Определение режимов резания статическим методом
При определении режимов резания статическим (табличным) методом пользуют нормативные таблицы в зависимости от выбранного типа производства и установленного вида обработки заготовки. Табличный метод определения режимов резания табличным методом широко применяют в производственных условиях, т.к этот метод даёт возможность ускорить разработку технологического процесса и сократить сроки подготовки к запуску изготовления данного изделия.
Определение режимов резания статистическим методом ведут следующим образом:
1.Устанавливают глубину резания на обрабатываемую поверхность. При черновой обработке следует назначать наибольшую глубину резания, равную всему межоперационному припуску на обработку, если это позволяют жёсткость крепления заготовки режущего инструмента, а также жёсткости станка и мощности выбранного станка. При чистовой обработке глубину резания следует назначать исходя из степени точности и качества обрабатываемой поверхности в пределах 0,5…2,0 мм на диаметр при шероховатости поверхности Ra = 4 мкм и Ra = 2,5…1,25 мкм в пределах 0,1…0,4 мм.
Глубина резания при сверлении составляет t = 0,5D, при рассверливании, зенкеровании, развёртывании и растачивании t = 0,5(D-d),
где d и D – диаметры до обработки и после её.
2. Устанавливают подачи станка исходя из прочности державки пластинки из твёрдого сплава, жёсткости станка и характера установки заготовки. При чистовой обработке поверхности детали величина подачи зависит от технологических факторов (точности и качества обработки поверхности), Для резцов с пластинками из твёрдого сплава выбранную подачу необходимо согласовать по прочности пластинки по табличным нормативам.
|
|
Вспомогательное время Тв состоит из времени на установку и снятие детали; времени, связанного с переходом (установки инструмента по лимбу, разметке; предварительного промера; взятия пробной стружки и др); времени, связанного с переходом на приёмы не вошедшие в комплексы (изменения частоты вращения шпинделя станка, изменения подачи, поворота резцовой головки др); вспомогательного времени на контрольные измерения, которые устанавливают по нормативным таблицам в зависимости от точности измерения; размеров измерительных поверхностей с учётом коэффициента периодичности.
Вспомогательное время на технологическую операцию:
Тв=(Туст+ԐТпер+ ԐТпер.к+ ԐТизм).Кtв , | (3.6) |
где Туст – вспомогательное время на установку и снятие детали, мин; |
Тпер – вспомогательное время, связанное с переходом, мин;
Тпер.к– вспомогательное время, связанное с переходом на приёмы, не вошедшие в комплексы, мин;
|
|
Тизм– вспомогательное время на контрольные измерения, мин;
Кtв– поправочный коэффициент на вспомогательное время в зависимости от размера партии обрабатываемых изделий (по таблицам).
Время на техническое обслуживание рабочего места, затрачиваемое на установку, снятие и замену затупившихся режущих инструментов, на заправку шлифовальных кругов, смазывание и подналадку станка, уборку стружки в процессе работы и т.д.
Тт.о=(То+Тв).(ат.о /100), | (3.7) |
где ат.о- время на техническое обслуживание рабочего места в % к оперативному времени, которое выбирается по нормативным таблицам в зависимости от типа производства.
Время на отдыхи физические надобности | |
Топ= (То+Тв) . (ао.п /100), | (3.8) |
где ао.п- время на отдых физические потребности (в %) к оперативному времени, которое выбирают по нормативным таблицам.
В серийном и единичном производстве за техническую норму времени принимается штучно-калькуляционное время
Тш.к=Тш+(Тп.з /nД), | (3.9) |
|
|
где Тп.з – подготовительно- заключительное время, затрачиваемое на подготовку и наладку станка для обработки данной партии деталей, получение необходимой технологической оснастки, документации, а также на сдачу обработанных деталей, документации и оснастки;
nД – число обрабатываемых деталей в партии.
При фрезеровании различают подачу на один зуб фрезы Sz и подачу на один оборот фрезы Sо, мм/об; Sо= Sz·Z и подачу за одну минуту ( минутная подача), которую определяют по формуле
Sм= Sz· Z· nД, | (3.10) |
где Z- число зубьев фрезы.
Минутная подача корректируется по паспортным данным станка и далее определяется действительная подача на зуб.
При шлифовании различают две подачи – поперечную (глубина резания)
и продольную. Продольная подача задаётся в долях ширины круга SД на один оборот заготовки:
Sш= SД·Вкр , | (3.11) |
где Вкр – ширина шлифовального круга, мм.
Доля ширины шлифовального круга для черновой обработки SД=0,3…0,5 при диаметре заготовки до 20 мм; при Дзаг=20мм SД=0,7…0,85; для чистовой обработки SД=0,2…0,4
Продольная подача на шлифование назначается после выбора скорости вращения заготовки. Выбранные подачи по таблицам необходимо согласовывать с паспортными данными станочного оборудования.
|
|
Определяют скорость резания. Скорость резания устанавливается по табличным нормативам для определённых условий работы, и если конкретные условия отличаются от данных таблицы, тогда скорость резания, взятая из таблицы, умножается на поправочные коэффициенты.
3. После установления скорости резания по табличным нормативам определяют частоту вращения шпинделя станка и уточняют её по паспорту станка. Обычно принимают ближайшее меньшее значение станка, однако допускается принимать ближайшее большее число частоты вращения шпинделя станка, если оно превышает не более, чем на 10 % по паспорту станка. После установления частоты вращения шпинделя по паспорту станка определяют действительную скорость резания по формуле
VД= (n · Дnст) /60·1000
4. Проверяют режимы резания по мощности станка. Потребная мощность для резания, взятая из нормировочных таблиц, не должна превышать фактической мощности электродвигателя станка. При недостаточной мощности привода станка рекомендуется уменьшать скорость резания, а не подачу или глубину резания, т.к. одинаковое изменение указанных параметров, обеспечит больше повышение стойкости режущего инструмента.
5. Определяют технические нормативы времени на технологический переход или операцию на основе расчёта режимов резания и возможностей режущего инструмента, технологической оснастки и станочного оборудования.
Дата добавления: 2019-07-15; просмотров: 637; Мы поможем в написании вашей работы! |
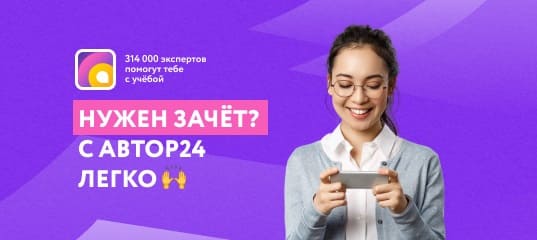
Мы поможем в написании ваших работ!