Обоснование выбора оборудования
Операция 105 – Агрегатная. На этой операции производится фрезерование поверхностей, сверление отверстий и развертывание (подготовка чистовых баз на последующую операцию). Целесообразно применять агрегатный станок.
Операция 110 – Агрегатная. На этой операции производится фрезерование верхней плоскости, фрезерование правого торца, растачивание центрального отверстия справа, цековка лапок, сверление крепежных отверстий на правом торце и сверху, нарезание резьбы. Целесообразно применять агрегатный станок.
Операция 115 – Агрегатная. На этой операции производится фрезерование левого торца, растачивание центрального отверстия слева, сверление крепежных отверстий на левом торце и нарезание резьбы. Целесообразно применять агрегатный станок.
Операция 120 – Алмазно-расточная. На этой операции производится очень точное растачивание центрального отверстия. Целесообразно применять алмазно-расточной станок.
Расчет и назначение межоперационных припусков
Расчет припусков производится на отверстие ø158H7(+0,04). Данная поверхность обрабатывается на трех переходах одной операции: Агрегатная.
Расчет припусков на обработку наружной поверхности ведется путем составления таблицы 3, в которую последовательно записывается технологический маршрут обработки поверхности и все значения элементов припуска.
Величина допуска заготовки зависит от выбранного способа ее получения и точности заготовки. Допуск на данный размер составляет 0,8 мм, поэтому предельные отклонения на размер составляют ±0,4 мм.
|
|
Допуск на черновое растачивание - 400 мкм (H12), допуск на получистовое чистовое растачивание – 100 мкм (H10), на чистовое растачивание - 40 мкм (H7).
Качество поверхности заготовки Rz40. Глубина дефектного слоя, получаемого при механической обработке алюминиевого сплава h=250 мкм.
На основании записанных в таблице данных производится расчет минимальных значений межоперационных припусков, пользуясь основной формулой:
, (7)
где Rzi -1 – шероховатость поверхности на предыдущей операции, мкм;
hi-1 – величина дефектного слоя, мкм;
εgi – погрешность установки на данной операции, мкм
Пространственное отклонение для заготовки при литье в кокиль.
(8)
где rкор - погрешность заготовки короблению, rкор =7мкм;
rсм - величина смещения отверстия, rсм =33 мкм.
По формуле (8) определяем суммарную погрешность заготовки:
=33,7 мкм =34 мкм
Остальные пространственные отклонения считаются по формуле/2/:
, (9)
|
|
где Kу– коэффициент уточнения формы
=0,06 – при однократном и черновом точении.
=0,05 – при получистовом точении.
=0,04 – при чистовом точении.
После черновой обработки:
.
После получистового точения:
После чистового точения:
Погрешность установки определяется по формуле:
(10)
Погрешность базирования при обработке на плоскости и установочных пальцах.
(11)
где l=162 мм – длина обрабатываемого отверстия,
α – угол поворота заготовки на пальцах.
, (12)
где δ A=0,015 мм – допуск на базовое отверстие,
δ B=0,011 мм – допуск на палец,
Smin=0,517 мм – минимальный зазор между отверстием и пальцем,
l 1=72, l 2=206 мм – расстояния между базовыми отверстиями.
Тогда
Тогда погрешность базирования по формуле (11) будет равна
Погрешность закрепления заготовки εз=90 мкм
Погрешность установки по формуле (10) будет равна
εу п/ч=27 мкм
εу чист=1,3 мкм
Тогда подставляя значения в формулу (7) получим:
|
|
;
;
;
Номинальный припуск определяется по формуле:
; (13)
Тогда по формуле (13):
;
;
.
Графа «Расчетный размер» заполняется начиная с конечного (чертежного размера) путем последовательного вычитания расчетного минимального припуска каждого технологического перехода по формуле:
; (14)
;
;
.
В графе «допуск» записывается значения допусков на каждом технологическом переходе и заготовке. В графе «номинальный предельный размер» записывается округленное значение размера. Округление производится с точностью, определяемой допуском на данный переход или в сторону увеличения массы детали. При широких допусках округление рекомендуется выполнять в соответствии с /3/.
