Пневматический рубильный молоток
Прямая ручная шлифовальная электрическая машина (рис. 7.10) имеет корпус 8 с вмонтированным асинхронным трехфазным электродвигателем 7 повышенной частоты, корпус 3 редуктора со шпинделем 4, рукоятку 10 и шлифовальный круг 1. Ротор электродвигателя вращается на двух шариковых подшипниках, один из которых установлен в задней, другой — в промежуточной крышке 5. На валу ротора установлен вентилятор 6 для охлаждения двигателя. Вращение от вала ротора передается шпинделю 4 через одноступенчатый цилиндрический редуктор, ведущее зубчатое колесо которого нарезано на валу, а ведомое — закреплено на шпинделе шпонкой. На выступающем конце шпинделя фланцами и гайками крепятся шлифовальный круг или стальная радиальная щетка, закрытые защитным кожухом 2. В рукоятке 10 смонтирован выключатель с курком 9 и закреплен токоподводящий кабель. Корпус 3 редуктора служит одновременно второй рабочей рукояткой.
Рис. 7.11. Угловая ручная шлифовальная электрическая машина:
1 — корпус редуктора; 2 — одноступенчатый редуктор с коническими зубчатыми колесами; 3 — корпус машины; 4 — асинхронный трехфазный электродвигатель повышенной частоты; 5 — рукоятка; 6 — курок выключателя; 7 — вентилятор; 8 — защитный кожух; 9 — шпиндель; 10 — шлифовальный круг
|
|
Рис. 7.10. Прямая ручная шлифовальная электрическая машина
Угловая ручная шлифовальная электрическая машина (рис. 7.11) аналогична по конструкции прямой машине и имеет корпус 3 с вмонтированным асинхронным трехфазным электродвигателем 4 повышенной частоты, корпус 1 редуктора со шпинделем 9, рукоятку 5 и шлифовальный круг 10. На валу ротора, вращающегося на двух шариковых подшипниках, установлен вентилятор 7 для охлаждения двигателя. Вращение от вала ротора передается шпинделю 9 через одноступенчатый редуктор 2 с коническими зубчатыми колесами. Ведущее колесо имеет шлицевое соединение с валом ротора, а ведомое — закреплено на шпинделе шпонкой. На выступающем конце шпинделя фланцем и гайками крепится шлифовальный круг, закрытый защитным кожухом 8. В рукоятке 5 смонтирован выключатель с курком 6 и закреплен токоподводящий кабель. Дополнительная рукоятка устанавливается с левой или правой стороны корпуса. Для подвешивания машины над рабочим местом имеется рым-болт..11. Угловая ручная шлифовальная электрическая машина
|
|
Фрезерный трактор. Фрезерный трактор (рис. 7.12) предназначен для снятия выпуклости сварных швов на листах и обечайках. Он перемещается по изделию с помощью электропривода, состоящего из электродвигателя, клиноременной передачи и червячного редуктора. Шпиндель с фрезерной головкой приводится во вращение электродвигателем через клиноременную передачу. Фрезерование осуществляется торцовой фрезой, головка которой имеет копировальное устройство, препятствующее врезанию фрезы в изделие.
Рис. 7.12.Фрезерный трактор
Оборудование для нанесения защитных покрытий
Для защиты поверхностей сварных изделий применяются покрытия на основе эмалей, лаков, масляных и синтетических красок.
Наиболее распространенным способом нанесения защитных покрытий сварных конструкций является пневматическое распыление. В комплект оборудования для пневматического распыления (рис. 7.13) входит краскораспылитель 5, красконагнетательныи бак 11 и масловлагоотделитель 9. Сжатый воздух из центральной пневмомагистрали или от компрессора поступает по шлангу 8 в масловлагоотделитель 9, где проходит очистку от паров воды и масла. Очищенный сжатый воздух по шлангу 6 подводится к краскораспылителю 5, а по шлангу 7 через редуктор давления 10 — в красконагнетательный бак 11, где с помощью мешалки 1 перемешивается лакокрасочный материал. Под давлением сжатого воздуха лакокрасочный материал по трубке 2 вытесняется из красконагнетательного бака и через кран 4 по шлангу 3 подается к краскораспылителю 5.
|
|
Рис. 7.13.Схема действия оборудования для пневматического распыления:
1 — мешалка; 2 — трубка; 3, 6, 7, 8 — шланги; 4 — кран; 5 — краскораспылитель; 9 — масловлагоотделитель; 10 — редуктор давления; 11 — красконагнетательный бак
При выходе из сопла краскораспылителя лакокрасочный материал встречает струю сжатого воздуха, раздробляется ею, захватывается и наносится на обрабатываемую поверхность.
При малых объемах работ применяют краскораспылители со съемными наливными бочками. Распыление может осуществляться вручную и автоматически. Автоматизация процесса окраски достигается применением различных средств передвижения краскораспылителей и окрашиваемого изделия.
|
|
Пневматическое распыление производится в специальных распылительных камерах, оборудованных мощной вентиляционной системой для отсоса лакокрасочного тумана и фильтрами для очистки удаляемого воздуха от пыли. Камеры подразделяют на тупиковые (применяемые в непоточном производстве) и проходные (используемые в поточных линиях).
Недостатками пневматического распыления являются значительные потери (20…40%) лакокрасочного материала из-за туманообразования и сложность конструкции распылительных камер. Поэтому наряду с пневматическим распылением для нанесения защитных покрытий на сварные изделия применяются безвоздушное распыление, распыление в электрическом поле высокого напряжения, электроосаждение, струйный облив. Сушка сварных изделий после нанесения защитных покрытий производится в сушильных камерах (тупиковых или проходных) конвективной или терморадиационной сушки.
Контрольные вопросы
1. Какое оборудование применяется для правки сварных конструкций?
2. Как устроены гидравлические правиґльные прессы и машина для устранения грибовидности сварных двутавровых балок?
3. Какое оборудование применяется для улучшения механических свойств сварных швов?
4. Как устроены станки для прокатки и проковки швов?
5. Какие ручные машины применяют для отделки сварных соединений?
6. Как устроены ручные пневматические и электрические шлифовальные машины?
7. Какие меры безопасности предусмотрены в конструкции ручных пневматических и электрических шлифовальных машин?
ГЛАВА8Подъемно-транспортное оборудование
· 8.1. Классификация
· 8.2. Универсальное оборудование общего применения
· 8.3. Специализированное оборудование
· 8.4. Грузозахватные приспособления
· 8.5. Конвейеры
· 8.6. Вспомогательные транспортные средс
8.1Классификация
Подъемно-транспортное оборудование в сборочно-сварочном производстве применяется на всех стадиях технологического цикла и является необходимым средством комплексной механизации производства и повышения производительности труда.
Подъемно-транспортное оборудование подразделяется на универсальное оборудование общего применения и специализированное. Специализированное оборудование предназначено не только для подъема и перемещения деталей и узлов, но и для установки их в определенном положении при сборке и сварке.
Универсальное подъемно-транспортное оборудование общего применения широко используется в индивидуальном и мелкосерийном производстве сварных конструкций. Однако оно недостаточно производительно, поэтому в серийном и массовом производстве наряду с ним широко применяются специальные транспортные средства, приспособленные для обслуживания определенных операций.
Различают внешний, межцеховой и внутрицеховой транспорт. Для внешнего и межцехового транспортирования служат, как правило, универсальные транспортные средства общего применения, для внутрицехового — универсальные и специализированные транспортные средства. В составе внутрицехового транспорта особенно важен межоперационный транспорт, назначение которого — передача изделий с одного рабочего места на другое в соответствии с технологическим процессом.
По принципу действия подъемно-транспортное оборудование можно подразделить на две основные группы: оборудование периодического действия (грузоподъемные машины) и непрерывного действия (транспортирующие машины и конвейеры).
8.2Универсальное оборудование общего применения
Основным универсальным оборудованием общего применения в сборочно-сварочном производстве являются электротали, краны, самоходные транспортные средства.
Электротали выпускаются грузоподъемностью 0,25; 0,5; 1; 2; 3,2; 5 т. Они передвигаются по монорельсу. Электротали грузоподъемностью 0,25 т имеют ручной привод передвижения, а грузоподъемностью 1 т и больше — электрический. Привод передвижения электротали грузоподъемностью 0,5 т может быть ручным или электрическим. Скорость передвижения стандартных электроталей составляет 20 м/мин, скорость подъема — 8 м/мин. Управление осуществляется с помощью подвесного пульта. В качестве монорельса используют двутавровые балки (от № 18 до № 45 в зависимости от грузоподъемности электротали). При необходимости монорельс может быть закругленным в горизонтальной плоскости. Электротали применяются для обслуживания сварочных участков, отдельных рабочих мест и поточных линий (в качестве межоперационного транспорта).
Краны, используемые в сварочном производстве, могут быть передвижными (мостовые, козловые, полукозловые, консольные) и стационарными поворотными.
Мостовые краны широко применяются при изготовлении сварных конструкций в единичном и мелкосерийном производстве. Наибольшее распространение получили электрические мостовые краны как универсальное подъемно-транспортное оборудование, обслуживающее почти всю площадь цехового пролета, не занимая при этом производственную площадь.
Мостовые краны подразделяют на двухбалочные и однобалочные. Все мостовые краны опираются четырьмя колесами на подкрановые пути, установленные на колоннах цеха, и передвигаются по ним вдоль всего пролета (у тяжелых кранов может быть от 8 до 16 колес). Двухбалочные мостовые краны имеют широкий диапазон грузоподъемности (3…320 т) и выпускаются с пролетом (колеей подкрановых путей) 10,5…32 м. Краны грузоподъемностью 15…20 т и более оборудуются двумя независимыми механизмами подъема — главным и вспомогательным. Грузоподъемность вспомогательного механизма в несколько раз меньше по сравнению с главным.
В однобалочных мостовых кранах вместо тележки применяются стандартные электротали. Грузоподъемность однобалочных кранов, как и электроталей, составляет 1…5 т. Однобалочные краны могут быть опорными, передвигающимися по подкрановым путям (как двухбалочные), и подвесными, передвигающимися по подвесному рельсовому пути.
Вдоль пролета, обслуживаемого опорным мостовым краном (рис. 8.1, а), остаются пространства вне зоны обслуживания (15…20% площади пролета) — «мертвые» зоны. У подвесных мостовых кранов (рис. 8.1, б) крайние положения крюка значительно ближе к границам пролета, и за счет этого увеличена зона обслуживания. С помощью подвесных кранов можно переносить грузы в соседний пролет путем состыковывания несущих балок подвесных кранов, расположенных в соседних пролетах.
Рис. 8.1.Схемы грузоподъемных кранов и обслуживаемых ими зон:
а — опорный мостовой; б — подвесной мостовой; в — козловый; г — полукозловый; д — консольный передвижной настенный; е — консольный передвижной велосипедный; ж — консольный стационарный поворотный, расположенный около стены; з — консольный стационарный поворотный, свободно стоящий в цехе
Козловые краны (рис. 8.1, в) отличаются от мостовых тем, что их мост опирается не на колеса, а на высокие опоры — ко́злы, установленные на ходовые тележки. Тележки передвигаются по рельсам, проложенным с обеих сторон вдоль зоны работы крана. Козловые краны применяются на складах металла и готовой продукции, расположенных на открытых площадках. Грузоподъемность козловых кранов достигает 32 т.
Полукозловые краны (рис. 8.1, г) передвигаются по двум рельсам, один из которых расположен на полу, второй — на стене цеха. Полукозловые краны используются для обслуживания отдельных участков на одной стороне пролета — между стеной и проходом.
Консольные передвижные краны перемещаются вдоль стен или колонн по двум рельсам, проложенным один под другим; нижний (опорный) рельс воспринимает основную нагрузку от веса крана и груза, а верхний рельс удерживает кран от опрокидывания. В настенных консольных передвижных кранах (рис. 8.1, д) оба рельса закреплены на колоннах. В велосипедных консольных передвижных кранах (рис. 8.1, е) нижний рельс располагается на полу, а верхний крепится к колоннам или верхней металлоконструкции цеха. Подъемным механизмом в консольных кранах обычно является электроталь грузоподъемностью до 3,2 т.
Консольные стационарные поворотные краны используются для обслуживания отдельных рабочих мест и передачи изделий с одного рабочего места на другое. Краны могут располагаться около стены (рис. 8.1, ж) или свободно стоять в цехе (рис. 8.1, з). Краны изготовляются в двух исполнениях: с переменным или постоянным вылетом стрелы. Переменный вылет обеспечивается наличием передвижного подъемного механизма (например, тали); у кранов с постоянным вылетом грузовой крюк расположен на конце консоли.
Стационарные поворотные краны выполняются со складывающейся стрелой, что позволяет увеличить зону обслуживания по сравнению с обычными поворотными кранами.
Самоходные транспортные средства (аккумуляторные электротележки, тягачи с прицепными тележками, электропогрузчики) широко применяются в сборочно-сварочном производстве для внутрицеховых перевозок. В единичном и мелкосерийном производстве их применяют для перевозки грузов до 5 т на всех стадиях технологического процесса — от склада металла до склада готовой продукции. В серийном и массовом производстве их используют для подачи заготовок к началу поточных линий и транспортирования готовых изделий от поточных линий на склад, а также для передачи изделий между участками, расположенными в разных пролетах одного цеха, и между цехами.
Для работы на складах с многоярусными стеллажами используются краны-штабелеры и электроштабелеры, обеспечивающие передачу грузов массой до 2 т между рабочими местами и стеллажами.
Для перемещения между пролетами грузов массой более 5 т используются рельсовые самоходные тележки грузоподъемностью до 120 т с электроприводом.
8.3Специализированное оборудование
Специализированные транспортные средства имеют то же назначение, что и универсальные, но изготовлены с учетом специфики сборочно-сварочного производства и используются в серийном и массовом производстве для установки деталей и узлов, т. е. выполняют функции монтажно-сборочного оборудования и оборудования для поворота изделий. К этим средствам относятся четырехкрюковый мостовой кран, самоходная портальная тележка и самоходная стапельная тележка с плунжерным гидродомкратом.
Четырехкрюковый мостовой кран (рис. 8.2, а) предназначен для подъема, перемещения и кантования крупногабаритных сварных конструкций (например, главных балок мостовых кранов). На тележке четырехкрюкового крана установлены два независимых механизма подъема, каждый из которых имеет по два канатных барабана. Изделие располагают на двух круглозвенных цепях, каждая из которых накинута на крюки, подвешенные к разным механизмам подъема (рис. 8.2, б). Для кантования изделие сначала немного приподнимают над стеллажом (рис. 8.2, в), затем один механизм подъема начинает работать на спуск, второй — на подъем (рис. 8.2, г) до тех пор, пока изделие не повернется на требуемый угол. После этого изделие опускают (рис. 8.2, д).
Рис. 8.2.Четырехкрюковый мостовой кран (а) и последовательность операций (б—д) при кантовании главной балки мостового крана:
1 — подкрановый путь; 2 — кантуемое изделие
Портальная тележка (рис. 8.3) используется для перемещения и установки листовых заготовок в горизонтальном положении при сборке. На портальной раме 5 с подъемной кареткой 4 смонтирована траверса 3 с электромагнитными захватами 2, закрепленными на пружинных подвесках. Тележка перемещается по рельсовому пути с помощью электромеханического привода 8. Каретка поднимается и опускается по вертикальным направляющим портальной рамы на 500 мм с помощью двух гидравлических цилиндров 7. Траверса установлена на катках и может перемещаться по каретке в поперечном направлении в пределах 500 мм. Гидроцилиндры портала приводятся в действие станцией гидропривода 6. Тележку подводят к складу листов, опускают каретку до соприкосновения захватов с транспортируемым листом 1 и включают электромагниты захватов, затем поднимают каретку, и тележка перемещается к месту сборки. Для более точной укладки лист перемещают с помощью передвижной траверсы поперек тележки, затем опускают каретку и отключают электромагниты. Тележка перевозит листы массой до 5 т со скоростью 60 м/мин.
Рис. 8.3.Портальная тележка для транспортирования листов в горизонтальном положении:
1 — транспортируемый лист; 2 — электромагнитные захваты; 3 — траверса; 4 — подъемная каретка; 5 — портальная рама; 6 — гидропривод цилиндров портала; 7 — гидравлические цилиндры; 8 — электромеханический привод
Самоходная стапельная тележка с плунжерным гидродомкратом (рис. 8.4) предназначена для перевозки и точной установки при сборке блоков судовых корпусов. Каждая тележка состоит из рамы 1, четырех колес 5 и плунжерных гидродомкратов 4. Гидродомкраты можно приводить в действие ручными насосами 2, а также гидронасосами с пневмоприводом. Тележка оснащена электроприводом 3. Грузоподъемность тележки 75…200 т, ход домкрата 200…300 мм, давление масла в гидродомкратах до 33 МПа.
Рис. 8.4.Самоходная стапельная тележка с плунжерным гидродомкратом:
1 — рама; 2 — ручной насос; 3 — электропривод; 4 — плунжерный гидравлический домкрат; 5 — колесо
8.4Грузозахватные приспособления
Применение грузозахватных приспособлений для строповки (захвата) и удержания грузов способствует повышению безопасности подъемно-транспортных операций. Стропальные операции связаны с определенным риском для рабочего, поэтому к грузозахватным приспособлениям предъявляются следующие требования: надежность, удобство и безопасность в работе; минимальное время захвата и освобождения груза; возможность замены ручного труда механизированным; минимальные собственный вес и размеры; простота конструкции и эксплуатации; низкая стоимость. Наиболее важным и безусловным является первое требование.
Конструкция грузозахватных приспособлений зависит от формы, размеров и массы захватываемых грузов. Приспособления подразделяются по назначению: для строповки и удержания листов, полотнищ, цилиндрических изделий. Приспособления классифицируются также по способу строповки груза: охватывающие и поддерживающие (стропы, петли, поддоны, скобы); защемляющие груз и удерживающие его трением (эксцентриковые и клещевые захваты); притягивающие (электромагнитные, с постоянными магнитами и вакуумные).
Охватывающие и поддерживающие приспособления наиболее надежны и безопасны в работе, но требуют много времени для зачаливания. Кроме того, при строповке большинства грузов значительное затруднение вызывает подвод приспособления под изделие.
