Средства автоматизированного диагностирования машин.
Разработанные высокоэффективные динамические методы диагностирования, электронные автоматизированные системы создали условия для решения проблемы диагностирования на принципиально новой индустриальной основе, то есть выполнении почти всех операций технического диагностирования блоками электронной установки с выдачей конечного результата о состоянии объекта в виде «годен», «не годен», «норма», «меньше нормы», «больше нормы», категории качества и т. п.
При этом процесс диагностирования машины осуществляется непрерывно по заданной оптимальной программе в определенной закономерной последовательности.
142
Рис. 6.5. Общий вид прибора ЭМДП:
1 — шкала; 2, 3 — переключатели марки двигателя и рода работы; 4, 5 — гнезда для подключения датчика вибрация и телефона; 6, 7, 8 — разъемы для подключения датчиков частоты вращения, подачи топлива, температуры; У — предохранитель
На основе закономерностей изменения текущей величины параметра от наработки с учетом допускаемых и предельных его значений устанавливают классификационные зоны, характеризующие качественные, энергетические или ресурсные показатели машин. Разделение классификационных зон осуществляется допускаемыми значениями параметров. Процесс диагностирования в этом случае заключается в определении области (зоны),
в которой находится диагностический параметр. Каждая зона возможного нахождения диагностического параметра ограничивается верхними и нижними допускаемыми значениями параметров.
|
|
В простейшем случае разделяется область работоспособного состояния механизма от области неработоспособного.
Допускаемые значения параметра определяют с учетом его изменения до следующего диагностирования, а также на основе зависимости диагностического параметра от структурного (см. гл. II).
Диагностические измерительные системы.Диагностическиеизмерительные системы представляют собой
143
Наиболее совершенные средства технического диагностирования машин. ДИС —это единый измерительный комплекс, позволяющий проводить формирование, статистическую обработку результатов измерения диагностических параметров, а также поддерживать заданный оптимальный режим работы агрегата.
Диагностическая измерительная прогнозирующая система (ДИПС КИ-13940) предназначена для диагностирования и определения остаточногоресурса тракторов, зерноуборочных комбайнов и оборудования животноводческих ферм. Число контролируемых или измеряемых Параметров до 400.
Структурная схема системы ДИПС приведена на рисунке 6.6. Первичные измерительные преобразователи ПИП (датчики) осуществляют преобразование диагностических параметров, представленных в виде неэлектрических величин, в электрический сигнал. В результате Все многообразие диагностических параметров сводится к конечному набору электрических сигналов (напряжения постоянного и переменного тока, частоты, временного интервала, сопротивления). Датчики устанавливают на объект диагностирования и с помощью индивидуальных кабелей подключают к блоку связи, размещенному непосредственно у объекта.
|
|
Блок связи БС осуществляет нормирование,согласование икоммутацию сигналов датчиков.
Фазовый селектор предназначен для формирования импульсов сдлительностью, равной заданной доле периода следования. В цифровом преобразователе предусмотрен режим, позволяющий проводить простейшую статистическую обработку сигнала (усреднение на 10 и 100 измерений). В системе используется магистральный принцип обмена цифровой информации между большинством функциональных блоков.
В системе ДИПС часть функций управления работой системы выполняется вручную оператором с помощью клавиатуры, расположенной на пульте управления (ПУ). Кроме того, часть клавиатуры пульта ПУ дублируется на выносном пульте.
|
|
С помощью центрального пульта управления ПУ оператор задает род и вид работы системы, тип измерений, параметры статистической обработки измеряемого сигнала, режим запуска, формирует команды, следит за состоянием режима объекта, контролирует функцио-
144
Рис. 6.6. Структурная схема системы ДИПС
145
Рис. 6.7. Общий вид электронной диагностической установки КИ-13940:
1 — цифропечатная машина; 2 — блок связи; 3 — пульт управления; 4 — переносной пульт управления; 5 — блок программирования; 6 — измерительная стойка
нирование системы и выполняет диагностическую часть программы, заданную технологической картой, которая определяет последовательность измерений параметров.
Блок управления БУ выполняет автоматическую тактовую частьпрограммы работы системы, определяющую последовательность выполнения управляющих, измерительных и обрабатываемых операций.
Кроме того, блок управления снабжен самостоятельным постоянным запоминающим устройством ПЗУ, позволяющим оперативно переводитьсистему в режим контроля состояния режима объекта. В системе предусмотрены два вспомогательных рода работы — контроль и запись тактовой программы. Серийный образец ДИПС (КИ-13940) показан на рисунке 6.7.
|
|
Диагностическая система ДИПС является универсальной автоматизированной установкой, предназначенной для диагностирования тракторов и сложных сель-
146
скохозяйственных машин, и вполне применима для диагностирования оборудования животноводческих ферм, комплексов и другой сельскохозяйственной техники.
