Диагностирование на основе применения встроенных контрольных средств
В период эксплуатации машин необходимо контролировать режим работы, работоспособность, техническое состояние агрегатов и механизмов. В связи с этим к технике предъявляются требования контролепригодности, приспособленности машин к техническому диагностированию непосредственно в процессе эксплуатации на основе встроенных в конструкцию машины
110
датчиков (преобразователей), специальных лючков, глазков, штуцеров
и т. д.
На машины устанавливают, как правило, недорогие, сравнительно простые приборы, позволяющие непрерывно контролировать работу агрегатов машины, вести наблюдения за их техническим состоянием. Это приборы, контролирующие загрузку двигателя, температуру охлаждающей жидкости и масла, давление в системах, частоту вращения коленчатого вала и др.
Периодический внешний осмотр и проверка отдельных механизмов простейшими методами и средствами по параметрам: давление в шинах, уровень масла в картере двигателя, натяжение ременных, цепных передач и др. — в сочетании с использованием встроенных средств есть функциональное диагностирование машины в период ее работы. Чем большевстроенных средств, обеспечивающих непрерывный контроль за показателями работы и работоспособности агрегатов машины, тем выше ее надежность и эффективность использования.
Важнейшими энергетическими параметрами, характеризующими уровень использования машин и их работоспособность, являются: 1) среднее индикаторное давление в цилиндрах дизеля, которое можно непрерывно контролировать с помощью датчика давления; максимальное давление цикла, измеряемое вибрационным методом (см. гл. 4). Непрерывный контроль этих параметров позволяет поддерживать оптимальную загрузку двигателя в период эксплуатации машин;
|
|
2) часовой расход топлива, измеряемый встроенными датчиками-расходомерами типа КИ-12371, КИ-5524, КИ-13967 и др., устанавливаемыми
в разъем топливопровода низкого давления.
Измерение этих параметров позволяет непрерывно контролировать мощностные и топливоэкономнческне показатели (N e , g e , P i , ηe) и управлять работой машины в целом, обеспечивая оптимальный режим на основе фактических показателей в конкретных условиях, а также обеспечивать своевременное эксплуатационное обслуживание (смена воздушного фильтра, регулировка или замена форсунок, профилактика топливной магистрали, корректировка угла начала нагнетания топлива и др.).
В процессе эксплуатации непрерывно или периодически с помощью простых диагностичес-
111
ких средств целесообразно Проверять темпера туру отработавших газов, давление в топливной магистрали, гидросистеме, впускном тракте дизеля и др.
|
|
Периодическое функциональное диагностирование с использованиемсредств непрерывного контроля, внешнего осмотра и простейших средств обеспечивают нормальную эксплуатацию машины, управление ее надежностью и работоспособностью.
Результаты функционального диагностирования могут являться основанием для отправки данной эксплуатируемой машины на стационарный ПТО для углубленного диагностирования и предупредительных мероприятий.
Показатели работы машин, регистрируемые встроенными средствами,
2. результаты функционального диагностирования в эксплуатации являются исходными для ресурсного диагностирования.
К Прогнозирование технического состояния машин по результатам диагностирования
Основой теории прогнозирования служит прогностика —научная дисциплина, изучающая поведение прогнозируемых систем (в частности, состояние машины) в зависимости от изменения параметров других (прогнозирующих структурных параметров составных частей после определенной наработки). Полный процесс прогнозирования технического состояния машин состоит из трех этапов: 'ретроспекции, диагностирования и прогноза. Первый этап заключается в исследовании процесса изменения параметров состояния машины в прошлом. При диагностировании (второй этап) устанавливают номинальные, допускаемые и предельные значения параметров, измеряют текущие значения этих параметров. На третьем этапе осуществляют прогноз состояния машины, в результате анализа которого принимают конкретные решения о виде и объеме ремонтно-обслуживающих работ.
