Сухая фторидная технология получения магнитных сплавов
С целью устранения недостатков вышеперечисленных технологий на Сибирском химическом комбинате (СХК), в плане его конверсии, с учетом его особенностей и действующих на нем технологий производства специальных материалов, совместно с СТИ ТПУ была проведена серия работ по разработке принципиально новой малоотходной технологии, вписываю-щейся в технологию основного производства [80, 84]. Результатом явилось создание на СЗ и ХМЗ СХК производства получения сплавов на основе Nd-Fe-B внепечным способом по сухой фторидной технологии с применением элементного фтора. Она включает следующие основные переделы: получение фторидов редкоземельных и переходных металлов, восстановление этих фторидов, получение магнитов и переработку отходов.
Принципиальная схема данной технологии приведена на рисунке 7.
Рисунок 7 – Принципиальная схема сухой фторидной технологии
получения магнитных материалов на основе РЗМ
Основными достоинствами этой технологии являются:
- универсальность газообразного фтора, как фторирующего агента. Он может быть применен для переработки практически любого вида сырья: оксидов, металлов, концентратов, отходов, содержащих РЗЭ;
- высокая интенсивность процесса;
- уникальность физико-химических свойств фторидов, получающихся по этой технологии. Например, их меньшая склонность к гидролизу и больший (в 2-4 раза) тепловой эффект металлотермического восстановления по сравнению с хлоридами. Это позволяет работать с ними в атмосферных условиях и получать компактные сплавы внепечными способами;
|
|
- возможность использования в производстве большого научного и производственного опыта, накопленного в атомной промышленности, по получению и применению фтора, синтезу фторидов, металлотермическому восстановлению;
- экологические достоинства, основанные на короткой, малоотходной схеме, отсутствии жидких отходов и возможности регенерации фтора.
Подробное описание данной технологии приведено в многочисленных публикациях [41,42,80,110-114]. Однако, если в них достаточно подробно приведены и описаны физико-химические и технологические особенности переделов получения фторидов РЗМ и переходных металлов, получения сплавов и лигатур, переработки отходов, то получению магнитов методами порошковой металлургии и, в частности, получению порошков РЗ-сплавов для изготовления магнитов уделено, на наш взгляд, недостаточное внимание. А именно это – одна из важнейших стадий, лимитирующая качество конечного изделия – магнита.
Получение порошков магнитных сплавов
Для получения порошков магнитных сплавов используют:
|
|
- многостадийное механическое измельчение магнитных сплавов до получения частиц доменов с размерами 2-10 мкм;
- распыление расплавленного металла из вращающегося тигля;
- HDDR-измельчение (гидрогенизация, диспропорционирование, десорбция, рекомбинация) [127].
Рассмотрим более подробно эти способы, их достоинства и недостатки.
Механическое измельчение осуществляется:
· с помощью щековой дробилки;
· с помощью шаровой вибромельницы.
Основными рабочими органами щековой дробилки служат неподвижная щека, составляющая часть станины, и подвижная щека. Щёки защищены от истирания стальными рифлеными литыми плитами из износоустойчивой марганцевой стали. Подвижная щека, подвешенная в верхней части на оси, может совершать колебательное движение. Нижний зазор между щеками, а следовательно, и размеры выходящего из дробилки материала регулируются колодками. Материал поступает в верхнюю часть пространства между щеками, измельчается раскалыванием и раздавливанием за счёт возвратно-поступательного движения подвижной щеки, постепенно проваливается и выходит через нижнюю щель. Измельчение происходит при рабочем ходе, когда расстояние между щеками уменьшается.
|
|
Достоинства щековой дробилки: позволяет дробить куски размером до 1,5 м в поперечнике.
Недостатки щековой дробилки: применяется для крупного дробления при подготовке сырья, потребляется значительное количество энергии.