Автоматизированный машинотестер (АМТ К И-13950-ГОСНИТИ) предназначен для автоматизированного диагностирования тракторов, зерноуборочных комбайнов и кормоуборочных машин на станциях ТО машин, ремонтных предприятиях, пунктах технического обслуживания тракторов и сельскохозяйственной техники колхозов, совхозов, производственных сельскохозяйственных объединений как в стационарных, так и в полевых условиях (передвижное использование АМТ) в целях определения технического состояния машин, поиска неисправностей, их устранения, определения потребностей агрегатов и машин в ремонте, оценки качества выпускаемой или отремонтированной машины. Возможно применение для диагностирования грузовых автомобилей и автобусов с дизельными двигателями. Конструктивно АМТ состоит из измерительно-вычислительного комплекса К539: блока связи 1, системного контроллера, терминала 2, датчиков с кабелями 3 и переходных устройств (рис. 6.8). Функциональная схема К539 представлена на рисунке 6.9. Из 23 входов блока связи (БС) 9 предназначены для тензодатчиков давления, 4 — для вибропреобразователей, 4 — температурных входа, 3 - для датчиков постоянного и переменного напряжения, 2— для датчиков частот вращения (ОВИ1) и углового ускорения (ОВИ2), 1 — для датчика расхода топлива.
Электроизмерительная часть АМТ выполнена на основе микропроцессорного набора и дисплея с размером экрана по диагонали 23 см. Имеющиеся 63 программы машинотестера служат для измерения 12 физических величин, с дополнительной приставкой, включающей фильтр нижних частот, — до 20 величин, включая индикаторные параметры рабочего процесса в цилиндрах двигателя внутреннего сгорания.
На дисплей 2 выводятся цифробуквенная информация о наименовании объекта, результат измеренного параметра и его сравнение с допускаемыми значениями. Графики диагностических параметров по времени, частоте вращения или углу поворота коленчатого вала выводятся на дисплей совместно с линиями границ изменения параметра. На дисплее регистрируются ско-
147
Рис. 6.8. Общий вид установки КИ-13950:
1 — блок связи; 2 — терминал с дисплеем; 3 — кабель
ростной и тепловой режимы ДВС, высвечивается краткая технологическая информация, приводятся результаты сравнения параметра с допускаемым значением и показатель вариации амплитуды вибросигнала.
Управление измерением диагностических параметров осуществляется оператором при помощи клавиатуры, расположенной на лицевой панели, терминала (рис. 6.8), путем выбора типа машины и номера параметра. Всего можно измерить 63 параметра агрегатов трактора и зерноуборочного комбайна. В отличие от установки КИ-13940 АМТ имеет более широкие функциональные возможности:
измерение большой группы статистических и динамических параметров с регистрацией их результатов на цифровом индикаторе;
графическое отображение на дисплее сложных динамических процессов: ускорения разгона, выбега, вибраций, рабочего процесса в цилиндрах двигателя внутреннего сгорания, топливопроводах, гидросистемах, смазочной системе и др.;
на дисплей терминала выводится служебная информация о марке диагностируемой машины, наименование
148
Рис. 6,9. Функциональная схема (КИ-13950} автоматизированного машинотестера:
ВС —блок связи; СВОС —схема выделения опорного сигнала; МПР — мультиплексор;
ХРМ —хрономер; АЦП—аналого-цифровой преобразователь: КСГ — контролерсигнализации МТ; БС— магистраль блока связи; АБС — адаптер блока связи; СГВ — сигнализатор выносной; КТ — контроллер; КЛ — клавиатура; ДПЛ — дисплей; ТМ – терминал; ИП — измерительные преобразователи; ОВИ1 — датчик частоты вращения; ОВИ2 —датчики ускорения; ПСИ —преобразователь синхроимпульса
и номер контролируемого параметра, результат измерения и сравнения его с нормативными значениями (больше, меньше, норма).
АМТ позволяет не только измерять диагностические параметры, но и анализировать рабочие процессы и осуществлять различные сложные операции по восстановлению работоспособности агрегатов машин.
Пример 1. По анализу вибрационного процесса молотильногобарабана зерноуборочного комбайна устанавливается не только величина дисбаланса, но осуществляется балансировка до заданных параметров (рис. 6.10).
