Проектировочный расчет на изгибную выносливость
Выбор материалов для изготовления зубчатых колес
Заготовки зубчатых колес могут быть получены ковкой, штамповкой и литьем. Существует также сборные конструкции зубчатых колес.
При выборе материала зубчатых колес, необходимо учесть следующие факторы:
1. Передаваемая мощность.
2. Условия ее работы.
3. Требования технологии.
4. Оборудование, на котором будут производиться зубчатые колеса.
Себестоимость.
6. Доступность материала.
7. Обрабатываемость.
8. Возможность осуществления термической обработке (ТО) или химико-термической обработки (ХТО).
9. Назначение передачи и д.р.
Для изготовления зубчатых колес в основном применяются, стали – конструкционные или легированные, чугуны, неметаллические материалы и сплавы цветных металлов. Они (стали) отличаются содержанием углерода. Стали можно подвергнуть ТО или ХТО. При содержании углерода - С > 0,35% , ТО – улучшение, нормализация. Твердость НВ<350. Объемной и поверхностной закалке подвергаются, стали с содержанием углерода, 0,4…0,5%, например, стали марок: 45, 50, 50Г, 40Х, 40Хн, 45ХН, 40ХН4А и д.р. Твердость при закалке 40…50НRC .
Стали с ТО – улучшение, нормализация, закалка (объемная), имеют однородную структуру, при применении поверхностной закалки и ХТО всех видов имеем неоднородную структуру материалов.
Для колес с твердостью активных поверхностей зубьев НВ>350 используется сталь марок 40, 45, 50, 50Г, 35Х, 40Х, 45Х, 40ХН, 45ХН, 35ХМА, 30ХН3А, 35ХМ и д.р.
|
|
Материал колес, может быть, подвергнут ХТО: цементации, азотированию, цианированию.
Цементация зубьев с последующей закалкой дает высокую твердость поверхностей зубьев, их твердость до 55…63 НRC при достаточно мягкой сердцевине. При этом используются стали с содержанием углерода 0,12…0,3%, марок: 15, 20, 15Х, 20ХР, 12ХН3, 12Х2Н4А, 12ХН3А, 20ХН3А, 18НГТ, 18ХНВА, 18ХН3А, 18ХФ и д.р. После цементации необходимо применять доводочные операции, например шлифование.
Цианирование также дает высокую поверхностную твердость (60…63НRC), но получаемый твердый слой имеет небольшую толщину. Применяются, стали марок 20Х, 35Х, 40Х, 30ХГТ, 20ХГТ и д.р. Цианирование является финишной операцией.
Азотирование обеспечивает высокую поверхностную твердость, но полученный твердый слой имеет небольшую толщину, что делает опасным подслойные разрушения. Азотирование является также финишной операцией. Для азотированных зубчатых колес обычно применяются, стали марок: 38ХМЮА, 35ХЮА, 38ХВФЮ, 30ХН2МФА, 45Х2Н2МФЮА и д.р.
Чугуны обладают хорошими литейными качествами и являются наиболее дешевым материалом. Колеса, выполненные из чугуна, хорошо обрабатываются и прирабатываются, поэтому шум, возникающий при работе передачи, меньше, чем у передач со стальными колесами. Для открытых передач, при спокойном режиме работы применяется серый чугун СЧ 18-36 и СЧ 21- 40. При окружных скоростях до 4…5 м/с рекомендуется применять модифицированный чугун марок СЧ 28-48 и СЧ 32-52, а также высокопрочный чугун марок ВЧ 45-5 и ВЧ 40-10.
|
|
Для изготовления зубчатых колес применяются неметаллические материалы. Данный вид материала применяется в малонагруженных, скоростных передачах и изделиях бытовой техники.
Проектировочный расчет
Проектировочный расчет на контактную выносливость
По заданию, исходя из указанных выше факторов, выбираем материалы и термообработку зубчатых колес.
Выбор материалов и способы термообработки зубчатых колес рекомендуется производить в зависимости от мощности на выходе (N ВЫХ).
1.1. Если N ВЫХ < 4 кВт
Материал зубчатых колес – Сталь 45, 40Х.
Термообработка:
шестерни – улучшение, нормализация, твердость Н1 = (269…262)НВ;
колеса – улучшение, нормализация, твердость Н2 = (235…262)НВ.