Шаровая вибромельница состоит из корпуса, покоящегося на пружинной подставке, загруженного на 70-80% объёма шарами. Корпус мельницы приводится в колебательное движение валом, имеющим дисбаланс и частоту вращения 1000-3000 об/мин. При вращении неуравновешенной массы вала шары вместе с загруженным материалом совершают движение по эллиптическим траекториям в плоскостях, перпендикулярных оси вращения вала. Мелющие тела при этом вращаются вокруг собственных осей и всё содержимое приводится во вращение по направлению, обратному вращению вала. Происходят соударения мелющих частиц, их скольжение и интенсивное истирание материала. В вибрационных мельницах помол производится сухим и мокрым способами.
Достоинства шаровой вибромельницы: высокий коэффициент заполнения объёма (Кзап= 80-85%); небольшое время обработки материалов (обычно 0,5-2 часа); благодаря интенсивному ударно-истирающему действию обеспечивается высокая дисперсность продукта и однородность размеров измельчаемого материала.
|
|
Недостатки шаровой вибромельницы: намол материала мельницы и шаров; относительно низкая производительность за счёт наличия в рабочем объёме рабочих тел, занимающих до 80% объёма; вследствие трения всей массы шаров и материала значительная часть подводимой энергии переходит в теплоту, вызывая разогрев, поэтому нельзя применять для помола материалы с низкой температурой плавления; значительная часть подводимой энергии затрачивается на преодоление инерционных усилий корпуса мельницы и мелющих тел.
Из вышеизложенного следует, что механическая обработка очень дорогая операция, основными недостатками которой являются: легкая окисляемость порошков, высокая твердость сплавов, сложность и многостадийность процесса. Всё это привело к разработке новых способов измельчения, лишенных этих недостатков [29,30]. Это – распыление расплава из вращающегося тигля (разработка ВНИИНМ) и быстрое охлаждение расплава на массивном вращающемся медном цилиндре (рисунок 8) [87-88], а также водородное (гидридное) измельчение [83-86]. В настоящее время, ввиду высокой экономичности и эффективности, водородное измельчение используется на большинстве предприятий, производящих магнитные материалы.
а б
Рисунок 8 – Методы получения быстроказаленных сплавов
Процесс гидридного измельчения сплавов Nd-Fe-B осуществляется путем дробления слитка магнитного сплава на куски размером 10-20 мм и обработки их водородом. Этот процесс известен как водородная декрипитация (HD). Температура процесса 300-3500С. При этом происходит гидрирование межзёренной богатой неодимом фазы и ее деструкция (рисунок 9). После гидрирования материал легко разрушается в порошок 1-3 мкм, так как зерна основной фазы Nd-Fe-B уже не связаны.
Достоинства метода HD: высокая производительность и простота процесса, получаемые порошки стабильного качества, легко измельчаются, продолжительность измельчения незначительное. За это время не происходит окисления прогидрированного продукта, измельчение идёт, в основном, по границам зёрен Nd2Fe14B.
Недостатки метода HD: опасности при работе с водородом.
Рисунок 9 – Процесс водородного охрупчивания (HD)
Полученные порошки сплавов Nd-Fe-B по одному из рассмотренных методов готовы для прессования из них магнитов.
Прессование порошков в магнитном поле осуществляется либо "сухим" либо "мокрым" способами. Наилучшая текстура получается при уплотнении "мокрым" способом, а наивысшая плотность – при газо- и гидростатическом прессовании [89], а также при уплотнении взрывной волной [70].
Спекание заготовок для получения высоких значений плотности, намагниченности и коэрцитивной силы производится в вакууме или инертной атмосфере. Для получения высоких свойств Br, Hcm, (BH)max для каждого состава сплава требуется своя температура и время спекания. Влияние этих параметров на свойства магнитов подробно рассматриваются в работах [91-92].
Высокотемпературный отжиг после спекания магнитов Nd-Fe-B осуществляется для повышения коэрцитивной силы в интервале температур 500-700 °С.
