Режимы работы ГД при плавании во льдах и узкостях. Рекомендуемая характеристика работы ГД в этих условиях судна
Вопрос 1
Подготовка дизельной установки к действию и пуск дизеля
1.1. Подготовка дизельной установки к действию должна обеспечить приведение дизелей, обслуживающих механизмов, устройств, систем и трубопроводов в состояние, гарантирующее их надежный пуск и последующую работу.
1.2. Подготовка дизеля к работе после разборки или ремонта должна производиться под непосредственным наблюдением механика, в заведовании которого находится дизель. При этом необходимо убедиться в том, что:
.1. все разбиравшиеся соединения собраны и надежно закреплены, обратив особое внимание на стопорениекрепежных элементов;
.2. выполнены необходимые регулировочные работы. Особое внимание должно быть обращено на установку нулевой подачи топливных насосов высокого давления;
.3. все штатные контрольно-измерительные приборы установлены на место, соединены с контролируемой средой и не имеют повреждений;
.4. при прокачке маслом при открытых картерных щитах смазка поступает ко всем подшипникам и другим точкам смазки;
.5. защитные крышки, щиты и кожухи установлены на место и надежно закреплены;
.6. трубопроводы топливной, масляной, водяной и воздушной систем, а также рабочие полости дизеля, топливных и масляных фильтров, теплообменных аппаратов и вспомогательные механизмов не имеют пропусков рабочих сред. Особое внимание должно быть обращено на отсутствие протечки охлаждающей воды через уплотнения цилиндровых втулок, а также на возможность попадания топлива, масла и воды в рабочие цилиндры или в продувочный (всасывающий) и выпускной ресиверы дизеля;
|
|
.7. выполнена проверка форсунок дизеля на плотность и качество распыла топлива.
После перечисленных выще проверок должны быть выполнены операции, предусмотренные для подготовки дизельной установки к действию после непродолжительной стоянки (см. пп 1.3-1.9.11).
1.3. Подготовка дизельной установки к действию после непродолжительной стоянки, во время которой не выполнялись работы, связанные с разборкой, должна производиться вахтенным механиком и включать в себя операции, предусмотренные пп. 1.4.1-1.9.11. При экстренном пуске время подготовки можно сократить только за счет прогрева.
Вопрос 2(4)
Подготовка масляной системы. При этом необходимо:
.1. Проверить уровень масла в сточных цистернах или в картерах дизеля и редуктора, в маслосборниках и гравитационных цистернах турбокомпрессоров наддува, в масляных сервомоторах, в лубрикаторах, в регуляторе частоты вращения, в корпусе упорного подшипника, в цистерне смазки распределительного вала. При необходимости пополнить их маслом.
|
|
.2. Убедиться в исправности устройств автоматического пополнения и поддержания уровня масла в цистернах, лубрикаторах.
.3. Перед проворачиванием дизеля подать масло в рабочие цилиндры и к другим местам лубрикаторной смазки, а также ко всем точкам ручной смазки.
.4. Подготовить к работе масляные фильтры и маслоохладители, установить клапаны на трубопроводах в рабочее положение. Пуск дизеля и его работа с неисправными масляными фильтрами запрещается. Дистанционно управляемые клапаны должны быть опробованы в действии.
.5. При температуре масла ниже рекомендованной инструкцией по эксплуатации его необходимо подогреть. При отсутствии специальных нагревательных устройств масло прогревают путем прокачки его через систему во время прогрева дизеля (см. п. 1.5.4). Температура масла при прогреве не должна превышать +45°С.
.6. Подготовить к работе и пустить автономные масляные насосы дизеля, редуктора, турбокомпрессоров или прокачать дизель ручным насосом. Проверить действие средств автоматизированного (дистанционного) управления основными и резервными масляными насосами, выпустить из системы воздух. Убедиться в наличии показаний всех контрольно-измерительных приборов системы, а также в наличии потока в смотровых стеклах. Прокачивание маслом производить в течение всего времени подготовки дизеля (при ручной прокачке - перед проворачиванием и непосредственно перед пуском).
|
|
1.5. Подготовка системы водяного охлаждения. При подготовке системы необходимо:
.1. Подготовить к работе охладители и подогреватели воды, установить клапаны и краны на трубопроводах в рабочее положение, опробовать в действии дистанционно управляемые клапаны.
.2. Проверить уровень воды в расширительной цистерне контура пресной воды и в цистернах автономных систем охлаждения поршней и форсунок. При необходимости пополнить системы.
.3. Подготовить к работе и пустить автономные или резервные насосы пресной воды охлаждения цилиндров, поршней, форсунок. Проверить действие средств автоматизированного (дистанционного) управления основными и резервными насосами. Довести давление воды до рабочего, выпустить из системы воздух. Прокачку дизеля пресной водой производить в течение всего времени подготовки дизеля.
.4. Прогреть охлаждающую пресную воду имеющимися средствами до температуры около 45°С на входе. Темп прогревания должен быть по возможности медленным. Для мало-оборотных дизелей скорость прогрева не должна превышать 10°С в час, если в инструкции по эксплуатации нет других указаний.
|
|
5. Для проверки системы забортной воды пустить главные насосы забортной воды, проверить систему, включая работу регуляторов температуры воды и масла. Остановить насосы и вновь запустить их непосредственно перед пуском дизеля. Избегать длительной прокачки забортной водой масло- и водоохладителей.
1.6. Подготовка топливной системы. При подготовке системы необходимо:
.1. Спустить отстой из расходных топливных цистерн, проверить уровень топлива и при необходимости пополнить цистерны.
.2. Подготовить к работе топливные фильтры, регулятор вязкости, подогреватели топлива, расходомеры.
.3. Установить в рабочее положение клапаны на топливном трубопроводе, опробовать в действии дистанционно управляемые клапаны. Подготовить к работе и пустить автономные насосы топливоподкачивающий и охлаждения форсунок. После подъема давления до рабочего убедиться в отсутствии воздуха в системе. Проверить действие средств автоматизированного (дистанционного) управления основными и резервными насосами. Если во время стоянки проводились работы, связанные с разборкой и опорожнением топливной системы, заменой или разборкой топливных насосов высокого давления, форсунок или форсуночных труб, удалить воздух из системы высокого давления путем прокачки насосов при открытых деаэрационных клапанах форсунок либо другим способом.
.4. Если дизель конструктивно приспособлен для работы на высоковязком топливе, включая пуск и маневрирование, и был остановлен на высоковязком топливе на длительное время, обеспечить постепенный прогрев топливной системы (цистерн, трубопроводов, топливных насосов высокого давления, форсунок) путем включения обогревающих устройств и непрерывной циркуляции подогреваемого топлива. Перед пробными пусками дизеля температура топлива должна быть доведена до значения, обеспечивающего необходимую для качественного распыливания вязкость (9-15 сСт). Темп прогрева топлива не должен превышать 2° С в минуту, а время циркуляции топлива в системе должно быть не менее одного часа, если в инструкции по эксплуатации не содержатся другие указания.
.5. При пуске дизеля на маловязком топливе заблаговременно подготовиться к переводу его на высоковязкое топливо, включив обогрев расходных и отстойных цистерн. Максимальная температура топлива в указанных цистернах должна быть не менее чем на 10°С ниже температуры вспышки паров топлива в закрытом тигле. На морских судах не допускается применение топлива с температурой вспышки ниже 60°С, если не приняты специальные конструктивные противопожарные меры, согласованные с Регистром.
.6. При пополнении расходных цистерн высковязкое топливо перед сепаратором должно подогреваться до температуры не выше 90°С. Подогрев топлива до более высокой температуры допускается только при наличии специального регулятора для точного поддержания температуры.