Наибольшие предельные размеры получаются по формуле:
(15)
Наименьшие предельные размеры получаются по формуле:
; (16)
Предельные значения минимальных припусков Zmin определяются как разность наименьших предельных размеров на предыдущей операции и наибольших предельных размеров на последующей:
|
|
мм=100>27,8мкм,
мм=100>94мкм.
мм=1300>1260мкм.
Предельные значения максимальных припусков Zmax как разность наибольших предельных размеров на предыдущей операции и наименьших предельных размеров на последующей:
мм=240мкм,
мм=600мкм,
мм=2500мкм.
Общие припуски вычисляются по формулам:
2Zomin=2Zomin чист +2Zominп/ч +2Zominчерн, (17)
2Zomax=2Zomax чист +2Zomaxп/ч +2Zomaxчерн, (18)
2Zo=2Zo чист +2Zoп/ч +2Zoчерн, (19)
Тогда
2Zomin=100+100+1300=1500 мкм,
2Zomax=240+600+2500=3340 мкм,
2Zo=200+500+1700=2400 мкм.
Таблица 3 - Расчет припусков и предельных размеров по технологическим переходам на обработку поверхности ø158H7(+0,04).
Технологические переходы обработки поверхности | Элементы припуска, мкм | Расчетный припуск 2 Zmin, мкм | Номинальный припуск 2Zomin, мкм | Расчетный размер, мм | Допуск, мкм | Предельные размеры, мм | Предельн. значение припуска, мкм | |||||||
Шероховатость | Дефектный слой | Пространств. погрешность | Погрешность установки | Номинальный | Наибольший | Наименьший | Номинальнычй | Наибольший | Наименьший | |||||
RZ | h | r | eу | |||||||||||
Заготовка | 40 | 40 | 34 | - | - | - | 155,679 | 800 | 155,6 | 156 | 155,2 | - | - | - |
Растачивание |
| |||||||||||||
черновое | 20 | 20 | 2,04 | 549 | 1260 | 1660 | 157,339 | 400 | 157,3 | 157,7 | 157,3 | 1700 | 2500 | 1300 |
получистовое | 6,3 | 6,3 | 0,102 | 27 | 134 | 494 | 157,833 | 100 | 157,8 | 157,9 | 157,8 | 500 | 600 | 100 |
чистовое | 1,25 | 1,25 | 0,004 | 1,3 | 27,8 | 167 | 158 | 40 | 158 | 158,04 | 158 | 200 | 240 | 100 |
Схема расположения припусков и допусков на обработку размера
Ø158H7(+0,04) представлена на рисунке 2.
Рисунок 2 – Схема расположения припусков и допусков на обработку размера ø158H7(+0,04)
Расчет операционных размеров
Производится расчет межоперационных размеров на обработку 240±1 мм. Для расчета межоперационных размеров необходимо составить схему механической обработки, а затем решить размерные цепи, где замыкающим звеном будет являться припуск на механическую обработку. В данном случае получается две размерные цепи. Минимальным припуском назначается
Схема размерных цепей представлена на рисунке 3.
Рисунок 3 – Схема размерных цепей
Таким образом, с помощью размерных цепей были определены все межоперационные размеры на обработку торцевой поверхности. Расчет показал, что припуск на заготовку, взятый из таблицы достаточен.
Нормирование операции 105
Дата добавления: 2020-04-25; просмотров: 257; Мы поможем в написании вашей работы! |
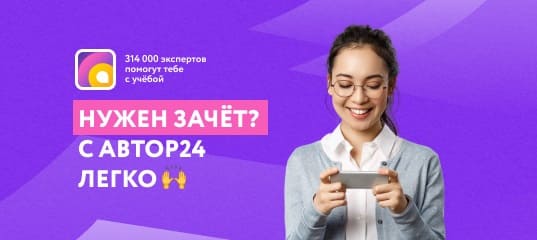
Мы поможем в написании ваших работ!