2. По индикаторной диаграмме рабочего процесса, выведенного на дисплей, осуществляются измерение энергетических параметров, оценка жесткости и характера протекания рабочего процесса в цилиндрах двигате-
149
Рис. 6.10. Диаграмма вибрационного процесса молотильного барабана комбайна «Дон-1500» на экране дисплея машинотестера КИ-13950:
А(ω)D—кривая изменения амплитуды вибрации панели молотильного барабана принеуравновешенном состоянии
ля, технического состояния топливоподающей системы, цилиндропоршневой группы, газораспределения и ряда регулировочных параметров.
Экономический эффект от применения АМТ достигается благодаря внедрению микропроцессорной техники и реализации новых методических методов диагностирования и выражается в следующем:
снижена масса устройства электронной части — К-539 до 65 кг по сравнению с 400 кг К-736 (электронная часть ДИПС);
повышена наработка на отказ до 5000 ч по сравнению с 2000 ч К-736;
снижено энергопотребление с 800 до 250 Вт;
снижена трудоемкость диагностирования трактора с 5 до 3 ч;
увеличено число диагностируемых машин.
и Технология диагностирования тракторов и сложных сельскохозяйственных машин
Технология диагностирования тракторов и сложных сельскохозяйственных машин определяется задачей, назначением и местом технического диагностирования.
На заводе-изготовителе диагностированием контролируют качествоагрегатов и машины в целом, опреде-
150
ляют качество сборки, обкатки агрегатов, соответствие показателей работы машины, основных и регулировочных параметров техническим требованиям. Контроль обычно осуществляют по обобщенным параметрам технического состояния, например по двигателю измеряют мощность, удельный расход топлива, общий уровень вибрации и др., а также по качественным признакам состояния.
На ремонтном предприятии диагностированием предварительноопределяют ресурсные параметры агрегатов и узлов с целью установления объема ремонтных операций. Это относится к сопряжениям гильза — поршень, подшипник-шейка коленчатого вала и т. п.
После проведения ремонта диагностированием оценивают его качество. При этом обычно контролируют параметры и качественные признаки состояния, что и на заводах-изготовителях после сборки и обкатки машин. Отличительные особенности при этом заключаются в том, что на ремонтном предприятии при диагностировании применяют в основном менее жесткие допускаемые значения параметров, чем на заводе-изготовителе.
При эксплуатации машин сельскохозяйственных механизатор восновном контролирует ее состояние по встроенным приборам: манометрам и термометрам для определения давления и температуры масла и охлаждающей жидкости, тахометру для контроля частоты вращения деталей.
в последнее время в машинах все большее распространение получают сигнализаторы для визуальной, а в некоторых случаях и для звуковой оценки технического состояния агрегатов машин и их технологической регулировки. Загорание красной лампочки (визуального сигнализатора), например, свидетельствует о низком давлении масла в главной масляной магистрали двигателя, недопустимом увеличении температуры масла, охлаждающей жидкости; появление в прозрачной части устройства для контроля воздухоочистителя на поплавке красной полосы свидетельствует о загрязненности воздушного фильтра; исчезновение уровня масла или топлива в прозрачных «глазках» или трубках свидетельствует о недопустимом понижении уровня рабочей жидкости.
Наряду с оценкой состояния по встроенным приборам и сигнализаторам механизатор в процессе работы обращает внимание на качественные признаки техничес-
151
кого состояния машины: появление постороннего шума, чрезмерной, вибрации, течи масла, охлаждающей жидкости, специфического запаха, изменение цвета отработавших газов и т. п.
При техническом обслуживании в хозяйствах диагностированиемопределяют функциональные и выходные параметры технического состояния машины. Чем сложнее ТО, тем больше контролируют параметров и качественных признаков состояния машины. При небольшом числе машин в хозяйстве, например тракторов менее 30 ед., при ТО-3 вызывают передвижную диагностическую установку или отправляют трактор на СТОТ,
ее особенности если у него обнаруживают серьезную неисправность. При этом в технологии диагностирования применяют менее жесткие допускаемые значения параметров, чем на ремонтном предприятии.
При техническом обслуживании машин на СТОТ или СТОА практически контролируют при определенном виде ТО такие же параметры и качественные признаки, что и в хозяйстве. Отличие заключается в том, что СТОТ или СТОА применяют более производительные и точные средства диагностирования: стенды для определения тяговых, тормозных ходовых качеств, автоматизированные системы диагностирования и т. п.
При хранении диагностированием в основном контролируютнебольшое число параметров, характеризующих качество хранения: отсутствие коррозии рабочих и окрашенных поверхностей, герметичность агрегатов, плотность электролита.
качестве базовых диагностических средств необходимо применять
малогабаритные электронные диагностические приборы, автоматизированные установки и системы, мотор-тестеры, машинотестеры, выполненные на единых базовых элементах и общих принципах измерения диагностических параметров.