|
|
и результате прогноза принимается решение о проведении капитального, текущего ремонта, регулировочных и других операций обслуживания или устанавливается остаточный ресурс машины. При этом под остаточным ресурсом понимают наработку от момента диагно-
112
стирования до предельного состояния машины или агрегата. Прогнозирование технического состояния машины осуществляют с
учетом комплекса факторов, действующих на это состояние, и в первую очередь управляющих показателей. Ими служат, как уже отмечалось, технические требования на обслуживание и ремонт: допускаемые значения параметров, в том числе допускаемые износы, периодичность ТО (контроля)
3. др. Реальный процесс технического состояния выражают функциями изменения структурных параметров, в частности степенной функцией (1.1).
|
|
При прогнозировании технического состояния машины применяют в основном два метода: прогнозирование по среднему статистическому изменению параметра совокупности одноименных составных частей и прогнозирование по индивидуальному изменению параметра одной конкретной составной части. В подавляющем большинстве используют первый метод прогнозирования из-за его простоты. При этом методе предварительно устанавливают показатели функции изменения параметра, экономические характеристики, связанные с отказом, предупредительным восстановлением, контролем параметра. В итоге определяют оптимальное допускаемое значение параметра с учетом вероятности, отказа совокупности составных частей, среднего фактически используемого их ресурса, межконтрольной наработки согласно выражению (2.2).
По результатам диагностирования сравнивают измеренное значение параметра с его предварительно установленным оптимальным допускаемым значением. При превышении измеренного значения параметра, если последний со временем увеличивается (износ детали, радиальный зазор подшипников качения и скольжения, удельный расход топлива двигателем), или меньшем измеренном значении параметра, когда он с течением времени уменьшается (диаметр вала, давление впрыскивания топлива форсункой, мощность двигателя производительность машины), принимают решение о восстановлении номинального значения параметра путем замены деталей, регулирования зазоров, давления и др.
113
Таким образом, при первом методе прогнозирования сам процесс прогнозирования изменения параметра предварительно моделируют с учетом возможных скоростей этого изменения, и по результатам диагностирования остается только сравнить измеренное значение параметра с его допускаемой величиной.
При методе прогнозирования по индивидуальному изменению параметра учитывают по результатам диагностирования его скорость изменения у конкретной составной части по наработке последней. Обычно второй метод применяют для прогнозирования надежной работы машины в течение заданной наработки (первая задача) или для прогнозирования остаточного ресурса агрегата (машины) до капитального ремонта (вторая задача). Индивидуальное прогнозирование дает больший технико-экономический эффект, чем прогнозирование по среднему статистическому, так как при индивидуальном прогнозировании погрешность учета истинной скорости изменения параметра составной части в несколько раз меньше, а значит и точнее прогноз.
Пусть в момент t K машину подвергли техническому диагностированию,
в результате которого определили изменение (приращение) параметра u(t K )=u K . В случае заданной прогнозируемой наработки(первая задача)решение сводится к ответу на вопрос: не превышает ли значение и к допускаемого при условии, что машина должна еще работать в течение t M . Если t M не задано (вторая задача), то находят остаточный ресурс агрегата по параметру при известных tк и uк.
простейшем случае решения задачи изменение параметра характеризуется гладкими выпуклыми или вогнутыми кривыми, т. е. степенной функцией (1.1) при Z(t)=0. При этом Считается, что характеристики функции изменения параметра, в частности показатель а, известны. Эти характеристики обычно устанавливают на основе анализа изменения параметра совокупности данных составных частей в прошлом.
После определения t и и к , используя выражение (1.1), находят показатель скорости изменения параметра
114
Рис. 5.15. Изменение параметра состояния конкретной составной части
Затем экстраполируют (прогнозируют), принимая во внимание заданную предстоящую наработку tм. При изменении параметра u(t K +t M ) = V c (t K +t M ) α , не превышающем предельное значение и п , данная составная частьне будет нуждаться в предупредительном обслуживании. Остаточный ресурс, когда t M не задано (вторая задача), подсчитывают по выведенной с учетом предшествующего выражения формуле
где
При учете случайной величины Z(t) выражения (1.1), обусловленной тем, что изменение параметра является ломаной возрастающей кривой, решение задачи усложняется. Известно, что такой вид реализации объясняется случайным характером эксплуатационных нагрузок составной части. На рисунке 5.15 представлены фактическое изменение параметра в виде сплошной ломаной линии, штриховые линии, характеризующие экстраполяционную функцию с показателями Vc и α, и отклонения Z от экстраполяционной функции. Штрихо-
115
вые линии идут от точек, соответствующих моментам предшествующего измерения.