1.7. Подготовка систем пуска, продувки, наддува, выпуска. При подготовке систем необходимо:
.1. Проверить давление воздуха в пусковых баллонах, продуть из баллонов конденсат, масло. Подготовить к работе и пустить компрессор, убедиться в его нормальной работе. Проверить действие средств автоматизированного (дистанционного) управления компрессорами. Пополнить баллоны воздухом до номинального давления. Запорные клапаны на пути от баллонов к стопорному клапану дизеля открывать плавно. Продуть пусковой трубопровод при закрытом стопорном клапане дизеля.
.2. Спустить воду, масло, топливо из ресивера продувочного воздуха, впускного и выпускного коллекторов, подпоршневых полостей, воздушных полостей воздухоохладителей, тазовых и воздушных полостей турбокомпрессоров наддува.
.3. Убедиться в том, что все запорные устройства газоотвода дизеля открыты.
1.8. При подготовке к работе водопровода необходимо:
.1. Убедиться в отсутствии посторонних предметов на валопроводе, а также в том, что тормоз валопровода отжат.
2. Подготовить к работе дейдвудный подшипник, обеспечив его смазку и охлаждение маслом или водой. При дейдвудных подшипниках с масляной системой смазки н охлаждения необходимо проверить уровень масла в напорном бачке (при необходимости заполнить его до рекомендуемого уровня), а также отсутствие протечек масла через уплотнительные сальники (манжеты).
.3. Проверить уровень масла в опорных и упорных подшипниках, проверить исправность и подготовить к работе смазывающие устройства подшипников. Проверить и подготовить к работе систему охлаждения подшипников.
.4. После пуска насоса смазки редуктора проверить по приборам поступление масла к местам смазки.
.5. Проверить действие разобщительных муфт валопровода, для чего произвести несколько включений и выключении муфт с пульта управления. Убедиться в исправности действия сигнализации включения и выключения муфт. Разобщительные муфты оставить в выключенном положении.
.6. В установках с винтами регулируемого шага ввести в действие систему изменения шага винта и выполнить проверки, предусмотренные в п. 4.6.5 части I Правил.
Вопрос 3
Проворачивание и пробные пуски
1.9.1. При подготовке дизеля к работе необходимо провернуть его валоповоротным устройством на 2-3 оборота вала, а затем сжатым воздухом при открытых индикаторных кранах. Если дизель главный, то необходимо также произвести пробные пуски на топливе на передний и задний ход. При проворачивании дизеля валоповоротным устройством или воздухом дизель и редуктор необходимо прокачивать смазочным маслом, а при пробных пусках также и охлаждающей водой.
1.9.2. Проворачивание и пробные пуски необходимо производить:
в установках, не имеющих разобщительных муфт между дизелем и гребным винтом, - только с разрешения вахтенного помощника капитана;
в установках, работающих на гребной винт через разобщительную муфту - при отключенной муфте.
Проворачивание и пробные пуски главных дизель-генераторов производятся с ведома лица, ответственного за эксплуатацию электрооборудования.
1.9.3. Перед соединением валоповоротного устройства с дизелем необходимо убедиться в том, что:
.1. рычаг (штурвал) поста управления дизеля находится в положении "СТОП";
.2. клапаны на пусковых баллонах и трубопроводе пускового воздуха закрыты;
.3. на постах управления вывешены таблички с надписью "Валоповоротное устройство соединено";
.4. индикаторные (декомпрессионные) краны (клапаны) открыты.
1.9.4. При проворачивании дизеля валоповоротным устройством следует тщательно прослушивать дизель, редуктор, гидромуфты. Убедиться в отсутствии в цилиндрах воды, масла, топлива. Во время проворачивания необходимо следить по показаниям амперметра за нагрузкой электродвигателя валоповоротного устройства. При превышении предельного значения силы тока либо при резком ее колебании немедленно остановить Валоповоротное устройство и устранить неисправность дизеля либо валопровода. Категорически запрещается проворачивание до выявления и устранения неисправностей.
1.9.5 Проворачивание дизеля сжатым воздухом необходимо производить при открытых индикаторных кранах (декомпрессионных клапанах), спускных кранах ресивера продувочного воздуха и выпускного коллектора. Убедиться в том, что дизель нормально набирает обороты, ротор турбокомпрессора вращается свободно и равномерно и при прослушивании нет ненормальных шумов.
1.9.6. Перед пробными пусками установки, работающей на винт регулируемого шага (ВРШ), необходимо лопасти винта установить в положение нулевого шага.
1.9.7. Пробные пуски дизеля на топливе следует производить при закрытых индикаторных и спускных кранах. При этом убедиться в исправности систем пуска и реверса, работе всех цилиндров, отсутствии посторонних шумов и стуков, поступлении масла к подшипникам турбокомпрессоров.
1.9.8. В установках с дистанционным управлением главными дизелями необходимо пробные пуски произвести со всех постов управления (из ЦПУ, с мостика), убедиться в правильности действия системы дистанционного управления.
1.9.9. Если по условиям стоянки судна нельзя произвести пробные пуски главного дизеля на топливе, то такой дизель допускается к работе, но при этом капитан обязан принять все необходимые меры предосторожности на случай невозможности пуска или реверсирования дизеля, а в машинном журнале должна быть сделана специальная запись.
1.9.10. После окончания подготовки дизеля к пуску следует поддерживать давление и температуру воды, смазочного и охлаждающего масла, давление пускового воздуха в баллонах в пределах, рекомендуемых инструкцией по эксплуатации.
1.9.11. Если подготовленный двигатель не вводится в работу длительное время и должен находиться в состоянии постоянной готовности, необходимо каждый час по согласованию с вахтенным помощником капитана проворачивать двигатель валоповоротным устройством с открытыми индикаторными кранами.
Пуск дизеля в ход.
1.10.1. Операции по пуску дизеля должны выполняться в последовательности, предусмотренной заводской инструкцией по эксплуатации. Во всех случаях, где это технически возможнот пуск дизеля должен осуществляться без нагрузки.
1.10.2. При вводе в действие главных дизелей за 5-20 минут до дачи хода (в зависимости от типа установки) с ходового мостика в машинное отделение должно быть передано соответствующее предупреждение. За это время должны быть выполнены окончательные операции по подготовке установки к действию: запущены дизели, работающие на винт через разобщительные устройства, выполнены необходимые переключения в системах. О готовности установки к даче хода вахтенный механик докладывает на мостик установленным на судне способом.
1.10.3. После запуска следует избегать длительной работы дизеля на холостом ходу и самой малой нагрузке, так как это приводит к повышенным отложениям загрязнений в цилиндрах и проточных частях дизеля.
1.10.4. После пуска дизеля необходимо проверить показания всех контрольно-измерительных приборов, обратив особое внимание на давление смазочного масла, охлаждающих сред, топлива. Убедиться в отсутствии ненормальных шумов, стуков и вибрации. Проверить работу лубрикаторов смазки цилиндров.
1.10.5. При наличии системы автоматизированного запуска дизель-генераторов необходимо периодически контролировать состояние дизеля, находящегося в горячем резерве. При автоматическом запуске дизеля следует установить причину запуска и проверить значения контролируемых параметров имеющимися средствами. После исчезновения надобности в работе резервного дизель-генератора его следует остановить и вновь ввести в горячий резерв.
1.10.6. Необходимо обеспечивать постоянную готовность к запуску дизельных приводов аварийных агрегатов и спасательных средств. Проверка готовности аварийных дизель-генераторов, двигателей спасательных и дежурных шлюпок должна осуществляться еженедельно. Проверка работоспособности и готовности к запуску двигателей аварийных пожарных насосов и других аварийных агрегатов должна производиться механиком по заведованию не реже одного раза в месяц. Запись о проверке аварийных агрегатов заносится в машинный журнал.
