Подбор смазывающе-охлаждающих технологических средств
В качестве смазывающе-охлаждающих технологических средств принимается «Аквол-10м», это концентрат на гликолевой основе, содержит анионоактивные и неионогенные эмульгаторы и незначительное количество жировых присадок. Предназначен для приготовления синтетических СОЖ с широкой областью применения.
2.8.2 Расчет режимов резания детали «Корпус 6153
Методика и справочные данные приведены в /3/. Определяются режимы резания на фрезерование поверхности (операция 105 переход 1)
Исходные данные:
Агрегатный станок, мощность привода главного движения – 15 кВт;
Твердость обрабатываемого материала – 55…60HB;
Глубина резания - t=2 мм;
Подача S=0,5 мм/зуб;
Ширина фрезерования B=270мм;
Диаметр фрезы D=315;
Количество зубьев z=18.
Скорость резания определяется по формуле:
, (20)
где Сv=155, q=0,25, x=0,1, y=0,4, u=0,15, p=0,1, m=0,2 /3/,
Т=180 мин. – период стойкости инструмента (фрезы)
Kv – суммарный коэффициент, учитывающий условия обработки.
Кv=KMv*Kпv*Kuv, (21)
где KMv=1 – коэффициент, учитывающий влияние физико-механических свойств обрабатываемого материала, определяется по формуле:
Kпv=1 – коэффициент, учитывающий влияние состояния поверхности,
Kuv=0,9 – коэффициент, учитывающий влияние инструментального материала
По формуле (21) определяется:
|
|
КV = 1×1×0,9=0,9
Тогда скорость резания по формуле (20) равна
=82,8 м/мин
Частота вращения n, об/мин шпинделя станка определяется:
n= , (22)
где D – диаметр фрезы,
n= =83 об/мин.
По паспорту станка уточняется:
nф=80 об/мин,
Тогда фактическая скорость резания определяется по формуле:
Vф= , (23)
Vф= =79,1 м/мин.
Сила резания при фрезеровании рассчитывается по формуле
(24)
Коэффициенты берутся по справочнику /3/
где СР = 825; х=1; y=0,75; u=1,1; q= 1,3; w= 0,2; Kp=0,9.
Мощность резания N равна:
N=
N= =2,2 кВт.
Методика и справочные данные приведены в /3/. Определяются режимы резания на сверление четырех отверстий Ø12 (операция 105 переход 2).
Исходные данные:
Агрегатный станок, мощность привода главного движения – 15 кВт;
Твердость обрабатываемого материала – 55…60HB;
Глубина резания - t=6 мм;
Подача S=0,3 мм/об;
Диаметр сверла D=12.
Скорость резания определяется по формуле:
, (30)
где Сv=36,3, q=0,25, y=0,55, m=0,125 /3/,
|
|
Т=60 мин. – период стойкости инструмента,
Kv=1 – суммарный коэффициент, учитывающий условия обработки.
Тогда скорость резания по формуле (30) равна
=78 м/мин
Частота вращения определяется по формуле (19):
n= =2070 об/мин.
По паспорту станка уточняется:
nф=2000 об/мин,
Тогда фактическая скорость резания определяется по формуле (26):
Vф= =75,4 м/мин.
Сила резания:
, Н (31)
где
Для силы резания: Ср=9,8; q= 1; y= 0,7/3/.
Тогда,
Крутящий момент, рассчитывается по формуле:
(32)
где Сm=0,005, q=2, y=0,8, Kp=1 /3/,
Мощность резания N по формуле (28):
N= =0,56 кВт.
Методика и справочные данные приведены в /3/. Определяются режимы резания на сверление двух отверстий Ø9 (операция 105 переход 3).
Исходные данные:
Агрегатный станок, мощность привода главного движения – 15 кВт;
Твердость обрабатываемого материала – 55…60HB;
Глубина резания - t=4,5 мм;
Подача S=0,5 мм/зуб;
Диаметр D=9.
где Сv=36,3, q=0,25, y=0,55, m=0,125 /3/,
Т=30 мин. – период стойкости инструмента,
Kv=0,8 – суммарный коэффициент, учитывающий условия обработки.
|
|
Тогда скорость резания по формуле (30) равна
=22,45 м/мин
Частота вращения определяется по формуле (19):
n= =794 об/мин.