При индивидуальном прогнозировании обычно применяют два критерия: вероятность безотказной работы и удельные издержки. Припервом критерии определяют такой остаточный ресурс или допускаемое отклонение параметра, которые обусловливают заданную вероятность безотказной работы. Применение экономического критерия связано с соблюдением условия (целевой функции): вероятные удельные издержки, возникающие при устранении последствий отказа за прогнозируемый период tм и при предупредительной замене в конце периода, должны быть меньше удельных издержек на замену в момент прогноза t K . Условие соблюдается в случае неравенства
(5.32)
где Q (tм) — вероятность отказа составной части за период t м ; Т СР (t M )—средний ресурс составной части по параметру; А, С — издержки соответственно на устранение последствий отказа с учетом потерь от простоя машины и на предупредительное восстановление параметра.
При изменении параметра составной части в виде ломаной кривой можно определить остаточные ресурсы: средний, с заданной вероятностью безотказной работы и оптимальный.
Средний остаточный ресурс является частным случаем остаточного ресурса с вероятностью безотказной работы, равной 0,5.
Оптимальный остаточный ресурс обусловливает минимум выражения (5.32):
(5.33) Здесь стоимость проверки, как и в выражении (5.32), есть слагаемое
величин А и С.
Вероятность отказа составной части по прогнозируемому параметру
116
где F0 (Б) —нормально распределенная функция случайной величины с нулевым математическим ожиданием и средним квадратаческим отклонением, равным единице, то есть табулированный интеграл вероятностей; σп — среднее квадратическое отклонение погрешности прогнозирования.
Среднее квадратическое отклонение погрешности прогнозирования находят по формуле
где п — число одноименных составных частей; m i — число измерений параметра i-й составной части i, j — номера составных частей и измерений.
Для повышения точности прогнозирования остаточного ресурса используют несколько значений диагностического параметра по результатам предшествующих его измерений. Общее число т значений диагностического параметра в этом случае должно быть равным 3... 5.
При т значениях диагностического параметра остаточный ресурс вычисляют по формуле, полученной методом наименьших квадратов.
Формула остаточного ресурса с заданной вероятностью безотказной работы при ломаной кривой изменения параметра имеет вид
При среднем остаточном ресурсе вероятность безотказной работы равна 0,5, а величина Б равна 0. В этом случае формула превращается в формулу (5.41).
Для упрощения расчетов используют номограмму (рис. 5.16). Она имеет вертикальные шкалы и п , tост (верхняя часть) и шкалы значений остаточного ресурса, нормированного в долях наработки t K до момента контроля (нижняя часть). Числа на наклонных прямых в верхней части номограммы одновременно обозначают
117
Рис. 5.16. Номограмма для определения остаточного ресурса составной части по параметру состояния
118
отклонение параметра к моменту контроля и наработку tк.
Порядок определения остаточного ресурса элемента.На левойверхней вертикальной шкале отмечают предельное отклонение параметра (точка А). От сделанной отметки проводят горизонтальную линию до наклонной прямой (точка Б), характеризующей отклонение параметра к моменту контроля. От точки пересечения опускают вертикаль в нижнюю часть номограммы до шкалы с заданной величиной α (точка В). Затем переходят на верхнюю горизонтальную ось, отмечая на ней значение, полученное на шкале α (точка В'). От точки В' опускают вертикаль до наклонной прямой (точка Г), характеризующей наработку tк. Проекция точки пересечения на правую верхнюю ось (точка) покажет остаточный ресурс элемента.
