Анализ технологичности конструкции детали «Корпус 6128». Расчет такта выпуска, определение типа производства
Введение
Человеческое общество не может существовать и развиваться без постоянного производства продукции самого разнообразного назначения. В свою очередь производство уже нельзя представить без применения машин. Их изготовление – особая область человеческой деятельности, основанная на использовании закономерностей технологии машиностроения.
Отличительной особенностью современного машиностроения является существенное ужесточение эксплуатационных характеристик машин: увеличиваются скорость, ускорение, температуры, уменьшается масса, объем, вибрация, время срабатывания механизмов и т.п. Темпы такого ужесточения постоянно возрастают, и машиностроители вынуждены все быстрее решать конструкторские и технологические задачи. В условиях рыночных отношений быстрота реализации принятых решений играет главенствующую роль.
Технология машиностроительного производства представляет собой совокупность различных технологических процессов – литья, ковки, штамповки, термической обработки, окраски и др. Технология же машиностроения охватывает заключительные стадии машиностроительного производства – превращение заготовок в готовые детали и сборку, т.е. изготовление машин/1/.
Обзор и анализ научно-технологической и патентной информации.
Различают следующие виды зажимных устройств:
1. Резьбовые с прихватами;
|
|
2. Резьбовые кулачковые;
3. Резьбовые разные (например резьбовой с штифтовым упором);
4. Эксцентриковые (клиновые);
5. Зажимы по резьбовой поверхности;
6. Блокированные (резьбовые и клиновые).
Из перечисленных зажимных устройств, рассмотрим наиболее типичные, то есть резьбовые с прихватами.
№ 1 Прихват отводной с отнесенным болтом.
Обеспечивает надежное крепление и хороший доступ к месту зажима. Положение прихвата по высоте регулируется.
№ 2 Прихват с эксцентриковым отводом.
Отвод прихвата осуществляется одновременно с разжимом благодаря воздействию эксцентрикового кулачка 1 на упорный уголок 2. При зажиме эксцентриковый кулачок отходит от уголка и прихват под действием пружины 3 возвращаются положение для зажима.
№ 3 Прихват отводной внутренний.
Применяют для зажима в труднодоступных местах. При смене заготовки отводится в сторону вместе с болтом.
№ 4 Прихват с рукояткой.
Рукоятка исключает применение кулачка.
№ 5 Зажим через бон..
Применяют для крепления заготовок в приспособлениях закрытого типа, когда со стороны крепления копир, кондукторная плита или стенка приспособления, которые по соображениям точности нельзя загружать зажимными усилиями.
|
|
№ 6 Прихват с плунжером.
Допускает закрепление в двух точках, смещенных одна относительно другой по направлению зажима. Плунжер 1 в поднятом состоянии удерживается пружиной 2.
№ 7 Прихват отводной для крепления с внутренней стороны.
Применяют для крепления заготовок, имеющих внутренние буртики. Отводится через паз в корпусе приспособления.
№ 8 Прихват отводной качающийся
Обеспечивает надежное крепление. Высота зажима не регулируется. При смене заготовки, прихват отводят в сторону.
№ 9 Прихват с вынесенной рукояткой.
Применяют для крепления заготовок в труднодоступных местах. Рукоятка управления вынесена вверх.
№ 10 Зажим откидной с планкой и болтом.
Применяют в тех случаях, когда заготовку устанавливают и снимают со стороны зажима. При большом расстоянии между опорными точками планки применять не рекомендуется.
№ 11 Прихват с вынесенной рукояткой.
Применяют для крепления заготовок со стороны, закрытой стенкой приспособления. Требует значительного отвода вследствие качания планки.
№ 12 Зажим рычажный накидной.
|
|
Применяют для закрепления сверху по окружности или вдоль заготовки. При смене заготовки откидывают вместе с винтом.
№ 13 Зажим, устраняющий деформацию корпуса приспособления
Применяют в условиях, не допускающих деформации корпуса приспособления под действием зажимающего усилия
№ 14 Прихват откидной.
Применяют для зажима по двум точкам. При смене заготовки прихват отводят и поворачивают. Сильного зажима не обеспечивает
Технологическая часть
Анализ технологичности конструкции детали «Корпус 6128». Расчет такта выпуска, определение типа производства
Деталь “Корпус 128” (представлена в графической части курсового проекта на чертеже ТПЖА.731000.128-01). Заготовка получается из литейного алюминиевого сплава АК7ч. Деталь имеет крепежные отверстия, плоские поверхности, внутренние и наружные цилиндрические поверхности.
Применяются виды механической обработки – растачивание, сверление, зенковка, фрезерование, зенкерование, развертывание, цекование, нарезание резьбы.
Для обработки черновых баз, а так же фрезерования верхней плоскости, торцев, растачивания отверстия, цекования лапок, сверления отверстий, зенкования фасок и нарезания резьбы используется агрегатный станок.
|
|
Все заданные на чертеже размеры можно измерить и проверить широко распространенными мерительными инструментами: скобой, пробкой, шаблоном и калибром. Для контроля позиционных допусков применяются комплексные калибры. Для контроля допуска параллельности, необходимо спроектировать специальное контрольное приспособление.
Определение такта выпуска и типа производства
Величина такта выпуска рассчитывается по формуле:
tВ= , (1)
где
Fд =4015ч. – действительный годовой фонд времени работы оборудования;
N=200000 шт. - годовая программа выпуска детали.
tВ = =1,2 мин/шт.
Для определения типа производства рассчитывается коэффициент серийности по формуле:
КС= . (2)
где Tшт.ср. – среднее штучное время.
Для определения среднего штучного времени Tшт.ср. рассчитывается основное технологическое время Tо, укрупнено для каждой операции технологического процесса. Результаты расчета сведены в таблицу 1.