Более совершенны приспособления, не требующие подвода под изделие. Для подъема листовой заготовки из пачки защемляющим приспособлением необходимо приподнять только край листа или немного сдвинуть лист с пачки, тогда как при использовании охватывающего и поддерживающего приспособления требуется приподнять лист над пачкой, после чего можно подвести приспособление.
Притягивающим приспособлением можно захватить лист прямо из пачки без предварительных операций. Это особенно ценно при межоперационном транспортировании в массовом и серийном производстве, а также в единичном производстве при наличии большого числа однотипных по форме грузов.
Недостаток электромагнитных и вакуумных приспособлений — невысокая надежность, вызываемая вероятностью прерывания подачи электроэнергии или нарушения вакуума. К недостаткам вакуумных приспособлений относится также быстрое изнашивание резиновых уплотнений. К тому же те и другие приспособления требуют прокладки коммуникаций для подвода электроэнергии, сжатого или разреженного воздуха. Грузоподъемность электромагнитных приспособлений колеблется в значительных пределах и зависит от качества контактирующей с электромагнитом поверхности груза, формы груза, воздушного зазора между грузом и электромагнитом. Этим объясняется применение электромагнитных и вакуумных приспособлений в основном на оборудовании, предназначенном для строповки определенных грузов в условиях, гарантирующих полную безопасность работы.
Вакуумные приспособления применяются на самоходных тележках при транспортировании листов. Электромагнитные приспособления используются на аналогичных устройствах и на мостовых кранах при перевозке листов на обособленных участках. Охватывающие и поддерживающие приспособления применяются в тех случаях, когда форма изделия позволяет выполнить их строповку без дополнительных операций (обечайки, трубы).
Грузозахватные приспособления иногда используются в сборочно-сварочном производстве нe только для строповки, но и для кантования груза. Для некоторых грузозахватных приспособлений универсального характера сборочно-сварочное производство является основной областью применения.
На рис. 8.5 показаны эксцентриковые захваты: грузоподъемностью 500 кг для строповки и кантования листов толщиной 6…25 мм в горизонтальном положении (рис. 8.5, а) и грузоподъемностью 1000 кг для строповки и кантования таких же листов в вертикальном положении (рис. 8.5, б). При зачаливании листов первым захватом и натяжении серьги эксцентрик рычага надежно зажимает лист в скобе и удерживает его в процессе подъема, транспортирования и опускания. Второй захват отличается от первого наличием двух пар тяг. Действие обоих захватов аналогично.
Рис. 8.5.Эксцентриковые захваты для строповки и кантования листов в горизонтальном (а) и вертикальном (б) положениях:
1 — скоба; 2 — эксцентрик; 3 — серьга; 4 — тяги
Электромагнитное грузозахватное приспособление (рис. 8.6) предназначено для строповки и перемещения на короткие расстояния небольших листов массой до 250 кг. Приспособление подвешено к крану и состоит из магнитов 1 постоянного тока, траверсы 2 и подвески 3. Питание к магнитам подается от трансформатора и выпрямителя, установленных на кране. Для строповки и перемещения небольших плоских изделий успешно применяются приспособления с постоянными магнитами.
Рис. 8.6.Электромагнитное грузозахватное приспособление:
1 — магнит постоянного тока; 2 — траверса; 3 — подвеска
Для строповки и транспортирования полотнищ применяются траверсы с эксцентриковыми захватами и с электромагнитами. Траверса с эксцентриковыми захватами (рис. 8.7) способна поворачивать полотнище на 90° и состоит из сварной балки 1, направляющих 2, уравнительных блоков 3 и цепей 6 с захватами. Траверса переносится мостовым краном на цепях 4. На уравнительных блоках 3, подвешенных на тросе 5, закреплены цепи 6 с вертикальными 7 и горизонтальными 9 захватами. Груз может транспортироваться горизонтально (полотнище 10) или вертикально (полотнище 8) с помощью соответствующих захватов. Неработающие захваты навешивают на специальные крюки на балке траверсы. Для кантования используют вертикальные захваты.
Траверса с электромагнитами (рис. 8.7, б) применяется для транспортирования полотнищ в горизонтальном положении специальным мостовым краном 14. Эта траверса состоит из сварной балки 1 с направляющими 11 и электромагнитов 13, которые снимают листы со стеллажа 15. Балка подвешена к мостовому крану с помощью блоков 12. Грузоподъемность траверсы 3 т; напряжение питания электромагнитов 220 В.
Рис. 8.7.Траверсы с эксцентриковыми захватами (а) и с электромагнитами (б) для захвата и транспортирования полотнищ:
1 — сварные балки; 2 — направляющий блок; 3 — уравнительный блок; 4 — цепь; 5 — трос; 6 — цепь с захватом; 7 — вертикальный захват; 8, 10 — вертикально и горизонтально транспортируемые полотнища; 9 — горизонтальный захват; 11 — направляющая; 12 — блок; 13 — электромагнит; 14 — специальный мостовой кран; 15 — стеллаж для складирования листов
Для транспортирования грузов цилиндрической формы (обечаек, технических сосудов, труб) применяются охватывающие и поддерживающие приспособления, которые легко подводятся под изделие. Простые скобы (рис. 8.8, а, б) для транспортирования коротких обечаек и технических сосудов заводят с торцовой стороны изделий.
Рис. 8.8.Простые скобы для транспортирования коротких обечаек (а) и технических сосудов (б); захват для строповки и перемещения труб (в):
1 — подвеска; 2 — тяга; 3 — скоба; 4 — упор; 5 — штырь; 6 — опорный ролик
Захват для строповки и перемещения труб (рис. 8.8, в) применяется при сварке труб магистральных трубопроводов. Захват состоит из двух скоб 3, двух тяг 2 и подвески 1, шарнирно соединенных между собой. На концах скоб имеются опорные ролики 6, а в верхней части скоб — упоры 4, предотвращающие зажим трубы. При ориентировании захвата перед опусканием его на трубу скобы автоматически раскрываются и закрепляются в этом положении штырем 5. После опускания и закрепления захвата штырь вынимают. При подъеме скобы смыкаются, подхватывая роликами трубу. При необходимости труба может поворачиваться на роликах вокруг своей оси.
8.5Конвейеры
Классификация. В сварочном производстве конвейеры применяют в основном в поточных механизированных и автоматических линиях серийного и массового производства как наиболее перспективный вид межоперационного транспорта.
По месту установки конвейеры могут быть напольными и подвесными.
По характеру движения различают конвейеры с непрерывным, пульсирующим и возвратно-поступательным движением.
Конвейер с непрерывным движением перемещается в одном направлении без остановок. Конвейер с пульсирующим движением перемещается с периодическими остановками. Конвейер с возвратно-поступательным движением перемещается попеременно вперед и назад, при этом груз перемещается на определенный шаг, и только при ходе вперед. Такие конвейеры называются шаговыми и широко применяются в поточных линиях для транспортирования средних и крупногабаритных изделий.
Различают конвейеры с гибким тяговым органом и без него.
Конвейеры с гибким тяговым органом. К конвейерам с гибким тяговым органом относятся ленточные (в которых лента служит тяговым, а также грузонесущим органом) и цепные (в которых тяговым органом служат цепи). Ленточные конвейеры в сварочном производстве имеют ограниченное применение — для доставки флюса и удаления шлака. Цепные конвейеры называют по конструкции элементов, которые крепятся к цепям: пластинчатые, тележечные, катковые. Все они успешно применяются при изготовлении сварных конструкций.
Пластинчатые конвейеры используются для транспортирования малогабаритных изделий. Конструктивно они наиболее просты. Несущими элементами в них служат поперечные пластины, прикрепленные к тяговым цепям.
Тележечные конвейеры применяются для межоперационного транспортирования крупногабаритных изделий. Конвейеры подразделяются на вертикально-замкнутые и горизонтально-замкнутые. Изделия перемещаются в этих конвейерах по одной или нескольким ветвям. Ветви вертикально-замкнутых конвейеров расположены в одной вертикальной плоскости, компактны и занимают мало места. Тележки на нижней ветви могут быть опрокидывающимися и неопрокидывающимися. В горизонтально-замкнутых конвейерах ветви расположены в одной горизонтальной плоскости. Эти конвейеры занимают большую производственную площадь. Их применение целесообразно в случаях, когда рабочие места можно расположить вдоль ветвей конвейера.
В сборочно-сварочном производстве тележечные конвейеры могут найти широкое применение благодаря возможности размещения на тележках сборочно-сварочных приспособлений, что обеспечивает высокое качество изделий, так как в продолжение всего процесса сборки и сварки изделие закреплено в одном приспособлении. Выбор схемы перемещения тележечного конвейера зависит от размеров и веса изделия, числа рабочих мест, наличия производственной площади, используемого технологического оборудования.
Вертикально-замкнутый конвейер с неопрокидывающимися тележками (рис. 8.9, а) предназначен для работы в составе линии сборки и сварки клавишей соломотряса самоходного комбайна. Конвейер состоит из приводной 1 и натяжной 5 станций и направляющих 4, по которым передвигаются тележки 3. Передние оси всех тележек связаны между собой тяговой цепью 2. На тележках размещены сборочно-сварочные кондукторы, в которых закрепляются свариваемые изделия. Направляющие в головной и хвостовой частях конвейера имеют специальные откидные участки 6 и 7 для прохода колес тележек при каждом переходе с одной ветви на другую.
Рис. 8.9.Схемы вертикально-замкнутого тележечного конвейера с неопрокидывающимися тележками (а) и тележечного конвейера с возвратно-поступательным движением (б):
1, 5 — приводные и натяжные станции; 2 — тяговая цепь; 3 — тележки; 4 — направляющая; 6, 7 — откидные участки; 8 — рельсовый путь; 9 — домкрат; 10 — стойка; 11 — выдвижная опора; 12 — тяговый орган; I—VII — исходные позиции тележек конвейера; в скобках приведены номера элементов конвейера, движения которых показаны соответствующими стрелками
Тяговый орган пластинчатого конвейера может совершать непрерывное и пульсирующее движение, а тележечного конвейера — еще и возвратно-поступательное. Пример такого конвейера — тележечный конвейер для транспортирования крупногабаритных изделий (рис. 8.9, б), работающий в составе линии сборки и сварки тепловозных рам.
Конвейер состоит из приводной 1 и натяжной 5 станций, рельсового пути 8, тележек 3 с домкратами 9 и стоек 10 с выдвижными опорами 11. Все тележки конвейера связаны тяговым органом 12 в единую линию. Свариваемые изделия устанавливаются мостовым краном на выдвижные опоры стоек конвейера. Тележки с опущенными домкратами находятся на шести исходных позициях. По окончании технологической операции на позиции I домкраты тележек поднимают изделие, выдвижные опоры стоек освобождаются и устанавливаются в нерабочее положение. После этого все тележки передвигаются на одну позицию и занимают позиции II—VII. Затем опоры стоек вновь устанавливаются в рабочее положение, домкраты тележек опускаются, изделие укладывается на стойки. После опускания домкратов все тележки одновременно возвращаются на исходные позиции. Начинается следующий цикл обработки изделия.
Конвейер имеет два режима работы — автоматический и ручной. При автоматическом режиме работы конвейером управляет диспетчер с центрального пульта. При ручном режиме управление каждой операцией осуществляется соответствующими кнопками управления: команды на выдвижение опор и передвижение тележек выдаются с помощью кнопок пульта управления диспетчера, а на подъем и опускание домкратов — с помощью кнопок, установленных на каждой тележке.
Разновидностью цепных конвейеров являются грузоведущие конвейеры, в которых тяговая цепь не связана постоянно с тележками, а толкает их специальными кулачками. Цепь прокладывается обычно в траншее ниже уровня пола, а тележки движутся по направляющим, закрепленным на полу, или непосредственно по полу. Грузоведущие конвейеры применяются для транспортирования тяжелых грузов, в том числе изделий на собственном колесном ходу. Преимущество таких конвейеров — отсутствие жесткой связи грузовой тележки с тяговой цепью, что позволяет в любом месте конвейера остановить тележку или передать ее на другой конвейер. Для расцепления тележки с цепью применяются устройства для отвода толкающих кулачков, управляемые автоматически или оператором. Стандартные грузоведущие конвейеры предназначены для транспортирования грузов на стандартных прицепных тележках грузоподъемностью до 3,2 т.
Катковые конвейеры характеризуются тем, что в них тяговые цепи связаны с роликами-катками, передвигающимися по направляющим. На рис. 8.10, а изображен роликовый катковый конвейер, работающий в составе линии сварки автомобильных колес. Изделие находится на несущих роликах 3, расположенных между двумя тяговыми цепями 1. С обеих сторон от несущих роликов размещены ролики-катки 2, передвигающиеся по направляющим 4. Такой конвейер одновременно служит накопителем. Изделие, находящееся на конвейере, передвигается до тех пор, пока не наткнется на препятствие, в том числе и на предыдущее изделие. В этом случае изделие останавливается, конвейер продолжает двигаться, и несущие ролики свободно проворачиваются под изделием, не перегружая механизмы движущегося конвейера. Скорость движения конвейера составляет 7,5 м/мин.
Рис. 8.10.Роликовые катковые конвейеры, работающие на линии сварки автомобильных колес (а) и на поточной линии сборки-сварки широких листовых полотнищ (б):
1 — тяговые цепи; 2, 7 — ролики-катки; 3 — несущий ролик; 4 — направляющие; 5 — ведущая звездочка; 6 — общий приводной вал
В катковых конвейерах опорные ролики могут быть и грузонесущими. При этом скорость груза в два раза больше скорости тяговой цепи конвейера. Такие конвейеры применяются в составе поточных линий сборки-сварки широких листовых полотнищ на судостроительных предприятиях (рис. 8.10, б). Конвейер состоит из нескольких тяговых цепей, огибающих ведущие звездочки 5, связанные общим приводным валом 6. К цепям прикреплены несущие ролики-катки 7.
Подвесные конвейеры, обеспечивающие межоперационное и внутрицеховое транспортирование изделий при любом расположении рабочих мест, получили широкое распространение во всех отраслях машиностроения, в том числе в автомобилестроении. Трасса подвесного конвейера может проходить в любом направлении и в любой плоскости.
Подвесные конвейеры можно подразделить на грузонесущие и грузотолкающие. В подвесном грузонесущем конвейере (рис. 8.11, а) тележки 3, передвигающиеся на роликах 2 по пути 1, связаны общей тяговой цепью 4. В подвесном грузотолкающем конвейере (рис. 8.11, б) тяговая цепь 4 не связана жестко с тележками 3, а толкает их специальными устройствами — кулачками 5. Тележки передвигаются на роликах 2 по подвесному пути 1. Конвейеры могут быть оборудованы системами автоматического адресования и управления.
Рис. 8.11.Грузонесущий (а) и грузотолкающий (б) подвесные конвейеры:
1 — путь; 2 — ролики; 3 — тележки; 4 — тяговая цепь; 5 — кулачок
Подвесные конвейеры одновременно с транспортированием изделий можно использовать в качестве межоперационных складов-накопителей. При этом рационально используется верхняя часть объема цеха. Грузонесущие конвейеры применяются для транспортирования грузов массой до 800 кг со скоростью до 20…25 м/мин, грузотолкающие — для транспортирования грузов массой до 2 т со скоростью до 10 м/мин.
Конвейеры без гибкого тягового органа. К конвейерам без гибкого тягового органа относятся роликовые, карусельные, штанговые и шагово-балочные конвейеры.
Роликовые конвейеры (рольганги) применяются для транспортирования изделий между рабочими местами. Они могут быть неприводными или приводными. Шаг роликов (расстояние между их осями) должен быть в 3—4 раза короче длины изделия. Роликовые конвейеры отличаются простотой и безотказностью в работе, что обусловило их широкое применение в сварочном производстве.
Конвейеры с цилиндрическими роликами применяются для транспортирования изделий с плоской опорной поверхностью (полотнищ, рам, балок). Ролики приводных конвейеров имеют следующие технические характеристики: диаметр 40…159 мм, длина 200…1200 мм, шаг 50…630 мм, нагрузка на ролик — до 20 кН (2000 кгс).
Для транспортирования труб применяются желобчатые и призматические ролики. Ролики устанавливаются на шариковых подшипниках. По неприводным рольгангам изделия перемещаются вручную или под действием собственного веса. В последнем случае конвейеры располагают с небольшим уклоном (2…3%). При этом наклонными выполняются короткие участки, находящиеся между соседними рабочими местами.
В приводных конвейерах ролики получают вращение от электродвигателя посредством трансмиссионного вала с коническими передачами или посредством цепных передач, либо от индивидуальных электродвигателей, установленных непосредственно на каждом ролике. Последний вариант применяется в конвейерах для перемещения крупногабаритных изделий. Для лучшего сцепления с изделием и для уменьшения шума используются обрезиненные ролики. Скорость приводных роликовых конвейеров — до 30 м/мин.
Роликовые конвейеры поточных механизированных и автоматических линий состоят из отдельных секций с независимыми приводами. Благодаря этому они широко распространены в линиях с гибкой связью, где обеспечивают возможность независимого управления отдельными участками линии.
Специальный роликовый конвейер для транспортирования крупногабаритных цилиндрических изделий (рис. 8.12) применяется в поточной линии сборки и сварки железнодорожных цистерн. Он включает в себя отдельно стоящие приводные 1 и неприводные 6 обрезиненные ролики, причем напротив каждого приводного ролика установлен неприводной. Ролики закреплены на раме 3 в стойках 2. Приводной ролик вращается электродвигателем 4 мощностью 1 кВт через редуктор 5. Свариваемые обечайки диаметром 2800 мм, длиной 9280 мм, массой 7300 кг передвигаются по конвейеру со скоростью 11,2 м/мин.
Рис. 8.12.Специальный роликовый конвейер для транспортирования крупногабаритных цилиндрических изделий:
1, 6 — приводной и неприводной ролики; 2 — стойка; 3 — рама; 4 — электродвигатель; 5 — редуктор
Карусельные конвейеры (рис. 8.13), заметно отличающиеся по конструкции от других конвейеров, представляют собой поворотный круг 1, вращающийся на опорных катках 3 по замкнутому рельсовому пути 4. Вращение круга осуществляется от приводной станции 7 через цепь 6 либо от цевочного (или зубчатого) зацепления. На поворотном круге устанавливаются сборочно-сварочные приспособления для выполнения всех необходимых рабочих операций.
