Силовой расчет приспособления
Для обеспечения надежного закрепления заготовки необходимо произвести расчет необходимой силы зажима, чтобы исключить вырыв и смещение заготовки в процессе обработки. Расчет необходимо вести по силе, максимально стремящейся сместить заготовку в направлении минимального контакта с зажимными элементами, то есть расчет необходимы вести по самому неблагоприятному фактору.
При фрезеровании возникает крутящий момент и сила, которая направлена вдоль плоскости фрезерования.
Исходные данные:
D=50 мм - диаметр фрезы;
Z=3 – число зубьев;
Sz=0,5 мм – подача на зуб;
n=950 об/мин – частота вращения шпинделя;
t=0,5 мм – толщина срезаемого слоя;
f=0,6 – коэффициент трения по необработанной поверхности;
Кр=0,9 мм - поправочный коэффициент.
Сила резания при фрезеровании рассчитывается по формуле
(58)
(59)
Коэффициенты берем исходя из того, что материал режущей части фрезы ТТ8030/5/
где СР = 825; х=1; y=0,75; u=1,1; q= 1,3; w= 0,2; Kp=0,93.
Расчетные усилия зажима определяются по формулам
(60)
Рассчитывается коэффициент закрепления
, (61)
где К0 = 1,5 – гарантированный коэффициент запаса для всех случаев;
К1 – коэффициент, учитывающий состояние поверхности заготовок: (К1 = 1,2 – для черновой поверхности);
|
|
К2 – коэффициент, учитывающий увеличение сил резания от прогрессирующего затупления инструмента (К2 = 1,5);
К3 – коэффициент, учитывающий увеличение сил резания при прерывистом резании (К3 = 1);
К4 – коэффициент, учитывающий постоянство силы зажима, развиваемой силовым приводом приспособления. (К4 = 1 – для механизированных силовых приводов);
К5 – данный коэффициент учитывается только при наличии крутящих моментов, стремящихся повернуть обрабатываемую деталь. (К5 = 1,5).
Коэффициент закрепления должен быть не менее 2,5, поэтому данное значение удовлетворяет требованиям.
Усилие зажима находится по формуле (55)
Рассчитывается исходное усилие. Необходимое усилие Q рассчитывается по формуле:
(62)
где W – сила зажима;
l=36мм – длина рычага прихвата, (Прихват 7011-0737 ГОСТ14733-69);
H=55мм – высота прихвата;
f =0,1 – коэффициент трения;
q=24,7 Н – усилие пружины.
Тогда
Описание конструкции и точностной расчет контрольного приспособления
Основным назначением технических измерений является обеспечение взаимозаменяемости и предупреждение брака.
|
|
В данном курсовом проекте был разработан комплексный калибр для измерения зависимого позиционного допуска четырех отверстий М5-7Н. Сборочный чертеж комплексного калибра представлен на чертеже ТПЖА.401412.128СБ.
Расчет калибра ведется по /6/.
Зависимый допуск TP = 0,250 мм
Для пробки, контролирующей расположение отверстий диаметром M5-7H:
F=0,032 мкм – основное отклонение;
H 0 = H=0,010 мкм – допуск на изготовление;
W 0 = W=0,012 мкм – величина износа;
TPK=0,020 мкм – позиционный допуск;
Расчитываются предельные отклонения пробок калибра:
Наибольший диаметр измерительных пробок калибра:
(61)
где – наименьший диаметр отверстия (средний диаметр)
Тогда
Наименьший диаметр измерительных пробок калибра:
(62)
Тогда
Размер предельно изношенного измерительного элемента
(63)
Тогда
Позиционный допуск калибра
Предельное отклонение диаметра окружности центров
Предельное отклонение центрального угла между осями измерительных элементов
Наибольший предельный размер базовой пробки:
мм (64)
|
|
где =104 мм – размер предельно изношенного поэлементного проходного калибра, предназначенного для контроля размера поверхности изделия.
Наименьший диаметр базовой пробки:
(65)
Тогда
Диаметр предельно изношенной базовой пробки калибра:
(66)
Тогда
Наибольший диаметр измерительных пробок калибра:
(67)
где – наименьший диаметр отверстия (средний диаметр)
Тогда
Наименьший диаметр измерительных пробок калибра:
(68)
Тогда
Размер предельно изношенного измерительного элемента
(69)
Тогда
Позиционный допуск калибра
Автоматизация обработки детали «Корпус 6128» на агрегатной операции 3.1 Обзор возможных методов автоматизации обработки детали «Корпус 6128», обоснование варианта решения поставленной задачи и типа средства автоматизации
При выборе оборудования и унифицированных узлов учитывается потребная мощность резания, величина рабочих ходов, а также габариты детали.
|
|
Первоначально к агрегатному станку подбирают силовую головку. При выборе силовой головки необходимо учитывать следующие основные требования:
- мощность привода силовой головки, кВт;
- ход пиноли, мм.