Пример 5.1. В результате технического диагностирования дизеля,работающего в стационарных условиях, когда t(t) мало и этой величиной можно пренебречь, установлен расход картерных газов после наработки 1,6 тыс. мото-ч, равный 68 л/мин. Предельный и номинальный расходы картерных газов соответственно равны 90 и 28 л/мин. Требуется определить остаточный ресурс дизеля, если известно, что показатель α =1,3.
Решение.Сначала устанавливают предельное отклонение параметраuп=Пп—Пн = 90—28 = 62 л/мин и отклонение параметра к моменту контроля uк = П(t)—Пн=68—28=40 л/мин. Отмечают на оси uп номограммы (рис. 5.21) значение и п в десятках единиц и проводят горизонтальную линию до наклонной прямой, обозначение которой соответствует uк=4 (в десятках единиц). От точки пересечения опускают вертикаль в нижнюю часть номограммы до шкалы tост/tк, обозначенной заданным значением α=1,3 (точка В). Отсчитывают по шкале значениеtост/tк= 0,39и переносят его на верхнюючасть номограммы. От найденной точки В' опускают вертикаль до наклонной линии, обозначенной заданным значением наработки tк = 1,6 в тысячах единиц, и затем проводят горизонталь до шкалы остаточного ресурса, на которой находят искомое tост=640 моточасов.
Тот же результат получают по формуле (5.37):
Пример 5.2. В условиях примера5.1определить остаточный ресурспри вероятности безотказной работы ЦПГ, равной 0,95, и ломаной кривой изменения параметра, характеризуемой средней квадратической погрешностью прогнозирования σп = 0,3.
Решение.Вначале находят величинуБ.Для этого используют таблицуинтеграла вероятностей (см., например, Вентцель Е. С. Теория вероятностей.—М.: Наука, 1964). При F0(B)=0,95 величи-
119
нa Б = 1,64. Подставляя найденную величину в формулу (5.37), определяют
Приближенный способ установления оптимального остаточного ресурса заключается в определении среднего остаточного ресурса по формуле (5.31) и последующей его корректировке умножением на коэффициент 0,7 (при относительно большой экономической характеристике А) или0,8.Для этого на номограмме(см.рис. 5.16)нанесены в верхнейправой части две соответствующие масштабные оси.
4. ряде случаев у диагноста отсутствуют сведения о наработке сопряжений, сборочных единиц или агрегатов машины с начала эксплуатации или ремонта, при котором их заменили или отрегулировали. Однако известны значения параметров состояния и наработка от предыдущего контроля. Например, при обезличенном ремонте двигателя' были поставлены изношенные, но годные для эксплуатации детали. При этом наработка их с момента эксплуатации неизвестна. Спустя некоторое время при ТО-3 провели первую проверку двигателя и измерили его параметры состояния. После определенной наработки вторично провели проверку с измерением тех же параметров состояния. По результатам двух измерений и известной наработке между ними находят остаточный ресурс при гладкой кривой изменения параметра: tocт=Rt'ocт;
где uп — предельный износ детали, соединения или предельное отклонение параметра; u'
и и'' —износы детали,соединения или изменение параметра состояния,установленныепри первом и втором измерениях; f — наработка между двумя измерениями.
Значения R и t'оот могут быть найдены по номограмме на рисунке 5.16. Для определения t’ост вместо t, т.е. наработки с момента эксплуатации, используют f — наработку между измерениями, а вместо и к используют и". В этом случае t’ост находят таким же путем, что и tост.
120
Для определения R вместо предельного- отклонения параметра и„ применяют и", а вместо uк—и'. Значение R устанавливают следующим образом. После нахождения в верхней части номограммы точки пересечения горизонтальной линии с отметкой и" и наклонной прямой, характеризующей и к =и', проводят вертикаль в нижнюю часть номограммы к шкале,характеризующей заданный показатель α. По полученному на этой шкале значению К, используя самую нижнюю горизонтальную шкалу К—R (на рисунке не указана), определяют R.