В последнее время все большее внимание специалистов привлекает второй способ изготовления ПМ Nd-Fe-B – метод центрифугирования из расплава, разработанный американской фирмой "General Motors Co" [93-94]. Полученные таким образом ПМ получили название магниты системы "magnequench". При данном способе сверхбыстрой закалки расплавленный в инертной атмосфере сплав направляется на поверхность быстро-вращающегося барабана и, мгновенно на нем охлаждаясь, затвердевает. В зависимости от скорости вращения барабана сплав, затвердевший в форме чешуек, мелких частиц или лент, будет иметь различную аморфную структуру: изотропную или кристаллическую. Полученные ленты, чешуйки и порошок при необходимости доизмельчаются и из них изготавливают либо изотропные магниты и магнитопласты, либо анизотропные магниты. Магнитопласты получаются так же как и изотропные магниты прессованием порошков с различными наполнителями. Их свойства составляют от 60 до 80% от свойств магнитов, полученных по технологии порошковой металлургии. Анизотропные же магниты изготавливаются путем горячего прессования этих порошков и осадки их в матрице. Их магнитные характеристики не ниже, чем у магнитов, полученных методом ПМ, а плотность, в отличии от них, близка к 100 %.
Наряду с совершенствованием указанных выше методов получения магнитов, разрабатываются новые способы их изготовления:
- механическое сплавление порошков с последующим взаимодействием в твердой фазе [95]. Свойства магнитов сравнимы с магнитами "magnequench";
- горячая механическая обработка (экструзия, горячее прессование, прокатка) отливок из сплавов Nd-Fe-B, помещенных в стальную оболочку при температуре 750-950°С [96,97]. Свойства магнитов не уступают магнитам, полученным методом порошковой металлургии. Разрабатываются и другие методы. Подробный обзор нетрадиционных способов изготовления ПМ на основе Nd-Fe-B изложен в обзорах [28,30,98,99].
В последние несколько лет ведутся активные исследования по разработке метода твёрдофазного синтеза магнитных материалов на основе РЗМ [115]. Метод основан на взаимодействие нанопорошков исходных компонентов магнитного материала с активированной поверхностью. Активация поверхности проводится в специальных мельницах, способных сообщать мелющимся телам энергии в десятки килоджоулей. Частицы преодолевают активационный барьер и образуются кристаллы магнитной фазы. Полученные кристаллы обладают высокой анизотропией, при этом из технологического цикла исключается операция сплавления компонентов. В работе [115] в качестве РЗМ – составляющей вводится гидрид неодима, в результате установлено, что водород, отщепляемый в ходе измельчения, облегчает твёрдофазное взаимодействие между железом и неодимом, а магнитные характеристики синтезированных порошков превосходят характеристики порошков, полученных обычным HD способом.
Одним из направлений твёрдофазного синтеза магнитных материалов является твёрдофазное легирование (ТФЛ) [117]. Этот метод разрабатывался, в основном, для исправления состава некондиционных по химическому составу магнитных порошков, однако его можно использовать, в перспективе, и для синтеза магнитной фазы. Легирующая добавка вводится на этапе помола магнитного сплава и равномерно распределяется по всей массе порошка. Данный метод имеет существенный недостаток – легирующий высоконеодимовый сплав Nd-Fe практически не может быть измельчён существующими механическими методами.
Таким образом, после обзора литературных данных можно сказать, что технология твердофазного легирования актуальна и востребована в магнитном производстве, поэтому и была поставлена задача получения гидрированием из этих сплавов порошков, отвечающим требованиям метода ТФЛ.
Дата добавления: 2020-01-07; просмотров: 280; Мы поможем в написании вашей работы! |
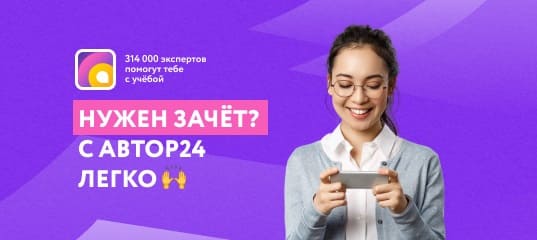
Мы поможем в написании ваших работ!