Структура сварного соединения 3 страница
Wa = Ua¢= Ua + (j + 2кТ); Wк = Uк¢= Uк − (j + 2кТ),
(1.12)
где Ua, Uк — соответственно анодное и катодное падение напряжений; j, кТ — соответственно потенциальная и термическая энергия электронов.
При сварке на переменном токе количество теплоты, выделяющейся на электроде и свариваемом изделии, одинаково, т. е. Wa = Wк.
На катоде не вся энергия Uк переходит в теплоту, часть ее (j + 2кТ) переносится в плазму столба дуги. На аноде выделяется энергия Ua и прибавляется потенциальная и термическая энергия электронов. Количество теплоты, выделенное на катоде, зависит от потенциала ионизации дугового промежутка. Разница в тепловыделении на катоде и аноде определяется способом дуговой сварки. В реальных условиях при сварке на прямой полярности (анод на детали) глубина проплавления оказывается меньшей, чем при сварке на обратной полярности (катод на изделии).
Угол наклона электрода . При ручной сварке покрытыми электродами, изменяя наклон электрода в плоскости продольной оси шва, можно существенно влиять на размеры сварочной ванны и шва. При a < 90° сварку выполняют углом вперед. Давление дуги вытесняет расплавленный металл в головную часть ванны. При этом глубина проплавления основного металла уменьшается. При a > 90° сварку выполняют углом назад. Давление дуги способствует интенсивному вытеснению расплавленного металла из головной части ванны в хвостовую. Глубина проплавления увеличивается.
|
|
Колебание электрода . При поперечных колебаниях электрода увеличивается ширина шва и уменьшается глубина проплавления. Изменяются условия кристаллизации и тепловой цикл в зоне термического влияния. Колебания электрода в процессе сварки обычно осуществляют с частотой 10…60 колебаний в 1 мин с амплитудой 2…4 мм.
Сжатие столба дуги . При сварке сжатой дугой появляется новый дополнительный параметр режима сварки — степень сжатия дуги. С увеличением степени сжатия дуги возрастает температура плазмы дуги, повышается концентрация теплоты в пятне нагрева, увеличивается глубина проплавления и уменьшается ширина сварочной ванны и шва.
Импульсная подача тока . При импульсном горении дуги появляются два новых дополнительных параметра процесса: время импульса tи и время паузы tп. Тепловая энергия подводится только во время импульса. Оба этих параметра оказывают влияние на размеры сварочной ванны и шва. При неизменной погонной энергии в течение цикла tц = tи + tп увеличение времени паузы ужесточает режим. Значительно возрастает термический КПД процесса. Благодаря этому до определенных значений времени импульса увеличивается глубина проплавления основного металла и уменьшается ширина шва.
|
|
1.5Плавление и перенос электродного материала
При дуговой сварке нагрев и расплавление электрода осуществляются за счет энергии, выделяемой дугой в активном пятне, расположенном на его торце. Вылет электрода нагревается за счет теплоты, выделяемой при прохождении по нему тока.
Вылет — участок электрода от места контакта с токоподводящим устройством до его конца.
Например, при сварке вручную вылет электрода в начале сварки составляет 200…400 мм, в конце — 30…40 мм. Количество теплоты, выделяемой в электроде в единицу времени, тем больше, чем больше плотность тока, удельное сопротивление и вылет электрода. Качество шва будет обеспечено только тогда, когда температура электрода в момент расплавления его торца не будет превышать определенной температуры, например 600…700°С при сварке стальными электродами. Нагрев электрода до более высоких температур приводит к отслаиванию покрытия, ухудшению формирования шва и увеличению потерь на разбрызгивание.
|
|
Основная характеристика плавления электрода — линейная скорость его расплавления в единицу времени, которая зависит от состава электрода, вида покрытия, режима сварки, плотности и полярности тока. В общем случае скорость плавления электрода возрастает с увеличением силы тока примерно по линейной зависимости.