Последовательность и взаимосвязь технологий диагностирования машин на всех этапах осуществляются на единых принципах технологических процессов с учетом использования предшествующих результатов диагностирования (рис. 6.11).
Технология диагностирования состоит из трех частей. Первая часть включает подготовительные операции: очистка, мойка, установка машины на пост диагностирования, снятие защитных щитков, подготовка диагно-
152
стических средств к работе, внешний осмотр и занесение его результатов в контрольно-диагностическую карту, монтаж переходных устройств и измерительных преобразователей на составные части машины.
Вторая часть — непосредственно операции диагностирования машины: обязательное диагностирование по обобщенным базовым параметрам и дополнительное диагностирование—по потребности, в зависимости
отрезультатов обязательного диагностирования. Технология диагностирования должна строиться в определенной последовательности, обоснованной определенными критериями.
Обычно применяют критерий
(6.1)
где Р i , B i — вероятность неисправности и стоимость диагностирования 1-го элемента.
Продолжительность обязательного диагностирования машины можно представить в виде
где t P—средняя продолжительность разогрева тракторного или комбайнового дизеля до
номинального теплового состояния, ч; — оперативная продолжительность выполнения i-х операций обязательного процесса диагностирования подготовительных, заключительных и основных операций измерения параметров), ч.
Производственная проверка технологии диагностирования тракторов автоматизированными установками показала, что на присоединение и отсоединение датчиков и переходных устройств из-за низкой приспособленности тракторов затрачивается до 80% общего времени диагностирования машины. На установление режима диагностирования объекта и непосредственное измерение диагностических параметров затрачивается 10...15%. На фиксацию результатов и прогнозирование остаточного ресурса — 5...6%. Большая доля затрат времени уходит на подготовительно-заключительные операции, включающие снятие и установку боковин капота, очистку поверхностей на блоках агрегатов для установки датчиков — до 25%. Из приведенных данных видно, что рам процесс диагностирования занимает 15...20% от об-
153
Рис. 6.11. Общая схема технологии диагностирования тракторов и сложных сельскохозяйственных машин ДИПС:
ПУ—переходные устройства; ИП —измерительные преобразователи; ДМ—динамический метод по параметрам разгона; ВМ— вибрационный метод; ЭМ — электрический метод; ИМ — индуктивный метод; МРГ — метод измерения расхода газа; МЭМ —магнитоэлектрический метод; МДС —метод измерения датчиком силы; ТМ —температурный метод; МП — метод перемещений; ВО — визуальный осмотр; К.П — коробка передач; РУ — рулевое управление; НО — навесные орудия
щего времени. В этой связи следует больше внимания уделять вопросам взаимной приспособленности машин и диагностических средств, а также организационным вопросам работы слесаря и мастера-диагноста.
При диагностировании машины автоматизированными диагностическими средствами заняты два специалиста— оператор и мастер-Диагност. Для уменьшения времени диагностирования необходимо обеспечить равномерную загрузку их в процессе диагностирования путем правильного распределения обязанностей. Необходимым условием является высокая квалификация мастера-диагноста и оператора.
Начав работу вместе, каждый из них выполняет строго определенную часть операций. Включив систему в сеть, оператор проводит внешний осмотр
2. с помощью выносного пульта управления фиксирует результаты осмотра в карте диагностирования, а также устанавливает часть датчиков. Мастер-диагност также устанавливает в это время переходные устройства и датчики.
154
Важное значение имеет оптимальный маршрут специалистов. Например, установка переходных устройств и датчиков с одновременным внешним осмотром проводится, начиная с левой стороны трактора, заканчивается —с правой, что снижает потери времени.
Закончив внешний осмотр трактора, установив переходные устройства
* датчики, оператор занимает свое рабочее место у пульта управления системой, а мастер-диагност — в кабине трактора.
период разогрева двигателя возможно одновременное выполнение ряда диагностических операций: выявление качественных признаков состояния диагностируемого трактора (например, работоспособность контрольно-измерительных приборов, течи масла, охлаждающей жидкости, топлива, операции проверки состояния пневмосистемы и т. д.).
*** Оптимизаций взаимной приспособленности диагностических средств и сельскохозяйственной техники
Ряд эффективных методов, реализованных в диагностических приборах, автоматизированных установках, машинотестерах, не представляется возможным применить на практике без предварительных мер по улучшению приспособленности как диагностических средств, так и сельскохозяйственной техники.
Монтаж и демонтаж датчиков на неприспособленную машину связаны с большой трудоемкостью и снижением достоверности диагностирования.