ВОПРОС 6
Системы сжатого воздуха. Условия выбора емкости, воздухохранителей. Определяющие факторы при расчете запаса пускового воздуха, выбора производительности и мощности компрессоров. Стадии обработки воздуха после сжатия в компрессоре и до поступления в баллоны.
Такие системы предназначены для получения сжатого воздуха, который в судовой практике используется для различных .целей. Например, для пуска и реверсирования ДВС, подачи сигналов, продувки кингстонов, привода пневматических инструментов, создание напора в пневмоцистернах и других нужд.
Исходя из своего назначения система сжатого воздуха включает ряд подсистем, к которым относятся системы пуска ГД и ВД, хозяйственных нужд, пневмоавтоматики и ДАУ, тифонов, продувки кингстонов, пневматического инструмента, и других общесудовых и специальных нужд.
В качестве примера на рис. 2. 1 приведена простейшая принципиальная схема такой системы.
Обычно в состав системы сжатого воздуха ДЭУ входят 2-3 главных автоматизированных компрессора, один подкачивающий компрессор, два баллона пускового воздуха ГД, 1-2 баллона ВД, водомаслоотделители, арматура, КИП, трубопроводы. '
Принципиальная схема системы сжатого воздуха ДЭУ
1 - главный компрессор, 2 -- водомаслоохладитель; 3 баллоны (воздухохранители) ГД; 4 ~ ГД; 5 -- подкачивающий автоматизированный компрессор;6 - редукционный клапан;7 - первичный компрессор; 8 -- баллон ДГ; 9 - ДГ).
ВОЗДУХОХРАНИТЕЛИ. Они представляют собой емкости предназначенные для хранения запасов воздуха. В целях уменьшения габаритов давление сжатого воздуха в них составляет от 30 МПа до 60 МПа. При использовании сжатого воздуха в случае необходимости его давление снижают с помощью редукционных клапанов до требуемого по условиям работы источника потребления. В комплекте средукционными устанавливаются и предохранительные клапаны, как правило, отрегулированные на давление, превышающее рабочее не более чем на 10%, и манометры, показывающие давление до и после редукционных клапанов. Емкость всех воздухохранителей определяется необходимым запасом воз духа. Согласно Правилам Регистра запас пускового воздуха :воздухохранителях должен быть достаточным без подкачки воздуха для12-ти последовательных пусков и реверсов всех ГД (реверсивных), для 4-х последовательных пусков всех ГД или для 3-х последовательных пусков всех ВД. Необходимое количество воздухохранителей для пуска ГД должно быть не менее двух в каждом МО. По опытным данным, удельный расход пускового воздуха составляет в среднем «ζ = (6 — 9) л на 1 л суммарноного рабочего объема цилиндров двигателя.Исходя из этого запас пускового воздуха при t =15°С и р=1ата будет определяться по формуле:
где i - Число цилиндров; Yh - рабочий объем цилиндра; m - число возможных пусков и реверсов.
Для определения емкости воздухохранителей запаса пускового воздуха может быть использована формула:
где Рн, Рк - начальное и конечное давление воздуха в воздухохранителях (Рк = 0,7-0,8 МПа).
Емкость баллонов для тифонов принимают от 2 м3 для малых судов до 10 м3 для крупнотоннажных.
Воздух из любого баллона ГД можно использовать для пуска ВД, питания через отдельные редукционные клапаны потребителей' воздуха низкого давления и тифона. В этих случаях для обеспечения необходимого запаса воздуха, предназначенного для двигателей, баллоны должны иметь на магистрали разобщительные клапаны, исключающие возможность расхода воздуха из двух или большего количества пусковых баллонов.
Практика показывает, что даже при частых маневрах обеспечивается поддержание или рост давления в пусковом баллоне при работе одного воздушного компрессора. Во всех случаях второй пусковой баллон должен иметь полное рабочее давление и быть отсеченным от пусковой магистрали на случай выхода из строя воздушного компрессора или превышения расхода пускового воздуха над производительностью компрессоров при большом, количестве пусков. Наибольший расход воздуха на один пуск (реверс) наблюдается в диапазоне давления 2-3 МПа (3).
Для тифона устанавливаются специальные баллоны, которые могут пополняться воздухом из пусковых баллонов ГД через редукционные и разобщительные клапаны. Для надежного обеспечения возможности подачи сигналов на этих баллонах устанавливаются автоматические сигнализаторы падения давления ниже допускаемого уровня, и из этих баллонов не отбирают воздух на хознужды. Исключение допускается, если в системе предусмотрено реле, автоматически включающее электродвигатель компрессора, когда половина используемого для тифона перепада давления в воздухохранителе израсходована.
Баллоны сжатого воздуха как сосуды, находящиеся под давлением, подвергаются гидравлическим испытаниям на прочность до сдачи их в эксплуатацию.
КОМПРЕССОРЫ. Они предназначены для осуществления сжатия воздуха и заполнения им воздухохранителей. В конструктивном отношении в качестве главных обычно используют двухступенчатые электроприводные, вертикального типа компрессоры с числом цилиндров от одного до четырех. Частота вращения вала не превышает 1000 об/мин. Ход поршня измеряется в пределах 125 - 180 мм, диаметр поршней не более 270 мм у цилиндров низкого давления. Согласно Правилам Регистра на судах неограниченного района плавания должен быть установлен первичный дизель-компрессор с ручным пуском. В соответствии с этими Правилами производительность компрессоров с механическим приводом (кроме первичного) должна обеспечить в течение 1 часа пополнение сжатым воздухом всех пусковых баллонов ГД с повышением давления от начального (5 кг/см2) до рабочего давления. Исходя из этого часовая производительность компрессоров будет определяться как
где z — число воздухохранителей емкостью каждый, равный
Для определения мощности, необходимой для привода компрессора, может быть использована формула: |
где часовая производительность компрессора; кг/ч;
- удельный вес воздуха при 15° С и 1 ата;
= О,9 - механический КПД компрессора. :
Воздух после сжатия в компрессоре до поступления в баллоны очищается в сепараторе масла и воды и охлаждается в охладителе до температуры не выше 40° С.
Давление сжатого воздуха в зависимости от его назначения может изменяться в широких пределах. Например, для пуска МОД и СОД оно составляет 2,0 МПа, на судах с дизелями фирмы "Бурмейстер и Вайн" - 2,5 МПа, на остальных 3 МПа (3)., Сжатый воздух общесудового использования составляет 0,6 — 1,0 МПа Для работы пневмоинструмента используется воздух давлением 0,8 -- 1,0 МПа, подачи сигналов -- (0,6 -- 0,8) МПа, продувания кингстонов - 3 МПа.
Учитывая, что при частых пусках главных компрессоров в
процессе их эксплуатации происходит повышенный износ ЦПГ и частые провалы напряжения вследствие пуска электродвигателей большой мощности, в некоторых схемах используют подкачивающий компрессор. В то же время на судах с ГД малой мощности применение таких компрессоров нецелесообразно
ВОПРОС 7
Системы отвода газа. Требования, предъявляемые к газовыпускному трубопроводу. Факторы, определяющие его проходное сечение. Сущность работы эжектирующего устройства. Типы глушителей и искрогасителей и целесообразность их использования.
Такие системы предназначены для удаления в атмосферу отработавших продуктов сгорания топлива из ДВС, ГТ и уходящих газов из ПГ. Их основными элементами являются газоходы, дымоходы, искрогасители, шумоглушители.
