусмотренное рецептурой взвешивают и вносят в фаршмешалку в следующей последовательности: сахар, предварительно смешанный с ванилином, или какао, или кофе растворимым. Затем вручную закладывают масло перемешивают в течение 10-15 мин. При достижении однородной консистенции мешалку отключают. Получению массу температурой (12±3)°С перемешивают в течение 3-5 мин., после чего вносят вкусовые и ароматические наполнители (курагу, цукаты, чернослив и ароматизаторы), предусмотренные рецептурами и все это вновь перемешивают. Общая продолжительность перемешивания должна составлять от 5 до 10 мин. Порядок внесения компонентов может быть изменён.
Полученную сырковую массу высыпают в специально промаркированные тележки, закрывают их крышкой и перевозят в холодильную камеру и охлаждают до температуры (7 ± 2)°С.
Приготовление глазури. Глазурь приготавливают согласно СТБ 1207-2000, технологической инструкции, рецептур, утверждённых в установленном порядке. Для улучшения глазировочных свойств глазури в неё добавляют кондитерский жир в количестве до 20 % к массе глазури в зависимости от её состава, не нарушая при этом установленных качественных показателей готовой глазури. Глазурь заливают вручную в бункер глазировочной машины, где автоматически поддерживается температура глазури (40 ± 3)°С.
Формование и глазирование сырков. Цель операции - придание продукту окончательного товарного вида. Охлажденную сырковую массу с температурой (7 ± 2)°С подают вручную совком в дозировочно-формовочный автомат линии производства глазированных сырков откуда они выходят в виде нескольких сформованных потоков, которые автоматически разрезаются на части установленной массы. При изготовлении сырков в глазури с начинкой наполнитель вносится в промежуточную ёмкость с крышкой, откуда подаётся в дозировочно-формовочный автомат, где происходит одновременное формование сырка и наполнение начинкой в виде стержня по всей длине сырка, откуда они выходят в виде нескольких сформованных потоков, которые автоматически разрезаются на части установленной массы. Полученные сырки по транспортеру поступают в глазировочную машину, где они покрываются сверху глазурью, подаваемой по трубопроводу насосом глазури. Нижняя часть сырков покрывается глазурью при помощи вращающихся валиков глазировочной машины. Отношение массы глазури к массе сформованного сырка должно составлять не менее 20%. Излишняя глазурь с сырков удаляется струёй тёплого воздуха, подаваемого вентилятором через воздушное сопло глазировочной машины. При производстве сырков в шоколадной глазури с орехами (кокосовой стружкой) глазированные сырки перед охлаждением посыпаются из дозатора орехами (кокосовой стружкой). После глазирования сырки по транспортёру поступают в воздушный охладитель, где при температуре (0 ± 1)°С глазурь застывает на сырках в потоке, после чего сырки поступают на упаковку.
Упаковка и маркировка. Упаковку и маркировку производят в соответствии с требованиями стандарта на этот продукт. С целью улучшения консистенции готового продукта, упакованные сырки рекомендуется выдерживать в холодильной камере перед реализацией. При достижении температуры 6ºС технологический процесс считается законченным и продукт готов к реализации.
Хранение. Сырки глазированные хранят при температуре воздуха не выше 5°С. Срок годности сырков при хранении при температуре 4±2°С - не более 10 суток, при температуре не выше - 18°С - 90 суток.
Изменение срока годности сырков в зависимости от особенностей технологического процесса производства, применяемого сырья и упаковочных материалов осуществляется на основании гигиенической оценки и заключения Министерства здравоохранения Российской Федерации.
Контроль технологического процесса и управление им автоматизированы.
Дата добавления: 2015-12-19; просмотров: 16; Мы поможем в написании вашей работы! |
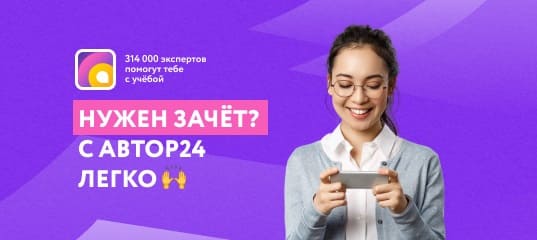
Мы поможем в написании ваших работ!