Динамические методы, применяемые для диагностирования тракторов и сложных сельскохозяйственных машин
Измерение энергетических показателей дизелей виброакустическимметодом. Индикаторная диаграмма цилиндра дизеля несет в себе большую информацию о рабочем процессе, техническом состоянии и нагрузке дизеля. Получение диаграммы традиционными средствами с помощью датчиков индицирования, устанавливаемых в полость камеры сгорания, отличается большой трудоемкостью, связанной со сверлением отверстия в головке блока.
Большие возможности для получения индикаторной диаграммы имеет виброакустический метод, основанный на измерении изменения виброперемещения наружной поверхности головки блока или торцевой поверхности шпильки крепления блока цилиндров, пропорционально изменению давления газов в цилиндре дизеля.
Для измерения вибропроцессов шпильки, вызванных давлением газов на ее торцевую поверхность, с помощью резьбового соединения устанавливают вибропреобразователь типа Д-14. При воздействии механических упругих колебаний вдоль продольной оси вибропреобразователя инерционная масса испытывает действие силы, при этом пьезоэлементы подвергаются деформации сжатия-растяжения, и на электродах пьезоэлементов возникают электрические заряды, пропорциональные действующему ускорению.
Для конкретного датчика при постоянной частоте диагностического сигнала уравнение колебания материальной точки блока агрегата имеет вид
|
|
Fsin((ωt±(φ)=CX(t), (5.20)
где F — сила, действующая на шпильку; ω=2πf — круговая частота гармонического колебания (f — частота гармонического колебания); С—постоянная величина, зависящая от частоты диагностического сигнала, от параметров датчика и параметров канала про-
102
хождения сигнала; X(t) — перемещение места крепления датчика вдоль шпильки.
Выражение (5.20) показывает, что изменение амплитуды виброперемещения X пропорционально изменению давления газов в цилиндре дизеля P z .
На рисунке 5.10 показаны осциллограммы трех сигналов: сигнал индицирования Г, вибросигнал 2' и отметки ВМТ 3'. Диаграмма, полученная виброакустическим методом, идентична индикаторной диаграмме, полученной с помощью датчика индицирования.
Амплитуда вибросигнала Ав изменяется пропорционально изменению давления в цилиндре дизеля:
A B =(1-I)k K k KP F(t), (5.21)
где I — коэффициент прохождения волны сжатия-расширения; F(t)— сила, действующая на шпильку за рабочий цикл; kк — коэффициент, характеризующий конструктивные особенности дизеля данной марки; k кp -—коэффициент, учитывающий способ крепления вибропреобразователя.
|
|
На рисунке 5.11 приведены зависимости максимальных амплитуд и сигнал индицировання А i от нагрузочного режима работы дизеля Д-240.
По максимальным значениям амплитуд вибросигнала при рабочем процессе (Аzmах, рис. 5.10) и при прокручивании дизеля (А с ) определяется максимальное давление газов рабочего процесса Ртах и максимальное давление сжатия Р с .
Виброакустический метод определения индикаторных параметров представляет большой практический интерес как для диагностирования технического состояния, так и для непрерывного контроля степени загрузки дизеля.
Диагностирование топливоподающей системы тракторных и комбайновых дизелей. При впрыскивании топлива игла или штифтраспылителя перемещается до упора, открывая сопло распылителя, и в конце опрыскивания под действием
Рис. 5.10. Осциллограммы трех сигналов:
1' —сигнал индицирования; 2' —видеосигнал; 3' —отметки ВМТ
103
Рис. 5.11. Зависимости максимальных амплитуд сигнала индицирования и вибросигнала от нагрузки дизеля (а); значения параметров индикаторной диаграммы от нагрузки дизеля Д-249 (б)
упругости пружины садится в гнездо. Скорость подъема и посадки иглы 1,6... 2,2 м/с Перемещение иглы с такой скоростью, ударный характер -
|
|
ее подъема и посадки вызывают интенсивное соударение и формирование
вибрационных импульсов, регистрируемых вибродатчиком, устанавливаемым на терец форсунки.
104
Достаточно полную информацию о динамике иглы-форсунки в процессе впрыскивания топлива имеют максимальные виброускорения форсунки, возникающие при подъеме и посадке иглы распылителя.
Между давлением начала впрыскивания, и максимальными виброускорениями форсунки, возникающими при подъеме и посадке иглы распылителя, существует линейная связь (рис. 5.12). Уменьшение давления начала впрыскивания, происходящее в условиях эксплуатации, увеличивает амплитуду вибросигнала, возникающего при ударе иглы распылителя о корпус форсунки, и уменьшает амплитуду вибросигнала, возникающего при посадке иглы распылителя.