ГАЗОХОДЫ И ДЫМОХОДЫ. В процессе эксплуатации СЭУ выпускные газы имеют высокую температуру. Например, в СЭУ с 4-х тактными ДВС температура поступающих газов в выпускной коллектор достигает 400 - 500° С, в ГТУ без регенерации тепла - (400 - 450° С), а в дымоходах ПГ - (140 - 200° С). В результате чего в МО могут передаваться значительные количества, тепла. Кроме того, высокие температуры поверхностей стенок газоходов могут быть причиной ожогов обслуживающего! персонала и. возникновения пожара. Во избежание этого поверхности газоходов изолируются. При этом предельная температура наружной поверхности изоляции не должна превышать 50° С, а в тех местах, где возможно повреждение изоляции предусматриваются защитные кожухи. При работе газоходов в условиях высоких температур возможно увеличение их линейных размеров. Поэтому на участках газохода, где нет самокомпенсации температурных деформаций должны быть включены компенсаторы в противном случае может произойти, например, деформация корпуса двигателя, вызванная воздействием сил со стороны газохода, либо остаточных деформаций газохода, либо обрыв сопряженных с ним деталей двигателя. Обычно газоходы выполняются из круглых стальных труб стандартных размеров. Газонепроницаемость стыков достигается установкой между фланцами прокладок из паронита. Крепление газоотвода выполняется эластичным при помощи пружинных подвесок. Упругость и расположение пружин выбирается таким образом, чтобы масса трубопровода воспринималась пружинами и передавалась ими прочным опорам на корпусе судна, а не деталям двигателя или устройств на газоотводе.
Газовыпускной трубопровод, например, ДВС состоит из коллектора и газоотводного трубопровода. Согласно Правилам Регистра каждый двигатель должен иметь отдельный газоотвод.
При установке УК система газоотвода должна обеспечивать возможность подачи газа в УК и в обход ему. На газоотвод широко применяются сальниковые и линзовые компенсаторы отличающиеся высокой компенсирующей способностью и малыми габаритами. Сальниковые компенсаторы могут, компенсировав деформации только прямолинейных участков газоотвода, если силы направлены по оси компенсатора. В противном случае может произойти заклинивание стакана в корпусе компенсатора. Линзовые компенсаторы герметичны, эластичны, имеют сравнительно малые габариты и вес, а также способны воспринимать усилия, не совпадающие с осью компенсатора. Возможно применение резино-металических охлаждаемых вибро и звукоизолирующих компенсаторов. Площадь его проходного сечения определяется из уравнения сплошности в зависимости от расхода газов V и допустимой скорости их движения Сг
где — плотность газов.
Допустимая скорость движения газов, например, для 4-х такт-
ных ДВС составляет 40 - 45 м/сек, 2-х тактных 25 -- 30 м/сек.
Для определения секундного расхода газов можно использовать формулы:
для 4-х тактных ДВС
;
Рг для 2-х тактных ДВС
где а - коэффициент избытка воздуха при горении топлива в цилиндре двигателя; - коэффициент избытка продувочного
воздуха; - соответственно средняя температура и среднее давление отходящих газов, °К, кг/см2;
- удельный расход топлива, кг/л. с. ч.;
- эффективная мощность, л. с.
Площадь проходного сечения газовыпускного трубопровода ГТУ также определяется по уравнению сплошности, при этом значение допустимой скорости движения газов принимается равной 30 - 50 м/сек.
Дымоходы ПГ соединяются в один при помощи отводов,
имеющих обычно прямоугольные сечения. Дымоход изготавли-
вается сварным из листовой стали толщиной 3 - 4 мм. Для
осмотра и очистки дымохода на его стенках предусматриваются лазы. Площадь поперечного сечения дымоходов определяется также в зависимости от секундного объемного расхода газов Vсек и допустимой скорости Сг. При этом она может быть принята при естественной тяге 5-8 м/сек. Секундный расход дымовых газов может быть определен по формуле:
где - теоретически необходимое количество воздуха для сжигания 1 кг топлива, кг/кг;
— удельный вес газа, кг/м3.
Важное значение для дымоходов имеет высота дымовых труб. Недостаточная их высота может явиться причиной задымления палуб. Во избежание этого на дымовой трубе устанавливается эжектирующее устройство. Его принцип работы заключается в следующем. Вентилятор нагнетает воздух в приемную камеру, охватывающую дымовую трубу. Из приемной камеры воздух движется по кольцеобразному суживающемуся каналу вверх, выходит в атмосферу через узкий кольцевой зазор между трубой и "козырьком" со скоростью, в 5 - 6 раз большей скорости выходящих дымовых газов, и оказывает эжекционное действие на струю дымовых газов. В качестве примера на рис. 2.4 приведено эжектирующее устройство на дымовой трубе судна с ДЭУ.
Эффект эжекционного действия этого устройства заключается в выпрямлении и охлаждении потока газа над дымовой трубой, в результате чего значительно уменьшается задымление палубы.
ГЛУШИТЕЛИ И ИСКРОГАСИТЕЛИ. Глушители служат для снижения аэродинамического шума. Они устанавливаются на выпускном трубопроводе и по принципу действия разделяются на активные и реактивные.
В активных глушителях энергия звука поглощается "активным сопротивлением" и превращается в тепловую. В качестве таких сопротивлений
Эжектирующее устройство на дымовой трубе судна с ДЭУ
1 приёмная камера; 2 ~ труба; 3 ~ козырек).
могут использоваться сетки, перфорированные листы, пористые материалы, достаточно стойкие при температурах выпускных газов.
Реактивные глушители работают по принципу акустического фильтра, состоящего из расширительных или резонансных камер.
Активные сопротивления наиболее эффективно поглощают колебания высокой частоты, а реактивные колебания низкой частоты.
Роль глушителей высокочастотных колебании могут выполнять ГТ и УК, устанавливаемые в системе газоотвода ДВС. Поэтому целесообразно за котлом размещать реактивный глушитель для поглощения низкочастотных звуковых колебаний.
Применяемые в эксплуатационной практике искрогасители можно подразделить на две группы: "сухие" и "мокрые". В процессе работы первых раскаленные частицы несгоревшего топлива и масла выводятся из потока газа в сборник, где они охлаждаясь, гаснут. Во- вторых гашение раскаленных частиц может происходить по-разному: путем орошения выхлопных газов водой, в результате соприкосновения искр с постоянной поверхностью воды в корпусе искрогасителя, пропуском потока выхлопных газов через слой воды постоянного уровня.
Сравнительный анализ указанных типов искрогасителей показывает, что мокрые более эффективнее сухих, но они более дороги в эксплуатации, т. к. требуют непрерывной подачи воды в корпус искрогасителя, и менее долговечны вследствие усиленной коррозии. Возможно использование и комбинированных конструкций(глушитель-искрогаситель), позволяющих одновременно осуществлять процессы глушения шума и искрогашения. Такие функции могут выполнять утилизационные ПГ.
ВОПРОС 8
Масляные системы. Роль циркулирующего в системе масла, источники его загрязнения и последствия. Требования, предъявляемые к маслам. Выбор оборудования масляных систем и сорта масла. Определяющие факторы при расчете емкости сточно-цкркуляционных цистерн, запаса и цилиндрового масла. Основные марки моторных масел и их характеристики.
Эти системы в процессе эксплуатации СЭУ имеют различное функциональное назначение. Цирклирующее в них масло используется для смазки трущихся поверхностей, охлаждения части деталей двигателей, применяется как рабочая жидкость в гидромуфтах и сервомоторах, а также в качестве силовой и импульсной жидкости в системах автоматического регулирования.
Масла исходя из своего назначения делятся на антифрикционные, консервационные, гидравлические, уплотнительные, электроизоляционные и моющие. Например, функции циркуляционного масла в ДЭУ заключаются в смазке и охлаждении подшипников зубчатых колес и цепей привода. Источниками его загрязнений являются остаточные продукты сгорания, износа деталей;
пыль, вода и топливо, продукты окисления.