Рис. 8.13.Карусельный конвейер:
1 — поворотный круг; 2 — вращающийся воздухопровод; 3 — опорный каток; 4 — замкнутый рельсовый путь; 5 — рабочие места; 6 — цепь; 7 — приводная станция
Большое преимущество карусельных конвейеров — возможность изготовления изделия без перестановки, т. е. в одном сборочно-сварочном приспособлении. Такой конвейер может быть легко оборудован пневматическими сборочными приспособлениями, питание которых осуществляется сжатым воздухом по вращающемуся воздухопроводу 2 через центральную ось. Сварочные аппараты подвешиваются на круговом монорельсе над рабочими местами 5, а источники питания располагаются внутри кольца поворотного круга. Конвейер может совершать непрерывное или пульсирующее движение.
Штанговые конвейеры (рис. 8.14) широко применяются в поточных линиях для шагового перемещения изделий средних размеров. Штанги 3 конвейера жестко связаны с приводным гидро- или пневмоцилиндром 1. На штангах через определенный шаг на осях 7 закреплены собачки 4, прижимаемые пружинами 6 к штифтам 8. Рядом со штангами находятся направляющие 2, на которых располагается изделие. При каждом ходе цилиндра штанги с выступающими собачками перемещают изделие 5 на один шаг, равный ходу цилиндра. При обратном ходе собачки наталкиваются на расположенные сзади изделия и, опускаясь, свободно проходят под ними, после чего цикл повторяется.
Рис. 8.14.Штанговый конвейер:
1 — гидро- или пневмоцилиндр; 2 — направляющие; 3 — штанги; 4 — собачки; 5 — изделие; 6 — пружина; 7 — ось; 8 — штифт; а — шаг конвейера
Шагово-балочные конвейеры (рис. 8.15) применяются для шагового перемещения крупногабаритных изделий массой до 7 т. Конвейер состоит из двух связанных между собой горизонтальных балок 1, перемещающихся по опорным роликам 2, расположенным вдоль нескольких рабочих мест. Между балками на рабочих местах расположены подъемные столы 3. Балки совершают периодические возвратно-поступательные движения на длину шага, равную расстоянию между соседними рабочими местами. Перед началом перемещения балок подъемные столы опускаются ниже их уровня и изделия оказываются на балках (положение I). В таком положении балки с изделиями передвигаются на шаг вперед. После остановки балок подъемные столы поднимаются выше их уровня и снимают изделия (положение III). Во время технологической операции балки совершают обратный ход (положение IV), после чего столы опускаются и цикл повторяется. Привод движения балок может быть электрическим и гидравлическим. С учетом значительной величины перемещаемых масс и требования точной остановки изделия напротив установочных баз рабочего места привод должен обеспечить плавное замедление в конце хода. Для уменьшения шума при работе конвейера используются обрезиненные опорные ролики. Такие конвейеры широко применяются в автомобильной промышленности (например, при сборке и сварке основных частей кузовов легковых автомобилей).
Рис. 8.15.Шагово-балочный конвейер:
1 — горизонтальная балка; 2 — опорный ролик; 3 — подъемный стол; I—IV — последовательные положения изделия в процессе перемещения
8.6Вспомогательные транспортные средства
К вспомогательным транспортным средствам относятся средства для передачи изделий между конвейерами: подъемные и поворотные столы, кантователи, механические руки (автооператоры), перегружатели, скаты, склизы.
Подъемные столы, или подъемники (рис. 8.16, а), используются для передачи изделий между смежными конвейерами, расположенными на разных уровнях. Подъем осуществляется гидро- или пневмоцилиндром. Поворотные столы (рис. 8.16, б) используются для поворота изделия в плане на заданный угол (до 180°). Для этого поворотные столы оснащаются гидро-, пневмо- или электроприводами.
Кантователи, используемые для кантования изделий на 90 или 180°, по конструкции могут быть кольцевыми или рычажными. Кантователи с гидро- или электроприводом не требуют закрепления изделий.
Рис. 8.16.Подъемный (а) и поворотный (б) столы для передачи изделий между конвейерами
Механические руки (автооператоры) успешно используются не только для передачи изделий между конвейерами, но и для загрузки и разгрузки конвейеров, для передачи изделий с конвейеров на рабочие места и обратно.
Перегружатели по назначению аналогичны механическим рукам и представляют собой захватные устройства с механизмом подъема, закрепленным на передвигающейся по монорельсу тележке. Монорельс располагается между обслуживаемыми позициями. В качестве захватных устройств в перегружателях используются механические захваты или электромагниты, в качестве механизма подъема и передвижения — электротали. Как и автооператоры, перегружатели могут быть автоматизированными.
Для передачи небольших изделий на коротких участках под действием собственного веса применяются скаты — наклонные секции неприводных рольгангов, склизы — наклонные плоскости или желоба.
Контрольные вопросы
1. Для чего предназначено и как классифицируется подъемно-транспортное оборудование в сборочно-сварочном производстве?
2. Какие универсальные средства внутрицехового транспорта применяются в сборочно-сварочном производстве?
3. Для чего предназначены специализированные подъемно-транспортные средства? Чем они отличаются от универсальных средств общего применения?
4. Как работает четырехкрюковый мостовой кран?
5. Какие грузозахватные приспособления вы знаете?
6. Как работают конвейеры с гибким тяговым органом?
7. Расскажите о подвесных конвейерах.
8. Как работают штанговые и шагово-балочные конвейеры?
9. Опишите устройство роликовых и карусельных конвейеров.
10. Какие вспомогательные транспортные устройства вы знаете?
ГЛАВА9Автоматизация сварочного производства
· 9.1. Станки-полуавтоматы
· 9.2. Станки-автоматы
· 9.3. Станочные комплексы с ЧПУ для автоматической аргонодуговой сварки
· 9.4. Особенности автоматизации управления электронно-лучевой аппаратурой
· 9.5. Механизированные и автоматические линии
· 9.6. Комплексно-механизированные и комплексно-автоматизированные линии
· 9.7. Промышленные роботы и роботизированные комплексы
9.1Станки-полуавтоматы
Станок для сборки и автоматической сварки корпусов шахтерских ламп (рис. 9.1) работает следующим образом. Детали корпуса лампы (обечайку, кольцо и донышко) устанавливают на патроне 1. С помощью пневмоцилиндра 4 секторы патрона разжимаются, и детали закрепляются на медных подкладках патрона. Затем включается вращатель 3, поворачивающий патрон с изделием, и сварочной головкой 2 выполняется первый кольцевой шов. Далее выполняется продольный шов. При этом патрон неподвижен, а головка перемещается с помощью механизма продольного перемещения. Затем головка останавливается, а патрон начинает вращаться — происходит сварка вторым кольцевым швом. Переключение механизмов станка со сварки одним швом на сварку другим швом происходит автоматически, и сварка всеми тремя швами выполняется непрерывно (без обрыва дуги). Все механизмы станка размещены на станине 5, внутри которой находится флюсоприемник. Сварка производится под слоем флюса со скоростью 50…200 м/ч на постоянном токе. При установке деталей и снятии изделия сварочную головку отводят в сторону. Толщина стенок свариваемых деталей 1,5 мм, внутренний диаметр обечайки 104 мм, длина корпуса лампы 176 мм.
Рис. 9.1.Станок для сборки и автоматической сварки корпусов шахтерских ламп:
1 — патрон; 2 — сварочная головка; 3 — вращатель; 4 — пневмоцилиндр; 5 — станина
Вальцесварочный станок для сборки и дуговой сварки под слоем флюса кузовов шахтных вагонеток работает в составе механизированной поточной линии. Кузов вагонетки (рис. 9.2) состоит из боковины 2 и двух днищ 1 (лобовин). На станке одновременно производятся вальцовка-гибка боковины валками 3 и сборка боковины с лобовинами, а также выполняется автоматическая сварка горелками 4 лобовины с боковиной двумя криволинейными швами.
Рис. 9.2.Кузов шахтной вагонетки:
1 — лобовина; 2 — боковина; 3 — валок прижимного устройства; 4 — горелки сварочного аппарата
Изготовление кузова на вальцесварочном станке происходит в следующем порядке. Штампованные лобовины подаются специальным механизмом на станок и закрепляются в нем. Затем заводится плоская заготовка боковины и с помощью валка 3 прижимного устройства плотно прижимается к лобовинам. После этого начинается автоматическая сварка двумя швами одновременно. В дальнейшем сварка происходит непрерывно по всему контуру лобовины, состоящему из двух прямых и одного полукруглого участка. По достижении сварочными аппаратами начала круговых швов движение сварочной тележки автоматически прекращается и одновременно включается привод вращателя.
На полукруглых участках лобовин боковина под действием прижимных валков 3 и благодаря вращению кондуктора сгибает лобовины. При этом изделие вращается со скоростью сварки, и одновременно с вальцовкой боковины происходит сварка круговыми швами. Когда кондуктор поворачивается на 180° и полукруглые участки стыков оказываются сваренными, вращение автоматически прекращается и снова включается движение сварочной тележки вдоль прямых участков швов. По окончании сварки кузов снимается с кондуктора и подается на поток. Скорость сварки составляет 50 м/ч, производительность станка — 10 вагонеток в час. Система управления станком — децентрализованная с помощью путевых и конечных переключателей.
9.2Станки-автоматы
Необходимая часть сварочных и сборочно-сварочных станков-автоматов — загрузочное устройство, обеспечивающее бесперебойную подачу заготовок в станок. Каждое загрузочное устройство должно иметь накопитель (магазинный или бункерный) для хранения запаса заготовок и механизмы для отделения от всей массы одной заготовки и подачи ее в рабочую зону станка. В станках для изготовления изделий, состоящих из нескольких одинаковых деталей, в рабочую зону одновременно подается соответствующее количество заготовок.
В магазинных накопителях заготовки заранее укладывают в один ряд в определенном положении в специальный лоток. Схемы подачи круглых заготовок различными загрузочными устройствами показаны на рис. 9.3. При подаче заготовок вертикальным магазинным накопителем (рис. 9.3, а) очередная (нижняя) заготовка подается в рабочую зону толкателем 1, совершающим возвратно-поступательное движение. При этом он придерживает все остальные заготовки, т. е. выполняет функции не только питателя, но и отсекателя. При возвратном ходе толкателя заготовки под действием собственного веса опускаются, и очередная заготовка оказывается подготовленной к выдаче. Толкатель приводится в действие пневмо- или гидроцилиндром.
Рис. 9.3.Схема подачи круглых заготовок различными загрузочными устройствами:
а — вертикальным магазинным накопителем; б — бункерным накопителем; в — штифтовым отсекателем; г — устройством барабанного типа; 1, 3 — толкатели; 2 — бункер; 4, 7 — лотки; 5 — питатель; 6 — упор; 8, 10 — верхний и нижний штифты; 9 — рычаг; 11 — диск
В бункерных накопителях (рис. 9.3, б) заготовки укладывают в бункеры навалом, что является преимуществом этих накопителей, поскольку в этом случае не требуется выполнения специальной операции по укладке заготовок в определенном положении. Из бункера 2 заготовки подаются толкателем 3 на лоток 4, где задерживаются упором 6 и располагаются в один ряд. Отсюда питатель 5 выдает заготовки поштучно. Питатель 5 работает синхронно со всем станком, включаясь в работу в начале каждого цикла, а толкатель 3 включается тогда, когда запас заготовок в лотке 4 становится меньше допустимого. В этом устройстве лоток 4 с питателем 5 работают как самостоятельное загрузочное устройство магазинного типа.
Штифтовой отсекатель (рис. 9.3, в) отделяет по одной заготовке от общей группы заготовок. Отсекатель состоит из двух штифтов 8 и 10, поочередно выдвигающихся в лоток 7. При этом нижний штифт 10 задерживает движение всех заготовок, а верхний штифт 8 освобождает нижнюю заготовку, задерживая остальные (положение показано на схеме). Штифты приводятся в движение рычагом 9, связанным с приводным механизмом.
Устройство барабанного типа (рис. 9.3, г) также предназначено для отделения одной заготовки от общей группы заготовок. При каждом повороте диска 11 на определенный угол очередная заготовка, захваченная его гнездом, поступает к рабочей зоне. На схеме изображен диск с шестью гнездами, следовательно, угол поворота равен 1/6 полного оборота, т. е. 60°.
Конструкция загрузочного устройства зависит от формы, размеров и массы заготовок. Все рассмотренные схемы применяются при подаче круглых заготовок (цилиндров, труб, осей, шаров). Загрузочные устройства для подачи фасонных заготовок имеют более сложную конструкцию.
Рассмотрим устройство сварочных станков-автоматов на примере станка-автомата для шовной сварки цилиндров гидроамортизатора автомобиля. Станок состоит из вала с двенадцатью радиальными оправками, загрузочного устройства с толкателем, двух сварочных головок (с роликами, фрикционными приводными колесами и пневмоцилиндрами), двух приводов.
Цилиндры гидроамортизатора с предварительно запрессованными проушинами укладывают в загрузочное устройство. Отсюда они пневмотолкателем подаются на одну из двенадцати радиальных оправок. Вал периодически поворачивается на угол 30°, и при каждом повороте очередная оправка с надетым на нее цилиндром оказывается между роликами. Пневмоцилиндры прижимают к изделию ролики, получающие вращение от приводов через карданные передачи и фрикционные колеса. Осевое смещение изделия предотвращается пневмоцилиндром. Каждый ролик выполняет половину шва (по длине). После сварки ролики раздвигаются, вал поворачивается на 30° и сваренное изделие снимается съемником. Система управления автоматическим циклом — централизованная.
Станок, показанный на рис. 9.4, предназначен для сборки и автоматической сварки в среде углекислого газа пустотелых стальных шаров. Каждый шар диаметром 200 мм сваривается из двух полусфер, штампуемых из листовой стали толщиной 2 мм; кромки полусфер обтачиваются на токарном станке. Сварной шов должен быть прочно-плотным, выдерживающим давление 4…5 МПа.
Рис. 9.4.Станок для сборки и автоматической сварки в среде углекислого газа пустотелых стальных шаров:
1, 4 — передняя и задняя бабки; 2 — пружинящий захват; 3 — сварочная головка; 5 — тормоз; 6 — откидной нож; 7 — упор; 8 — блок управления
Станок состоит из загрузочного устройства с отсекателем заготовок, передней и задней бабок с центрирующими конусами и пружинящими захватами, откидного ножа для точной установки заготовок, сварочной головки, пневмосистемы и аппаратуры управления. Передняя бабка (приводная) снабжена редуктором со сменными зубчатыми колесами; задняя бабка оборудована колодочным тормозом.
Большинство механизмов станка (передняя и задняя бабки, тормоз задней бабки, откидной нож, отсекатели загрузочного устройства) приводится в действие пневмоцилиндрами; передняя бабка получает вращение от электродвигателя.
Заготовки поступают в станок попарно по наклонному лотку. В конце лотка расположены два откидных упора 7, первый из которых задерживает весь поток, а второй — очередную пару заготовок. В момент загрузки второй упор откидывается, и очередная пара заготовок катится по направляющим до неподвижного упора. Здесь заготовки попадают в центрирующие конусы передней 1 и задней 4 бабок, цилиндры которых прижимают заготовки к плоскостям откидного ножа 6, находящегося при загрузке в верхнем положении. После этого шток задней бабки фиксируется тормозом 5, а передняя бабка отходит влево на 2 мм, освобождая откидной нож. Заготовки при этом удерживаются в конусах пружинящими захватами 2. Освобожденный нож откидывается в нижнее положение, передняя бабка подается вперед и плотно поджимает полусферы друг к другу и к задней бабке.
Благодаря наличию откидного ножа и тормоза на задней бабке стык располагается всегда в одной и той же вертикальной плоскости, перпендикулярной оси вращения. Таким образом, обеспечивается расположение электрода сварочной головки 3 в этой же плоскости, над стыком, в любой момент сварки независимо от неточности действительных размеров и формы заготовок. После прижима полусфер включается привод вращателя и начинается сварка, необходимую длительность которой обеспечивает реле времени.
Работой большинства механизмов управляет блок управления 8, кулачки которого вращаются и через пневмораспределители и конечные выключатели включают пневмоцилиндры, двигатели и электромагниты строго в заданной последовательности. Механизм загрузки включается с помощью путевого выключателя скатывающимся по наклонному желобу сваренным шаром. Наблюдение за сваркой ведется через стекло защитного щитка.
Благодаря полной автоматизации всего процесса сборки и сварки шаров станок легко встраивается в автоматическую линию. Продолжительность цикла 70 с, из которых непосредственно сварка занимает 55 с.
9.3Станочные комплексы с ЧПУ для автоматической аргонодуговой сварки
Изготовление авиационных сварных конструкций связано с применением специальных алюминиевых сплавов, сталей и титановых сплавов. Использование таких материалов с особыми свойствами вызвало необходимость разработки специальных способов сварки, обеспечивающих качественное формирование шва без разбрызгивания присадочного металла, надежную защиту свариваемого металла от окисления и предотвращение потерь легирующих элементов. Одним из таких способов сварки является аргонодуговая сварка, длительное время остающаяся основным способом соединения деталей летательных аппаратов.
В течение десятилетий все авиационные конструкции изготовлялись по традиционной технологии формообразования и сборки-сварки: сварка на универсальных стендах (продольными швами — на продольных стендах с пневмоклавишным прижимом, кольцевыми — на универсальных вращателях с разжимными кольцами); формообразование на традиционном оборудовании (листогибочных прессах, листогибочных валковых машинах и обтяжных прессах); торцовка стыкуемых кромок изделий под сварку на универсальных металлорежущих станках (фрезерных, токарных и карусельных). Все сварные швы выполнялись с ручной прихваткой. Для автоматической сварки использовались универсальные сварочные головки, которые перемещались вдоль стыков на легких направляющих. Регулирование длины дуги и направления вдоль стыка в процессе сварки, как правило, проводилось сварщиком вручную.