При плавлении на торце электрода образуется капля жидкого металла. Характер переноса электродного металла зависит от соотношения сил, действующих на каплю металла на торце электрода. К основным силам относят силу тяжести, силу поверхностного натяжения, электромагнитную силу, силу реактивного давления паров, аэродинамическую силу и др. Значения отдельных сил и направление их равнодействующих зависят от режима сварки, полярности тока, состава электродного металла, газовой среды, состояния поверхности и диаметра электрода.
|
|
Сила тяжести оказывает существенное влияние лишь при сварке на малых токах (стремление капли под действием собственной силы тяжести переместиться вниз). Сила поверхностного натяжения проявляется в стремлении жидкости под действием молекулярных сил приобрести сферическую форму, имеющую минимальную площадь поверхности при данном объеме. В общем случае увеличение поверхностного натяжения способствует увеличению размеров капель, образующихся на торце электрода и переносимых через дуговой промежуток.
Электромагнитная сила обусловлена взаимодействием проводника с током и магнитного поля, создаваемого этим током. Эта сила стремится деформировать проводник в радиальном направлении и разрушить перемычку между каплей и электродом. Ее значение пропорционально квадрату силы тока.
Испарение металла с поверхности капли и химическое взаимодействие жидкого металла со шлаком или газовой фазой, сопровождаемое образованием и выделением газа, приводят к возникновению реактивных сил. Металл испаряется в области активных пятен, перемещение которых вызывает изменение положения места приложения реактивных сил и значительную подвижность капель. Величина реактивных сил зависит от размеров активных пятен, плотности тока в них и теплофизических свойств материала электрода. В металлах с высоким давлением паров (магний, цинк) отталкивание капель реактивными силами наблюдается при сварке на обеих полярностях, а в металлах с низким давлением паров — главным образом при сварке на прямой полярности.
Сила аэродинамического торможения пропорциональна плотности газа, его скорости и эффективной площади сечения капли, спроектированной на направление газового потока.
При сварке покрытыми электродами наблюдается в основном крупнокапельный и мелкокапельный перенос (рис. 1.9, а). Тип переноса зависит от состава, толщины и вида покрытия, режима сварки, рода тока и полярности.
Рис. 1.9.Схемы процессов переноса электродного металла в сварочную ванну:
а — капельный; б — струйный; I—IV — этапы процесса переноса капли
При малом напряжении (короткая дуга) перенос металла может осуществляться путем коротких замыканий, поскольку свободный рост капель затруднен. В момент коротких замыканий металл перетекает с торца электрода в ванну. С удлинением дуги масса переносимых капель увеличивается, так как создаются условия для свободного роста капли на торце электрода.
При струйном переносе (рис. 1.9, б) образуются мелкие капли, которые следуют одна за другой в виде непрерывной цепочки (струи). Струйный перенос электродного металла возникает при сварке с большой плотностью тока электродом малого диаметра. Обычно струйный перенос электродного металла приводит к меньшему выгоранию легирующих элементов в сварочной проволоке и повышению чистоты металла капель и сварного шва. Скорость расплавления сварочной проволоки увеличивается, поэтому струйный перенос имеет преимущества перед капельным переносом.
1.6Плавление основного металла
Процесс распространения теплоты в металле зависит от ряда факторов: эффективной тепловой мощности дуги, характера ее перемещения, размера и формы свариваемого изделия, теплофизических свойств материала. Влияние этих факторов на нагрев изделия можно оценить по изменению формы изотерм температурного поля (рис. 1.10). С увеличением тока (мощности) дуги области металла, нагретые до определенных температур, расширяются, а увеличение скорости перемещения дуги приводит к сужению этих областей в направлении, перпендикулярном оси шва, и сгущению изотерм перед дугой. Форма сварочной ванны при дуговых процессах характеризуется длиной, шириной и глубиной проплавления основного металла (рис. 1.11). Объем сварочной ванны в зависимости от способа и режима сварки изменяется от 0,1 до 10 см3. Время нахождения металла в жидком состоянии в различных ее участках неодинаково. Приближенно среднюю продолжительность существования сварочной ванны tср, с, можно рассчитать с помощью соотношения
tср = Lв/vср,
(1.13)
где Lв — длина ванны, мм; vcp — скорость перемещения источника нагрева, мм/с.