Уравнения зависимостей имеют вид:
Апс = k1Рнв-k2; Апд = k3-k4Рнв,
где Апс—значение амплитуды вибросигнала при посадке; Aпд — значение амплитуды вибросигнала при подъеме; k 1 , k 4 — коэффициенты; k2, k 3 — коэффициенты.
Ухудшение подвижности иглы распылителя в большей мере отражается на виброускорениях форсунки, возникающих при посадке иглы распылителя. При ухудшении подвижности иглы возрастает нестабильность максимальных амплитуд виброимпульсов.
|
|
Амплитуда вибросигнала, возникающего при посадке иглы распылителя (рис. 5.13), при диагностировании форсунки играет первостепенную роль, так как изменение любого параметра технического состояния форсунки в условиях эксплуатации дизелей приводит к уменьшению ее максимального значения.
Магнитоэлектрический метод диагностирования по параметрам перемещения подвижных деталей. Метод основан на регистрацииизменяющегося магнитного потока в предварительно намагниченных деталях диагностического механизма. Индицируемая ЭДС в магниточувствительном элементе датчика пропорциональна скорости движения намагниченной детали, то есть
vвых = kс(t),
где v вых — ЭДС на выходе датчика; k — коэффициент пропорциональности; с — скорость движения детали, м/с; t — время, с.
Метод позволяет регистрировать перемещения, фазовые параметры деталей агрегатов, определять отклонения этих параметров от номинальных значений и при-
105
Рис. 5.12. Временные диаграммы процессов при впрыскивании топлива:
а — давление в топливопроводе у форсунки; б — скорость подвижных деталей у форсунки; в — вибрации форсунки; г — скорость движения нагнетательного клапана; д — вибрации секции топливного насоса; ВМТ К и НМТ К — нижняя и верхняя мертвая точка
кулачка; ВМТ п — верхняя мертвая точка параметра
меним для определения многих показателей работы и технического состояния механизмов и систем машин. Так, например, установлена в определенных условиях связь между интегральной характеристикой движения нагнетательного клапана с подачей топлива секцией насоса, моментом начала нагнетания и степенью износа плунжерной пары золотникового типа,
106
Рис. 5.13. Зависимость амплитуды виброакустического сигнала форсунки от давления начала впрыскивания:
1 — при посадке иглы распылителя без частотной фильтрации; 2 — при посадке иглы распылителя с фильтром 16 кГц; 3 — при подъеме иглы распылителя без частотной фильтрации; 4 — при подъеме иглы распылителя с фильтром 16 кГц
Движение нагнетательного клапана и вибрации форсунки определяются характером нагнетания и впрыскивания топлива. В связи с этим определена связь параметров движения нагнетательного клапана с объемом топлива, поданного из надплунжерного пространства в полость штуцера, и моментом начала нагнетания топлива плунжерной парой. Общий объем топлива, нагнетаемого плунжерной парой, определяется выражением
(5.22)
где SK - площадь нагнетательного клапана, м2; hp - величина нагружающего хода нагнетательного клапана, м; k - коэффициент, зависящий от числа Рейнольдса и шероховатости поверхности, кг·с, hK - высота подъема нагнетательного клапана, м; B = R/δ, R - постоянная результирующая сила; δ - жесткость пружины, Н/м; t — время, с.
Выражение (5.22) показывает связь величины нагнетания топлива плунжерной парой с параметрами движения нагнетательного клапана.
Нагнетание топлива из полости штуцера в топливопровод высокого давления начинается при движении разгрузочного пояска по каналу седла. Нагнетательный клапан для объема полости штуцера играет такую же роль, что и плунжер для объема надплунжерного пространства.
Угол поворота кулачкового вала от начала нагнетания топлива, а следовательно, от начала движения нагнетательного клапана до ВМТ плунжера соответствует
107
углу нагнетания φнн. Косвенно угол φнн определяется углом поворота кулачкового вала топливного насоса φннд от нижней мертвой точки кулачка до начала движения нагнетательного клапана, то есть φннд= (180—φ1)—φнн.
Так как угол φ1 постоянный для данного профиля кулачка, то угол φннд является диагностическим параметром угла начала, нагнетания (рис. 5.12).
Оценка качества сборки и обкатам агрегатов машин.После сборкиагрегаты машин проходят обкатку на стендах, где осуществляется приработка трущихся поверхностей зубчатых передач, подшипников, шлицевых соединений и других механизмов. В ряде случаев на заводах-изготовителях и ремонтных предприятиях оценку качества сборки и обкатки агрегатов осуществляют путем внешнего осмотра, что исключает их объективную оценку.
