Классификация методов диагностирования машин
Методы диагностирования подразделяют на две группы (рис. 5.2). органолептические (или субъективные) и инструментальные (объективные). По характеру измерения параметров различают прямой (непосредственное измерение) и косвенный методы.
83
Рис. 5.2. Классификация методов диагностирования
Органолептические методы диагностирования включают в себяослушивание, осмотр, проверку осязанием и обонянием.
Ослушиванием выявляют места и характер ненормальных стуков, шумов, перебоев в работе двигателя, отказов в трансмиссии и ходовой системе (по скрежету и шуму), неплотности (по шуму прорывающегося воздуха) и т. п. Осмотром устанавливают места подтекания воды, масла, топлива, цвет отработавших газов, дымление из сапуна, биение вращающихся частей, натяжение цепных передач, увеличение количества несрезанных растений, невымолоченных зерен и т. п.
Осязанием определяют места и степень ненормального нагрева, биения, вибрации деталей, вязкость, липкость жидкости и т. п.
Обонянием выявляют по характерному запаху отказ муфт сцепления, поворота, течь бензина, электролита, отказ электропроводки и т. п.
84
Инструментальные, или объективные,методы применяют дляизмерения и контроля всех параметров технического состояния, используя при этом диагностические средства.
По назначению методы диагностирования подразделяются на функциональные, предназначенные для измерения параметров состояния,характеризующих функциональные свойства составных частей и агрегатов, и ресурсные, предназначенные для определения остаточного ресурсадиагностируемых узлов и агрегатов машины.
|
|
По физическому принципу или процессу методы диагностированияделятся на энергетический, пневмогидравлический, тепловой, виброакустический, спектрографический, магнитоэлектрический, оптический и некоторые другие.
Каждый метод предназначен для контроля определенного физического процесса и основан на применении определенного физического явления. Классификация по использованному физическому процессу позволяет наиболее полно выявить возможности и техническую характеристику соответствующего метода диагностирования.
Физический процесс характеризуется изменением физической величины во времени. В основе энергетического процесса лежит физическая величина — сила, мощность; пневмогидравлического — давление; теплового
— температура; виброакустического — амплитуда колебаний на определенных частотах и т. д.
По характеру измерения параметров методы диагностированиямашин подразделяются на прямые и косвенные.
|
|
Прямые методы основаны на измерении структурных параметровтехнического состояния непосредственно прямым измерением: зазоров в подшипниках, прогиба ременных и цепных передач, размеров деталей и т. д.
Из-за своей простоты прямые методы нашли широкое практическое применение особенно при контроле и регулировании механизмов и устройств, расположенных снаружи агрегатов машины, доступных и удобных для проверки, не требующих разборки механизмов (приводные механизмы, режущие аппараты комбайнов, ходовая часть, рулевое управление тормозная система и др.). Применение прямых методов измерения параметров технического состояния объектов, находящихся внутри
85
агрегатов (цилиндропоршневая группа, подшипниковые узлы коленчатого вала двигателя), ограничено большой трудоемкостью и необходимостью разборки агрегата.
Косвенные методы основаны на определении структурных параметровтехнического состояния агрегатов машин по косвенным (диагностическим) параметрам при установке датчика или диагностического устройства снаружи агрегата без разборки механизмов машины. Косвенные методы основываются на измерении непосредственно физических величин, характеризующих техническое состояние механизмов, систем и агрегатов машин: давление, перепад давления, температура, перепад температуры рабочего тела в системе, расход газа, топлива, масла, параметры вибрации составных частей машин, ускорение при разгоне двигателя и др. Многие методы осуществляются на основе преобразования механических величин в электрические с применением электронных диагностических приборов и установок.
|
|
Рассмотрим различные методы определения диагностических параметров.
Измерение давления.Величина давления(Р),нарастания давления(dP/dt), перепад давления(ЛР)в значительной степени определяюттехническое состояние и показатели работы многих агрегатов и систем машин.