Масло должно поддерживать во взвешенном состоянии продукты окисления, сгорания и остальные твердые загрязняющие вещества, чтобы предотвратить образование отложений на стенках картера и других деталях дизеля. Оно должно хорошо счищаться с этих загрязнений в элементах масляной системы.
Наиболее распространенный источник загрязнения масла
вода(пресная, забортная). Ее проникновение возможно через не
плотности, в результате утечки через сальники телескопический труб, из системы охлаждения и в результате конденсации водяных паров. Вода в масле при образовании эмульсии представляем собой серьезную опасность, так как стойкая водомасляная эмульсия не разрушается при сепарировании. Присутствие воды в масле, способствует возникновению коррозии вследствие неблагоприятных условий для роста различного вида бактерий, дрожжей, плесени (3). Наиболее опасным является разбавление масла газойлем
или дизельным топливом, в результате чего снижается вязкость
масла. Это может привести к разрушению подшипников и даже к взрывам в картерах из-за повышения температуры подшипников вала и воспламенения масляных паров.
При использовании масла в качестве смазывающей и охлаждающей среды его количество определяется не из потребностей смазки поверхностей деталей, а из условия отвода им тепла, эквивалентного работе трения, (например, в дизелях до 8 - 12% теплей ты топлива отводится циркуляционным маслом). Исходя из этого количество масла во много раз больше необходимого только для смазки трущихся поверхностей. Масло, отводимое от мест смазки и охлаждения, должно быть приведено в первоначальное состояние, соответствующее первоначальным значениям температуры; вязкости и чистоты. Восстановление таких свойств требуется и в случаях применения его для охлаждения высоконагретых деталей (например, головок поршней ДВС) и в качестве рабочей жид< кости в гидромуфтах. Таким образом, МС должна обеспечивать подвод масла ко всем его потребителям, а также охлаждение | выполнение операции по очистке и перекачке масла. При этом особенно важным является обеспечение нормальной работы системы смазки и требуемого количества масла, в противном случае, например, прекращение подачи масла к нагруженным поверхностям трения даже на короткий срок или применение недоброкачественного масла может привести к авариям. В зависимости от способа создания напора масла у мест смазки используют два вида МС: гравитационные (давление масла 0,07 - 0,1 МПа), напорные (давление масла 0,3 - 0,4 МПа).
Отличие гравитационной от напорной состоит в том, что масляные насосы не подают масло непосредственно к местам смазки, перекачивают его из сточной цистерны в напорную и, таким образом, создают в ней аварийный запас, на случай отказа ГМН, достаточный для работы СЭУ в течение нескольких минут. Гравитационная МС имеет свои достоинства. В процессе ее работы давление масла, поступающего к двигателю, постоянно и не зависит от расхода масла в системе. Кроме того, в напорной цистерне происходит дополнительный отстой масла и выделение из него газов. Гравитационная система смазки может применяться в тех случаях, когда располагаемый напор достаточен для преодоления гидравлических сопротивлений в системе смазки при требуемом расходе масла? На больших морских судах напорная цистерна может быть поднята на 10 м и более над ГД, что во многих случаях обеспечивает циркуляцию масла через узлы трения.
Основными элементами МС являются насосы, фильтры, сепараторы, маслоохладители и цистерны.
ВЫБОР ХАРАКТЕРИСТИК ОБОРУДОВАНИЯ МС Основой такого выбора являются исходные данные. В их качестве используется количество тепла, отводимого маслом и количество масла, прокачиваемого в МО.
Емкость цистерн определяется исходя из часового расхода масла в системе и принятой кратности циркуляции (т). Под
кратностью циркуляции понимается число, показывающее сколько раз в течение часа масло, залитое в сточную цистерну, пройдет через МС. Эта величина выбирается в зависимости от типа, мощности и назначения СЭУ. При этом необходимо учитывать, что повышенная кратность циркуляции приводит к быстрому старению масла, так как при уменьшении продолжительности пребывания масла в сточной цистерне затрудняется выделение из масла воздуха, газов и отстоя влаги, что способствует образованию пены, эмульсин и старению.
Для ДЭУ малой мощности величина m составляет (40 – 60)1/ч, ДЭУ средней и большой мощности — (10 - 20) 1/ ч. В системах смазки гидро- зубчатых передач m = (7-15) 1/ч. Для турбинных СЭУ она равна (6-8) 1/ ч. Для определения емкости цистерн могут быть использованы следующие формулы: сточно-циркуляционная
где \\' - производительность ГМН, кг /ч; удельный в масла, кг/ м3 ;
- коэффициент, учитывающий заполнений объема цистерны деталями ее конструкции, свободный объем над уровнем масла в ней, увеличение объема при нагревании и вспенивании.
Запаса масла
где
- количество основного запаса, кг. Цилиндрового масла
где
-- соответственно удельный расход масла на ГД и ВД;
— эффективная мощность;
— время работы;
коэффициент, равный (1,4 - 1,5).
ВЫБОР СОРТА МАСЛА. При выборе марки масла для СЭ необходимо учитывать режим работы ГД, материал вкладышей подшипников, условия эксплуатации и качества применяемого топлива. Например, для ДЭУ, в частности смазки ГД, рекомендуется использовать два сорта масел: на смазку подшипников и смазку цилиндров.
Причем масло, применяемое на смазку подшипников
используется и для охлаждения поршней. Смазка цилиндров
и подшипников ВД (например, тронковых с числом оборотов до750 о6 /мин) обычно производится одним и тем же маслом. Масла для СОД и ТК выбирают в соответствии с инструкцией завода-изготовителя. Так, для ТК обычно рекомендуются стойкие против старения, преимущественно турбинные масла с вязкостью 30 – 76 мм2/с (или 4-10 "Е) при 50 "С в зависимости от частоты вращения ТК. Масла с повышенным содержанием различных присадок (например, среднещелочные масла) непригодны. Масла для СОД работающих на тяжелом топливе, должны соответствовать
следующим требованиям (3):
Вязкость при 50 "С, мм2 /с....60-100
Вязкость по стандарту SАЕ..30-40
Индекс вязкости (VI)......98
Температура, °Стекучести... 10
вспышки.....200
Содержание воды, % по объему........ 0,1
Содержание золы, % по массе.......... 0, 02
Коксуемость по Конрадсону, %...... 0, 5
Для смазки крпвошнпно-шатунного механизма, цилиндров, ТК, а также охлаждения поршней СОД лучше всего зарекомондо-вало себя масло типа 5АЕ40. Это масло имеет необходимые нейтрализующую и моющую способности.
Для МОД рекомендуется использовать некоторые масла вязкостью порядка 10 мм2/'с со щелочным числом 30 (5АЕ40) для циркуляционных систем и вязкостью 16 мм2/с со щелочным числом 40 - 50 (5АЕ40, 5АЕ50) для ЦПГ, а также турбинные масла для смазки подшипников ТК. Все моторные масла делятся на шесть групп: А, Б, В,Г,Д, Е, причем каждая группа включает масла, различающиеся вязкостью от 6 до 20 мм2/с при 100 °С (3).
ВОПРОС 9
Системы охлаждения. Виды охлаждаемых сред и их характерные особенности применительно к разным типам СЭУ. Факторы, учитываемые при выборе конкретного теплоносителя. Условия при определении производительности насоса. Факторы, определяющие целесообразность использования самопроточной циркуляции в ГТУ. Отличительные особенности систем охлаждения ДЭУ. Особенности системы охлаждения ГТУ.
В зависимости от типа СЭУ эти системы по своему назначению имеют отличительные особенности.