Применение такой технологии сборки-сварки изделий приводило к большому числу дефектов сварных швов. На некоторых изделиях выполнялось 20—50 ремонтных подварок. При ручной подварке удавалось устранить дефекты только после 2—3-й подварки. Сварные изделия в ряде случаев не соответствовали требованиям конструкторской документации по геометрическим размерам, а сварные швы имели низкие механические свойства, особенно в местах многочисленных подварок.
Проведенный анализ традиционной технологической схемы формообразование—сборка—сварка—механическая обработка позволил выявить ее основные недостатки:
§ низкая точность деталей, входящих в сварные узлы;
§ частое несовпадение траектории перемещения сварочной горелки по свариваемым стыкам с осью подкладки;
§ неплотное и неравномерное прижатие кромок к подкладке;
§ непостоянство дугового промежутка в процессе сварки;
§ большой разрыв во времени между зачисткой кромок и сваркой;
§ значительные деформации кромок в процессе сварки и остаточные напряжения после сварки;
§ чрезвычайная сложность оснастки для выполнения швов сложной формы.
Эти недостатки вызваны рядом причин:
§ выполнение обработки торцов резанием и сварки на разных рабочих местах;
§ недостаточные точность и жесткость конструкций сборочно-сварочных стендов;
§ малые усилия прижатия кромок заготовок к подкладке;
§ невозможность выполнения сложных швов применяемыми сварочными механизмами;
§ отсутствие средств и приемов снижения остаточных деформаций;
§ нестабильность работы датчиков автоматического слежения по высоте при сварке с присадочной проволокой;
§ проведение зачистки кромок вручную шабером или металлической щеткой.
Анализ отмеченных недостатков и вызвавших их причин позволил определить основные направления работы по изменению технологического процесса формообразование—сборка—сварка—механическая обработка и совершенствованию оборудования для сборки, обработки резанием и сварки сложных пространственных конструкций. Было признано целесообразным: производить формообразование по возможности на станках с ЧПУ; выполнять механическую обработку, сборку и сварку на одном рабочем месте и по единой программе; значительно повысить жесткость и точность сварочных приспособлений; внедрять устройства и приемы снижения остаточных деформаций; разработать технологию и конструкцию инструмента для механизированной зачистки кромок непосредственно перед сваркой; применять наиболее эффективные способы сварки; изменить способ прижатия кромок к подкладке.
Для обоснованной оценки каждого из этих мероприятий были проведены эксперименты на специально созданном стенде на базе серийного фрезерного станка ФП-17М. С учетом предварительно выполненных экспериментов разработана новая технология процесса формообразование—сборка—сварка—механическая обработка и создана гамма специализированного оборудования на базе станков с ЧПУ, охватывающая все типоразмеры изготовляемых сварных узлов. Это обеспечило возможность обслуживания операционного поля диаметром 0,25…7 м при любой длине обрабатываемого изделия.
Специализированная станочная установка типа УПСФ обеспечивает выполнение ряда технологических операций: механической обработки, подготовки поверхности под сварку, сборки, сварки, правки. Установка состоит из унифицированных агрегатов и механизмов-модулей. При наличии готовых модулей на базе одного станка легко компонуется оборудование для изготовления любых изделий с применением аргонодуговой сварки. Гамма специализированных головок позволяет выполнять все операции технологического процесса: фрезерование торцов деталей под сварку; механизированную зачистку кромок под сварку; сварку с применением локальных подвижных роликовых прижимов; механизированную правку после сварки. Посадочные места всех специализированных головок унифицированы, что позволяет устанавливать любую головку на любой установке типа УПСФ.
Применение конкретного станка в качестве базы позволило резко повысить жесткость и стабильность системы станок—приспособление—инструмент—заготовка при обработке резанием и при сварке, что обеспечило возможность проведения с большой точностью (недостижимой ранее) всех разметочных и контрольных работ до сварки и после нее на комплексах с использованием устройств цифровой индикации станка. Точность и качество выполняемых операций определяются уже не квалификацией сварщика или фрезеровщика, а качеством записи и воспроизведения единой программы. Наличие единой программы базирования по контрольно-фиксирующим отверстиям обеспечило серийный выпуск сварных узлов при стабильном качестве и практически одинаковых геометрических размерах. Программируемые координаты и механическое копирование локальным подвижным роликовым прижимом гарантирует постоянство дугового промежутка (с точностью ±0,05 мм) по всей длине швов любой геометрической формы и точность прохождения вольфрамового электрода вдоль оси стыка любой формы (с точностью ±0,08 мм).
Процесс установки, обработки резанием и сварки происходит следующим образом. В каждой из соединяемых заготовок со стороны конца стыка последовательно по кондуктору сверлят отверстия (не меньше двух), по которым и проводят все установочные работы. Каждую заготовку устанавливают в приспособление с помощью зажимов с отверстиями для штырей. Штыри вставляют одновременно в отверстия заготовки и зажима, обеспечивая точную фиксацию стыков кромок под обработку. Со стороны начала стыка обе заготовки фиксируют в жестких зажимах, а со стороны конца стыка — в зажимах, имеющих возможность свободно перемещаться относительно оснастки. Перед началом фрезерования сварочная подкладка опускается на 15…20 мм. Обработку кромок проводят последовательно по единой программе (сначала левой, затем правой заготовки).
Для прижатия заготовок к подкладке при традиционной технологии применялись стенды с пневмоклавишными прижимами. Такие стенды были громоздкими, затрудняли обзор зоны сварки, не обеспечивали большое усилие прижатия, исключали применение средств и приемов снижения остаточных деформаций в процессе сварки.
Эксперименты показали, что более перспективным является подвижный роликовый прижим (рис. 9.5), состоящий из корпуса 3 и вертикальных ползунов 2 для закрепления и перемещения роликов 1. Каждый ролик установлен под углом к заготовкам 5 (расположенным на сварочной подкладке 6) и имеет возможность свободно перемещаться по вертикали. Сварочная горелка 4 жестко крепится к одному из ползунов с роликом, что обеспечивает механическое копирование поверхности при перепадах по высоте от 0 до 5 мм. Слежение по высоте при перепадах 5…1500 мм осуществляется за счет программируемой координаты. Рычажным механизмом можно быстро изменить усилие прижатия каждого ролика в пределах 10…500 даН, меняя величину груза и плечо его подвески. Диаметр роликов 125…200 мм, угол их наклона 40…60°, расстояние от оси стыка до точки контакта роликов с деталью 10…15 мм (в зависимости от толщины деталей и ширины шва).
Рис. 9.5.Схема локального подвижного роликового прижима:
1 — ролики; 2 — ползуны; 3 — корпус; 4 — сварочная горелка; 5 — заготовки; 6 — сварочная подкладка
Применение локального подвижного роликового прижима позволяет полностью отказаться от громоздких пневмоклавишных прижимов, значительно упростить конструкции сварочных приспособлений, улучшить обзор зоны сварки, значительно повысить и стабилизировать усилие прижатия кромок непосредственно в зоне сварочной ванны.
Технологический процесс сборки-сварки на станочных комплексах с ЧПУ был успешно внедрен в авиационно-космической промышленности при изготовлении конструкций из стали и алюминиевых и титановых сплавов. Этот технологический процесс применялся при создании такой современной техники, как орбитальный космический корабль многоразового использования «Буран» и самолеты серии МиГ.
9.4Особенности автоматизации управления электронно-лучевой аппаратурой
Технология электронно-лучевой сварки базируется на трех основных компонентах: генератор электронного луча, вакуумная камера, станочный комплекс. Для реализации технологического процесса с заданными параметрами требуется взаимозависимое управление этими компонентами. К тому же многофункциональность электронно-лучевой сварки выдвигает ряд дополнительных требований, связанных с формированием на изделии теплового пятна с заданными плотностью энергии и площадью обработки.
Для удовлетворения этих требований наиболее целесообразно применение устройств или систем программного управления. До недавнего времени применялись лишь УЧПУ, предназначенные для управления металлорежущими станками и обрабатывающими центрами. Эти устройства не имели в своем составе средств для специфического управления электронным лучом, поэтому управление электронно-лучевой аппаратурой возлагалось на специальные программные устройства, которые приходилось синхронизировать с УЧПУ станочного комплекса и дополнительно программировать на отработку заданного цикла.
Развитие компьютерной техники и создание промышленных аппаратных средств различного назначения позволили реализовать систему управления с заданными свойствами и функциональными возможностями практически для любой сферы применения.
Функциональные возможности системы управления в этом случае определяются в основном программным обеспечением, которое разрабатывается с учетом конкретных требований технологического процесса и пожеланий заказчика. Причем аппаратурная компактность такой системы позволяет разместить все основные модули (за исключением силовых) внутри единого устройства (например, в корпусе промышленного компьютера), установленного на рабочем месте оператора. В то же время для уменьшения количества соединений между исполнительными органами установки и устройством управления, а также для расширения возможностей системы по управлению исполнительными органами установки, удаленными от центрального устройства управления, целесообразно применение распределенной системы управления, когда ее отдельные части обмениваются между собой данными по последовательному каналу, подчиняясь командам центрального устройства. В обоих случаях можно говорить об интегрированной системе управления (ИСУ), обладающей одновременно свойствами нескольких систем.
Для интегрированной системы управления электронно-лучевой установки обязательно наличие следующих основных технологических возможностей:
§ контурное управление тремя осями станочного комплекса по прямолинейным и криволинейным траекториям;
§ управление параметрами режима электронно-лучевой сварки (в зависимости от пространственного положения луча относительно изделия — от 6 до 12 параметров);
§ управление отклонением и развертками луча для формирования заданного теплового пятна (по форме и по энергии) в процессе сварки;
§ дискретное автоматическое управление вспомогательным оборудованием для создания вакуума в рабочей камере, загрузки и выгрузки изделия из камеры;
§ дополнительные сервисные функции, облегчающие программирование, наблюдение, регистрацию параметров технологического процесса и контроль за работой оборудования.
Расширение возможностей интегрированной системы управления зависит от конкретных требований технологического процесса, пожеланий заказчика и свойств аппаратуры. В перспективе возможно включение в эту систему средств для реализации функций визуального наблюдения за технологическим процессом, наблюдения за зоной сварки, а также ряда специфических функций (контроль за глубиной проплавления, определение равного положения фокуса, распределение плотности энергии по сечению луча).
9.5Механизированные и автоматические линии
Общие сведения. Механизированные и автоматические линии сварочного производства классифицируют по степени охвата операций технологического процесса, номенклатуре изготовляемых изделий, признаку непрерывности технологического процесса, компоновке, пространственному расположению оборудования.
По степени охвата операций технологического процесса различают линии с полным охватом всего комплекса операций производства сварных изделий (многооперационные) или с частичным охватом операций (сборочно-сварочные, отделочные). Комплекс операций, выполняемых на линии, зависит от конструкции свариваемого изделия и масштаба производства.
По номенклатуре изготовляемых изделий линии подразделяют на однономенклатурные (предназначенные для изготовления изделий одного типоразмера) и многономенклатурные (для изготовления изделий разных типоразмеров). Многономенклатурные линии подразделяются на линии, работающие с переналадкой или без переналадки. Однономенклатурные линии применяются в массовом и крупносерийном производстве, многономенклатурные — в серийном и мелкосерийном.
По признаку непрерывности технологического процесса различают линии с непрерывным и прерывистым технологическим процессом. Первые характеризуются непрерывным воздействием инструмента на обрабатываемое изделие при непрерывном перемещении изделия. Эти линии отличаются большей производительностью, так как непрерывный производственный процесс не предусматривает непроизводительных затрат вспомогательного времени на установку изделия, подвод инструмента и другие вспомогательные приемы. Вторые линии характеризуются воздействием инструмента на обрабатываемое изделие с перерывами, необходимыми для снятия изделия после обработки, установки нового изделия, подвода инструмента.
По компоновке выделяют линии с жесткой и гибкой связью между рабочими местами. На линиях с жесткой связью (рис. 9.6, а) обрабатываемые изделия перемещаются от одного рабочего места к другому без образования заделов. Линии с гибкой связью (рис. 9.6, б) имеют накопители полуфабрикатов на каждом рабочем месте. Линии с жесткой связью занимают меньшую производственную площадь, состоят из простого по конструкции оборудования и поэтому значительно дешевле линий с гибкой связью. Однако в линиях с жесткой связью неисправность любого механизма влечет за собой остановку работы всей линии, что является серьезным недостатком. Второй недостаток линий с жесткой связью — это потери рабочего времени из-за несинхронности выполнения операций на разных участках линии. В многооперационных линиях этот недостаток устраняется разделением линии на участки из сблокированных рабочих мест, между которыми размещаются накопители полуфабрикатов (рис. 9.6, в).
Рис. 9.6.Классификация поточных линий по компоновке и по пространственному расположению оборудования:
а — с жесткой связью и последовательным расположением оборудования; б — с гибкой связью и последовательным расположением оборудования; в — с накопителями между участками и последовательным расположением оборудования; г — с последовательно-параллельным расположением оборудования; д — с параллельным расположением оборудования; 1—6 — номера единиц оборудования (рабочих мест)
По пространственному расположению оборудования выделяют линии с последовательным (см. рис. 9.6, а—в), последовательно-параллельным (рис. 9.6, г) и параллельным (рис. 9.6, д) расположением оборудования.
Рациональный выбор линий. Опыт эксплуатации механизированных и автоматических линий сварочного производства позволяет сформулировать рекомендации по их рациональному выбору.
1. Линии с более высоким уровнем комплексной механизации и автоматизации, с полным охватом всего комплекса операций производства сварных изделий (от подачи заготовки на линию до отделки готового изделия) эффективно работают в массовом производстве при выпуске простых по конструкции изделий с небольшим числом деталей. Примерами таких линий могут служить линии для изготовления прямошовных и спиралешовных труб и стальных радиаторов отопления. Для изготовления многоэлементных сложных сварных конструкций более подходят сборочно-сварочные линии с организацией изготовления деталей на отдельных линиях заготовительного производства.
2. Механизированные линии применяют как в массовом, так и в мелкосерийном многономенклатурном производстве. Типичными многономенклатурными линиями являются линии для изготовления стальных листовых полотнищ (для дальнейшей сварки резервуаров) и пролетных балок электромостовых кранов.
3. Линии с жесткой связью не имеют накопителей на рабочих местах, поэтому их целесообразно применять для изготовления крупногабаритных сварных изделий. Большинство линий с жесткой связью представляют собой многопозиционные комбинированные машины. К ним относятся линии для изготовления стальных листовых полотнищ (для дальнейшей сварки резервуаров), спиралешовных труб и стальных радиаторов отопления. В таких линиях обычно имеются накопители между отдельными участками сблокированных рабочих мест.
4. Линии с последовательным расположением оборудования (с незамкнутым и замкнутым потоком) получили наибольшее распространение в сварочном производстве, что объясняется наличием сквозного транспорта, освобождающего от необходимости применять сложные механизмы для передачи изделий с конвейера на рабочие места. Линии с последовательно-параллельным расположением оборудования целесообразно применять в тех случаях, когда невозможно синхронизировать все операции потока, а разделение линии на определенном участке на несколько параллельных ветвей позволяет сократить длительность операций. Примерами таких линий являются линии для изготовления прямошовных труб и кабин грузовых автомобилей. Линии с параллельным расположением оборудования, состоящие из ряда одинаковых машин, соединенных общим конвейером для транспортирования свариваемых изделий, эффективны при массовом выпуске малогабаритных изделий с использованием полуавтоматов или автоматов, выполняющих одинаковый объем операций.
5. Наиболее прогрессивной формой организации непрерывного технологического процесса являются линии для производства сварных изделий из рулонного проката, применяемые при изготовлении спиралешовных труб и стальных радиаторов отопления.
Основные параметры линий. Основными параметрами механизированных и автоматических линий являются ритм линии, такт выпуска и общая продолжительность производственного цикла. Под ритмом (производительностью) линии понимается количество продукции, выпускаемой в единицу времени. Часовая производительность Q линии определяется по формуле
Q = 60/t,
(9.1)
где t — такт выпуска, мин.
Такт выпуска — это интервал времени, через который периодически производится съем готовых изделий с линии. При проектировании линий такт t выпуска определяется по формуле
t = 60Fh/N,
(9.2)
где Ф — действительный (расчетный) годовой фонд времени оборудования, ч; h — коэффициент использования действительного фонда времени, учитывающий неизбежные простои линии из-за неполадок, повреждений и настроек, h = 0,7…0,9; N — годовая программа выпуска сварных изделий, шт.
Промежуток времени t между последовательными передачами равных количеств nт (транспортных партий) продукции с одного рабочего места линии на другое определяется по формуле
t = tnt.
(9.3)
У линий с жесткой связью и последовательным расположением оборудования этот промежуток времени равен такту. У линий с жесткой связью и последовательно-параллельным расположением оборудования на разветвленных участках промежуток времени t составляет
t = ti,
(9.4)
где i — число параллельных рабочих ветвей линии.
Продолжительность производственного цикла линии равна времени Т прохождения изделия по линии (от подачи заготовок или сырьевого материала на первое рабочее место до съема готового изделия с последнего рабочего места). Для линии с жесткой связью и последовательным расположением оборудования
T = tn,
(9.5)
где n — число рабочих мест.
9.6Комплексно-механизированные и комплексно-автоматизированные линии
Поточные линии. Поточная линия — это комплекс оборудования, взаимно связанного и работающего согласованно, с определенным заданным тактом, в рамках единого технологического процесса. Поточные линии используются в массовом производстве для изготовления однотипных сварных деталей. При этом размеры деталей могут варьироваться в широком диапазоне.
Комплексно-механизированная поточная линия для сборки и сварки листовых полотнищ относится к линиям с жесткой связью, прерывистым технологическим процессом и последовательно-параллельным расположением оборудования. На линии полотнища собираются из отдельных листовых заготовок и сворачиваются в транспортабельные рулоны. Ширина полотнищ 11920…17880 мм, толщина листов 4…16 мм, ширина 1490 мм, длина 5990 мм. Полотнища, свернутые в рулоны диаметром, не превышающим ширину железнодорожного вагона, перевозят на место установки, где из них сваривают резервуары объемом 5…20 тыс. м3.