Разработан метод оценки качества сборки и обкатки агрегатов машин по виброакустическим характеристикам. Вибрации агрегата оцениваются с
× ××
помощью виброперемещения х, скорости х и виброускорения х . Вибрационная (колебательная) мощность N × N x определяется произведением
x
×
соответствующей силы F на виброскорость х :
(5.23)
×
где φF, х – угол между направлением силы и виброскорости.
Амплитудно-частотные характеристики вибрационного процесса при установке датчика вибрации в диагностических зонах корпуса агрегата на режимах обкатки интенсивно изменяются в зависимости от качества изготовления, сборки узлов, возникающих, в процессе обкатки неисправностей и дефектов.
Так, например, для оценки неисправностей и износа зубчатых колес по спектральным составляющим используется уравнение
f(t)= А соs(2πfнt±φ), | (5.24) |
где f(t) —сигнал как функция от времени t; f н — несущая частота, Гц; А —амплитуда сигнала, м/с; φ —фазовый угол, рад.
Неисправности подшипниковых узлов вследствие овальности шейки, перекоса колец, дефектов посадочных мест, несоблюдения соосности и др. определяются по из-
108
менению вибропараметров, характеризуемому выражениями:
нарушение соосности
(5.25)
где А (ω)—амплитуда вибрации; М — масса вращающейся части узла; εс — эксцентриситет; ω — угловая скорость вращения;
погрешность, связанная с изготовлением зубчатых колес h 0 и износом
hi,
(5.26)
где А (f) — амплитуда вибрации на частоте f=n/60; В, С, R — постоянные данной конструкции.
Разностенность внутренних колец подшипников вызывает слагающую вибраций с частотой вращения f = n/60, Гц, где п — частота вращения вала подшипника, с-1, овальность внутренних колец — слагающую с двойной частотой вращения; неуравновешенность сепаратора и его смещения на величину зазора плавания вызывает слагающую f (Гц) с частотой вращения сепаратора, равную
(5.27)
где D0 — диаметр окружности, по которой расположены центры шариков; d 0 — диаметр шариков, м.
Разномерность шариков (роликов) и периодическое изменение жесткости подшипника при их перекатывании создают вибрации на частоте
(5.28)
где z —число тел качения (шариков).
Наличие k граней на поверхности шарика (ролика) вызывает вибрации на частоте
(5.29)
В результате износа рабочих поверхностей внутреннего и наружного колец могут появиться дополнительные колебания с частотами
(5.30)
где k 1 — число дефектных мест на рабочих поверхностях внутреннего или наружного кольца.
109
Неуравновешенность ротора (дисбаланс) при чисто статическом дисбалансе вызывает на опорах одинаковые по значению и совпадающие по фазе вибрации.
Чувствительность для контролируемой роторной машины и применяемого прибора определяют по результатам балансировки с креплением к ротору груза mпр.
Зная балансировочную чувствительность агрегата k, можно осуществлять балансировку однотипного ротора, не снимая с машины.
Из приведенных выражений видно, что в зависимости от состояния механизма, сборочной единицы могут возникать вибрации на многих частотах, которые и используются для качественной оценки или определения их технического состояния.
Спектры вибрации коробки передач трактора К-701 без дефектов были сняты на обкаточном стенде, вначале, через 2 и 4 ч обкатки. Из спектрограмм видно, что вначале исчезают составляющие низких частот (первый этап обкатки), через 2 ч обкатки в спектре вибрации остаются в основном составляющие только колебаний ведущего вала КД. При дальнейшей обкатке начинают измениться и составляющие высоких частот спектра. Через 4 ч обкатки КП интенсивность вибрации уменьшается и стабилизируется. Дальнейшая обкатка КП, не имеющей дефектов, не приводит к существенным изменениям спектра вибрации. Исследованиями установлено, что время обкатки для большинства КП составляет 4 ч. Допускаемые значения, определяющие нормальную обкатку КП трактора К-701 без дефектов, составляют до 200 Гц — 20 дБ, в области высоких частот 0,2 ... 12 кГц до 70 дБ.
Дата добавления: 2021-04-24; просмотров: 108; Мы поможем в написании вашей работы! |
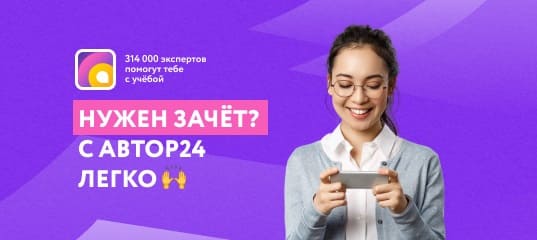
Мы поможем в написании ваших работ!