По паспорту станка уточняется:
nф=800 об/мин,
Тогда фактическая скорость резания определяется по формуле (26):
Vф= =22,6 м/мин.
Для силы резания: Ср=9,8; x= 1; y= 0,7/3/.
Тогда по формуле (31):
Для крутящего момента:
Сm=0,005, q=2, x=0,9, y=0,8, Kp=0,8 /3/,
Тогда по формуле (32):
Мощность резания N по формуле (28):
N= =0,01 кВт.
Методика и справочные данные приведены в /3/. Определяются режимы резания на черновое развертывание двух отверстий Ø9,9
(операция 105 переход 4). Исходные данные:
Агрегатный станок, мощность привода главного движения – 15 кВт;
Твердость обрабатываемого материала – 55…60HB;
Глубина резания - t=0,45 мм;
Подача S=0,5 мм/зуб;
Диаметр D=9,9.
где Сv=40,7, q=0,25, x=0,2, y=0,40, m=0,125 /3/,
Т=30 мин. – период стойкости инструмента,
Kv=0,8 – суммарный коэффициент, учитывающий условия обработки.
Тогда скорость резания по формуле (30) равна
=44,3 м/мин
Частота вращения определяется по формуле (19):
n= =1425 об/мин.
По паспорту станка уточняется:
nф=1400 об/мин,
Тогда фактическая скорость резания определяется по формуле (26):
|
|
Vф= =43,5 м/мин.
Для силы резания: Ср=9,8; x= 1; y= 0,7/3/.
Тогда по формуле (31):
Для крутящего момента:
Сm=0,02, q=0,85, x=0,8, y=0,8, Kp=0,8 /3/,
Тогда по формуле (32):
Мощность резания N по формуле (26):
N= =0,05 кВт.
Методика и справочные данные приведены в /3/. Определяются режимы резания на чистовое развертывание двух отверстий Ø10H9
(операция 105 переход 5). Исходные данные:
Агрегатный станок, мощность привода главного движения – 15 кВт;
Твердость обрабатываемого материала – 55…60HB;
Глубина резания - t=0,05 мм;
Подача S=1 мм/зуб;
Диаметр D=10.
где Сv=40,7, q=0,25, x=0,2, y=0,40, m=0,125 /3/,
Т=45 мин. – период стойкости инструмента,
Kv=0,8 – суммарный коэффициент, учитывающий условия обработки.
Тогда скорость резания по формуле (30) равна
=65,5 м/мин
Частота вращения определяется по формуле (19):
n= =2086 об/мин.
По паспорту станка уточняется:
nф=2100 об/мин,
Тогда фактическая скорость резания определяется по формуле (26):
Vф= =65,9 м/мин.
Для силы резания: Ср=9,8; x= 1; y= 0,7/3/.
Тогда по формуле (31):
Для крутящего момента:
Сm=0,005, q=2, x=0,9, y=0,8, Kp=0,8 /3/,
Тогда по формуле (32):
Мощность резания N по формуле (26):
N= =0,001 кВт.
Расчет норм времени
Норма штучного времени определяется по формуле /4/:
, (33)
где То - основное технологическое время на обработку, мин;
Тв - вспомогательное технологическое время, мин;
Тобсл - время на техническое обслуживание рабочего места, мин;
Тотд - время на отдых и естественные надобности, мин;
Тоо - время организационного обслуживания, мин.
Основное время на обработку определяется по формуле /4/:
, (36)
где - длина рабочего хода инструмента с учетом врезания и перебега;
i - число проходов;
Sо - подача инструмента, мм/об;
n - частота вращения инструмента, об/мин.
Расчет основного времени для фрезерования поверхности (операция 105 переход 1):
мин.
Расчет основного времени для сверления четырех отверстий (операция 105 переход 2):
мин.
Расчет основного времени для сверления двух отверстий (операция 105 переход 3):
мин.
Расчет основного времени для развертывания двух отверстий (операция 105 переход 4):
мин.
Расчет основного времени для развертывания двух отверстий (операция 105 переход 5):
мин.