В ПТУ они используются для охлаждения конденсаторов турбин, МОХ, ВОХ и других ТА. В ДЭУ - охлаждения втулок,вкладыш подшипников, условия эксплуатации и качества применяемого поршней, рабочих цилиндров ГД и ВД, форсунок, корпусов выпускных клапанов, выпускных коллекторов, МОХ, охладителей пресной, циркуляционной воды, ВОХ компрессоров пускового воздуха и наддувочных агрегатов, в ГТУ - промежуточного охлаждения воздуха при многоступенчатом сжатии., охлаждении МОХ, деталей ГГ.
Кроме того, в любой СЭУ с помощью таких систем производится охлаждение опорных и упорных подшипников валопровода; прокачка дейдвудных труб. Система охлаждения может выполнять функции судового водопровода противопожарной и рефрижераторной системы..
В качестве охлаждаемых сред при работе таких систем ис-
пользуются забортная вода, пресная вода, масло и воздух. Выбор теплоносителя для конкретного случая определяется средним значениями температур теплоотвода, конструктивными особенностями и размерами охлаждаемых узлов или ТА.
Каждая из указанных сред имеет свои особенности. Например, при использовании в качестве охлаждающей жидкости забортной воды ее температура на выходе из охлаждаемых деталей или ТА должна быть не выше 50 - 55 °С. Ограничение температуры связано с тем, что с ее повышением происходит ускорение осаждения солей жесткости. Из механических примесей, имеющихся в морской воде, на теплопередачу влияют только те, которые способствуют загрязнению полостей охлаждения. Чаще всего это вещества минерального и органического происхождения с большим размером частиц.
Пресная вода имеет меньшую коррозионную активность, меньше загрязняет поверхность теплообмена, так как содержит меньше растворенных веществ (не более 0,1%). При использовании пресной воды в качестве охлаждающей среды представляет возможность повысить температурный режим, например, для охлаждения дизелей. Для уменьшения коррозионного действия охлаждающей пресной воде добавляют хромпик (2,5 - 5 г на 1 дистиллированной воды и 5 - 10 г на 1 л сырой воды).
Масло в отличие от воды как охлаждающая среда имеет больше положительных качеств (высокая температура кипения при атмосферном давлении, низкая температура застывания, малая коррозионная активность). К недостаткам можно отнести высокую стоимость, малую теплоемкость, низкий коэффициент тепловосприятия от охлаждаемой поверхности. Поэтому масло рекомендуется применять по необходимости, например, для охлаждения поршней ДВС.
Воздух в качестве охлаждающей среды преимущественно используется в ГТУ, в некоторых случаях может использоваться и для охлаждения .электрических генераторов и электродвигателей большой мощности, при условии его охлаждения забортной водой в ВОХ.
Применяемые в судовой практике системы охлаждения подразделяют на два типа: проточные и циркуляционные. Особенность работы проточной системы состоит в том, что охлаждающая вода на выходе из системы выбрасывается. При работе циркуляционной системы охлаждающая среда многократно циркулирует по замкнутому контуру, а тепло от нее отводится проточной забортной водой, т. е. в этом случае в охлаждении детали и узла механизма принимают участие два потока. Такие системы иначе называют двухконтурными. Ориентировочный удельный расход забортной воды на СЭУ с учетом потребности на компрессоры, на охлаждение по4шипников линии вала и другие нужды составляет 50 - 75 дм3/(кВт. ч) (3). Применение проточной или циркуляционной системы охлаждения зависит от температурного режима охлаждения в СЭУ.
Основным элементом систем охлаждения являются ЦН. Обычно используют насосы центробежного типа, а при большой производительности - пропеллерные. Насосы располагаются ниже уровня ватерлинии. Напор, создаваемый ЦН, расходуется на преодоление гидравлических сопротивлений ТА и трубопроводов системы охлаждения, а также на создание динамического напора. Величина напора насоса в ПТУ составляет 7-10 м вод. ст., ДЭУ-(15 - 20) м вод..ст., ГТУ - (10 - 15) м вод.ст.
Требуемая производительность ЦН определяется из условий отвода тепла от объектов охлаждения
где Q. ~ количество отводимого тепла на расчетном режиме, ккал/ч, Δt - разность температур охлаждающей жидкости на выходе и входе; С - теплоемкость охлаждающей жидкости. С учетом запаса производительность ЦН
. При наличии одного главного ЦН резервом может служить вспомогательный ЦН. Его производительность составляет 15 - 20 % от производительности главного.
В ПТУ температура охлаждающей воды на выходе из главного и вспомогательных конденсаторов на 4 - 8 °С ниже температур! конденсации пара. При поддержании давления в конденсаторе на уровне 0,05 ата температура конденсации будет 32,5 °С. В этом случае температура воды, выходящей из конденсатора, будет не более 24,5 - 28,5 °С. При таком температурном режиме возможно использование только проточной системы охлаждения. Гидравлическое сопротивление зависит от конструктивных особенностей конденсатора и системы охлаждения. Например, для двухпроточного конденсатора и охлаждающей системы величина сопротивления составляет 7,5 - 8,5 м вод.ст., а однопроточного совместно | системой охлаждения -- (4,5 - 5) м вод. ст.
На судах с большой скоростью хода циркуляция забортной воды в конденсационной установке может осуществляться само протоком за счет преобразования скоростного напора набегающей потока воды, образующегося при движении судна, в статически; напор. Его величина достаточна для преодоления гидравлически сопротивлений системы охлаждения. На малых ходах, а так» при работе на ЗХ вода в систему подается ЦН.
Целесообразность использования самопроточной циркуляции может быть определена на основе сопоставления расходов топлива, соответствующих работе, совершаемой за счет ГТЗА в случае
самопроточной циркуляции и на выработку электроэнергии, затрачиваемой на привод ЦН в случае несамопроточной циркуляции, при одинаковых условиях. При этом могут быть использованы следующие выражения (5):
Затрачиваемая мощность ГТЗА
Нагрузка
где R - буксировочное сопротивление системы, - скорость движения судна,
- пропульсивный КПД,
- КПД валопровода,
- КПД муфты сцепления, Q- объемный часовой расход воды, H-напор ЦН,
-КПД ЦН,
-КПД электродвигателя.
При этом расходы топлива для указанных случаев будут соответственно равны:
На транспортных судах ЦН кроме основного назначения используется
для аварийного водоотлива. Его производительность принимается
на 10 - 12% больше расхода воды на конденсатор при расчетной нагрузке турбины. Из этого избытка 4-5% расходуется на охлаждение некоторых вспомогательных устройств, а остальная часть составляет запас для компенсации снижения производительности из-за износа (6).
Для охлаждения ГД в системах предусмотрено два насоса равной производительности с электроприводом, из которых один является резервным. При размещении двух ГД в одном МО должно иметь только один резервный насос. Если на дизелях имеются навесные насосы, то роль резервного может выполнять автономный или навешенный насос. В таких системах в качестве охлаждающей жидкости используется пресная вода. Это дает возможность исключить образование накипи и отложений на стенка; охлаждаемых полостей, повысить температуру отвода тепла до 75 80° С, увеличить эффективный КПД двигателя и улучшить условия сжигания топлива.
Циркуляционная система охлаждения ДЭУ получила наибольшее распространение по сравнению с проточной, несмотря на то, что она сложнее, т. к. требует установки дополнительного насоса, цистерны, охладителя пресной воды и уравнительной цистерны. В качестве примера на рис. 2.7 приведена принципиальная схема циркуляционной системы охлаждения в ДЭУ.
Принципиальная схема циркуляционной системыохлаждения ДЭУ
1-дренажная трубка, 2 - конденсатор выпара, 3- расширительный бачок, 4 - компенсаторная трубка, 5 - клапан,-- терморегулятор, 7- насос забортной воды, 8 - ЦН, 9 - терморегулятор, 10 - ВОХ, 11 - МОХ).