Рис. 1.10.Влияние силы тока на положение изотерм:
а, б, в — соответственно при силе тока дуги 200, 300 и 400 А; х — ширина температурного поля Рис. 1.11.Параметры формы сварочной ванны:
Lв — длина ванны; В — ширина шва; h — разность уровней расплавленного металла в ванне под действием давления дуги; Н — глубина проплавления основного металла
В головной части ванны под воздействием источника теплоты металл нагрет значительно выше температуры его плавления, а в хвостовой части ванны температура приближается к температуре плавления основного металла.
Важным фактором, влияющим на геометрические параметры ванны, является пространственное положение выполняемых швов (рис. 1.12). При сварке в вертикальном положении (рис. 1.12, а) снизу вверх (на подъем) глубина проплавления резко возрастает, при сварке на спуск — уменьшается. При сварке в потолочном положении (рис. 1.12, в) необходимо ограничение объема ванны. Наиболее неблагоприятные условия формирования ванны создаются при выполнении горизонтальных швов (рис. 1.12, г).
Рис. 1.12.Формы сварочной ванны в зависимости от условий формирования шва при его положении в пространстве:
а — вертикальное (слева — на подъем; справа — на спуск); б — наклонное; в — потолочное; г — горизонтальное; vсв — скорость сварки; Рв — гидростатическое давление (вертикально вниз)
Структура сварного соединения
Сварные соединения, выполненные сваркой плавлением, состоят из трех зон (рис. 1.13): литого металла сварного шва в той части соединения, где существовала расплавленная ванна жидкого металла; основного металла, подвергшегося тепловому влиянию сварки, называемого зоной термического влияния, или околошовной зоной; основного металла, не испытавшего такого влияния. Условную поверхность раздела между металлом сварного шва и околошовной зоны называют границей сплавления.
Рис. 1.13.Основные структурные зоны в поперечном сечении сварного соединения:
1 — металл сварного шва; 2 — граница сплавления; 3 — металл в зоне термического влияния; 4 — основной металл
Структура основного металла определяется технологической обработкой заготовок перед сваркой. Детали могут быть изготовлены в виде листа из деформированного металла в состоянии нагартовки, отпуска или рекристаллизации; из отливок или поковок с литой и деформированной структурой.
Теплота, выделяемая при сварке, распространяется в основной металл. Чем ближе эта точка расположена к границе сплавления, тем быстрее в ней происходит нагрев металла и тем выше максимальная температура нагрева, поэтому структура и свойства основного металла в различных участках зоны термического влияния различны. Основной металл (нагартованный или после отжига на снятие напряжений) претерпевает в этой зоне возврат и рекристаллизацию. Степень развития этих превращений в каждом слое зоны зависит от максимальной температуры нагрева слоя, длительности нахождения выше температуры фазового превращения, скорости нагрева и охлаждения.
Жидкий металл сварочной ванны затвердевает в особой форме, какой являются оплавленные кромки основного металла. Кромки основного металла одновременно служат подложкой для затвердевающего металла. Переход жидкого металла в твердое состояние с кристаллическим строением называют кристаллизацией. Образующиеся при затвердевании кристаллы металла принято называть кристаллитами.
В центре сварных швов часто появляется зона равноосных кристаллитов в результате переохлаждения центральной части сварочной ванны. Кристаллиты этой зоны вследствие независимого зарождения ориентированы хаотично. В общем случае металл сварного шва состоит из сильно разориентированных кристаллитов. Чем больше кривизна поверхности сварочной ванны и меньше ее размеры, тем более разориентированы соседние кристаллиты в шве.
Чем больше скорость охлаждения, тем более вероятны зарождение и рост свободных кристаллитов с хаотической ориентацией и соответственно у́же зона и меньше размер столбчатых кристаллитов.