Линия состоит из двух ярусов. На верхнем ярусе производятся сборка полотнища, сварка (без прижимов) наружными поперечными и продольными швами (наружные швы резервуара), на нижнем — сварка внутренними поперечными и продольными швами (внутренние швы резервуара). Контроль швов и исправление дефектов выполняются на обоих ярусах линии.
Линия работает следующим образом. Предварительно выправленные листы с обработанными кромками загружаются цеховым мостовым краном в секционный склад. Порядок раскладки листов определяется конструкцией полотнища. Из склада листы захватываются вакуумными захватами самоходной тележки, которая перевозит их на верхний ярус. Подъем захватов осуществляется пневмоцилиндрами. Разложенные на месте сборки листы с помощью отводного бокового упора и бокового толкателя собираются поперек направления стыков. После этого листы задним толкателем (прижимом) досылаются до задней кромки ранее собранной части полотнища. При этом задний толкатель выравнивает задние кромки собираемых листов, сдвинутых к торцу собранной части полотнища. Кромки листов прижимаются к медной подкладке, расположенной на верхней тележке для поперечной сварки, двумя рядами клавишных пневмоприжимов тележки (с усилием до 40 кН на 1 м кромки).
Сварка под слоем флюса наружными продольными и поперечными швами выполняется одновременно двумя двухдуговыми сварочными аппаратами, перемещающимися на тележках.
Сварка продольными швами начинается от середины привариваемой части до середины ранее приваренной части через предыдущий поперечный шов. Тележки перемещаются поперек полотнища, и каждая устанавливается над местом сварки. Следующий участок служит для визуального контроля выполненных швов и исправления дефектов.
Затем полотнище огибает барабан, переворачиваясь при этом на 180°, и попадает на нижний ярус. Здесь одновременно со сваркой на верхнем ярусе выполняется сварка внутренними продольными и поперечными швами тем же способом и аналогичными сварочными аппаратами. На следующем участке нижнего яруса выполняется контроль герметичности швов и исправление дефектов.
Таким образом, на линии одновременно выполняется сварка четырьмя сварочными аппаратами четырех швов.
В процессе изготовления полотнище передвигается сворачивающим устройством, расположенным в конце нижнего яруса. Сворачивающее устройство снабжено приспособлением и механизмами для съема готового рулона и перекатки его на транспортную платформу.
Комплексно-механизированная поточная линия для изготовления прямошовных труб из листа (рис. 9.7) состоит из пяти участков: заготовки листа, формообразования, сварки наружными швами, сварки внутренними швами, контроля и отделки труб. На линии изготовляются трубы диаметром 529…820 мм и длиной до 12 м из листа толщиной 6…12 мм.
Рис. 9.7.Технологическая схема линии для изготовления прямошовных труб из листа:
1 — складирование листа; 2 — подача листа; 3 — правка листа; 4 — строгание кромок листа; 5 — подгибка кромок; 6 — предварительное формообразование заготовок; 7 — окончательное формообразование заготовок; 8 — сварка наружным швом; 9 — сварка внутренним швом; 10 — отрезка кратерных участков и торцовка труб; 11 — снятие выпуклости внутреннего шва; 12 — раздача и гидроиспытание; 13 — складирование труб
На участке заготовки листы магнитами листоукладчика подаются на приводной роликовый конвейер, по которому поступают в листоправильные вальцы. Затем лист передается в кромкострогальный станок для двухстороннего строгания кромок со снятием фасок под шов. Во время строгания лист перемещается приводными валками вдоль неподвижных резцов станка. После этого гильотинные ножницы обрезают обе торцовые кромки листа. Часть поверхности листа (пњлосы шириной 50…70 мм вдоль края верхней и нижней продольных кромок) подвергается дробеметной очистке.
Подготовленный лист поступает на участок формообразования для подгибки продольных кромок, предварительного формообразования на валковой машине и окончательного формообразования на гидравлических прессах.
После этого труба передвижными рольгангами подается на участок сварки наружными швами, состоящий из нескольких параллельно расположенных трубосварочных станов. Сборка и сварка наружным швом производятся одновременно на непрерывной валковой машине, которая в процессе сварки обжимает трубу, плотно прижимает свариваемые кромки друг к другу и со скоростью сварки перемещает трубу. Сварочный аппарат при этом неподвижен. Прихватка кромок перед сваркой не требуется. Для сварки на медной скользящей подкладке (башмаке) используется трехдуговой сварочный аппарат А-688. Флюсовая аппаратура обеспечивает в процессе работы подачу, удержание и удаление флюса из зоны сварки, а также отсос газа и пыли. Для направления электрода по стыку линия оснащена следящими системами.
Внутренний шов выполняется аппаратами А-850, укрепленными на длинных штангах. В процессе сварки труба на специальной тележке с роликовыми опорами перемещается со скоростью сварки на штангу. После сварки труба возвращается в исходное положение. Наружные и внутренние швы выполняются при скоростях 100…200 м/ч в зависимости от толщины стенки трубы. Поскольку скорость сварки внутренними швами меньше, чем наружными, число трубосварочных станов для сварки внутренними швами увеличено до пяти, что обеспечивает заданный ритм линии.
После сварки труба поступает на участок отделки, где ее внутреннюю полость очищают от остатков флюса, шлака и окалины. Затем труба проходит ультразвуковой контроль и возвращается на участок отделки. Там она подвергается осмотру и (при необходимости) вырубке, заварке и зачистке дефектов сварных швов. На участке отделки выполняются также плазменная отрезка концов труб и снятие выпуклости внутренних сварных швов на расстоянии до 300 мм от обрезанных торцов (на специальных фрезерных станках). Далее труба поступает в пресс-расширитель для правки, калибровки и гидравлического испытания. Калиброванная труба возвращается на участок контроля для рентгенодефектоскопии концевых участков швов, снятия фаски на торцах труб и маркировки.
По компоновке линия относится к линиям с гибкой связью, поскольку между отдельными агрегатами имеются склады-накопители. Часть агрегатов (листоправильные вальцы, кромкострогальный станок, валковый стан для подгибки продольных кромок, трубосварочные станы наружной сварки) работают при непрерывном движении обрабатываемого изделия, остальные агрегаты — при неподвижном положении изделия. Таким образом, линия по признаку непрерывности является смешанной — частично с непрерывным, частично с прерывистым технологическим процессом. По пространственному расположению оборудования линия относится к последовательно-параллельным. Линия характеризуется высоким уровнем комплексности механизации и автоматизации, т. е. охватывает полный комплекс операций технологического процесса — от подачи заготовки на линию до отделки готового изделия. Годовая производительность линии при производстве труб диаметром 820 мм — до 800 тыс. т в год.
Поточная линия для изготовления спиралешовных труб из полосы показана на рис. 9.8. Линия предназначена для изготовления труб диаметром 1020 мм из полосы толщиной до 12 мм. Всю линию можно условно разделить на участок подготовки полосы и формовочно-сварочный стан. Все оборудование для подготовки полосы установлено стационарно на фундаментах, а формовочно-сварочный стан — на поворотном мосту.
Рис. 9.8.Технологическая схема поточной линии для изготовления спиралешовных труб из полосы:
1 — разматыватель; 2 — правиґльная машина; 3 — гильотинные ножницы; 4 — сварочная машина; 5 — подающие ролики; 6 —петлеообразователь; 7 — дисковые ножницы с кромкокрошителем; 8 — подающая машина; 9, 11 — внутренняя и наружная сварочные головки; 10 — формовочная машина; 12 — «летучий» отрезной станок; 13 — поворотный мост
Стальные рулоны массой до 10 т, наружным диаметром до 1650 мм разматываются в полосу, направляемую подающими роликами разматывателя в машину для правки. Выправленная полоса поступает в гильотинные ножницы, где обрезаются задний конец предыдущей полосы и передний конец последующей. Эти концы свариваются на сварочной машине способом электродуговой сварки под слоем флюса односторонним швом на медной цилиндрической подкладке. Совмещение свариваемых концов обеспечивается вертикальными направляющими роликами, расположенными с обеих сторон от сварочной машины. При сварке концы ленты зажимаются поперечными балками с гидроцилиндрами; медный башмак поджимается к стыку клиновым прижимом с пневмоприводом.
После сварочной машины на линии также установлены подающие ролики для перемещения полосы. Скорость сварки составляет 60 м/ч. Сварка выполняется без технологических планок, так как дефектный начальный участок шва выводится на край полосы, который в дальнейшем обрезается дисковыми ножницами.
Наличие компенсирующей петли длиной до 22 м, образующейся в петлеобразователе, куда поступает сваренная полоса, обеспечивает непрерывность формообразования и сварки. Петлеобразователь представляет собой яму глубиной 36 м с направляющими роликами на входе и выходе. Полоса получает равномерный изгиб в пределах упругих деформаций.
При остановке механизмов, расположенных до петлеобразователя (при обрезке концов и при сварке), механизмы, расположенные после него, продолжают работать, и петля сокращается.
После обрезки и сварки концов остановленные подающие механизмы опять включаются и полоса до петлеобразователя продолжает прерванное движение со скоростью, большей, чем скорость после петлеобразователя. Размер петли увеличивается, постепенно достигая максимальной величины. После этого скорость движения полосы до петлеобразователя автоматически замедляется до скорости движения после петлеобразователя, т. е. становится равной скорости сварки спиральным швом. В яме петлеобразователя установлено фотореле, контролирующее размеры петли и регулирующее скорость подающих роликов.
В настоящее время работают линии, в которых обрезка концов и сварка ленты осуществляются передвижными («летучими») машинами, и необходимость использования петлеобразователя отпадает.
«Летучие» машины перед началом сварки специальными зажимными устройствами сцепляются с лентой и перемещаются вместе с ней до завершения сварки, после чего отцепляются от ленты и возвращаются в исходное положение. Таким образом, неподвижность ленты не требуется. «Летучие» машины применяются в линиях с непрерывным процессом, в которых направление рабочего движения не совпадает с направлением движения изделия.
Затем полоса по направляющим роликам попадает в дисковые ножницы, обрезающие кромки шириной 15…25 мм с обеих сторон полосы, что обеспечивает точный размер полосы по ширине. Обрезанные кромки подаются к кромкокрошителю, где разрезаются на полуметровые куски. После ножниц ровная полоса по направляющим вертикальным роликам поступает к подающей машине. Эти направляющие ролики точно ориентируют обрезанную полосу относительно ножей дисковых ножниц, что обеспечивает прямолинейность полосы. Необходимость этой операции продиктована тем, что черная (необрезанная) полоса до дисковых ножниц проходит через ролики, только грубо ориентирующие ее, поскольку для исключения заклинивания полосы они установлены с гарантированным зазором (с учетом плюсового допуска на ширину заготовки).
Движение полосы от образования петли до съема сваренной трубы обеспечивает четырехвалковая подающая машина. Нижние ее валки стационарные, верхние (подвижные) закреплены на качающихся рычагах, шарнирно связанных с гидроцилиндрами. Подвижное крепление верхних роликов обеспечивает проход через машину трубы с еще не снятой выпуклостью сварного стыкового шва, сохраняя при этом необходимое тяговое усилие.
Пройдя все эти механизмы, полностью подготовленная полоса поступает во втулку формовочной машины, насаженную на ось поворота выходного моста. Эта ось находится на линии пересечения в плане оси участка подготовки полосы с осью трубы.
На внутренней поверхности втулки формовочной машины по спирали наплавлены и отшлифованы пояски из твердого сплава, которые вместе с регулируемыми роликами формируют спираль из полосы. Сварка спиральной полосы в трубу производится под слоем флюса тремя швами — двумя внутренними и одним наружным. Вначале накладывается первый внутренний (технологический) шов, через полвитка — наружный шов, еще через полвитка — второй внутренний (перекрывающий) шов. Первый шов является по существу сборочным швом: он обеспечивает жесткое соединение свариваемых кромок, что устраняет возможность их взаимного смещения при сварке основными швами. В результате предотвращается образование горячих трещин в шве. Скорость сварки до 120 м/ч.
Несмотря на обрезку кромок, небольшая серповидность полосы имеет место и влияет на величину зазора между кромками. Для его регулирования необходимо немного изменить угол формообразования (в пределах ±0,5°) путем поворота моста с формовочно-сварочным станом.
Внутренние швы выполняются сварочным аппаратом У-124 — самоходной тележкой с длинной штангой, на которой закреплены две сварочные головки. Аппарат перемещается по направляющим поворотного моста. Подача флюса к сварочным головкам (находящимся внутри трубы) от флюсоаппарата (расположенного на тележке) производится ленточным конвейером внутри штанги. Наружный шов выполняется сварочным аппаратом А-807, закрепленным на стойке поворотного моста.
Сваренная труба попадает на приводные отводящие ролики, расположенные на поворотном мосту. Здесь же находится «летучий» отрезной станок для плазменной резки трубы на мерные части, установленный на тележке, перемещающейся по рельсам вдоль трубы. В месте разрезания вращающаяся обойма станка специальным гидравлическим механизмом прочно закрепляется на трубе, и станок перемещается поступательно вдоль оси трубы вместе с ней. Резак, установленный на раме станка, отрезает трубу за один ее оборот. Одинаковая скорость перемещения станка и трубы (поскольку станок закреплен на трубе) обеспечивает строгую перпендикулярность реза к оси трубы.
Отрезанная труба по рольгангу поступает на участок отделки, а станок на повышенной скорости возвращается в исходное положение. Затем качество спирального шва трубы по всей длине проверяется ультразвуком (на потоке) и производится рентгеноскопия обнаруженных дефектных мест (на участке отделки). Там же проводится гидравлическое испытание всех готовых труб.
Линия — автоматическая, поскольку большинство операций выполняется без участия человека. В то же время на основной операции — сварке необходимо присутствие рабочих для наблюдения за процессом и его регулирования, что является серьезным недостатком линии. В настоящее время ведутся работы по замене электродуговой сварки индукционной сваркой токами высокой частоты, что позволит полностью автоматизировать весь процесс изготовления труб, значительно увеличить скорость сварки (до 15…25 м/мин), а также улучшить условия труда благодаря отсутствию вредных газов и флюсовой пыли. Кроме того, отпадет необходимость в сварочных материалах — проволоке и флюсе.
Комплексно-механизированная поточная линия для изготовления кабин грузовых автомобилей состоит из двух параллельных сборочных ветвей и одной сварочной ветви.
Кабина представляет собой сложную пространственную конструкцию из тонколистовой стали. Для обеспечения механизации сборки кабина разбита на семь основных сварных узлов: передняя часть кабины, пол, каркасы боковин (правый и левый), каркас задней части, панель задней части, крыша.
Каждая сборочная ветвь состоит из двухпозиционной многоэлектродной сварочной машины и четырех последовательно расположенных сборочных кондукторов, соединенных между собой тележечно-шаговым конвейером. Сборочные кондукторы оборудованы мощными пневматическими зажимными устройствами, обеспечивающими точность и стабильность геометрических размеров кабины. Между всеми рабочими местами находятся промежуточные позиции. Между первой сборочной и сварочной ветвями находится загрузочное рабочее место, связанное со второй сборочной ветвью поперечным конвейером. Сварочная ветвь линии состоит из четырех многоэлектродных многотрансформаторных машин, расположенных последовательно и связанных между собой тележечно-шаговым конвейером.
Линия работает следующим образом. Пол кабины подвесным толкающим конвейером подается с линии сборки и сварки пола к многоэлектродной сварочной машине. Туда же другим подвесным толкающим конвейером подается передняя часть кабины. Оба сварных узла снимаются двумя рабочими с подвесного конвейера и укладываются на приспособления машины, где фиксируются по технологическим отверстиям, что обеспечивает их правильное взаимное расположение. На машине сваривается 50 точек. После сварки пол и передняя часть кабины подаются тележечно-шаговым конвейером к одному из сборочных кондукторов, где их собирают с обоими каркасами боковин. Затем конструкция поочередно передается на последующие рабочие места, где к ней крепятся на прихватках три оставшихся сварных узла: каркас задней части, панель задней части и крыша — каждый в отдельном кондукторе.
На каждом рабочем месте имеется подъемный стол, при ходе которого вверх поступающее в кондуктор изделие снимается с конвейера и подается в рабочую зону. На рабочей поверхности подъемных столов имеются конусные фиксаторы, на которые кабина устанавливается технологическими отверстиями пола, что обеспечивает точную фиксацию кабины по постоянным базам на всех рабочих местах. Собранные на обеих сборочных ветвях кабины поступают поочередно на многоэлектродные машины: с одной ветви — напрямую, с другой ветви — по поперечному конвейеру. Там каждая кабина сваривается 274 точками. После сварки готовая кабина автооператором снимается с линии и устанавливается на отделочный конвейер для грунтования и окраски.
Многоэлектродная машина состоит из портальной станины, подъемного стола с конусными фиксаторами и нескольких сварочных клещей, закрепленных шарнирно на траверсах. Клещи — самоустанавливающиеся, с гидроприводом электродов. Ограничительные упоры клещей обеспечивают правильную их установку относительно кромок свариваемых деталей. Траверсы с клещами подводятся к изделию цилиндрами. На траверсах расположены также малогабаритные сварочные трансформаторы, которые задействуются одновременно несколькими группами. Последовательность их включения обеспечивается электронной схемой управления. При этом выполняются необходимые блокировки (движение траверс возможно только при разжатых электродах) во избежание поломки электродов и повреждения изделия. На верхней части станины размещаются электрошкафы управления, станции гидропривода и другие вспомогательные устройства.
Сварочная ветвь линии работает без участия операторов и может рассматриваться в качестве автоматической линии с параллельно-последовательным расположением, жесткой связью, прерывистым технологическим процессом, сквозным транспортом. Недостатком линии является необходимость присутствия рабочих на сборочных стендах (для загрузки сварных узлов кабины и для постановки прихваток). В настоящее время намечается использование роботов на операциях сборки подобных изделий.
Автоматическая поточная линия для изготовления автомобильных колес отличается высокой надежностью, которая объясняется тем, что наиболее сложная и ответственная операция (сварка) производится на четырех параллельных автоматах и вероятный кратковременный выход из строя одного из них не нарушает работу всей линии.
Колесо состоит из двух деталей — штампованного диска и сварного обода. На линии выполняются сборка диска с ободом, сварка диска с ободом (электродуговая под слоем флюса), очистка сварного шва от шлака, пробивка ниппельного отверстия, зачистка заусенцев на кромках пробитого отверстия, визуальный контроль сваренного колеса, исправление дефектов, погрузка готового колеса на главный конвейер цеха.