Основное время всей операции определяется как сумма основного времени на каждом переходе:
Вспомогательное время на операцию рассчитывается по формуле, при этом учитывается только его часть, не перекрываемая машинным временем /4/:
, (37)
где
tуст=0,16 – время на снятие и установку заготовки;
tпуск=0,02 – время на пуск и остановку станка;
tпер.=0,15 – время связанное с переходом;
tизм=0,12 – время на измерение;
tвкл=0,02 – время на включение подачи.
Соответственно, вспомогательное время на операцию составит:
Оперативное время определяется как сумма основного и вспомогательного времени на операцию /4/:
, (38)
мин.
Время на техническое обслуживание рабочего места Тобсл составляет 3% от оперативного времени:
мин.
Время на отдых составляет 10% от оперативного времени:
мин.
Время организационного обслуживания рабочего места составляет 2% от оперативного времени:
Тоо=0,02·1,15=0,02 мин.
Таким образом, штучное время на операцию, составит:
мин.
Подготовительно-заключительное время определяется по формуле (32), в которой используются следующие исходные данные:
время на наладку станка, инструмента и приспособлений Т1 = 10 мин;
время на дополнительные приемы Т2 = 5 мин;
времени на получение инструмента и приспособлений до начала и сдачу их после окончания обработки, Т3 = 10 мин.
2.9 Расчет суммарной погрешности обработки поверхности Ø158 H 7+0,04
Расчет суммарной погрешности чистового точения поверхности Ø158H7+0,04 определится по формуле:
, (39)
где упр – погрешность, связанная с колебанием упругих отжатий системы;
изн – погрешность вызванная износом;
ст – погрешность, связанная с геометрической неточностью станка;
тепл – погрешность, вызванная тепловой деформацией;
з – погрешность закрепления;
пр – погрешность, связанная с неточностью приспособления;
см – погрешность смещения центра группирования относительно настроенного размера;
рег – погрешность регулировки;
изм – погрешность измерения.
Погрешность, связанная с колебаниями упругих отжатий определяется по формуле
упр=WmaxPmax-WminPmin, (40)
где Wmax и Wmin – максимальная и минимальная податливость станка, мкм/кН;
Pmax и Pmin – максимальная и минимальная составляющая силы резания, кН.
Сила Pz вычисляется по формуле:
Pz=10·Сpz×tXpz×SYpz×VNpz×Kp , (41)
где
Сpy- коэффициент, зависящий от постоянных условий обработки, Сpy=40;
t – глубина резания, t=3,375 мм;
S – подача, S=0,3 мм/об;
V – скорость резания, V=54,3 м/мин;
xpz, ypz, npz – показатели степени, соответственно при глубине резания, подаче, скорости резания (xpz= 1; ypz= 1; npz= 0);
Кр – коэффициент на изменённые условия, Кр=0,83.
Сила резания максимальна при глубине резания tmax, которая вычисляется по формуле:
tmax= tmin + , (42)
где tmax – минимальная глубина резания, tmin=3,375 мм;
TD – допуск на обработанную поверхность, Td=0,04 мм.
Тогда
tmax= 3,375 + =3,395 мм.
Минимальная сила резания по формуле (37):
Pymin=10·40×3,3751×0,31×54,30×0,83=336,1 Н
Максимальная сила резания:
Pymax=10·40×3,3951×0,31×54,30×0,83=338,1 Н.
Максимальная податливость станка:
Wmax=Wст +Wинстр , (43)
где Wст – податливость станка;
Wинстр – податливость инструмента, мкм/кН.
Wст= , (44)
где У – перемещение, У=50 мкм [2];
-предельное значение силы,
=980 Н ,
Тогда
W= =0,051 мкм/Н.
Податливость инструмента принимается Wинстр=0, так как его вылет довольно мал, тогда: Wmax= Wст=0,051 мкм/Н.
Минимальная податливость: Wmin= Wmax=0,051 мкм/Н.
Тогда по формуле (36):
=0,051 ×338,1 – 0,051 ×336,1=0,1 мкм.
Погрешность, вызванная износом инструмента, определяется по формуле:
, (45)
где uо – удельный износ материала резца, uо=2 мкм/км /5/;
Lрез - длина резания инструмента в период стойкости,
Lн – начальный перебег инструмента, Lн=1000 м.