Физическая сущность основана на том, что в системах и полостях агрегатов машин устанавливаются определенные оптимальные величины Р, dP/dt, Р,характерные для соответствующих конструкций и марок машины.
В процессе эксплуатации машины ее техническое состояние изменяется в результате износа сопряженных деталей, нарушения регулировок, загрязнения фильтров, что приводит к изменению состояния системы и соответственно изменению упомянутых величин. Так, например, связь износа шейки и давления масла в смазочной системе двигателей
|
|
внутреннего сгорания (ДВС) определяется формулой | |
Им = b(а/Рм)1/m, | (5.1) |
где Им — износ шейкн вала; b —увеличение зазора, обусловленного износом шейки; а постоянный коэффициент, m — показатель степени, зависящий от частоты вращения коленчатого вала
86
По давлению в смазочной системе, которое в процессе эксплуатации изменяется от начального Рмн = 0,2 ...0,7 до предельного РМпр =0,1 ...0,15 МПа определяют техническое состояние подшипников коленчатого вала, на номинальной частоте вращения коленчатого вала. Для каждого типа двигателя устанавливаются номинальная, допускаемая и предельная величины давления в смазочной системе.
Исключив фактор влияния масляного насоса и фильтров, по изменению давления масла в системе определяют общее техническое состояние подшипниковых узлов.
Таким образом, по давлению в масляной магистрали определяют общее техническое состояние масляного насоса, фильтров, подшипниковых узлов коленчатого вала двигателя. Давление в цилиндре ДВС в конце такта сжатия характеризует герметичность надпоршневого пространства (техническое состояние поршневых компрессионных колец, плотность прилегания клапанов газораспределения). Нарастание давления в цилиндре ДВС в зоне активного горения топлива на градус поворота коленчатого вала характеризует жесткость протекания рабочего процесса, существенно влияющую на надежность и долговечность цилиндропоршневой группы и кривошипно-шатунного механизма двигателя. Максимальное и среднеиндикаторное давление цикла характеризует мощностные параметры двигателя. В топливоподающей системе дизеля важнейшими показателями ее работы и технического состояния являются давление начала впрыскивания топлива форсункой в цилиндре двигателя, давление, развиваемое плунжерной парой топливного насоса, время падения давления в полости штуцера высокого давления (над нагнетательным клапаном), перепад давления в системе низкого давления.
Показатели работы гидросистемы: давление срабатывания автоматов золотников, предохранительного клапана, производительность насоса, утечки в прецизионных парах при заданном давлении.
Метод диагностирования по изменению температуры рабочего тела в полостях агрегатов машин. Температура рабочего тела многихсистем агрегатов машин является важным показателем работы и технического состояния многих механизмов. Так, например, температура
87
|
—угловое |
газов в цилиндре в конце такта сжатия дизеля определяет его пусковые качества, температуру Отработавших газов, характер протекания рабочего процесса в цилиндрах двигателя. По температурным параметрам определяется техническое состояние системы охлаждения: степень загрязненности радиатора, образование накипи в головке и блоке двигателя и т. д. Кроме того, при Диагностировании многих механизмов и систем машин необходимо контролировать и поддерживать в заданных пределах температуру системы охлаждения, смазки Двигателя, масла гидросистемы и т. п.
Метод диагностирования по параметрам ускорения на неустановившихся режимах работы ДВС (переходных процессах разгона или выбега).Метод основан на измерении ускорения,времени разгона иливремени выбега коленчатого вала двигателя.
Индикаторный крутящий момент двигателя в динамических режимах определяется выражением
(5.2)
где M i — индикаторный крутящий момент двигателя, Н•м; М мп — момент механических
потерь, Н•м; I — приведенный момент инерции двигателя, Н•м•с2; dωdt ускорение коленчатого вала, рад/с2.