к Экономическая эффективность диагностирования машин
Эффективное применение диагностических средств позволяет:
сохранить оптимальные рабочие характеристики в течение всего срока
службы машины;
2...2,5 раза снизить простои тракторов, зерноуборочных комбайнов, автомобилей и других машин по техническим неисправностям за счет предупреждения отказов;
1,3... 1,5 раза увеличить межремонтную наработку сборочных единиц
5. агрегатов машин, что соответственно уменьшает число и трудоемкость ремонтов, расход запасных частей на их ремонт;
на 5...8% снизить расход топлива;
получить годовой экономический эффект от внедрения технического диагностирования минимум 100... 150 руб. на трактор и 40 руб. на комбайн, автомобиль.
В колхозах Богодуховского района Харьковской области впервые были внедрены три передвижные диагностические установки КИ-4270-ГОСНИТИ. Ими в течение трех лет продиагностировано 897 тракторов, из которых 390 отработали межремонтный период, у 234 тракторов проведены необходимые регулировки и устранены неисправности. Это позволило продлить их работу без ремонта на 160 тыс. моточасов. Общие затраты средств на ремонт и техническое обслуживание снизились на 5,9 коп. на у. э. га.
В результате внедрения диагностических установок получена экономия в сумме 184 тыс. руб. Затраты на содержание диагностических установок, включая зарплату диагностов, составили 60 тыс. руб. Расход за-
121
пасных частей на ремонт и техническое обслуживание в расчете на 1 у.
э. га снизился на 20%.
Об эффективности внедрения в сельскохозяйственном производстве диагностических методов и средств можно судить также по результатам анализа работы 51 передвижной диагностической установки, эксплуатируемой в 40 районах. Применение технического диагностирования уже в первый год эксплуатации передвижных установок позволило значительно повысить межремонтную наработку тракторов. Так, по 1222 тракторам- была продлена фактическая межремонтная наработка в среднем на один трактор на 475 моточасов. Внедрение диагностических средств в Нежинском районе Черниговской области, в хозяйствах которого работало 600 тракторов, позволило получить экономический эффект в сумме 102 тыс. руб. и продлить моторесурс тракторов на 90 тыс. моточасов. Подобные результаты получены и в ряде других зон страны.
Как показала практика, там, где широко применяется техническое диагностирование, резко уменьшаются годовые простои машин и затраты на их обслуживание и ремонт. В качестве примера можно привести Старо-минский район Краснодарского края, где техническое диагностирование и предупреждение неисправностей стали основным мероприятием в области ТО и ремонта машин.
За период внедрения диагностирования с 1981 по 1987 г. годовые простои по техническим неисправностям около 1000 тракторов хозяйств района сократились с 29240 до 16820 тракторо-дней (рис. 5.17), или на 42%, а затраты на ТО и ремонт достигли 62 коп. на 1 у. э. га при нормативе 77 коп. Коэффициент охвата капитальным ремонтом тракторов уменьшился при этом в два раза и составил в 1987 г. 0,08.
Подобные результаты наблюдаются во многих районах Украины, Белоруссии, Эстонии и России.
Диагностирование при ремонте высокоресурсных .сборочных единиц только ходовой системы 650 гусеничных тракторов при их капитальном необезличенном ремонте позволило получить годовой экономический эффект более 12 тыс. руб. в Новокубанском ремонтном предприятии Целиноградский области.
Тщательное диагностирование комбайнов «Дон-1500» первой промышленной партии в 1986 году в колхозе
122
Рис. 5.17. Сокращение годовых простоев по техническим неисправностям тракторного парка хозяйств Староминского района Краснодарского края (по оси ординат —тракторо-дни).
«Победа» Красногвардейского района Ставропольского края обеспечило увеличение наработки на отказ в 2,5 раза, уменьшение простоя при устранении последствий отказов в 1,6 раза, сокращение издержек от простоя комбайна в 1,7 раза.
Ленинградским СХИ проведено обследование 200 двигателей Д-50 тракторов МТЗ в хозяйствах Ленинградской области. При этом брались пробы Масла у 100 тракторов, эксплуатируемых в хозяйствах с развитой системой технического обслуживания, с применением диагностических средств, и у 100 тракторов, эксплуатируемых в хозяйствах, где техническое обслуживание поставлено слабо, а диагностические средства не используются. Полученная по данным анализа проб мас-
123
да скорость изнашивания основных сопряжений двигателя во втором случае оказалась (в среднем по обследованным тракторам) примерно в 1,5 раза выше, чем в первом. В хозяйствах, где диагностические средства не использовались, не менее 50% тракторов работало с форсированным износом.