1.2. Если N ВЫХ = 4…8 кВт
Материалы зубчатых колес – Сталь 40Х, 40ХН.
Термообработка:
шестерни – закалка, твердость Н1 = (40…60)HRC;
колеса – улучшение, твердость Н2 = (269…302)НВ.
1.3. Если N ВЫХ = 8…15 кВт
|
|
Материалы зубчатых колес – Сталь 40Х, 40ХН.
Термообработка:
шестерни и колеса – закалка, твердость Н1 = Н2 (40…60)HRC.
1.4. Если N ВЫХ > 15 кВт
Материалы зубчатых колес – Сталь 20ХН2М, 12ХН2, 12ХН3А, 8ХГГ, 25ХГНМ.
Термообработка:
шестерни и колеса – цементация, твердость Н1 = Н2 (54…64)HRC;
колеса – нитроцементация, азотирование, твердость Н1 = Н2 (550…750)HV.
Примечание: Соотношения между числами твердости, определенной различными методами, приведены в приложении 1.
Минимальное число зубьев зубчатых колес, выполненных без смещения, для предотвращения подрезания принимается равным zmin = 17. Выбираем коэффициент ширины зуба: из ряда 0,1; 0,15; 0,2; 0,25; 0,315; 0,4; 0,5; 0,63; 0,8; 1,0; 1,25 придерживаясь, следующих рекомендаций:
Расположение колес относительно опор | ![]() |
Симметричное | 0,4-0,5 |
Несимметричное | 0,315-0,4 |
Консольное | 0,2-0,25 |
Коэффициент ширины зуба по диаметру определяем по формуле:
=
(3.1)
Полученное значение можно уточнить:
Твердость материалов зубчатых колес | Расположение колес относительно опор | ![]() | ||
Н1 £ НВ 350 и Н2 £ НВ 350 или Н2 ³ НВ 350 | При симметричном | 0,8…1,4 | ||
При несимметричном | 0,6…1,2 | |||
При консольном | 0,3…0,4 | |||
Н1 > НВ 350 и Н2 > НВ 350
| При симметричном | 0,4…0,9 | ||
При несимметричном | 0,3…0,6 | |||
При консольном | 0,2…0,25 |
Расчет на контактную выносливость зубьев служит для предотвращения усталостного выкрашивания активных поверхностей зубьев. Но следует отметить, что после проектировочного расчета необходимо выполнить уточненные проверочные расчеты.
Определяем межосевое расстояние из условия контактной выносливости активных поверхностей зубьев по формуле, мм:
, (3.2)
где «+» для внешнего зацепления, «–» для внутреннего зацепления;
Ka – вспомогательный коэффициент;
T2H – вращающий момент на валу колеса, Нм;
u – передаточное отношение;
– коэффициент, учитывающий неравномерность распределения нагрузки по длине контактных линий;
– коэффициент ширины зуба;
– допускаемое контактное напряжение, МПа.
Вспомогательный коэффициент Ka принимают по табл. 3.1:
Таблица 3.1
Значения коэффициента Ka
Вид колес | Ka | ||||||
Материалы шестерни и колеса | |||||||
Сталь-сталь | сталь-чугун | сталь-бронза | чугун-чугун | текстолит-сталь | ДСП- сталь | полиамид (капрон) – сталь | |
Прямозубые | 495 | 445 | 430 | 415 | 200 | 225 | 155 |
Косозубые и шевронные | 430 | 390 | 375 | 360 | 170 | 195 | 135 |
Коэффициент , учитывающий неравномерность распределения нагрузки по длине контактных линий, принимают в зависимости от параметра
, схемы передачи и твердости активных поверхностей зубьев по графику, представленному на рис. 3.1.
Допускаемые контактные напряжения определяют раздельно для шестерни и колеса по формуле, МПа:
, (3.3)
где – предел контактной выносливости, соответствующий базовому числу циклов напряжений, МПа;
SH – коэффициент запаса прочности;
ZN – коэффициент долговечности;
ZR – коэффициент, учитывающий шероховатость сопряженных поверхностей зубьев;
– коэффициент, учитывающий окружную скорость;
ZL – коэффициент, учитывающий влияние вязкости масла;
ZX – коэффициент, учитывающий размер зубчатого колеса.