В линию входит следующее основное технологическое оборудование: пресс для запрессовки диска в обод, четыре автомата электродуговой сварки под слоем флюса, автомат для очистки шлака, пресс-автомат для пробивки ниппельного отверстия, автомат для зачистки заусенцев. Транспортирование колеса между рабочими местами осуществляется несколькими конвейерами разных типов: ленточными, наклонными роликовыми, катковыми, роликовыми, штанговыми и конвейером возврата (роликовым).
Линия работает следующим образом. Собранное на прессе колесо по наклонному роликовому конвейеру поступает в накопитель. Далее колесо попадает на основной (штанговый) конвейер, приводимый в действие двумя пневмоцилиндрами и доставляющий колеса к сварочным автоматам. Наличие накопителя в составе линии обусловлено тем, что управление прессом не автоматизировано и необходимо обеспечить ритмичность поступления колес на основной конвейер. Скорость накопителя значительно выше средней скорости движения колес на линии, благодаря чему в его головной части всегда имеется запас собранных колес. Конструкция основного конвейера обеспечивает возможность свободного прокручивания нагруженных роликов и пробуксовки изделий на месте, что предохраняет конвейер от перегрузки, но обеспечивает его равномерную непрерывную загрузку.
Такт выпуска линии — 15 с. Сварка каждого колеса вместе с подготовкой занимает 1 мин. Этим и объясняется установка на линии четырех сварочных автоматов. С конвейера колеса подаются толкателями к автоматам попарно — сначала к первому и третьему, через 30 с — ко второму и четвертому и т. д. Соответствующее расположение автоматов и синхронность работы основного конвейера и толкателей обеспечивают постоянную равномерную загрузку всех четырех сварочных автоматов и подачу к ним всех колес, попадающих на основной конвейер. Величина перемещения колес за каждый ход (размер шага) составляет 600 мм. В случае остановки или нарушения работы части сварочных автоматов колеса, оставшиеся на основном конвейере, автоматически перегружаются в конце его на роликовый конвейер возврата, который устроен аналогично основному конвейеру и выполняет функции накопителя. По нему несваренные колеса попадают к началу потока, где по мере накопления перегружаются прессовщиком обратно на основной конвейер с помощью специального пневматического подъемника. В отличие от основного конвейера на роликовом конвейере возврата колеса передвигаются не плашмя, а в вертикальном положении. Поданное толкателем к сварочному автомату колесо после сварки попадает на штанговый конвейер, передающий его на последующие операции.
Колесо, не попавшее на сварочный автомат, по роликовому конвейеру передается на основной конвейер линии. Для сбора шлака имеются лотки и ленточный конвейер, расположенный под основным. Роликовый конвейер возврата передает сваренные колеса сначала на автомат для очистки шва от шлака, затем на автомат для пробивки ниппельного отверстия. Перед этим колеса правильно ориентируются специальным механизмом, так как ниппельное отверстие должно быть расположено определенным образом по отношению к отверстию для рук в диске колеса.
После пробивки отверстия колесо тем же конвейером подается к автомату для зачистки заусенцев, а затем на рабочее место для контроля. После визуального контроля, для облегчения которого имеется специальный подъемник с поворотным диском, годные колеса по поперечному рольгангу передаются на роликовый конвейер возврата, а колеса с дефектами — на рабочее место для исправления ручной дуговой сваркой. Исправленное колесо передается на вспомогательный конвейер (штанговый), который состоит из четырех самостоятельных параллельных ветвей, подающих готовые колеса на основной конвейер линии.
Колеса навешиваются на крючья основного конвейера посредством четырех пневмоподъемников, установленных в конце каждой его ветви.
Управление штанговыми конвейерами и толкателями осуществляется централизованно от электрического командоаппарата. Все автоматы управляются по принципу путевого контроля, при этом автоматы, установленные на конвейере, работают с ним в едином такте. Подъемники готовых колес управляются рабочим с помощью педали. Роликовые конвейеры включены непрерывно в течение всего времени работы линии.
Сварочный автомат состоит из подъемника с пневмогидроприводом, вращателя с фрикционным диском, сварочной головки и аппарата для подачи и сбора флюса. Поступившее в автомат колесо из исходного положения поднимается в рабочее положение подъемником. При этом автоматически включается электродвигатель вращателя, и колесо, прижатое к фрикционному диску, начинает вращаться. В это же время начинается подача флюса, и через некоторое время включается сварочная головка. В течение всего оборота колеса производится сварка, затем путевое реле переключает привод подачи проволоки в обратную сторону и сварочная дуга разрывается. Подача флюса при этом прекращается, а отсос его продолжается еще некоторое время, пока вращается колесо. Затем колесо опускается в исходное положение.
В одну смену на линии занято восемь человек: три наладчика, подсобный рабочий (контролирующий наличие сварочной проволоки и флюса), контролер, рабочий на исправлении дефектов, прессовщик, рабочий на погрузке готовых колес.
Комплексно-автоматизированная поточная линия для изготовления радиаторов отопления (рис. 9.9) — одна из наиболее совершенных в сварочном производстве — характеризуется полной автоматизацией всех технологических операций и управления, обслуживается двумя операторами-наладчиками. Кроме сборочных и сварочных операций на линии выполняются заготовительные и отделочные операции. Технологический процесс — непрерывный на всех операциях, в том числе заготовительных.
Рис. 9.9.Комплексно-автоматизированная поточная линия для изготовления радиаторов отопления:
1 — разматыватель; 2 — двухъярусная формовочная машина; 3 — контактная машина для приварки штуцеров; 4 — контактная машина для точечной сварки соединений между каналами; 5 — контактная машина для сварки продольными швами; 6 — «летучая» контактная машина для сварки поперечными швами; 7 — «летучие» гильотинные ножницы
Из тонколистовой рулонной стали толщиной 1,5 мм и шириной 600…650 мм изготовляются радиаторы панельного типа, состоящие из двух штампованных листов с гофрами, образующими после сварки зигзагообразный канал для горячей воды. Длина радиаторов составляет 545…1190 мм. К одной из панелей привариваются два присоединительных штуцера.
В начале линии имеется накопитель для рулонов. Движение изделия осуществляется приводными тянущими валками, расположенными между рабочими местами линии. В конце линии установлены гильотинные ножницы для обрезки продольных кромок и пресс для гидроиспытаний.
Линия работает следующим образом. Два рулона стальной полосы цеховым краном подаются в накопитель, откуда поступают в разматыватель 1. Из разматывателя обе полосы подаются в двухъярусную формовочную машину 2, где происходит формообразование (выдавливание гофров). Эта операция, как и все последующие технологические операции (до отрезки панелей от полосы), выполняется при непрерывном движении полосы. Цилиндрические поверхности двух пар вращающихся синхронно валков-штампов (по паре на каждую полосу) имеют соответствующие выступы и углубления.
После формообразования верхняя полоса поступает в контактную машину 3 для приварки штуцеров. При подходе выступа очередной панели конечный выключатель задействует специальное зажимное устройство и машина 3, сцепленная с полосой, передвигается вместе с ней, выполняя следующие операции: автоматическая подача двух штуцеров к полосе, контактная стыковая сварка оплавлением штуцеров с полосой, пробивка отверстий в полосе по внутренним отверстиям приваренных штуцеров, развальцовка отверстий. Такая технология обеспечивает полное совпадение отверстий в полосе и штуцерах.
После выполнения всех операций машина 3 отцепляется от полосы и возвращается в исходное положение специальным механизмом. Затем полосы поступают в контактную точечную машину 4 для точечной сварки соединений между каналами. Отсюда ленты поступают в контактную машину 5, где свариваются двумя продольными швами по кромкам полосы. Сварка выполняется двумя парами холостых контактных роликов, получающих вращение от движущейся полосы.
После сварки продольными швами полоса поступает в контактную машину 6 для сварки поперечными швами. Направление сварки не совпадает с направлением движения полосы, поэтому машина выполнена подвижной. Затем подвижными гильотинными ножницами 7 сваренная полоса разрезается на отдельные радиаторы. Гильотинные ножницы используются также для обрезки продольных кромок. Готовые радиаторы подвергаются гидроиспытаниям в многопозиционном прессе, откуда подаются на окраску.
Скорость движения полосы на линии регулируется в пределах 1,5…2 м/мин. Годовая производительность линии — 500 тыс. радиаторов.
Принципы работы линии для изготовления радиаторов отопления могут быть применены в линиях для изготовления других аналогичных изделий из тонколистовой рулонной стали.
Роторные линии. Роторная линия — это коплекс машин (роторов), транспортных средств и приборов, объединенных системой автоматического управления, в котором обрабатываемые изделия совершают движение по дугам окружностей вместе с обрабатывающим их инструментом. Роторные линии целесообразно использовать в массовом и крупносерийном производстве для изготовления сравнительно несложных малогабаритных изделий при небольшом числе операций и при необходимости высокой производительности.
В обычных автоматических линиях технологические операции выполняются на постоянных рабочих местах, расположенных на определенном участке линии. При этом изделие перемещается относительно неподвижного инструмента (либо другого рабочего органа) или останавливается для обработки движущимся инструментом.
Таким образом, имеет место относительное перемещение инструмента по отношению к изделию, а операция производится на одном и том же месте. На роторных же линиях изделия на каждой операции в процессе обработки перемещаются в пространстве вместе с инструментом, и обработка происходит во время этого перемещения. Роторные автоматические линии являются линиями с безостановочным движением, что характеризует их высокий класс.
Роторная автоматическая линия (рис. 9.10) состоит из нескольких рабочих роторов. По окружности каждого ротора выполнено некоторое число гнезд для размещения изделий. Гнезда представляют собой движущиеся рабочие места. Поскольку в каждом роторе выполняется определенная операция, то все гнезда этого ротора оснащены одним и тем же рабочим инструментом. В этом случае число роторов соответствует числу технологических операций, производимых на линии. Число гнезд в каждом роторе зависит от длительности выполняемой в нем операции: чем она больше, тем больше гнезд в роторе. Отсюда следует важное преимущество роторных линий — возможность применения их в тех случаях, когда в процессе изготовления изделия выполняются разные по длительности операции. Часто между рабочими роторами устанавливают транспортные роторы, служащие для передачи изделий с одного рабочего ротора на другой.
Рис. 9.10.Схема роторной автоматической линии
Иногда гнезда рабочего ротора оборудуют несколькими инструментами, которые задействуются в определенной последовательности. Это позволяет в одном роторе выполнять несколько операций, а иногда и весь технологический процесс. В последнем случае линия сводится к одному ротору, представляющему собой самостоятельный многоместный автомат. Именно таким является сборочно-сварочный роторный автомат для сборки и сварки тракторных катков.
Каток состоит из двух половин, сваренных кольцевым швом. Основная часть автомата — шпиндель с многоместной планшайбой. На планшайбе закреплены зажимные приспособления, в которых находятся свариваемые катки. Над катками расположены сварочные головки с катушками для проволоки и флюсоподающими трубками. Заготовки катков поступают к автомату по лотковому устройству, откуда специальным автооператором подаются в одно из сборочных зажимных приспособлений, установленных на планшайбе.
В зажимных приспособлениях заготовки получают вращение. При этом включается сварочная головка, возбуждается дуга и подается флюс. Сварка прекращается, когда каток совершит полный оборот вокруг своей оси. После этого каток освобождается и выгружается в приемное устройство. Загрузка и выгрузка происходят во время движения ротора. Верхняя часть полого шпинделя используется для отсоса газа из зоны сварки. Часовая производительность автомата составляет 150 катков, скорость сварки — до 1 м/мин, частота вращения ротора — 0,8 мин-1.
Недостатком роторных линий является их сложность и меньшая надежность по сравнению с обычными станками-автоматами, связанная с большим числом движущихся частей. Эти обстоятельства сдерживают широкое распространение роторных линий в сварочном производстве.
9.7Промышленные роботы и роботизированные комплексы
Роботами называют манипуляторы с программным управлением, которое является главным признаком автоматизации ручных операций и обеспечивает освобождение человека от двигательных и управляющих функций по перемещению объектов производства и технологической оснастки.
Различают жесткопрограммируемые и гибкопрограммируемые промышленные роботы. Жесткопрограммируемые роботы выполняют неизменные, заранее заданные движения, которые в большинстве случаев сравнительно просты и постоянно повторяются в течение относительно длительного времени. Они часто имеют небольшое число степеней свободы и сравнительно дешевы. Гибкопрограммируемые роботы способны выполнять более сложные движения, поскольку обладают большим числом степеней свободы и объем памяти их систем управления больше. Программы управления этими роботами могут быстро корректироваться. Эти работы более дорогие.
На рис. 9.11 приведена общая классификация промышленных роботов сварочного производства.
Рис. 9.11.Общая классификация роботов сварочного производства
Широкое внедрение робототехники в промышленность дает ряд экономических и социальных эффектов.
К экономическим эффектам относятся: экономия рабочих площадей; высвобождение рабочих, которые могут быть использованы в другом производстве, где ручной труд незаменим; повышение производительности в результате более эффективного использования мощности оборудования; повышение коэффициента использования оборудования; повышение качества продукции, уменьшение брака и объема работ по его исправлению; сокращение длительности производственного цикла и вспомогательного времени благодаря непрерывности технологического процесса; уменьшение оборотных средств.
К социальным эффектам от применения робототехники относятся: исключение человека из процессов, связанных с воздействием агрессивных сред, высоких температур и других факторов, отрицательно влияющих на его здоровье; освобождение человека от монотонного и утомляющего труда; освобождение человека от работ, связанных с перемещением тяжелых грузов или преодолением больших расстояний; независимость человека от такта производства; исключение несчастных случаев.
Суть применения промышленного робота для сварки состоит в том, что субъективный элемент (человек) исключается из процесса, и искусство квалифицированного сварщика заменяется последовательностью программируемых элементарных операций, позволяющих с достаточной точностью воспроизвести требуемый процесс сварки. При этом необходимо обеспечить сварку при любой конфигурации шва с учетом его геометрии и ограничений сварочного процесса.
Выполняя перемещения сварочного органа вместо человека, промышленный робот совершает их отличным от человека образом, поскольку возможности робота и человека различны. Так, выполняя точечный шов одноточечной подвесной машиной, сварщик перемещает автоматически работающие клещи вдоль линии шва с некоторой средней скоростью, выбранной им из расчета заданного расстояния между сварными точками. Он не пытается (и не в состоянии) задать точное положение каждой свариваемой точки. Движение клещей происходит рывками, прерываясь при сжатии электродов. Сила сжатия зависит от упругости мышц и тактильной чувствительности сварщика. К тому же разброс и пропуски сварных точек, допускаемые сварщиком, вынуждают предусматривать большее число сварных точек, чтобы обеспечить требуемую прочность сварного соединения.
Промышленный робот, выполняя ту же операцию, последовательно перемещает сварочные клещи от точки к точке, останавливая их в заданной позиции до начала сжатия электродов. Точное позиционирование сварных точек промышленным роботом позволяет обойтись значительно меньшим их количеством, хотя в данном случае движения робота оказываются менее целесообразными.
Далеко не всякий промышленный робот, способный выполнять транспортные операции, пригоден для сварки. Здесь необходима специализированная конструкция, обладающая универсальностью, способная обеспечить быструю переналадку с одного изделия на другое и вести сварку в любом направлении, выполняя любую из сварочных операций данного вида.
Специализация робота состоит не только и не столько в передаче промышленному роботу функций управления технологическими параметрами сварочного процесса, сколько в учете особенностей совершения роботом его основных движений при сварке.
К сварочному промышленному роботу предъявляются некоторые общие требования:
§ высокоразвитая система управления, способная обеспечить регламентированное движение исполнительного органа робота одновременно по нескольким координатам;
§ повышенная жесткость механической конструкции робота;
§ простая и точная система обучения робота, позволяющая ограничить количество субъективных ошибок, совершаемых наладчиком при обучении робота;
§ высокая надежность устройства управления и устойчивость его к сильным импульсным помехам, возникающим при работе сварочных аппаратов;
§ адаптация к отклонениям пространственного расположения и позиционирования заготовки от заданных значений.
При разработке сварочного промышленного робота необходимо иметь полное представление об объектах, с которыми ему придется иметь дело, и о технологии сварочного процесса. Естественно, что оптимальное решение конструкции робота окажется специфичным для каждого вида сварки.
Возможности комплексной автоматизации производства сварных конструкций значительно расширяются с использованием сварочных роботов. Обычная машина-автомат является специальным устройством для сварки одного вида деталей. Сварочный робот — это универсальная быстропереналаживаемая машина-автомат с программным управлением. По эффективности действия он не уступает специальным сварочным машинам-автоматам, но в отличие от них после окончания заданной работы может быть быстро переналажен на выполнение другой работы.
Сварочные роботы позволяют автоматизировать операции, которые до последнего времени не поддавались механизации (либо их механизация оказывалась экономически нецелесообразной). Так, роботы эффективно применяются при выполнении коротких и труднодоступных швов, а также при сварке изделий в мелкосерийном производстве. Наряду с этим роботы позволяют освободить человека от монотонного, тяжелого, утомительного, вредного и опасного труда.
Сварочный робот состоит из собственно робота (или манипулятора) и пульта управления. Робот имеет подвижную руку и шарнирную кисть с захватом, в котором закрепляется исполнительный орган: сварочные клещи (при контактной точечной сварке) или сварочная горелка (при дуговой сварке). Сварочные роботы имеют 4—6 степеней свободы (движений). Большинство сварочных роботов имеет 5 степеней свободы: три движения руки и два движения кисти. Комбинация этих движений позволяет устанавливать сварочные клещи или горелку в любых направлениях и положениях в пределах зоны действия робота. Набор видов движений (рис. 9.12) при одинаковом их числе может быть разным и зависит от конструкции робота.
Рис. 9.12.Виды движений робота:
а, б — два положения руки; 1 — выдвижение руки; 2 — наклон руки относительно горизонтальной плоскости; 3 — вертикальное перемещение руки; 4 — поворот руки; 5 — сгибание кисти; 6 — поворот кисти; 7 — вращение захвата; 8 — поперечное перемещение корпуса; 9 — продольное перемещение корпуса; 10 — разжим-зажим захвата
В качестве приводов движений робота в большинстве случаев используют электрогидравлические приводы.