Таблица 1 – Расчет основного технологического времени.
№ опе-рации | Название | № пере-хода | Название перехода | d | l | Формулы | То, мин | |
1 | 2 | 3 | 4 | 5 | 6 | 7 | 8 | |
105 | Агрегатная | 1 | Фрезерование | - | 196 | 0,006×l | 1,17 | |
2 | Сверление | 12 | 18 | 0,00052×d×l | 0,11 | |||
3 | Сверление | 12 | 18 | 0,00052×d×l | 0,11 | |||
4 | Сверление | 9 | 18 | 0,00052×d×l | 0,08 | |||
5 | Зенкерование | 9.9 | 18 | 0,00021×d×l | 0,03 | |||
6 | Развертывание | 10 | 18 | 0,00043×d×l | 0,07 | |||
| ∑=1,57 | |||||||
110 | Агрегатная | 1 | Фрезерование | - | 196 | 0,006×l | 1,02 | |
2 | Сверление | 4.2 | 13 | 0,00052×d×l | 0,02 | |||
3 | Нарезание резьбы | 5 | 10 | 0,0004×d×l | 0,02 | |||
4 | Растачивание | 156,5 | 95 | 0,00018×d×l | 2,67 | |||
5 | Растачивание | 157 | 95 | 0,00018×d×l | 2,68 | |||
6 | Фрезерование | - | 240 | 0,006×l | 1,44 | |||
7 | Сверление | 6,75 | 15,5 | 0,00052×d×l | 0,05 | |||
8 | Сверление | 6.75 | 15,5 | 0,00052×d×l | 0,05 | |||
9 | Цекование | 10 | 8 | 0,00021×d×l | 0,01 | |||
10 | Цекование | 10 | 8 | 0,00021×d×l | 0,01 | |||
| ∑=7,97 | |||||||
115 | Агрегатная | 1 | Фрезерование | - | 196 | 0,006×l | 1,02 | |
2 | Сверление | 4.2 | 13 | 0,00052×d×l | 0,02 | |||
3 | Нарезание резьбы | 5 | 10 | 0,0004×d×l | 0,02 | |||
4 | Растачивание | 156,5 | 95 | 0,00018×d×l | 2,67 | |||
5 | Растачивание | 157 | 95 | 0,00018×d×l | 2,68 | |||
∑=6,41 | ||||||||
120 | Алмазно расточная | 6 | Растачивание | 95 | 0,00018×d×l | 2,70 | ||
| ∑=2,70 | |||||||
ИТОГО | 18,65 |
Примечание:
d - диаметр обрабатываемой поверхности, мм;
l - длина обрабатываемой поверхности, мм.
Штучное время вычисляется по формуле:
Tшт=φк·Tо (3)
Расчет штучного времени сведен в таблицу 2.
Таблица 2 – Расчет штучного времени.
№ опе-рации | Название | № пере-хода | Название перехода | jк | То, мин | Тшт=jк*Т0, мин |
1 | 2 | 3 | 4 | 5 | 8 | 7 |
105 | Агрегатная | 1 | Фрезерование | 1,51 | 1,17 | 1,76 |
2 | Сверление | 1,3 | 0,11 | 0,14 | ||
3 | Сверление | 1,3 | 0,11 | 0,14 | ||
4 | Сверление | 1,3 | 0,08 | 0,10 | ||
5 | Зенкерование | 1,3 | 0,03 | 0,04 | ||
6 | Развертывание | 1,3 | 0,07 | 0,09 | ||
2,27 | ||||||
110 | Агрегатная | 1 | Фрезерование | 1,51 | 1,02 | 1,54 |
2 | Сверление | 1,3 | 0,02 | 0,02 | ||
3 | Нарезание резьбы | 1,3 | 0,02 | 0,02 | ||
4 | Растачивание | 1,41 | 2,67 | 3,76 | ||
5 | Растачивание | 1,41 | 2,68 | 3,77 | ||
6 | Фрезерование | 1,51 | 1,44 | 2,17 | ||
7 | Сверление | 1,3 | 0,05 | 0,06 | ||
8 | Сверление | 1,3 | 0,05 | 0,06 | ||
9 | Цекование | 1,3 | 0,01 | 0,01 | ||
10 | Цекование | 1,3 | 0,01 | 0,01 | ||
11,42 | ||||||
115 | Агрегатная | 1 | Фрезерование | 1,51 | 1,02 | 1,54 |
2 | Сверление | 1,3 | 0,02 | 0,2 | ||
3 | Нарезание резьбы | 1,3 | 0,02 | 0,2 | ||
4 | Растачивание | 1,41 | 2,67 | 3,76 | ||
5 | Растачивание | 1,41 | 2,68 | 3,77 | ||
9,47 | ||||||
120 | Алмазно расточная | 6 | Растачивание | 1,41 | 2,70 | 3,81 |
3,81 | ||||||
ИТОГО |
Среднее штучное время определяется по формуле:
Тшт.ср= . (4)
где k – количество всех переходов каждой операции,
n – количество операций.
Тшт.ср= мин.
Тогда коэффициент серийности равен:
КС= .
Дата добавления: 2020-04-25; просмотров: 428; Мы поможем в написании вашей работы! |
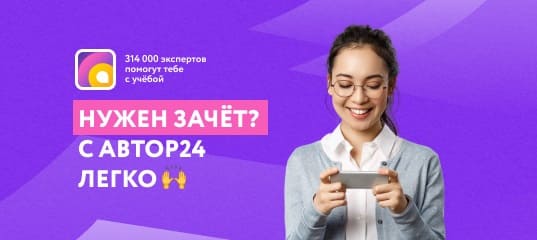
Мы поможем в написании ваших работ!