В проектировочном расчете = 0,9.
В качестве допускаемого контактного напряжения для прямозубой передачи при проектировочном расчете принимают допускаемое напряжение того зубчатого колеса (шестерни или колеса), для которого оно меньше.
В качестве допускаемого контактного напряжения для косозубой и шевронной передачи при проектировочном расчете принимают условное допускаемое контактное напряжение, определяемое по формуле:
=
. При этом должно выполняться условие:
< 1,23
, где
– меньшее из значений
и
. В противном случае принимают
=
.
Предел контактной выносливости , соответствующий базовому числу циклов напряжений, принимают по таблице 3.2.
![]() |
![]() |
Рис. 3.1. График для определения коэффициента ![]() |
Таблица 3.2
Предел контактной выносливости при базовом числе циклов
Способ термической и химико-термической обработки зубьев | Средняя твердость поверхности зубьев | Сталь | Формула для расчета значений ![]() |
Отжиг, нормализация или улучшение | Менее НВ 350 | Углеродистая и легированная | ![]() ![]() |
Объемная и поверхностная закалка | HRC 38…50 | ![]() ![]() | |
Цементация и нитроцементация | Более HRC 56 | Легированная | ![]() ![]() |
Азотирование | HV 550…750 | ![]() |
При отсутствии необходимых фактических данных можно применить следующие минимальные коэффициенты запаса прочности SH:
– для зубчатых колес, выполненных из материала однородной структуры, принимаем SHmin = 1,1;
– для колес с поверхностным упрочнением зубьев SHmin = 1,2;
– для передач, выход из строя которых связан с тяжелыми последствиями, значения минимальных коэффициентов запасов прочности следует увеличить до SHmin = 1,25 и SHmin = 1,35 соответственно.
Коэффициент долговечности ZN, принимают в зависимости от отношения суммарного и базового числа циклов перемены напряжений в зубьях NK/NHlim по графику, представленному на рис 3.4 или по следующим формулам:
ZN = при
, но не более 2,6 для однородной структуры материала и 1,8 для поверхностного упрочнения;
ZN = при NK >
, но не менее 0,75 (при использовании метода эквивалентных циклов вместо NK подставляют N Н E),
где NHlim – базовое число циклов перемены напряжений;
NК – суммарное число циклов перемены напряжений;
Nне – эквивалентное число циклов перемены напряжений.
Суммарное число циклов перемены напряжений NК при постоянной нагрузке определяется следующим образом:
, (3.4)
где с – число зубчатых колес, сцепляющихся с рассчитываемым зубчатым колесом, n – частота вращения, рассчитываемого зубчатого колеса, об/мин, t – срок службы передачи, в часах.
Если не задано конкретное число часов работы передачи, а задан срок работы передачи в годах, то t определится по формуле:
(3.5)
где L – срок службы в годах, КГОД, КСУТ – коэффициенты использования передачи в течение года и суток соответственно.
При нагрузках, изменяющихся во времени вместо NК используется эквивалентное число циклов перемены напряжений Nне.
Nне можно определить по формуле: NНЕ = , где коэффициент
учитывает характер циклограммы нагружения. Для упрощенных расчетов можно учитывать только ту часть циклограммы, в которой число циклов нагрузки не более
.
При этом для ступенчатой циклограммы (рис. 3.2):
. (3.6)
При плавном характере циклограммы:
. (3.7)
При уточненных расчетах для постоянной частоты вращения и невысоких значений динамической добавки при коэффициент
определяют по формуле:
, (3.8)
где in - полное число ступеней нагрузки в циклограмме.
Допускается приведение реальной циклограммы к одному из типовых режимов нагружения. При этом эквивалентное число циклов находится по формуле:
, (3.9)
где значения коэффициента для различных режимов нагружения:
Режим нагружения
Тяжелый…………………………………………………………………….. 0,466
Средний равновероятностный…………………………………………….. 0,250
Средний нормальный……………………………………………………… 0,185
Легкий………………………………………………………………………. 0,060
| |
а) | б) |
Рис. 3.2 Циклограммы моментов и скоростей в зацеплениях для шестерни и колеса |
Базовое число циклов перемены напряжений определяется по графику, представленному на рис. 3.3, или по формуле:
. (3.10)
Используя все найденные параметры, определяется межосевое расстояние. Полученное межосевое расстояние при необходимости округляется до стандартного значения:
РЯД 1 – 40, 50, 63, 80, 100, 125, 160, 200, 250, 315, 400
РЯД 2 – 71, 90, 112, 140, 180, 225, 280, 355, 450
Значения первого ряда следует предпочитать значениям второго.