Устойчивый экономический эффект по хозяйствам Ленинградской области, полученный от улучшения технического обслуживания с использованием диагностических средств, составляет 120... 150 руб. на трактор в год. В перспективе с учетом применения разрабатываемых методов
и средств диагностирования, повышения энергонасыщенности тракторов, приспособленности к диагностированию этот эффект может возрасти до 200
...300 руб.
Интересные результаты получены в результате технического диагностирования грузовых автомобилей:
35% автомобилей занижена мощность на ведущих колесах;
35... 40% установка угла опережения зажигания отличается от оптимальной;
30% автомобилей наблюдается неудовлетворительное состояние тормозов;
более чем -50% автомобилей рулевое управление не соответствует техническим требованиям.
Техническое диагностирование позволяет выявить эти неисправности и затем устранить их. В результате диагностирования и регулирования систем
и механизмов двигателя мощность на ведущих колесах грузового автомобиля увеличивается до 13% при снижении расхода топлива на 5... 10%.
Технико-экономическая эффективность диагностирования тракторов, автомобилей и сельскохозяйственных машин особенно возрастает в условиях хозрасчета и самофинансирования, при бригадном, семейном и арендном подряде, когда центр тяжести ремонта и технического обслуживания перемещается в мастерские хозяйства, бригады.
Описанную технико-экономическую эффективность диагностирования с последующими операциями обслуживания и ремонта в основном устанавливали на основе анализа отчетных и статистических данных. Ее можно также определять аналитическим путем. При этом основными показателями эффективности служат: увели-
124
чение вероятности безотказной работы составных частей и машины в целом; повышение фактически используемого ресурса составных частей; увеличение коэффициента готовности, снижение расхода топлива, запасных частей, суммарных удельных издержек на единицу наработки, связанных с техническим обслуживанием и ремонтом, и др.
Обычно вначале определяют технический эффект, затем, учтя экономические характеристики (издержки на устранение последствий отказа, издержки на предупредительное восстановление составной части, издержки на диагностирование), рассчитывают экономический эффект. Экономический эффект определяют, как правило, за один год.
Например, при установлении технико-экономической эффективности оптимизации допускаемого отклонения параметра, применяемого при диагностировании, определяют вероятности отказа составной части и предупредительного ее восстановления. Эти показатели при заданном межконтрольном периоде позволяют получить технический эффект в виде увеличения вероятности безотказной работы за межконтрольный период. Умножая полученные вероятности отказа и предупредительного восстановления соответственно на величины издержек и отнеся полученные вероятностные издержки к фактически используемому ресурсу, определяют в результате сравнения базового и оптимального вариантов экономический эффект за тот же межконтрольный период. Зная число периодов в году, вычисляют годовой экономический эффект.
При оптимизации допускаемого отклонения параметра и периодичности обслуживания используют тот же подход, но при этом сравнивают базовый и оптимальный варианты при различной периодичности. При этом применяют универсальную формулу
(5.39)
где И1 и И2 —годовые эксплуатационные издержки потребителя (колхоза, совхоза и т. п.) на машину, агрегат, составную часть при базовом и оптимальном (применение диагностирования) вариантах, руб.; K1 и К2 — сопутствующие удельные капитальные вложения потребителя на машину, агрегат, составную часть при базовом и оптимальном вариантах, руб.; Ен—нормативный коэффициент эффективности капитальных вложений. Обычно он равен 0,15; A1 — число диагностируемых в году машин, агрегатов, составных частей.
125
Издержки потребителя на единицу наработки обычно учитываютфункцией (2.2), где при базовом вариант те D может быть равным единице. Значение функции определяют за межконтрольный период. Учитывая долю или число г межконтрольных периодов в году, можно записать;
6. случае, если издержки G (D, t M ) вычисляют не за межконтрольный период, а на единицу наработки (моточасы, физический или условный эталонный гектар, тонна выработанной продукции и т. п.), издержки G(D, t M ) умножают на годовую наработку W при оптимальном варианте.