В настоящее время наибольшее распространение получили две конструктивные схемы сварочных роботов: с перемещением руки в сферической системе координат (роботы типа Unimate, США), схема движений которого приведена на рис. 9.13; с перемещением руки в прямоугольной системе координат (роботы типа Nachi, Япония), схема движений которого приведена на рис. 9.14. Для управления роботами применяются позиционная (от точки к точке), контурная (плавная) или смешанная системы управления, обеспечивающие движение исполнительного органа одновременно по нескольким (или всем) координатам. Запись программы работы робота осуществляется двумя способами: при обучении робота во время первого прохода, выполняемого вручную или с помощью клавишного командного устройства; с применением внешней системы управления.
Рис. 9.13.Схема движения робота типа Unimate:
1 — исходное положение руки; 2 — максимальное выдвижение руки; 3 — поворот руки в обе стороны; 4 — поворот руки в вертикальной плоскости; 5 — вращение захвата; 6 — сгибание кисти Рис. 9.14.Схема движений робота типа Nachi
Большинство роботов программируется способом обучения. Процесс программирования состоит в том, что исполнительный орган вручную последовательно устанавливается в требуемые положения и после каждой установки нажатием кнопки на панели управления соответствующие координаты фиксируются в памяти робота. Затем в промежутке между зафиксированными позициями вводятся скорость сварки, продолжительность остановки, ускорения, замедления и т. п.
Сварочные роботы используются как отдельно стоящее оборудование или в составе автоматических линий. Например, в автоматической линии для контактной точечной сварки кузовов легковых автомобилей установлено 25 роботов типа Unimate. В ряде случаев целесообразно разделить функции между механизмом перемещения сварочной горелки и манипулятором для перемещения свариваемых изделий (рис. 9.15). Эти устройства работают совместно по единой программе.
Рис. 9.15.Схема движений механизма перемещения сварочной горелки (а) и манипулятора для перемещения свариваемого изделия (б):
1 — сварочная горелка; 2 — направляющая; 3 — манипулятор; 4 — планшайба
В сварочном производстве роботы могут быть использованы также в качестве транспортных средств, выполняющих установку и снятие свариваемых изделий и работающих в сочетании со специальными сварочными машинами-автоматами. Кроме того, роботы могут эффективно работать на заготовительных и сборочных операциях.
В настоящее время используются роботы первого поколения, работающие по заданной жесткой программе.
Второе поколение роботов будет обладать техническими «зрением» и «осязанием» и самостоятельно адаптироваться в окружающей обстановке.
Промышленный робот для контактной точечной сварки выполняет вспомогательные операции.
Автоматизация процесса контактной точечной сварки с помощью промышленного робота является сложной комплексной задачей. Цикл контактной точечной сварки делится на две группы процессов: собственно сварка, выполняемая во время сжатия электродов, и вспомогательные операции, заключающиеся в транспортировании клещей или объекта обработки.
Можно выделить три варианта использования промышленного робота при контактной точечной сварке:
§ загрузка и разгрузка специализированной сварочной машины, рассчитанной на сварку определенного изделия. Здесь робот устанавливает деталь в машину, а после сварки вынимает и заменяет следующей деталью;
§ обслуживание стационарной сварочной машины. Здесь робот подает очередную деталь, располагает ее надлежащим образом, включает машину, перемещает деталь и убирает ее;
§ сварка с помощью автоматически работающих сварочных клещей, укрепленных на конце руки робота.
Первый вариант достаточно прост и требует применения позиционного транспортирующего робота обычного типа. Второй и третий варианты позволяют заменить промышленным роботом квалифицированного сварщика. Остановимся детально на последнем варианте.
Роль промышленного робота, производящего контактную точечную сварку, заключается в транспортировании сварочных клещей и размещении их в заданных пространственных точках при соответствующем позиционировании электродов. Управление перемещением клещей осуществляется по позиционной системе — от точки к точке. В большинстве случаев работа ведется на объектах, неподвижных в течение всего цикла сварки. Однако применение универсального позиционного промышленного робота, кисть которого оснащена сварочными клещами вместо схвата, не является оптимальным решением. Задача состоит в создании специализированного высокоскоростного робота, в конструкции которого учтены требования технологии сварки.
Промышленный робот, выполняющий контактную точечную сварку, работает в напряженном режиме. Контактная сварка точки представляет собой довольно быструю операцию, измеряемую долями секунды. Необходимо, чтобы время перемещения не превышало время сварки. Это требует высокой скорости перемещения, которая приводит к появлению вибраций сварочных клещей при выходе на очередную позицию. Вибрации увеличивают износ механизма и обусловливают динамическую составляющую ошибки позиционирования. Поэтому для повышения скорости сварки следует принять специальные меры по подавлению вибраций.
Основные технические характеристики рассматриваемого промышленного робота (за исключением тех случаев, когда необходимо удовлетворить условиям частной производственной задачи) приведены далее.
Технические характеристики промышленного робота для контактной точечной сварки
· Рабочий объем (зона обслуживания), м36…10
· Число степеней свободы5 или 6
· Номинальная грузоподъемность, кг15…30
· Точность позиционирования, мм±1
· Объем памяти (число запоминаемых точек)200…1000
Последняя величина выбрана из расчета, что за один цикл промышленный робот выполняет 20…100 сварных точек. Однако он должен иметь возможность сваривать поочередно несколько различных деталей, поступающих в произвольной последовательности. Для этого при обучении в запоминающее устройство робота вводится соответствующее количество подпрограмм, а фиксирующее устройство оборудуется специальными датчиками, которые информируют робот о том, какая деталь на подходе. Соответственно с этим меняется и программа сварки.
Особого внимания заслуживает помехоустойчивость системы управления роботом, так как работа его происходит в тяжелых условиях сильных импульсных помех, вызванных коммутацией сварочного тока клещей (нескольких тысяч ампер).
Возможны несколько вариантов оснащения робота.
В первом варианте используется стандартное сварочное оборудование: сварочные клещи монтируются на кисть робота, сварочный трансформатор размещается в рабочей зоне сварки, технологические параметры процесса сварки управляются традиционной автоматической аппаратурой. Для синхронизации действий во времени предусматривают каналы внешних связей робота с аппаратурой управления клещами и устройством фиксации заготовки. Основной недостаток этого варианта заключается в том, что толстые силовые кабели вторичного контура, соединяющие сварочные клещи с трансформатором и размещенные вне робота, создают значительную механическую нагрузку на кисть робота, ограничивают рабочую зону и выбор позиций для сварки.
Во втором варианте токоподводящие шины вторичного контура вводят в механическую конструкцию робота, а сварочный трансформатор встраивают в сварочную головку или укрепляют на траверсе руки робота. При этом целесообразно совместить устройство управления технологическими параметрами сварки с устройством управления робота. Здесь появляются проблемы, связанные с увеличением инерции и нагрузки на кисть робота.
Если доступ в рабочую зону затруднен, то возможно нестандартное размещение робота. Например, для сварки внутри кузова автомобиля робот устанавливают на портале в вертикальном положении.
Промышленный робот для дуговой сварки (шарнирно-рычажный) выполняет основные технологические операции. В отличие от контактной точечной сварки, когда робот выполняет только функцию перемещения сварочных клещей, при дуговой сварке его функции органически связаны с самим технологическим процессом. Это совершенно иная задача.
Если при контактной точечной сварке достаточно выполнить позиционирование инструмента, перемещая его до и после сваривания точки, то при дуговой сварке движения должны регулироваться непрерывно в течение всего цикла сварки так, чтобы получить равномерный и качественный шов по всей длине сварного соединения. Для этого нужно обеспечить стабильность основного движения сварочного электрода, перемещая его эквидистантно линии стыка с высокой точностью и постоянной скоростью.
При сварке швом переменного сечения этого недостаточно. Следует регулировать скорость движения электрода вдоль стыка и параметры режима сварки (силу сварочного тока, напряжение дуги, приток газа) в соответствии с требованиями технологии.
Квалифицированный сварщик, накладывая шов, выполняет сложный комплекс движений: направляет электрод вдоль стыка с переменной скоростью не только поступательно, но и возвратно-поступательно (при этом кончик электрода движется по сложной траектории в пространстве, поскольку осевое перемещение электрода сопровождается поперечным и круговым движениями); ведя электрод вдоль линии сварки, периодически возвращает дугу в хвостовую часть ванны, управляя тем самым не только ее конфигурацией, но и ходом металлургических процессов между металлом, шлаком и газом. Кроме того, сварщик непосредственно наблюдает результаты своих действий с целью поддержания постоянства требуемых размеров сварного шва. Сварщик выполняет также вспомогательные операции: очистку мундштука, предотвращение вытекания металла из ванны, отсос газа.
Робот перемещает сварочную горелку по жесткой программе контурной системы управления, контролирующей траекторию и скорость перемещения горелки. Программирование полной траектории перемещения горелки и непрерывно изменяющихся технологических параметров обусловливает увеличение объема памяти робота.
В пределах ограниченного круга задач — сварка линейными швами, сварка по ломаной линии рядом точек (например, приварка элементов жесткости к листовому материалу) — достаточно зафиксировать положение каждой из граничных точек в пространстве. В этом случае можно применить позиционную систему управления, дополненную блоком стабилизации скорости. Выбор системы управления — узловая задача при разработке промышленного робота для дуговой сварки.
Динамическая нагрузка на промышленный робот для дуговой сварки ниже по сравнению с роботом для контактной сварки. Это объясняется малой массой сварочной головки и отсутствием громоздких токоподводящих кабелей. Режим движения робота — плавный, со скоростью 3…50 мм/с.
Базовый механизм робота целесообразно выполнять в прямоугольной системе координат, так как применение цилиндрической или сферической системы связано с излишней сложностью управления скоростью. Общие технические характеристики промышленного робота для дуговой сварки приведены далее.
Технические характеристики промышленного робота для дуговой сварки
· Рабочий объем (зона обслуживания), м34…6
· Число степеней свободы5 или 6
· Максимальная грузоподъемность, кг5…8
· Точность позиционирования, мм±0,5
· Объем памяти (число зафиксированных позиций)5000…10000
Совмещение робота со сварочным оборудованием не вызывает серьезных затруднений: сварочная головка укрепляется на кисти робота; подвод тока, подача газа и проволоки могут осуществляться по подвесным линиям и по встроенным в конструкцию робота магистралям.
Как и в случае контактной точечной сварки, при дуговой сварке промышленный робот с жесткой программой эффективен только в том случае, если точность пространственного положения линии стыка будет того же порядка, что и точность позиционирования робота. К сожалению, этому условию на практике можно удовлетворить лишь ценой тщательной технологической подготовки. Чаще всего случайные отклонения линии стыка от заданной по чертежу превышают допуск на точность позиционирования, поэтому реализация жесткой программы только движения электрода недостаточна. Та же картина наблюдается и с программированием технологических параметров, регулирование которых по детерминированному закону может оказаться малоуспешным ввиду случайных отклонений (например, площади сечения разделки). В этих условиях необходим адаптивный промышленный робот, обладающий средствами, позволяющими учитывать изменения в объекте обработки и корректировать программу в процессе работы.
Промышленное применение роботов для дуговой сварки началось в середине 1970-х гг. в Швеции. С тех пор последовательно осуществлялась идея замены сварщика роботом. Сварщик становился оператором. Такое совмещение приводит к повышению производительности и улучшению качества сварки.
Сварщик освобождается от тяжелой, монотонной и грязной ручной работы, однако при работе с роботом его ответственность возрастает. Оператор задает роботу информацию (о начале и окончании сварки, об изменении рабочих ходов или технологических переходов), контролирует процесс сварки и обеспечивает правильное выполнение роботом всех функции. Обязанности оператора не менее важны, чем обычного сварщика, однако его труд менее утомителен и более интеллектуален.
В работу оператора необходимо вложить новое содержание и придать ей определенную гибкость, для того чтобы он квалифицированно выполнял свои обязанности и мог совершенствовать свои навыки.
На суставы, мышцы и другие части тела сварщика, непосредственно участвующие в выполнении технологических операций, а также на его органы кровообращения и чувств действуют физические нагрузки, отрицательно сказывающиеся на его здоровье. Большие динамические нагрузки на мышцы при тяжелой физической работе (например, при перемещении деталей или ручном манипулировании клещами при точечной сварке) повышают частоту пульса и вызывают физическое утомление. Статическое нагружение мышц при работе с малыми нагрузками часто обусловливается продолжительным пребыванием в одной позе или длительным удержанием инструмента в определенном положении (например, при ведении электродвигателя или сварочной горелки). Поэтому при назначении рабочего ритма сварщика или оператора сварочного робота следует учитывать, что периоды нагрузки должны чередоваться с периодами относительного покоя или отдыха.
Оператор становится в известной степени руководителем роботизированного сварочного рабочего места. Его обязанности состоят в выполнении несложных заданий по программированию, управлении и контроле всех процессов в пределах роботизированного сварочного поста, контроле качества деталей, сваренных роботом, устранении неполадок при незапланированных остановках робота, техническом обслуживании и уходе за роботом и периферийным оборудованием, выполнении дополнительных сварочных работ, недоступных для робота, заполнении магазинов для деталей и присадочных материалов, очистке и замене изношенных деталей (например, сопел горелок), работе в контакте с механиками по обслуживанию и ремонту, мастерами и технологами.
Проблемы внедрения комплексных роботизированных рабочих мест для дуговой сварки учтены изготовителями сварочных роботов.
В состав роботизированного рабочего места входят: шарнирно-рычажный робот со шкафом электрооборудования, пультом управления и программирующим устройством; периферийное оборудование для установки и перемещения деталей; сварочная оснастка, состоящая из источника тока, механизма подачи проволоки, неохлаждаемой или водоохлаждаемой горелки для сварки в среде защитного газа.
С помощью программирующего устройства горелку перемещают от точки к точке, а данные о координатах точек вводят в память системы управления путем нажатия на соответствующие кнопки программирующего устройства. Для каждого шага между точками задают свою скорость позиционирования или сварки, для сварочных движений выбирают соответствующую комбинацию параметров режима сварки (таких комбинаций пять). Перемещения деталей периферийным оборудованием, необходимые в определенных местах и совершаемые во время сварки, тоже программируются. Ошибочно введенные данные можно скорректировать или заменить.
Возможно совмещение сварочного робота с транспортным устройством. Тогда для сварки деталей с большой площадью поверхности используется роботизированный сварочный портал. Такие детали обычно применяются в судостроении, на железнодорожном транспорте, в строительстве. Портал состоит из двух колонн с поперечной балкой. Каждая из колонн установлена на тележке с двумя колесами. Одна из тележек имеет две пары горизонтальных направляющих роликов для перемещения по рельсовому пути с помощью прецизионных приводов, зубчатые рейки которых закреплены на рельсе. Система измерения точности перемещений обеспечивает подвод сварочной горелки к заготовке, замедление скорости подвода при подходе к свариваемому стыку, гарантирует точность позиционирования сварочной горелки в пределах ±0,3 мм. На поперечной балке подвешены два робота, развернутых на 180° и перемещающихся вдоль балки. Перемещения портала, позиционирование и согласование работы портала и роботов осуществляются по командам ЭВМ.
Большинство роботов, выполняющих дуговую сварку, используются для сварки плавящимся электродом в среде активных газов, а примерно 20…30% роботов оснащены аппаратами для сварки плавящимся электродом в среде инертных газов. Лишь небольшая часть промышленных роботов выполняет сварку вольфрамовым электродом в среде инертных газов и сварку под слоем флюса. Отдельные роботы с контурным управлением применяются для плазменной и газовой резки. Роботизированная плазменная резка обещает стать экономичным способом контурной обработки. Известны примеры применения такой резки в автомобилестроении для обрезки кромок деталей, полученных вытяжкой, и для удаления литников или вырезки контуров в трубах.
При рассмотрении вопроса о целесообразности внедрения сварочных роботов необходимо учитывать следующие характеристики деталей и технологии: размеры деталей, доступность стыковочных узлов для сварочного инструмента, объем свариваемой партии, форма швов, число сварочных проходов, требования к качеству, технологическое время, точность предварительной обработки заготовок.
При сварке роботами профиль зоны проплавления получается более плавным, чем при ручной сварке. Показатели качества сварных соединений, выполненных роботами, в среднем выше, чем соединений, выполненных вручную.
Максимальные производственные допуски на детали из тонких листов должны составлять ±0,5 мм. При сварке толстых листов угловыми швами допустимы несколько большие отклонения размеров, так как иногда они могут быть компенсированы колебаниями горелки.
При сварке роботом силу сварочного тока можно повысить (до 50%) по сравнению с ручной сваркой проволокой такого же диаметра. Благодаря программированию силы тока на отдельных участках шва сварку можно выполнять на разных токах. С помощью позиционирующего устройства заготовку устанавливают перед роботом (для сварки «в лодочку») или в горизонтальном положении. Это исключает неудобную и снижающую производительность сварку в других пространственных положениях.
Средняя скорость ручной дуговой сварки плавящимся электродом в среде углекислого газа составляет 15…18 м/ч (при сварке роботами ее можно удвоить), сварки тонких листов — 36…72 м/ч, сварки угловыми швами листов толщиной 4 мм — 24…30 м/ч. Увеличение скорости сварки снижает подвод теплоты к заготовке, что способствует уменьшению коробления детали и сокращению объема правки. Это особенно заметно при сварке деталей из хромоникелевых сталей. Благодаря быстрому перемещению робота при позиционировании значительно возрастает продолжительность включения: при выполнении роботом сварки плавящимся электродом в среде углекислого газа она обычно составляет 60…80%, а для ручной дуговой сварки — 20…40%.
Стабильное качество шва при равномерном движении сварочной горелки сокращает трудоемкость последующей обработки деталей, а необходимость шлифования, как правило, отпадает. Выбор оптимального режима сварки и соответствие силы тока заданному программой значению снижают потери металла на образование брызг до минимума.
Целесообразность внедрения сварочного робота в значительной степени зависит от возможности программирования его функций. Высокая кинематическая гибкость робота облегчает программирование, снижает его трудоемкость и повышает коэффициент использования.