|
![]() | ||||
Рис. 3.3. График для определения базового числа циклов перемены напряжений ![]() | ||||
![]() | ||||
Рис. 3.4. График для определения коэффициента ZN |
Проектировочный расчет на изгибную выносливость
Проектировочный расчет служит только для предварительного определения размеров и не может заменить проведение проверочного расчета на выносливость зубьев при изгибе.
Исходными данными для проектировочного расчета являются:
циклограмма нагружения;
параметр (см. п. 3.1.) или межосевое расстояние
;
число зубьев шестерни z1;
угол наклона зуба ( или
);
коэффициент осевого перекрытия > 1 или
;
способ термической или химико-термической обработки и твердость рабочих поверхностей зубьев.
Расчет производится для шестерни:
Ориентировочное значение модуля т, при заданном параметре , вычисляют по формуле, мм:
, (3.11)
где Кт - вспомогательный коэффициент;
T1F – вращающий момент на валу шестерни, Нм;
u – передаточное число передачи;
– коэффициент, учитывающий неравномерность распределения нагрузки по ширине венца;
z1 – число зубьев шестерни;
– коэффициент ширины зуба по диаметру;
s FP1 – допускаемое изгибное напряжение, МПа;
YFS1 – коэффициент, учитывающий форму зуба.
Для прямозубых передач Кт = 14; для косозубых ( > 1) и шевронных передач Кт = 11,2; для косозубых (
) передач Кт = 12,5.
Ориентировочное значение модуля т, при заданном межосевом расстоянии , вычисляют по формуле, мм:
, (3.12)
где Кта – вспомогательный коэффициент;
– рабочая ширина зацепления зубчатой передачи, мм.
Для прямозубых передач Кта = 1400; для косозубых передач ( ) Кта = 1100; для коcозубых (
> 1) и шевронных передач Кта = 850.
Коэффициент , учитывающий неравномерность распределения нагрузки по длине контактных линий, принимают в зависимости от параметра
, схемы передачи и твердости активных поверхностей зубьев по графику, представленному на рис. 3.5.
Допускаемое изгибное напряжение определяют по формуле, МПа:
(3.13)
где – базовый предел выносливости зубьев, определяемый в зависимости от способа термической или химико-термической обработкипо приложению 3.
![]() |
![]() |
Рис. 3.5. График для определения коэффициента ![]() |
Коэффициент долговечности YN определяют по формуле:
но не менее 1, (3.14)
где qF – показатель степени;
NFlim – базовое число циклов перемены напряжений;
NК – суммарное число циклов перемены напряжений (при использовании метода эквивалентных циклов вместо NК подставляют N FE).
Для зубчатых колес с однородной структурой материала, включая закаленные при нагреве ТВЧ со сквозной закалкой, и зубчатых колес со шлифованной переходной поверхностью, независимо от твердости и термообработки их зубьев qF = 6.
Для зубчатых колес азотированных, а также цементированных и нитроцементированных с нешлифованной переходной поверхностью qF = 9.
Максимальные значения YN :
YN max = 4 при qF = 6,
YN max = 2,5 при qF = 9.
Базовое число циклов нагружения принимают циклов. Под базовым числом циклов нагружения понимают число циклов, соответствующее на диаграмме усталости переход наклонного участка кривой усталости в горизонтальный участок или участок с очень малым наклоном к оси циклов;
Суммарное число циклов перемены напряжений NК определяется аналогично как в п. 3.1.
При нагрузках, изменяющихся во времени вместо NК используется эквивалентное число циклов перемены напряжений N FE.
При ступенчатой циклограмме нагружения N FE (рис. 3.2) определяется по формуле:
, (3.15)
где . В том случае, когда
, следует принимать
= 0. При определении N FE можно исключать нагрузки, которым соответствуют напряжения
, меньшие, чем
.