Если при работе тракторного дизеля на холостом ходу с малой частотой вращения быстро передвинуть рычаг подачи топлива до упора, то разгон двигателя произойдет при полной цикловой подаче топлива. Положение рейки топливного насоса будет соответствовать корректорной ветви характеристики до момента уменьшения подачи топлива за счет работы регулятора. В условиях разгона двигатель загружается до полной цикловой подачи топлива, и его индикаторная работа затрачивается на преодоление инерционных сил сопротивлений и механических потерь двигателя.
На основе уравнения моментов можно получить уравнение мощности
(5.3)
где ω — угловая скорость вращения коленчатого вала двигателя.
88
Учитывая, что приведенный момент инерции данного двигателя величина приблизительно постоянная,
(5.4)
где Сω — коэффициент, постоянный для данной марки двигателя.
Из выражения (5.3.) видно, что по изменению углового ускорения можно определить эффективную мощность двигателя.
Для оценки работы отдельных цилиндров целесообразно определять мощность двигателя при работе с частью выключенных цилиндров. Для бестормозного неустановившегося режима работы
(5.5)
где Z — число цилиндров двигателя; ZР и ZB — число работающих и выключенных цилиндров двигателя; М i1 — индикаторный крутящий момент одного цилиндра.
После преобразований для бестормозного разгона
(5.6)
где Р мп — давление механических потерь, МПа.
Для бестормозного выбега уравнение (5.6) будет иметь вид
(5.7)
где С = 9550Vh Z — механический КПД; Vh — рабочий объем цилиндра, л; тд — 30 д
коэффициент тактности двигателя.
Таким образом, по уравнению (5.6) можно определить неравномерность работы цилиндров, индикаторную мощность двигателя; по уравнению (5.7)—мощность механических потерь.
Эффективную мощность двигателя можно определять и по величине продолжительности разгона двигателя от минимально устойчивой частоты вращения п 1 до номинальной n2.
Для измерения мощности двигателя по временному интервалу при разгоне устанавливают минимально устойчивую частоту вращения коленчатого вала. Затем,
89
резко увеличивают подачу топлива путем перемещения рычага до упора. Цифровым измерительным устройством измеряется временной интервал между частотой вращения n 1 и п 2 . Временной интервал при разгоне изменяется обратно пропорционально мощности двигателя.
Метод реализован в электронном диагностическом приборе ИМД-Ц, автоматизированной диагностической установке ДИПС (КИ-13940) и автоматизированном машпкотестере АМТ (КИ-13950).
Виброакустический метод диагностирования.Виброакустическаядиагностика — отрасль знаний, включающая, теорию и методы организации процессов распознавания технических состояний машин и механизмов по исходной информации, содержащейся в виброакустическом сигнале.
Виброакустическим сигналом называют физические величины, характеризующие механические колебания, сопровождающие работы технического объекта. Характеристики виброакустического сигнала, содержащие информацию о структурных параметрах технического состояния объекта, являются диагностическими параметрами состояния.
Методы виброакустики отличаются от многих, методов большей универсальностью, мгновенной реакцией на незначительные изменения в системах и механизмах машин. Многообразие физической природы вибраций, широкий частотный диапазон обеспечивают высокую информативность энергетических параметров работы агрегатов, техническое состояние подшипников, зубчатых механизмов, цилиндропоршневой группы, позволяют контролировать качество изготовления, ремонта, обкатки машин, предотвращать разрушения, обнаруживаемые на- ранней стадии зарождающегося дефекта.
Знание особенностей взаимодействия возмущающих сил в механизмах агрегатов, распространения упругих волн, а также свойств среды позволяет найти допустимые границы применимости методов классической механики и сформулировать условия, при которых вибрации, возникающие под действием приложенной силы, зависят от параметров, характеризующих качество, техническое состояние, показатели работы машины.
Динамические процессы, протекающие в различных кинематических парах и системах машин, различаются
90
многими свойствами, в числе которых характер взаимодействия, момент появления ударного импульса, частота повторения и интенсивность взаимодействия.