(46)
где V – скорость резания,
Т – период стойкости инструмента.
Длина пути резания при обработке одной детали:
Lg = , (47)
где l – длина обрабатываемой поверхности,
S – подача, мм/об.
Lg =
Тогда, возможное количество деталей, обработанное за период стойкости резца будет равняться:
(48)
Погрешность, связанная с геометрической неточностью станка:
=
, (49)
где Сm – допускаемое отклонение от параллельности оси шпинделя и направляющих станка в вертикальной плоскости, Сm =6 мкм;
lm – длина обрабатываемой поверхности, lm =162 мм;
L – базовая длина, L=100 мм.
По формуле (52):
=
=5,7 мкм
Погрешность, вызванная тепловыми деформациями, определяется по формуле:
=B×(
), (50)
где В – коэффициент для лезвийной обработки, В=0,1.
Тогда
=0,1×(0,1+8,5+5,7)=1,4 мкм.
Погрешность смещения центра группирования определяется по формуле:
=
, (51)
где ωm – мгновенное поле рассеивания, мкм;
m – количество пробных деталей, m=5.
ωm =1,2× , (52)
ωm =1,2× =12,4 мкм.
Тогда по формуле (54):
=
=5,5 мкм.
Погрешность регулирования положения режущего инструмента на станке, мкм:
=1 мкм.
Погрешность измерения, мкм:
=10 мкм.
Погрешность закрепления:
=30 мкм
Погрешность неточности приспособления:
=10 мкм
Тогда суммарная погрешность обработки для диаметральных размеров определяется по формуле (42):
Δ∑=2,4 =85 мкм
Так как Δ∑=87,1 мкм не удовлетворяет условию: Δ∑≤0,8TD=40мкм, то заданный размер на данном переходе с достаточной точностью, при таком количестве деталей обеспечиваться не будет.
Таким образом, чтобы уменьшить ожидаемую погрешность, необходимо уменьшить погрешность, связанную с износом режущего инструмента. Она оказывает влияние не только непосредственно, но и воздействуя на величину некоторых других погрешностей. Для ее уменьшения следует задавать меньшее время стойкости режущего инструмента, так как при обработке стали имеет место интенсивный его износ, особенно по задней поверхности.
Погрешность, вызванная износом режущего инструмента определится по формулам:
LN =Lg×N, (53)
где LN – длина пути резания для партии N заготовок.
LN =476,2×6=2857,2 м.
=u0 ×
, (54)
=2×
=2,8 мкм.
Погрешность, вызванная тепловыми деформациями, определяется по формуле (53):
=0,1×(0,1+2,8+5,7)=0,86 мкм.
Погрешность смещения центра группирования определяется по формуле (54, 55):
=
=5,3 мкм.
Тогда суммарная погрешность обработки для диаметральных размеров определяется по формуле (42):
Δ∑=2,4 =82 мкм
Т.е. после 6 деталей необходимо заменить инструмент. Иначе получится брак.
2.10 Определение загрузки станков и требуемого количества оборудования
Правильный выбор оборудования определяет его рациональное использование во времени. При выборе станков для разработанного технологического процесса этот фактор должен учитываться таким образом, чтобы исключить их возможные простои.
Коэффициент загрузки определяется по формуле:
(55)
где расчетное количество станков, шт;
принятое (фактическое) число станков, шт.
Расчетное количество станков определяется по формуле:
(56)
Коэффициент использования оборудования по основному времени показывает долю машинного времени в общем времени работы станка:
(57)
Дата добавления: 2020-04-25; просмотров: 245; Мы поможем в написании вашей работы! |
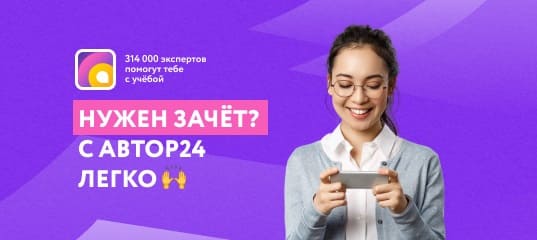
Мы поможем в написании ваших работ!