Система охлаждения включает несколько контуров: первичный,
(ЦН, поз. 8, полости охлаждения дизеля, ВОХ, поз. 10),дренажно-компенсаторный (ГД, расширительный бачок, поз. 3, ГД) основной, вторичный (кингстон, насос, поз. 7, ВОХ, поз710, МОХ поз. 11). Для нормальной циркуляции пресной воды в первичном контуре необходимо соблюдение следующих условий: паров воды и воздуха из полостей охлаждения, пополнение убыли воды и обеспечение возможности изменения объема, заполняющей контур, в соответствии с изменением температуры. Дренажная трубка служит для непрерывного отвода паров воды и воздуха из полостей охлаждения, а компенсаторная - для возвращения в основной контур воды, поступающей в расширительный бачок с паром и воздухом. Температура пресной воды на входе в полости охлаждения дизеля равна t1, а на выходе – t2(t2>t1), соответственно на входе в ВОХ – t*1, а на выходе t*2. Для обеспечения нормальной работы системы охлаждения необходимо поддерживать следующее соотношение t*2<t1. Температура пресной воды регулируется с помощью терморегулятора (поз. 9). Соответствующая температура масла поддерживается с помощью терморегулятора (поз. 6), путем перепуска части воды, минуя МОХ.
В дизелях большой мощности, кроме цилиндров и поршней, охлаждаются и форсунки. Для этой цели используется отдельная система, выделяемая из общей системы охлаждения ГД. В ее состав входят ВОХ и насосы. Это дает возможность поддерживать у форсунки более низкую температуру по сравнению с системой охлаждения ГД, быстро определить и устранить возможное в эксплуатации протекание топлива между соплом и соплодержателем, а также предотвратить попадание топлива в пресную воду, циркулирующую в общей системе охлаждения ГД. Система охлаждения форсунок делается разомкнутой. Для этого охлаждающую воду, выходящую из форсунки, направляют через смотровую воронку в уравнительный бачок, в котором находится топливоотделитель. В принципе форсунки можно охлаждать и топливом. Это дает возможность предотвратить в случае появления тяги в корпусе форсунки проникновение в воду циркуляционной охлаждающей системы. Однако, учитывая, что теплоемкость топлива меньше по сравнению с водой, в этом случае уменьшается отвод тепла от корпуса форсунки. С другой стороны различные примеси в топливе могут вызвать разъедание металла и создать затруднения в уплотнении системы.
Для охлаждения ГТН используется пресная вода замкнутой системы охлаждения ГД.
При охлаждении ВД может быть использована как автономная (отдельные насосы и ВОХ), так и объединенная (охлаждение производится из общей системы охлаждения) система пресной воды.
В некоторых случаях автономная система при необходимости
может сообщаться с системой охлаждения ГД. Считается боле
целесообразным применять объединенную систему забортной воды, из которой вода подается ко всем потребителям. Например, использование объединенной системы забортной воды, позволяй упростить эксплуатацию установки и уменьшить объем ремонтам работ. Кроме того, повышается надежность работы установки вследствие исключения возможности выхода из строя дизель-генераторов из-за отказа навешенных насосов. В настоящее время такими системами оборудовано 80% морских судов.
В ГТУ с помощью системы охлаждения производится отвод МОХ, промежуточных ВОХ, корпусах и проточной части ГТ. Устройство системы аналогично применяемой в ДЭУ, за исключением охлаждения проточных частей ГТ. Оно осуществляется воздухом, отбираемым из промежуточных ступеней компрессоров. Корпус турбины высокого давления, например, ГТУ-20 охлаждается водой. Во избежание местного вскипания воды давление на выходе воды в полости охлаждения составляет 0,4 - 0,45 МПа. Такой способ охлаждения позволяет уменьшить радиальные зазоры проточной части. Хотя потери тепла с охлаждением корпуса составляют 0,6 - 0,8%, они компенсируются увеличением КПД ГТ 3 - 3,5%, вследствие уменьшения радиальных зазоров. Повышение экономичности ГТУ с учетом потерь тепла с охлаждающей водой и затратами энергии на прокачку воды примерно 1 - 1,5%. Кроме того, водяное охлаждение корпуса ГТ высокого давления дает возможность производить быстрые пуски из холодного состояния. Это объясняется тем, что радиальные зазоры в холодном состоянии назначаются большими, а при пуске они выбираются исключительно за счет роторной части. При таком охлаждении повышается надежность ГТ.
БИЛЕТ
Режимы работы СЭУ и их сущность. Характеристика режима работы СЭУ. Виды режимов Характерные особенности переходных и стационарных режимов. Эксплуатационные условия осуществления ходовых режимов работы СЭУ.
Режим работы СЭУ характеризуется совокупностью рабочих параметров функционально взаимосвязанных ее элементов. Он определяется положением органов управления СЭУ и внешними эксплуатационными условиями (изменение температуры воздуха и заб. воды, ветер, волнение, обрастание корпуса, льды, мелководье, парциальная работа, буксировка, реверсирование)
Различают 2 основных режимов работы СЭУ: переходный (неустановившийся) и стационарный (установившийся). 1- при неизменном положении органов управления раб. Пар-ры элементов СЭУ под действием указанных условием изменяются с течением времени. Иногда их называют нестационарными.
-у 2х раб.пар-ры остаются неизменными или являются периодическими функция-ми времени в течение длительного периода эксплуатации СЭУ.
Ходовые режимы в зависимости от хода судна подразделяются на режимы: самый малый, малый, средний, полный, самый полный. Эти режимы возможны при любых внешних эксплуатационных условиях.
Ходовые режимы работы СЭУ, осуществляемые при ходе судна на прямых курсах в открытом море в условиях штиля или при волнении не > 2-3 баллов и неизменном положении органов управления ГД, условно относят к установившимися. Режимы работы СЭУ в условиях большого волнения явл. неустановившимися.
БИЛЕТ
Оптимальные режимы работы СЭУ. Факторы, определяющие выбор критерия оптимальности. Критерии оптимальности для маневровых режимов работы СЭУ.
Для определения технико-экономических требований, предъявляемых к судну в целом используются оптимальные режимы работы СЭУ. Цель их оптимизации заключается в достижении экстремальных (минимальных или максимальных) значений одной или нескольких величин, называемых критериями. Чаще всего оптимизация проводится по первому критерию оптимальности. Однако это не означает, что найденный режим работы СЭУ будет целесообразен и по остальным критериям. Выбор критерия оптимальности зависит от многих факторов: от конъюнктуры, сложившейся на международном рынке; назначения и типа судна, условий плавания; характеристик ГД; движетелй; корпуса судна и т.д. Для судов в загранплавании этими критериями могут быть «себестоимость инвалютного рубля» и удельный чистый доход.
В качестве критерия оптимальности для маневренных режимов работы СЭУ могут быть приняты: путь и время разгона судна до заданной скорости до остановки. Ø циркуляции, время изменения курса судна на определенный < и т.д.
12 БИЛЕТ
Работа ГД и гребных винтов на швартовном режиме. Условия их работы. Соотношения значения мощности, упора и частоты вращения на этом режиме работы с номинальными значениями. Причины ограничения допустимой частоты вращения ГД при работе на таком режиме.
Работа этих элементов СЭУ и ПК на швартовом режиме происходит при λР=0 и является частным случаем работы по утяжеленной характеристике. В реальных условиях близкие к таким могут возникнуть режимы при трогании и разгоне судна, при буксировки тяжелого воза и др.
При работе ПК на швартовном режиме скорость судна =0 (V=0), а создаваемые при этом винтом упор и момент имеют максимальные значения.