В соответствии с этим для выделения полезной составляющей из вибрационного процесса используют различные методы локализации: временной (выделение сигнала во времени, например в цикле работы двигателя), частотной, амплитудной селекции, перераспределение нагрузки на проверяемый механизм с целью повышения уровня полезного сигнала и снижения помех от непроверяемых механизмов.
Приближение места установки вибропреобразователя к месту взаимодействия соединения или узла, направленность его чувствительного элемента относительно возмущающей силы служат эффективным способом повышения относительного уровня полезного сигнала, что особенно важно при диагностировании сравнительно простыми малогабаритными электронными приборами. Правильно выбранный способ установки и крепления датчика на объекте способствует повышению эффективности вибрационного диагностирования.
Одним из наиболее эффективных способов оценки вибрационных процессов применительно к механическим системам является метод моделирования. В процессе построения моделей определяют основные связи составляющих частей и присущие объекту закономерности, отсеиваются второстепенные признаки.
Наиболее общими по степени формализации и удобными для формирования метода диагностирования машин служат математические модели.
Математические модели могут быть построены на основе выражения импульсов силы и приращения количества движения (изменения кинетической энергии), вызванного взаимодействием и соударением сопряженных деталей:
(5.8)
где v0 — скорость в начале удара; и скорость в конце удара; т — масса ударяющей детали, k коэффициент восстановления скорости при ударе, которым в первом
приближении определяется как
91
Рис. 5.3. Импульсы вибрации при начальном (а) и предельной (б) зазорах:
A 1 , А 2—амплитуды; φ1, φ2—фазы виброимпульса соответственно при начальном мпредельном зазорах в сопряжении
Коэффициент k характеризует упругость соударяющихся деталей и экспериментально определяется но результатам измерении высоты падения h шарика на деталь и высоты отскока шарика после удара h'. При упругом ударе k зависит от формы соударяющихся тел, соотношения масс и физических свойств металлов. Он определяет потерянную при ударе кинетическую энергию. Удары, вызнанные резким изменением направления силы или силового импульса детален в агрегате, движущихся с большой скоростью, рассматриваются как скоростные импульсные удары (перекладка поршня в заборе и удар об стенку гильзы, удар клапана при посадке в гнездо, иглы форсунки и т. д.).
Ударный импульс вызывает в соударяемых деталях деформацию и упругие колебания с соответствующими амплитудами, фазами и частотами (рис. 5.3).
Скорость детали в начале удара Do служит функцией многих величин, то есть
vo = f(S, n, F 1 , F 2 , m 1 , т 2 , t 1 , t2 и др.), | (5.9) |
где S — зазор между соударяемыми деталями; п — частота вращения пала; F1, F2— возмущающие силы; m 1 , т 2 — массы взаимодействующих деталей; t 1 , t2 — температуры соударяемых деталей.
На основе выражения (5.8) разработаны математические модели связи диагностических параметров со структурными (зазорами в сопряжениях).
Цилиндропоршневая группа.При работе двигателя происходитперекладка поршня в зазоре с одной стороны гильзы на другую, в результате па гильзу действует ударная нагрузка — основной источник деформации и вибрации гильзы цилиндра. Наиболее интенсивный удар
92
Рис. 5.4. Зависимости амплитуды (1) и фазы (2) виброимпульсов от зазора в ЦПГ дизеля СМД-6-1:
ЦПГлев — для левого рядя цилиндров; ЦПГправ — для правого ряда цилиндров
при перекладке поршня возникает вблизи ВМТ, так как величина нормальной боковой силы N имеет здесь наибольшее значение.
В результате исследования кинематики механизма цилиндропоршневой группы тракторного дизеля получена зависимость ударного Импульса ОТ зазора в сопряжении поршень — гильза:
(5.10)
где P i,j — давление газов и цилиндре; λ—отношение радиуса кривошипа к длине шатуна.
Для одного типоразмера двигателя и определенного установившегося режима работы уравнение (5.10) примет вид
(5.11)
где kп - постоянный коэффициент для данного типа двигателя.