Система управления промышленным роботом должна обеспечивать линейную и круговую интерполяцию, возможность программирования колебаний горелки и параллельного смещения инструмента, возможность программирования в цилиндрической или прямоугольной системе координат.
Многие детали автомобиля по форме являются как бы зеркальным отражением друг друга (например, левый и правый каркасы боковин). Программа сварки левой детали и зеркального «переноса» на правую деталь составляется роботом по трехточечному методу программирования. При этом зеркальное расположение осей деталей не обязательно. Программа для сварки левой детали, составленная по трехточечному методу, «переносится» на правую деталь, которая занимает зеркальное пространственное положение. При сварке роботами такой «перенос» особенно важен. Трехточечный метод программирования можно применять при конгруэнтности деталей, при сварке одинаковых деталей в нескольких сборочных приспособлениях, при замене робота, при сварке одинаковых деталей несколькими роботами.
При работе роботов по принципу обучение—воспроизведение программирование утомительно и часто требует больших временнћх затрат. Упрощение программирования возможно за счет использования вспомогательных средств управления. Система управления должна обеспечивать работу: в режиме проверки, при котором программа только обкатывается (частично или полностью); световую индикацию программных операций; коррекцию координат точек и шагов программы; введение и удаление координат точек; шаговое перемещение робота с помощью ручного программирующего устройства; ввод данных о скоростях движения; копирование программы; ввод и хранение параметров режима сварки; реализацию функции реле времени; ввод-вывод внешних сигналов и разветвление программы; сигнализацию о перебоях в работе и аварийных ситуациях; программирование операций во времени и выдачу команд на их повторение или изменение.
С внедрением микропроцессоров и интегральных схем памяти меняется соотношение стоимости аппаратного и программного обеспечения в сторону удорожания последнего. Сейчас на долю аппаратного и программного обеспечения приходится в общем случае соответственно 20 и 80% их общей стоимости. В прошлом сбои процесса сварки возникали главным образом вследствие погрешностей при программировании и реже — в результате выхода из строя электронных элементов. Рекомендуются следующие пути снижения затрат, связанных с программированием: создание более эффективных технических средств программирования всех операций независимо от их сложности; разработка методов пооперационного программирования; совершенствование языка программирования; использование при программировании табличных данных; совершенствование техники документирования.
Современные системы управления роботами позволяют оператору осуществлять ряд функций программирования и управления. Он может давать управляющие команды и получать информацию о регулируемых параметрах, устанавливать длительность задержки прохождения программы при изменении положения свариваемого стыка, изменять главную программу и подпрограмму и вводить команды, управляющие программами такта сварки, приводами подачи проволоки или источниками питания. Возможность корректирования и сохранения программ способствует удобству управления.
В современных системах управления роботами реализуются также такие функции, как повторение программы при осепараллельном смещении свариваемого стыка, смещение точки начала выполнения программы, автоматическая коррекция положения инструмента (коррекция положения горелки и конца сварочной проволоки при ее поперечных колебаниях), синхронизация работы робота, периферийного оборудования и транспортирующего устройства.
Устройства индикации параметров, удобно расположенные для обзора панелей управления и ручных программирующих приборов, позволяют визуально контролировать протекание технологического процесса и выявлять сбои, облегчая тем самым диалог оператора с системой управления.
Программы диагностики отдельных функций управления помогают быстро находить возникающие ошибки или неисправности, что способствует снижению длительности простоев, связанных с их устранением, и повышению степени загруженности робота.
В будущем требования к надежности, полноте использования и удобству обслуживания роботов возрастут. Для соответствия этим требованиям изготовители роботов должны ориентироваться на более высокую надежность аппаратных и программных средств и на совершенствование контрольно-диагностических систем.
Сейчас значительная часть роботов (в том числе и сварочных) программируется прямым или косвенным обучением. С усложнением задач, особенно при внедрении технологических роботов, возрастают временные затраты на составление программ. Простои роботов на стадии обучения снижают эффективность их использования в мелко- и среднесерийном производстве. Программа, составленная на соответствующем языке, упрощает программирование работы конкретного робота и позволяет возложить эту функцию на технологические службы.
Типичным представителем шарнирно-рычажного робота является стационарный робот IR 601/60 (рис. 9.16) грузоподъемностью 600 кг при максимальной скорости перемещения исполнительного механизма и 100 кг при пониженной его скорости. Робот позволяет манипулировать тяжелыми клещами для точечной сварки. Максимальная скорость перемещения составляет 3,7 м/с, погрешность позиционирования ±1,2 мм, объем зоны обслуживания — 28 м3. Микропроцессорная система управления позволяет хранить данные о 1000 точек в пространстве.
Рис. 9.16.Стационарный шарнирно-рычажный робот IR 601/60 с шестью степенями свободы (1—6)
Шарнирно рычажные роботы, оснащенные клещами, непригодны или мало пригодны для сварки деталей с большой площадью поверхности или деталей сильно искривленной формы. Промышленный робот IR 200 используется для односторонней точечной сварки на медной подкладке. Его гибкий рабочий орган, расположенный над свариваемыми деталями, оснащен подъемными клещами, электродным цилиндром или пружинным прижимом. Робот IR 200 выполнен в виде семиосной портальной установки, которая нагружает свариваемую деталь только через стойки портала. С помощью одного прижима робот может со скоростью 1,2 м/с объезжать деталь, размеры проекции которой на плоскость составляют 2,5×6 м. Максимальное усилие сжатия электрода при сварке равно 5 кН.
Роботы серии IR 200 комплектуются из унифицированных узлов, которые по виду главного движения при сварке можно разделить на вращательные, линейные и линейно-вращательные.
Интересна компоновка безлюдного участка точечной сварки боковых панелей легкового автомобиля. Производственный комплекс изготовления этих панелей включает в себя четыре вращающиеся барабанные установки, каждую из которых обслуживают три робота. На одной паре установок изготовляют правые панели, на другой — левые. По бокам каждого вращающегося барабана имеются два сварочных рабочих места, а сверху — рабочее место автоматической загрузки и выгрузки. Каждый барабан оснащен тремя сборочными рамами, на которых свариваемый узел закрепляется шестью зажимами. Шаговый двигатель поворачивает барабан относительно его горизонтальной оси на 120°.
На участок сварки боковин кузова мусоровоза сварка выполняется с чередующимся тактом. Один робот поочередно сваривает заготовки в узлы на двух рабочих местах: в то время, когда выполняется сварка на одном рабочем месте, на другом вручную укладывают заготовки в приспособление и прихватывают их.
Важную роль в обеспечении стабильного качества сварки угловыми швами играют контурное управление роботом и сенсорная настройка сварочной проволоки на стык. Сенсор нового типа измеряет электрические параметры дуги и выдает их в качестве корректирующих сигналов для поиска стыка свариваемых деталей и постоянной коррекции траектории движения сварочной горелки. Условиями функционирования сенсора колебаний проволоки являются минимальная сила сварочного тока 120 А и амплитуда колебаний проволоки в пределах ±1 мм. Сенсор используется при сварке стыковыми швами с V-образной разделкой кромок и для сварки угловыми швами. Если кромки свариваемых деталей вертикальны, то робот ведет сварку с выключенным сенсором. Допуски размеров разделки кромок должны быть меньше, чем при ручной сварке, что требует высокой точности размеров деталей. Время на прихватку и сварку боковины составляет около 450 мин, т. е. по сравнению с ручной сваркой экономия времени при сварке роботом достигает 20…25%. Такая компоновка участка сварки позволяет увеличить выпуск продукции вдвое, так как автоматизированная сварка выполняется одновременно с ручными операциями загрузки и прихватки.
Для автомобильной промышленности, выпускающей продукцию большими партиями, предпочтительны сборочно-сварочные линии, на которых для сварки деталей кузова вместо ручных сварочных клещей применяются роботы для точечной сварки.
Конструкции с точечными сварными соединениями представляют собой практически полностью скомплектованные кузова относительно большого объема или отдельные части кузова: боковые стенки, двери, полы и аналогичные им узлы. Чтобы отдельные детали в процессе сварки роботами сохраняли постоянное и точное взаимное расположение, их перемещают с помощью различных транспортных устройств, выбранных в зависимости от размера, массы и скорости перемещения деталей. Эти устройства перемещают детали от одного поста к другому и удерживают их в заданном положении во время сварки. При малой скорости движения по сборочно-сварочной линии применяются устройства типа салазок, несущих деталь и катящихся по роликовому конвейеру. При большой скорости предпочтительны устройства в виде ходовых шасси или транспортных тележек с колесами, жестко связанных с деталями и перемещающихся по рельсам. При сварке деталей одинаковой геометрической формы, представляющих зеркальное отражение друг друга, используются приемные и транспортные устройства.
Свариваемый узел полностью монтируется на транспортной тележке и с помощью прижимов удерживается в постоянном положении при всех сварочных операциях на разных рабочих местах линии. Этим обеспечивается соответствие положения сварных точек заданной программе и высокое качество сварки.
Стационарные и портальные роботы различных конфигураций (рис. 9.17 и 9.18) предназначены для выполнения точечной сварки в автомобилестроении. Разнообразие конфигураций роботов позволяет выбирать их в зависимости от геометрии детали и расположения сварных швов.
Рис. 9.17.Конфигурации стационарных и портальных роботов
Рис. 9.18.Конфигурации портальных роботов с полярными координатами в напольном и потолочном исполнениях
По виду движений, реализуемых по трем главным осям, роботы можно подразделить на три группы:
§ роботы, перемещающиеся в прямоугольной системе координат — портальные роботы без устройства наклона, выполняющие линейные движения;
§ роботы, перемещающиеся в полярной системе координат, с устройством наклона;
§ шарнирно-рычажные роботы.
Роботы указанных групп применяются для дуговой сварки. Если для точечной контактной сварки в зависимости от ее сложности можно использовать роботы с двумя — четырьмя степенями свободы, то для дуговой сварки необходимы роботы с пятью или шестью степенями свободы.
Иногда площадь для размещения робота ограничена (например, при последовательном расположении роботов в одной поточной линии). При использовании напольных роботов ширина производственной линии достигает 8…10 м. Портальные роботы шириной 4…5 м позволяют рационально использовать производственные площади.
На рабочих местах для изготовления или предварительного монтажа отдельных деталей автомобильного кузова, на рабочих местах для прихватки, а также на линиях окончательной сборки и сварки применение роботов с шестью степенями свободы необязательно. Часто для выполнения этих работ достаточно двух линейных и одного вращательного движения или одного линейного и двух вращательных движений, а иногда — только одного или двух линейных движений.
Исследование большого числа роботизированных комплексов позволило сделать вывод о целесообразности разделения различных движений роботов на независимые друг от друга и выполнения отдельными роботами только таких движений, которые не могут выполняться другими роботами. Такой метод обеспечивает ряд значительных преимуществ: сокращение парка оборудования и его меньшую сложность; уменьшение габаритных размеров и массы робота; сокращение аппаратуры управления; снижение риска ошибок; удешевление технического обслуживания; минимизация занимаемых роботами площадей; экономия капиталовложений. Возможность комбинирования конструктивных элементов обеспечивает более полное соответствие роботов выполняемым задачам и повышает их гибкость.
В настоящее время разработана система узлов, аналогичных унифицированным узлам, которые можно собирать в различных комбинациях. Узлы предназначены для разных вариантов роботов. Для централизованного управления большими сборочно-сварочными линиями и контроля их работы необходимы несколько автономных щитов переключений и значительное число информационных связей между элементами линии. Автономные интерфейсные стойки с дисплеями располагаются вдоль производственной линии, а центральный блок управления и запоминающее устройство устанавливаются стационарно в другом месте цеха.
Такое расположение аппаратуры обеспечивает централизацию технического обслуживания и текущего ремонта, уменьшение количества линий связи между элементами линии и сведение к минимуму числа запоминающих устройств, реализацию диалога с управляющим компьютером (на всем производственном участке или в цехе).
На сборочно-сварочной линии можно собирать автомобильные кузова пяти типов, которые имеют геометрическое подобие с базовой моделью, но отличаются друг от друга частностями. Кузова на салазках, скользящих по приводным роликовым конвейерам, поступают на рабочее место для прихватки. Каждая их трех главных линий оснащена шестью роботами простейшей конструкции, которые прихватывают детали кузова в зажатом состоянии. Операции зажатия и прихватки выполняются по командам системы управления, соответствующим данному типу кузова. Затем кузова по трем главным линиям подаются на выходной поперечный конвейер и далее поступают на две линии для окончательной сварки, которая тоже выполняется только сварочными роботами. На каждой из этих линий установлено по восемь сварочных роботов (по четыре робота с каждой стороны линии).
На рис. 9.19 показана часть линии окончательной сварки кузовов легковых автомобилей. На линии работают два робота модульного типа, собранные из унифицированных узлов. Производительность такой роботизированной сварочной линии составляет 150 кузовов в час. Каждый кузов сваривают примерно 400 точками.
Рис. 9.19.Роботы модульного типа из унифицированных узлов, работающие на линии окончательной сварки кузовов легковых автомобилей
Массовое производство с неблагоприятными для человека факторами должно перестраиваться в направлении средне- и мелкосерийного производства, что вызывает необходимость гибкой автоматизации с помощью промышленных роботов. Ответственность за качество продукции (в том числе и в области сварки) переносится по возможности на низший персонал, и предположительно около 60% нововведений будут предлагаться по его инициативе.
Широкое внедрение роботов и микроэлектроники в промышленности при активном участии производственного персонала явилась одним из факторов, обусловивших интенсивное развитие японской экономики. Автоматизация вообще, с использованием промышленных роботов особенно, все в большей степени охватывает небольшие предприятия японской промышленности, на которых работает около 60% всего производственного персонала.
То обстоятельство, что даже небольшие предприятия с ограниченными финансовыми возможностями могут покупать дорогие промышленные роботы, объясняется рациональностью и целесообразностью: стоимость такого робота соответствует примерно двухгодичной зарплате сварщика очень высокой квалификации, зато производительность робота в разы выше производительности того же сварщика.
На сварочных линиях большого японского завода по производству спортивных автомобилей выполняется 18 рабочих операций длительностью 3 мин. Контролер на конце линии следит за работой роботов. Внедрение на этих линиях 80 сварочных роботов повысило степень автоматизации до 90%.
Производительность труда на некоторых японских автомобилестроительных заводах при широкой автоматизации сварочных процессов за счет внедрения роботов повысилась за 10 лет в 4 раза, в то время как во всей мировой автомобильной промышленности за тот же период достигнуто лишь двукратное повышение производительности труда.
В сварочном производстве успешно применяются и являются перспективными мультироботные системы. Такая система состоит из нескольких подвешенных на портале шарнирно-рычажных роботов (их количество зависит от конкретной сварочной задачи). Такое положение роботов позволяет выполнять множество точных движений в ограниченном пространстве и не требует большой площади. Программы работы всех роботов на портале хранятся в памяти единой ЭВМ. Позиционная и контурная системы управления позволяют выполнять сложные перемещения.
Универсальный портал мультироботной системы оснащен восемью роботами для сварки кузовов. Система управления обладает таким объемом памяти, какой мог бы позволить отработку каждым роботом восьми программ одновременно. Данный объем памяти системы управления обеспечивает быструю переналадку на сварку кузова другой модели. Привод роботов гидравлический.
Сварочный робот перемещается в прямоугольной системе координат (рис. 9.20). Такие роботы изготовляются в напольном или потолочном исполнении, что расширяет зону их возможного применения. Они пригодны для сварки широкой номенклатуры деталей различных размеров осепараллельными швами, расположенными под небольшими углами к главным осям, или круговыми швами.
Рис. 9.20.Сварочный робот, перемещающийся по прямоугольным пространственным координатам:
а — напольное исполнение; б — потолочное исполнение
Контрольные вопросы
1. Какие системы автоматического управления вы знаете? Перечислите их основные особенности.
2. Перечислите основные средства автоматического управления.
3. Как работает станок для сборки и сварки корпусов шахтерских ламп?
4. Как работает вальцесварочный станок для сборки и сварки кузовов шахтных вагонеток?
5. Как работает станок для сборки и сварки пустотелых стальных шаров?
6. Как рассчитываются основные параметры механизированных и автоматических линий?
7. Что такое поточные линии?
8. Как работает линия для сборки и сварки листовых полотнищ?
9. Какие операции выполняются на линии для изготовления прямошовных труб?
10. Как работает линия для изготовления спиралешовных труб?
11. Как работает линия для изготовления кабин грузовых автомобилей?
12. Как устроена линия для изготовления автомобильных колес? Какие операции на ней выполняются?
13. Как работает линия для изготовления радиаторов отопления?
14. Что такое роторные линии?
15. Что такое роботы? Для чего они применяются в сварочном производстве?
16. Перечислите основные разновидности роботов. Какие движения они выполняют?
Список литературы
Гитлевич А.Д. Механизация и автоматизация сварочного производства / А.Д.Гитлевич, Л.А.Этингоф. — М. : Машиностроение, 1979.
Гитлевич А.Д. Альбом механического оборудования сварочного производства / А.Д.Гитлевич, Л.А.Животинский, А.И.Клейнер. — М. : Высш. шк., 1974.
Патон Б.Е. Промышленные роботы для сварки / Б.Е.Патон, Г.А.Спыну, В.Г.Тимошенко ; под общ. ред. Б.Е.Патона. — Киев : Наукова думка, 1977.
Сварочные роботы : [пер. с нем.] / [В.Геттерт, Г.Герден, К.Борн, Дж.Селеван]. — М. : Машиностроение, 1988.
Дата добавления: 2021-04-24; просмотров: 175; Мы поможем в написании вашей работы! |
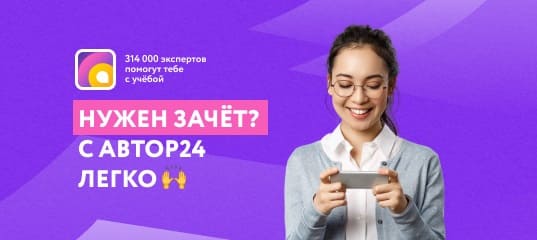
Мы поможем в написании ваших работ!