Первоначально к агрегатному станку подбирают силовую головку. Для данной детали из каталога [2] выбирается универсальная гидровинтовая силовая головка (общий вид представлен на рисунке 3). бесступенчатого регулирования величин рабочих подач, наличие гидравлического двигателя создало возможность изменять число оборотов шпинделя бесступенчато.
В качестве привода вращения в головке используется гидровинтовой двигатель. Он состоит из обоймы, ведущего винта и двух ведомых винтов.
Универсальная гидровинтовая головка предназначена для выполнения операций сверления, зенкерования, развертывания, фрезерования и нарезания резьбы.
Рисунок 3 – Кинематическая схема силовой головки 1УХ 4035
Для рабочих позиций станка выбирается самодействующая силовая головка модели 1УХ4035.
Она обладает следующими характеристиками:
Класс точности | Н,П |
Мощность электродвигателя, кВт | 1,5 |
Максимальный ход пиноли, мм | 83 |
Максимальная осевая сила, Н | 3500 |
Предел подачи на оборот шпинделя, мм/об | 0,005-1,785 |
Частота вращения шпинделя, об/мин | 72-3170 |
Максимальный крутящий момент, Нм | 27 |
Габаритные размеры, мм | 980 х 250 х 425 |
Максимальная масса без двигателя, кг | 320 |
Силовая головка пинольного типа с плоскокулачковым механизмом подачи предназначена для сверления, развертывания, торцевания и нарезания резьбы. При оснащении дополнительными приспособлениями можно выполнять фрезерование, обтачивание и растачивание кольцевых канавок в отверстиях. Конструкция предусматривает возможность оснащения многошпиндельной насадкой.
На рисунке 3 показана кинематическая схема силовой головки 1УХ 4035. Главное движение – вращение шпинделя передается от электродвигателя 1 через двухступенчатый редуктор со сменными зубчатыми колесами В, Г, Д, Е и промежуточным валом 2 на пустотелый червяк 3, установленный на подшипниках в корпусе 4 головки. Червяк с помощью подвижного шлицевого соединения передает вращение шпинделю 5, установленному на подшипниках качения в пиноле 6.
Для осуществления подачи движение передается от червяка к червячной шестерне 7 через предохранительную шариковую муфту 8, включенную муфту 9 и шлицевый валик 10, на котором установлена подвижная полумуфта кулачковой муфты, паре сменных зубчатых колес К и Л. Ведомая сменная шестерня установлена на валу шестерне 11, которая находится в зацеплении с зубчатым венцом дискового пазового кулачка подачи 12. Кулачок может вращаться на оси 13, закрепленной на крышке силовой головки (на схеме не показана). В пазу кулачка перемещается ролик 14, установленный на оси 15, закрепленной в шпонке 16, которая, в свою очередь, жестко закреплена на пиноли от поворота и перемещается вместе с ней по точно пригнанному пазу в корпусе силовой головки. Постоянный контакт между роликом и кулачком обеспечивается пружиной 17, действующей на шпонку через рычаг 18,
установленный на оси 19.
Для включения подачи силовой головки при включенном электродвигателе и, следовательно, вращающемся шпинделе подается команда на электромагнит 20, который через серьгу 21 поворачивает рычаг 22 вместе с валиком 23. При наладочных работах включение подачи можно осуществить вручную, нажимая на толкатель 24. На другом конце валика закреплен рычаг 25, который поворачивается и выводит тягу 26 из зацепления с верхним плечом двуплечего рычага 27. При этом освобождается пружина 28, которая поворачивает, связанный с ней рычаг 29 вместе с тягой вокруг оси 30. Нижнее плечо рычага через ролик 31, находящийся в пазу подвижной полумуфты кулачковой муфты, перемещает последнюю по шлицам и вводит в зацепление с неподвижной полумуфтой, включая муфту, и, таким образом, замыкает кинематическую цепь подачи.
Движение передается кулачку, который перемещает пиноль вперед до конечного положения. При этом шпонка освобождает рычаг 27, который под действием пружины 32 поворачивается вокруг оси 33. Верхнее плечо рычага перемещается влево до тех пор, пока не окажется против паза в тяге, которая под действием пружины 34 поворачивается и захватывает рычаг. Выбирается делительный поворотный стол. Он выбирается с учетом рабочих позиций и габаритов зажимных приспособлений для обрабатываемой детали, а также по их количеству. В данном случае выбирается поворотный делительный стол модели УХ2036.010, диаметр которого равен 800 мм, высота 220 мм, диаметр основания 800 мм.