На рисунке 5.4 показаны зависимости амплитуды и фазы вибросигнала, вызванного ударом поршня о гильзу, от зазора В сопряжении поршень — гильза.
Клапанный механизм газораспределения.На основе выражения(5.8)импульс силы при посадке или подъеме- .клапана определяется выражением
(5.12)
где kг— коэффициент упругости соударяемых деталей; т к — масса клапана, кг; mпр — масса пружины, кг; vкл — скорость движения клапана в момент конца подъема или посадки, м/с.
Скорость vкл определяется как производная перемещения толкателя с учетом передаточного числа коромысла:
(5.13)
93
где R к , r K — радиусы кулачка, м; φРВ — угол поворота распределительного вала, град; nрв
— частота вращения распределительного вала z передаточное число коромысла.
Текущее значение пути или высоты подъема толкателя
(5.14)
Для момента подъема или посадки клапана
(5.15)
где Sкл — тепловой зазор между коромыслом и стержнем клапана, м.
Перейдя от косинуса угла к его синусу, скорость Клапана в момент подъема или посадки
(5.16) Используя выражение (5.8), получают математическую модель связи
ударного импульса с зазором в клапанном механизме:
(5.17) Для одного типоразмера ДВС выражение (5.17) преобразуется в весьма
простую зависимость ударного импульса от теплового зазора.
Выражение (5.8) может быть использовано для получения аналогичных математических моделей для многих механизмов машин. На рисунке 5.5 показаны зависимости амплитуды виброимпульса от зазора в клапанном механизме (а), и от зазоров в шатунных подшипниках (б).
Для многих процессов, протекающих в ДВС, и механизмов машин получены математические модели связи диагностических вибрационных параметров с показателями работы и техническим состоянием агрегатов машин на основе дифференциального уравнения, описывающего колебания материальной точки детали или корпуса агрегата
94
Рис. 5.5. а) Амплитудные (1) и фазовые (2) зависиморти виброимпульсов от теплового зазора в газораспределительном механизме дизеля СМД-62; б) Зависимости амплитуды А (3, 4, 5, 6) и фазы(φ)виброимпульсов от зазора в шатунных подшипниках:
3 — работа на всех цилиндрах, датчик на блоке; 4 — работа на половине цилиндров, датчик на блоке; 5 — работа на всех цилиндрах, датчик на коленчатом валу; 6 — работа на половине цилиндров, датчик на коленчатом валу
По величине ускорения , скорости
перемещению х можно определить значение возмущающей силы F(t) (давление газов в цилиндре, давление начала впрыска топлива форсункой и другие параметры).
Детали агрегата имеют собственную частоту механических колебаний, отличную от собственной частоты колебаний других деталей. Большинство механизмов машин формируют вибрации импульсного характера с высокочастотным заполнением, отличающиеся по амплитуде колебаний. Частота следования импульсов в цикле работы машины соответствует кинематике механизма, определяется взаимодействием сил, возбуждающих вынужденные колебания, и, как правило, кратна частоте вращения основного вала, находящегося во взаимодействии с рассматриваемыми механизмами.
В таблице 5.1 приведены формулы для определения частот возмущающих сил основных механизмов тракторов и зерноуборочных комбайнов.
Частота собственных упругих колебаний деталей агрегатов определяется уравнением
95
Дата добавления: 2021-04-24; просмотров: 342; Мы поможем в написании вашей работы! |
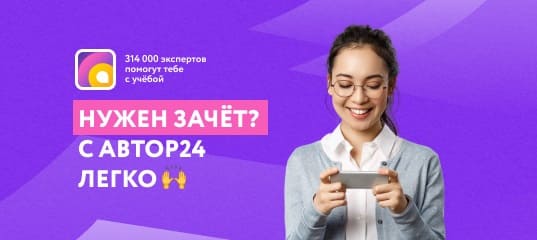
Мы поможем в написании ваших работ!