Металл зоны термического влияния химически более однороден, чем литой металл шва. Основной вид химической неоднородности в металле околошовной зоны — накопление примесей или легирующих добавок по границам зерен.
Низкоуглеродистые стали (содержание углерода — до 0,25 мас.%) обладают полиморфизмом (рис. 1.14). В исходном состоянии сталь представляет собой смесь зерен феррита (a-железо) с кристаллической решеткой в виде объемно-центрированного куба и перлита (смесь, состоящая из кристаллов a-железа и цементита Fe3C). При нагреве стали выше 723°С (обозначение этой температуры при нагреве А r1; при охлаждении — А с1) начинается превращение этой смеси в аустенит (раствор углерода в g-железе, имеющем решетку в виде гранецентрированного куба). При температурах А r2 (А с2) (примерно при 880°С) процесс заканчивается, т. е. структура стали становится полностью аустенитной. При нагреве выше 1100°С аустенитное зерно интенсивно растет, и сталь, нагретая выше этой температуры, имеет структуру перегрева.
Рис. 1.14.Структура (а) низкоуглеродистой стали в зоне сварного соединения в соответствии с диаграммой (б) состояния железо—углерод:
tmax — кривая максимальных температур нагрева стали в направлении, поперечном ведению сварки; х — расстояние от оси шва по горизонтали; Ж — расплавленный (жидкий) металл; А — аустенит (твердый раствор); Ц — цементит; Ф — феррит; П — перлит; АЕ, ES, SG, GP, PQ — линии растворимости углерода в железе
При сварке низкоуглеродистой стали в околошовной зоне, нагреваемой от температуры окружающей среды до температуры плавления, формируется (в соответствии с диаграммой состояния железо—углерод) набор структурных зон.
Участок неполного расплавления примыкает непосредственно к сварному шву и является переходным от литого металла шва к основному. Он представляет собой узкую (0,1…0,4 мм) область основного металла на границе сплавления, нагреваемую до частичного оплавления границ зерен.
Участок перегрева — область основного металла, где максимальные температуры при нагреве были выше 1100°С, а после охлаждения на базе крупнозернистого аустенита образовалась крупнозернистая ферритно-перлитная (или даже мартенситная) структура с пониженными механическими свойствами (низкая пластичность).
Участок нормализации соответствует нагреву в аустенитную область до температур 900…1100°С и перекристаллизации при охлаждении ниже Ac1 в мелкозернистую ферритно-перлитную структуру. Металл участка нормализации обладает высокими механическими свойствами, так как фазовое превращение проходит на базе мелкозернистого аустенита, не подвергшегося перегреву.
Участок неполной перекристаллизации нагревается в пределах 723…900°С. В связи с недостаточной длительностью и температурой нагрева структура металла состоит из смеси мелких перекристаллизовавшихся зерен и крупных зерен феррита и перлита, которые не успели перекристаллизоваться. Свойства металла этого участка более низкие, чем участка нормализации.
Участок рекристаллизации наблюдается при сварке сталей, подвергавшихся пластической деформации (прокатке, ковке, штамповке). При нагреве до 450…725°С в этой области основного металла развивается процесс рекристаллизации, приводящий к росту зерна, огрублению структуры и разупрочнению металла.
В участке, нагреваемом до 100…450°С, могут протекать процессы возврата и старения в связи с выпадением карбидов и нитридов железа. Результатом старения является снижение пластичности, вязкости и сопротивления хрупкому разрушению.
Дата добавления: 2021-04-24; просмотров: 104; Мы поможем в написании вашей работы! |
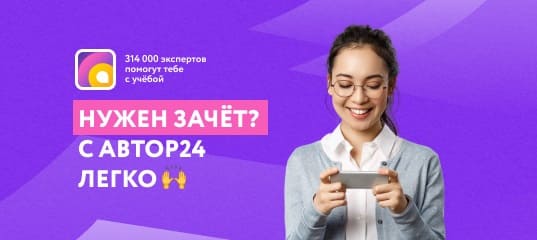
Мы поможем в написании ваших работ!