При плавном характере циклограммы нагружения N FE определяется по формуле:
, (3.16)
При такой циклограмме нагружения допускается приведение ее к одному из типовых режимов нагружения. При этом эквивалентное число циклов определяется по формуле:
,
где значения при mF = 6 и m F= 9 (
и
) приведены в табл. 3.3.
Таблица 3.3.
Значения и
.
Режим нагружения | ![]() | ![]() |
Тяжелый Средний равновероятный Средний нормальный Легкий | 0.270 0.143 0.072 0.020 | 0.175 0.100 0.042 0.019 |
Коэффициент YFS, учитывающий форму зуба и концентрацию напряжений, принимают по кривым (рис. 3.6) в зависимости от эквивалентного числа зубьев и коэффициента смещения или приближенно по формуле:
, (3.17)
где ; x – коэффициент смещения, мм.
![]() |
Рис. 3.6. График определения коэффициент YFS |
![]() |
Рис. 3.7. График определения коэффициент YFS для зубьев, изготовленных инструментом с протуберанцем |
Для зубчатых колес, изготовленных с применением червячной фрезы пли зубострогальной гребенки с протуберанцем, коэффициент YFS принимают по кривым (рис. 3.7) в зависимости от и коэффициента смещения или приближенно по формуле:
(3.18)
Формулы 3.17 и 3.18 не учитывают влияния шлифовочных ступенек, которые могут привести к значительному увеличению концентрации напряжений.
Примечание. Для реверсивных зубчатых передач уменьшить на 25%.
Проектирование передачи
Ориентировочно значение модуля при проектировочном расчете можно принять, мм:
(3.19)
По ГОСТ 9563-80 принимают стандартный нормальный модуль:
РЯД 1 – 1; 1,25; 1,5; 2; 2,5; 3; 4; 5; 6; 8; 10; 12; 16
РЯД 2 – 1,125; 1,375; 1,75; 2,25; 2,75; 3,5; 4,5; 5,5; 7; 9; 11; 14
Значения первого ряда следует предпочитать значениям второго.
Определяем суммарное число зубьев и число зубьев шестерни и колеса по формулам:
Предварительно принимают угол наклона зубьев и определяют суммарное zC, число зубьев шестерни z1 и колеса z2:
, (3.20)
, (3.21)
Полученные значения чисел зубьев округляем до целого числа.
z2 = z С – z1. (3.22)
Определяется действительное передаточное число и его погрешность:
. (3.23)
Погрешность передаточного числа не должна превышать 3% .
Уточняем значение угла :
,
. (3.24)
Значение угла наклона зубьев необходимо вычислять с точностью до секунд.
Далее определяются основные размеры шестерни и колеса:
Делительные диаметры шестерни и колеса определяются по формуле:
. (3.25)
Проверку полученных диаметров можно провести с помощью формулы:
(3.26)
Проверкой должно быть установлено, что межосевое расстояние сходится со значением принятым ранее.
Диаметры вершин зубьев определяются по формуле:
,
, (3.27)
диаметры впадин:
,
, (3.28)
где x – коэффициент смещения, мм.
Ширина колеса определяется по формуле, мм:
. (3.29)
Полученное значение ширины колеса округляем до нормального линейного размера.
Ширина шестерни определяется по формуле, мм:
b1 = b2 + (5...10). (3.30)
Полученное значение ширины округляем до нормального линейного размера.
Остальные необходимые геометрические параметры зубчатых колес определяются по таблице приложения 2.
Определим окружную скорость зубчатых колес по формуле, м/с:
. (3.31)
По окружной скорости колес с учетом рекомендации таблицы 3.4 назначают степень точности зубчатых колес.
Таблица 3.4
Дата добавления: 2019-09-13; просмотров: 410; Мы поможем в написании вашей работы! |
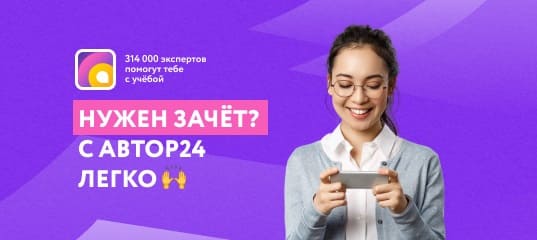
Мы поможем в написании ваших работ!