Удельные капитальные вложения могут появиться в результатеприобретения диагностического оборудования, стендов, установок, в том числе строительства здания, сооружения для установки оборудования. В большинстве случаев K1 = K2.
При определении технического эффекта в виде увеличения вероятности безотказной работы составной части При K1 = K2
(5.40) Здесь первое и второе слагаемые характеризуют соответственно
базовый п оптимальный варианты расчета.
Увеличение фактически используемого ресурса составной части по параметру (ед. наработки) подсчитывают по формуле
(5.41)
Годовой экономический эффект диагностирования
(5.42) Пример 5.3.Определить годовой экономический эффект отдиагностирования шариковых подшипников качения по параметру радиального их износа по сравнению с существующим базовым вариантом их замены после отказа. Оптимальный допускаемый износ подшипника при диагностировании D0 = D/uп = 0,5. Средний ресурс подшипника Тср = 2100 моточасов, коэффициент вариации ресурса v = 0,5, межконтрольный период
tм = 1000 моточасов, показатель степени функции изнаши-
126
вания α=1. Экономические характеристики A = 24 руб.; С =8 руб. и В = 0,3 руб. Существующий базовый вариант характерен отсутствием диагностирования (D0=1; tм→∞).
Машины, в которых рассматриваемые подшипники работают, имеют среднюю годовую наработку W= 1200 моточасов. Число диагностируемых в году подшипников A1 = 12 200 шт.
Решение.По номограмме на рисунке2.2определяют приT0= Tср/tM=2100/1000=1,1; v = 0,5 и D0 = 0,5 вероятность отказа Q(D, tM)=0,21. Фактически используемый при этом ресурс подшипника находят по номограмме на рисунке 2.3. Нормированный в единицах t M этот ресурс составляет T 0 (D, tM) = l,6 или T cp (D, tM) = To(D, t M ) t M = 1,6·1000= 1600 моточасов. Применяя формулу (5.40), устанавливают снижение средней вероятности отказа в течение одного года при диагностировании подшипника:
Здесь при базовом варианте вероятность отказа подшипника равна единице в течение его ресурса 2100 моточасов.
Применяя формулы (5.40), определяют экономический эффект как разность двух значений функции:
При базовом варианте С = В = 0. Число диагностирований Kп(D, tM) = 1,6 определено по формуле (2.9). Оно приближенно равно отношению T CP (D, t M )/t M .
Контрольные вопросы и задания. 1.Дайте определение технической диагностикемашин. 2. Что понимается под электронной диагностикой машин? 3. В чем заключается методика определения качества агрегатов машин? 4. Какие методы диагностирования машин применяются на практике? 5. В чем заключается сущность диагностирования ДВС по энергетическим параметрам переходных процессов (разгона или выбега)? 6. В чем сущность виброакустического метода диагностирования и его преимущества? 7. Какие способы выделения и формирования виброакустических диагностических параметров вы знаете? 8. Поясните физическую сущность вибрационного метода диагностирования ДВС по энергетическим параметрам ДВС. 9. Какие вы знаете методы диагностирования топливоподающих систем и в чем их сущность? 10 Какие методы прогнозирования остаточного ресурса вы знаете?
127
ГЛАВА VI.
Дата добавления: 2021-04-24; просмотров: 139; Мы поможем в написании вашей работы! |
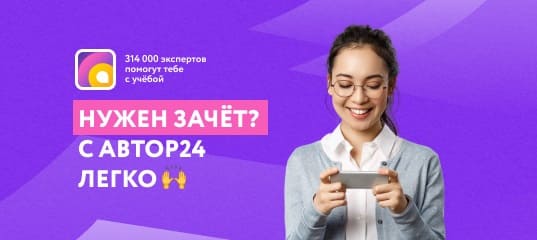
Мы поможем в написании ваших работ!