Выбор и обоснование измерительных средств
При проектировании технологического процесса механической обработки заготовки для межоперационного и окончательного контроля обрабатываемых поверхностей необходимо использовать стандартный измерительный инструмент, учитывая тип производства, но вместе с тем, когда целесообразно, следует применять специальный контрольно-измерительный инструмент или контрольно-измерительные приспособления.
Метод контроля должен способствовать повышение производительности труда контролёра и станочника, создавать условия для улучшения качества выпускаемой продукции и снижение её себестоимости. В единичном и серийном производстве обычно применяется универсальный измерительный инструмент (штангенциркуль, штангенглубиномер, микрометр, угломер, индикатор и т.д).
В массовом и крупносерийном производстве рекомендуется применять предельные калибры (скобы, пробки, шаблоны и т.д) и методы активного контроля.
В пояснительной записке необходимо дать объяснения применяемого метода контроля краткую техническую характеристику измерительного инструмента или контрольного приспособления на данную технологическую операцию.
В операционную карту технического контроля и в техническую карту механической обработки необходимо записывать условные обозначения измерительного инструмента в соответствии с присвоенным ему стандартным обозначением, например:
|
|
– условное обозначение скобы для контроля длины с полем допуска по Н6:
скоба 8102-0030Н6 ГОСТ 18355-73.
– приёмной скобы П-ПР: скоба 8102-0030Н6-П-ПР ГОСТ 18355-73.
Повышение качества продукции машиностроения во многом зависит от правильной организации технического контроля и применения прогрессивных методов контроля.
В зависимости от контролируемых изделий контроль может быть сплошным или выборочным. Более рациональным методом контроля в массовом производстве является выборочный контроль.
Для контроля промежуточных и окончательных размеров изделий используется как стандартный, так и специальный измерительный инструмент или специальные контрольные приспособления. Для конструирования измерительного инструмента в выпускных квалификационных работах могут быть предельные специальные калибры для цилиндрических, конических, резьбовых, шлицевых поверхностей. Для процесса контроля изделий могут быть спроектированы простые контрольные приспособления.
При проектировании контрольных предельных калибров производят расчёт исполнительных размеров и строят схему взаимного расположения полей допусков измеряемого изделия.
Рабочий чертёж измерительного инструмента должен соответствовать требованиям системы ЕСКД, а также должен иметь технические требования на изготовление.
|
|
Установление режимов обработки аналитическим методом
Чтобы добиться оптимальных норм времени на операции, необходимо в полной мере использовать режущие свойства инструмента и производственные возможности технологического оборудования.
При выборе режимов обработки необходимо придерживаться определённого порядка, т.е. при назначении и расчёте режима обработки указывают тип и размеры режущего инструмента, материал его режущей части, материал и состояние заготовки, тип оборудования и его состояние.
При расчёте режимов резания сначала устанавливают глубину резания в миллиметрах. Глубину резания назначат по возможности наибольшую, в зависимости от требуемой степени точности и шероховатости обрабатываемой поверхности и технических требований на изготовление детали. После установления глубины резания устанавливается подача станка. Подачу назначают максимально возможную, с учётом погрешности и жёсткости технологической системы, мощности привода станка, степени точности и качества обрабатываемой поверхности, по нормативным таблицам и согласовывают с паспортными данными станка. От подачи во многом зависит качество обработки и производительность труда. Для черновых технологических операций назначают максимально допустимую подачу.
|
|
После установления глубины резания и подачи определяют скорость резания по эмпирическим формулам с учётом жёсткости технологической системы.
Аналитический расчёт режимов резания производится с учётом необходимых поправочных коэффициентов на какую-нибудь обрабатываемую поверхность, указанную руководителем проекта.
В процессе определения режимов резания необходимо определить частоту вращения шпинделя станка, подачу или число двойных ходов скорректировать по паспорту станка. В справочной литературе и каталогах на металлорежущие станки обычно указывается минимальная nmin и максимальная nmax частота вращения шпинделя станка, двойных ходов (nmin дв.ход, nmax дв.ход) и подача(Smax, S min), поэтому необходимо производить расчёт промежуточных указанных значений.
Методика расчётов режимов резания при много инструментальных работах на токарных многошпиндельных и многорезцовых автоматах и полуавтоматах, сверлильных, фрезерных и других металлорежущих станках имеет ряд отличий от расчётов одно инструментальной обработки.
|
|
Рекомендуется использовать методику расчётов режимов резания при много инструментальных работах. Назначение режимов резания при много инструментальной обработке ведут по лимитирующему (наиболее загруженному инструменту).
При расчёте режимов резания на все виды работ следует установить исходные данные, необходимые для расчёта. К исходным данным можно отнести требования технологического процесса.
На изготовление детали, схемы обработки (наладки), технологической оснастки и станочного оборудования.
Основными особенностями расчётов режимов резания при много инструментальных наладках является согласование работы отдельных позиций, шпинделей, суппортов, а также отдельных инструментов между собой. При точении на одно-шпиндельных многорезцовых станках является общая для всех инструментов одного суппорта подача на оборот и общая частота вращения детали; при работе на многошпиндельных станках – время обработки, а при обработке многошпиндельными сверлильными головками – единая минутная подача.
Дата добавления: 2019-07-15; просмотров: 423; Мы поможем в написании вашей работы! |
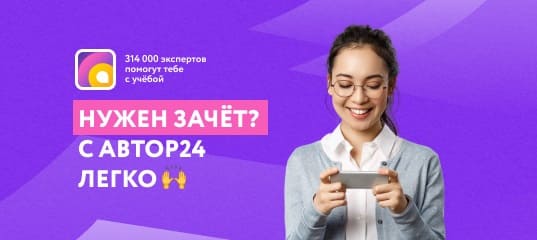
Мы поможем в написании ваших работ!