Технические характеристики стола У1Х2036:
Планшайба:
Диаметр, мм 800
Число позиций 2-14
Время поворота на одну позицию, с 2 - 9
Масса стола с приводом, кг 1128
Мощность привода, кВт 1,7
Точность фиксации, мм ±0.02 на радиусе 300 Стол предназначен для периодического перемещения обрабатываемых деталей из одной рабочей позиции в другую и точной фиксации на каждой позиции. Всего в данном случае будет четыре позиции: три рабочих, по количеству технологических переходов и одна загрузочная.
Общий вид стола приведен на рисунке 4. Данный стол подходит по габаритам детали и по точностным характеристикам. Рассматривается устройство и принцип действия поворотного делительного стола модели УХ2036.010.
Привод поворота состоит из электродвигателя 4, клиноплунжерной передачи 3 и червячного редуктора 2.
Стол работает следующим образом: по команде на поворот планшайбы 1 включается электродвигатель 3. Через клиноременную передачу и редуктор 2 вращение передается на кулачок 4 (рисунок 4) с поводковым пальцем 5, роликом 6 и кулачком 7. По закону, записанному на кулачке 7, переключается золотник 8 и открывает доступ сжатого воздуха в бесштоковую полость цилиндра 9, а также в пневмонаправляющие стола. Планшайба “всплывает” над корпусом на подшипнике 14. Вращаясь далее, кулачок 4 через рычажную систему 15, 16, 17 выводит фиксаторы 18 и 19 из гнезд 20, 21 планшайбы 13. Затем поводковый палец 5 с роликом 6 входит в пазы мальтийского механизма, образованного в детали 22, укрепленной на планшайбе и поворачивает последнюю.
В момент окончания поворота планшайбы кулачок 4 освобождает рычажную систему 15, 16, 17 и пружина 23 вводит фиксаторы 18 и 19 в гнезда 20 и 21. Поводковый палец 5 с роликом 6 выходит из пазов детали 22. Конический фиксатор создает натяг в системе фиксирования. Кулачок 7 теперь переключает золотник 8. Подача воздуха в пневмонаправляющие прекращается и планшайба ложится на корпус. Пневмоцилиндр 9 через рычажную систему 10, 11 и тягу 12 прижимает планшайбу 13 к корпусу. Прижим планшайбы и ввод цилиндрического фиксатора контролируется микропереключателями, которые при условии срабатывания обоих дают команду на отключение двигателя и на начало работы силовых головок.
Столы имеют ручное управление – кнопкой золотника 8 и специальным квадратом на рычаге 16. Сжатый воздух при этом должен подаваться в пневмосистему стола.
Рисунок 4 - Общий вид поворотного делительного стола УХ2036.010
Выбирается станина круглая модели СА2120 (Рисунок 5). Предназначена для установки поворотных делительных столов, присоединения боковых станин и подставок при компоновке агрегатных, специальных станков и автоматических линий.
Характеристики станины:
Диаметр рабочей поверхности для установки силовых головок, стоек и других узлов, мм
наружный 2120
внутренний 900
Диаметр рабочей поверхности для установки поворотного делительного стола, мм 630
Высота 630
Масса стола с приводом, кг 3050
.
Рисунок 5 – Станина
На конечном этапе подбирается стойка под силовую головку, модели 1УХ1535.010 с размерами Н = 1320 мм, L = 325 мм, m = 192 кг.
Стойка предназначена для установки в вертикальном положении силовых головок на рабочих позициях станка. Выбранная стойка изображена на рисунке 6.
Рисунок 6 - Стойка модели 1УХ1535.010
Техническая характеристика стойки 1УХ1535.010
1.Габаритные размеры, мм 1320 х 460 х 330
2.Вес стойки, кг 192
Дата добавления: 2020-04-25; просмотров: 936; Мы поможем в написании вашей работы! |
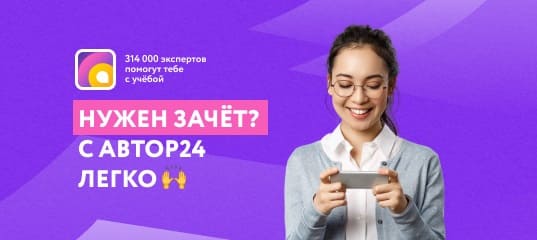
Мы поможем в написании ваших работ!