Улучшение приспособленности машин к базовым диагностическим средствам снижает трудоемкость установки датчиков на объект, уменьшает количество переходных устройств, повышает эффективность диагностирования.
Имеется два основных направления повышения приспособленности к диагностированию за счет конструктивного изменения сельскохозяйственной машины и внешних средств диагностирования.
В первому направлению можно отнести улучшение доступности выполнения работы на машине (появление в конструкции машины лючков, присоединительных, унифицированных для датчиков мест, применение встроенных датчиков, указателей, сигнализаторов, показыва-
155
ющих приборов, наконец, бортовой системы диагностирования).
Естественно, что это увеличивает в определенной мере стоимость машины.
Ко второму направлению относится применение накладных, а не встраиваемых в машину при диагностировании датчиков, реализация новых,
А том числе динамических методов диагностирования, электронизация и компьютеризация диагностических средств и др. Это, в свою очередь, сопряжено с увеличением стоимости диагностических средств.
Общий подход к оптимизации приспособленности диагностических средств и сельскохозяйственной техники сводится к следующему:
отбирают все возможные прогрессивные варианты улучшения конструкции сельскохозяйственных машин и внешних средств диагностирования. При этом должны учитываться варианты закупки отдельных узлов с.-х. техники и средств диагностирования, обеспечивающие улучшение приспособленности к этому процессу за рубежом, организации собственного производства на основе приобретения лицензий, организации совместного производства с зарубежными странами и др.;
по каждому варианту из числа потенциально возможных определяют затраты на изменение конструкции, результаты этого изменения и его экономический эффект при эксплуатации;
устанавливают лучший вариант, у которого экономический эффект максимален, либо — при одинаковых результатах — затраты на достижение результата минимальны.
Экономический эффект от повышения приспособленности к диагностированию рассчитывают по формуле
Эт=Рт —Зт, | (6.2) |
где Эт — экономический эффект от повышения приспособленности к диагностированию за расчетный период, руб.; Рг — стоимостная оценка результатов улучшения приспособленности к диагностированию за расчетный период при реализации определенного варианта, руб.; Зт — затраты, потребные на повышение приспособленности за тот же период при реализации того же варианта, руб.
Расчет экономического эффекта проводят е использованием приведения разновременных затрат к единому расчетному году путем умножения величины затрат за каждый год на коэффициент приведения αt.
156
Стоимостную оценку результатов улучшения приспособленности к диагностированию за расчетный период устанавливают по формуле
(6.3)
где Pt — стоимостная оценка результатов в t-м году расчетного периода; t H , t K — начальный и конечный, года расчетного периода.
Затраты, потребные на повышение приспособленности к диагностированию за расчетный период по определенному варианту, подсчитывают по формуле
(6.4)
где Зтп — затраты при производстве сельскохозяйственной машины или внешнего диагностического средства на улучшение приспособленности к диагностированию, руб.; Зтн—затраты при эксплуатации сельскохозяйственной машины или внешнего средства диагностирования с улучшенной приспособленностью, руб.
А качестве примера рассмотрим один из вариантов повышения контролепригодности трактора путем его оборудования сигнализатором навесного механизма.
Экономический эффект от внедрения сигнализатора обусловливается увеличением срока работы гидроагрегатов в связи с уменьшением попадания абразивных частиц в масло.
Гидроагрегаты работают на маслах, степень загрязнения которых приводит к снижению ресурса в 2 раза (4 тыс. вместо 8 тыс. моточасов).
Во время работы трактора масло дополнительно ускоренно загрязняется из-за работы при недостаточном его уровне в баке, негерметичности гидропривода и т. д. Это приводит к тому, что коэффициент охвата капитальным ремонтом гидроагрегатов трактора составляет 0,25. При существующем (базовом) варианте сигнализатор отсутствует.
Применение сигнализатора уровня масла позволяет уменьшить коэффициент охвата капитальным ремонтом гидроагрегата до 0,15.
Стоимостная оценка результатов улучшения приспособленности к диагностированию в расчетном периоде
(6.5)
157
Дата добавления: 2021-04-24; просмотров: 426; Мы поможем в написании вашей работы! |
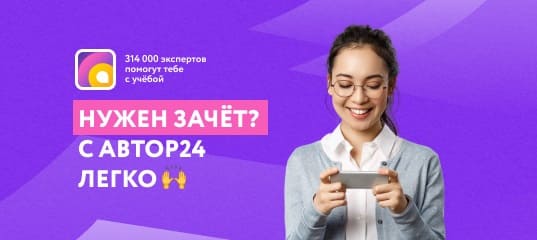
Мы поможем в написании ваших работ!