Поэтому, создание и развитие российской редкоземельной промышленности в данный период является выгодным как экономически, так и стратегически.
Способы получения магнитных сплавов на основе РЗМ
Обзор способов получения магнитных сплавов на основе РЗМ
Магниты на основе Nd-Fe-B получают, в основном, двумя способами - композитным – путем холодного прессования, экструдирования или колондрования металлических порошков совместно с полимерным связующим и способом порошковой металлургии путем спекания спрессованных металлических порошков при температурах, близких к плавлению. Оба способа имеют свои достоинства и недостатки и позволяют производить широчайшую гамму магнитных изделий различных конфигураций и свойств. Первой стадией обоих методов является операция получения сплавов Nd-Fe-B следующими основными способами:
- сплавлением компонентов [47-51];
- электролизом [52-55];
- металлотермическим печным или внепечным восстановлением [56-60].
Плавка индивидуальных компонентов сплавов проводится в вакууме или инертной среде в индукционных или электродуговых печах. Методы сплавления являются двустадийными – первоначально получаются отдельные компоненты в виде металлов или лигатуры, а затем эти полупродукты переплавляются с целью получения сплавов Nd-Fe-B различного состава. Индивидуальные РЗМ получаются либо методом печной металлургии при нагревании исходной шихты, состоящей из фторидов, хлоридов или оксидов РЗМ и металла – восстановителя (чаще всего кальция или гидрида кальция), до температур 800-1200°С, либо путем электролиза, в основном галогенидов, при температуре 800-1200°С [61-63]. Для получения из этих металлов магнитных сплавов требуется их предварительная очистка от примесей, например, электрорафинированием или переплавом в вакууме в индукционных, дуговых, электронно-лучевых, плазменно-индукционных или других типах печей.
|
|
Получение сплавов на основе Nd-Fe-B в большинстве случаев в промышленности осуществляется в инертной атмосфере индукционным способом, обеспечивающим хорошее перемешивание. РЗМ вводят после расплавления остальных компонентов в жидкий расплав. Для получения сплавов со столбчатой структурой, обладающих ярко выраженными анизотропными свойствами, используют охлаждение в массивных или охлаждаемых кристаллизаторах. Бор вводят в расплав либо в виде чистого металла, либо в виде лигатуры Fe-B с различным содержанием бора. В качестве материала тигля используют алунд, карбонитрид бора, тантал, ниобий или их сплавы. Данные процессы осложнены трудностью выбора конструкционных материалов для плавки и литья РЗМ из-за их чрезвычайно высокой химической активности и значительных в процессе плавки потерь РЗМ по причине высокого давления паров этих металлов при температурах 1300-1500 °С.
|
|
Электролитические способы производства РЗМ и магнитных сплавов основаны на электролизе или фторидов [52], или оксидов [54], или смеси фторидов и хлоридов РЗМ [64]. В качестве солевой ванны служат расплавы фторидов или хлоридов щелочных металлов (Li, Ca, Ba и т.д.). Обычно в качестве катода используется железо, а анода – уголь. Процесс ведется при температурах 650-1100 °С. Основными недостатками этих способов являются малый выход по току (65-70 %), значительные энергетические затраты и необходимость дополнительного рафинирования сплавов.
В металлотермическом способе получения магнитных сплавов отсутствуют дорогостоящие стадии получения и рафинирования РЗМ. В этом методе восстановлению подвергаются оксиды и концентраты оксидов [65-73], хлориды [74-76], фториды РЗМ [75, 77-80], смеси галогенидов и оксидов [78-79]. Переходные и легирующие элементы (Fe, Co и др.) вводятся в шихту для металлотермического восстановления в виде металлического порошка [65-77, 81,82], оксидов и галогенидов [78, 79], а бор – в виде металлического порошка [67-69, 74, 77-79, 81], ферробора [65, 66, 81], оксида [69, 82]. В качестве восстановителя соединений РЗМ, переходных металлов и бора используются металлический кальций, магний и их смеси [65,67,70-72,74,75-79,81,82], гидрид кальция или смесь гидрида кальция и кальция [68, 69, 73], щелочные металлы – литий, натрий [76,78], а также углерод [61]. Большинство из указанных процессов являются печными, то есть тепла, выделяющегося при протекании реакции восстановления соединений РЗМ и переходных металлов, недостаточно для перевода всех продуктов реакции в расплавленное состояние и формирования компактных слитков сплавов. Поэтому восстановление проводится при нагревании шихты до температур 800-1300 °С. Для снижения температуры плавления и увеличения жидко-текучести шлаков в шихту предлагается вводить хлорид кальция [79], а для увеличения масштаба плавки – прессовать шихту [79]. Фториды и хлориды РЗМ, применяемые для этого способа, получаются осаждением их из растворов плавиковой или соляной кислот с последующей сушкой и прокалкой осадков. Эти процессы не позволяют полностью удалить из продуктов влагу и, вследствие этого, на операциях восстановления выход РЗМ в слиток не превышает 80-85 %.
|
|
Недостатками рассмотренных выше методов прямого метало-термического получения сплавов является:
- необходимость подогрева системы в печи до высоких температур при использовании переходных РЗЭ в виде оксидов;
- высокая гигроскопичность и трудность получения безводных соеди-нений при использовании хлоридов металлов;
- наличие остаточной влаги и гидроксильной группы при исполь-зовании фторидов, полученных осаждением плавиковой кислотой;
- трудности переработки шлаков из-за их сложного состава при применении соединений РЗЭ и переходных металлов в виде оксидов, хлоридов и фторидов.
Дата добавления: 2020-01-07; просмотров: 217; Мы поможем в написании вашей работы! |
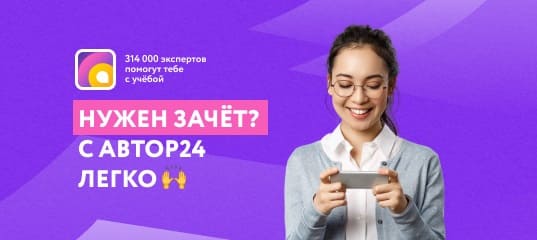
Мы поможем в написании ваших работ!