При достижении номинальной част.вращ. в процессе работы на швартовом режиме может произойти перегрузка ГД м СЭУ в целом, с последующим повреждением и др. элементов ПК. Указанная перегрузка и связанные с ней повреждения, обуславливаются прежде всего величиной развиваемого крутящего момента. Однако на швартовом режиме немаловажное значение имеет и величина создаваемого упора, который может существенно превосходить значение, соответствующее номинальному режиму. В конечном итоге это может привести к перегрузке упорного подшипника и его повреждению.
БИЛЕТ
Характерные особенности парциальных режимов ГД и гребных винтов. Основные параметры и факторы, определяющие работу ГД и гребных винтов на этом режиме. Взаимная связь степени парциальности и нагрузки на работающий ГД. Факторы, определяющие относительную мощность, развиваемую каждым из работающих дизелей многомашинной ДЭУ, при работе на этом режиме.
Парциальные режимы характерны для многовальных СЭУ. Например: в 2-х вальных СЭУ такой режим при выходе из действия 1-го из винтов. При работе ГД в этом режиме аналогично швартовному значение приобретает определение его предельно допустимой N и n. Это обусловлено тем, что при выходе из действия, например,1-го из винтов сопротивление воды движению судна увеличивается>,чем в двое, т.к. к сопротивлению корпуса судна еще прибавляется сопротивление свободно вращающегося или застопоренного винта
PВ и сопротивление отклоненного пера руля.
Для анализа работы винтов в парциальном режиме в некоторых случаях используют степень их парциальности под ней понимается отношение с учетом
величины F упор каждого работающего винта при парциальной работе будет равен:
Это выражение подтверждает возрастание упора на работающих винтах при их парциальном использовании, при чем < FB, тем >падает нагрузка на работающий ГД.
При жесткой связи между дизелями и валопроводом относ-ая част. вращ. винта соответствует относ-ой част.вращ. дизелей при этом относ-ая мощность NПАР, развиваемая каждым из работающих дизелей, будет опре-ся из соотношения: , i – число дизелей в СЭУ:
mД-кол-во неработающих дизелей.
БИЛЕТ
Работы: ГД и гребных винтов в режиме буксирования судном воза. Меры i, исключающие перегрузку ГД. Соотношение полезной тяги и сопротивления ' движению судна в зависимости от наличия воза. Условия сохранения постоянства эффективного крутящего момента при буксировке воза.
В таком режиме ГД может работать на 2-х типах судов: специально предназначенных для буксировки и транспортных судах при выполнении вынужденных буксирных операций. В обоих случаях осуществляется буксировка воза, т.е. др. судна, баржи, плавучего крана, плота и т.п.
Во избежании перегрузки ГД, его утяжеление приводит к необходимости перевода его на работу по частичной характеристике и ограничения част.вращ.
При работе ГД в этом режиме в сочетании с различными винтами, имеются свои особенности. Например при использовании ВРШ часть потенциальной мощности ГД может быть использована для буксировки воза но при условии, если част.вращ. винта будет < номинальной. Полезная тяга винта определяется как: Pе=(1-t)P. Соотношение Ре и сопротивление движению судна находятся в зависимости от наличия воза. Здесь возможны след.варианты:
- при отсутствии воза: Ре=Р
-при наличии воза: Ре>Р
Для поддержания крутящего момента ГД Мео=const при буксировке необходимо снижать скорость движения судна, а следовательно и част.вращ. ГД.
БИЛЕТ
Характеристика работы гребного винта при плавании судна в штормовую погоду. Факторы, определяющие амплитуду колебаний нагрузки винта. Рекомендации по выбору режима работы комплекса ГД - гребной винт при плавании в такую погоду.
При плавании судна в штормовую погоду происходит качка и рыскливость его на курсе, их приводит к необходимости производить частые перекладки руля. В результате чего увеличивается тормозящее действие руля. При этом судно испытывает сильные периодические воздействия воды и ветра, относительное постоянство сопротивление движения судна нарушается. Оно приобретает резко переменный характер изменение сопротивления оказывает непосредственное влияние на характер работы винта, вызывая его заметные отклонения от расчетных значений для установившихся режимов движения. Изменения нагрузки винта переводят его работу с расчетной винтовой характеристики попеременно на более «тяжелую», на более «легкую». Амплитуда этих колебаний зависит от многих факторов, а именно, высоты и длины волн, силы ветра, размерений водоизмещения, курса судна по отношению к волне и т.п.
Колебания нагрузки винта непосредственно передаются элементам СЭУ, вызывая повышенные переменные напряжения в передаче и ГД. Колебания упора сказываются на работе главного упорного подшипника. В некоторых случаях может произойти оголение винта, что приводит к резкому снижению нагрузки. Част.вращ. ГД при этом может превзойти предельную, что вызовет срабатывание регулятора безопасности и остановку СЭУ. При плавании в штормовых условиях СЭУ рекомендуется использовать на умеренных режимах, тем самым гарантируя ее от возможных перегрузок. Опыт показывает, что повышение сопротивления движению судна при плавании в штормовую погоду происходит в основном за счет килевой качки. При этом возрастает и воздушное сопротивление до 10% и >.
БИЛЕТ
Мощностные характеристики ГД и гребного винта при плавании судна на мелководье. Условия снижения скорости при плавании судна на мелководье и глубокой воде и обеспечение допустимой напряженности работы ГД.
При плавании судна на мелкой воде изменение обтекания его корпуса и силы сопротивления воды несколько иное. В этом случае существенное значение имеют размеры судна, глубина воды и скорость хода.
При движении судна с большой скоростью в условиях мелководья возможно увеличение дифферента на корму и как следствие, сильное заливание и касание дна. Поэтому при переходе судна с глубокой воды в район мелководья необходимо привести снижение скорости хода. В качестве условия снижения скорости может быть принято сохранение равенство сопротивлений при плавании судна на мелководье и глубокой воде, т.е. RM=RГВ.В этом случае может быть обеспечена допустимая напряженность работы ГД.
Резкое повышение потребной мощности при плавании на мелководье в процессе развития скорости может привести к не-допустимым перегрузкам ГД и др. элементов ПК. Подобное изменение сопротивлений воды движению судна происходит при плавании в узкостях и каналах.
БИЛЕТ
Режимы работы ГД при плавании во льдах и узкостях. Рекомендуемая характеристика работы ГД в этих условиях судна
Плавание во льдах может вызвать различную степень повышения сопротивления движению судна, а работа ГД в этих условиях соответствовать как швартовному, так и буксирному режимы. Повышение сопротивления способствует переводит его на работу по «утяжеленной» винтовой характеристике.
БИЛЕТ
Влияние изменения температуры наружного воздуха на режим работы ГТУ. Влияние превышения допустимого крутящего момента и упора на состояние зубчатой передачи и главного упорного подшипника.
Параметры, определяющие
Изменение условий (например t наружного воздуха) в основном сказывается на режиме работе ГТУ. Не исключается влияние др. факторов (загрязнения проточных частей ГТД, значительный износ уплотнений и увеличение зазоров в проточных частях, нарушение регулировки и др.) В принципе сюда же можно отнести и условия плавания (в шторм, при сильном обрастании корпуса, парциальной работе установки, при буксировке и во льдах).
Суд. ГТУ выполняются из 2-х частей, механически не связанных между собой (газогенератора и независимой силовой турбины, работающей на винт). Изменение параметров кол-во вырабатываемого газа осуществляется с помощью регулирующих органов. Характер работы силовой турбины изменяется под действием внешней нагрузки, воспринимаемой от винта и энергии газового потока, вырабатываемого газогенератором. Указанные конструктивные особенности и условия регулировки позволяет изменять нагрузки силовой турбины независимо от работы газогенератора. При этом она реагирует на снижение и увеличение нагрузки соответствующим, изменением част.вращ. Подобное положение может привести к неблагоприятным явлениям, связанным с существенным превышением допустимого крутящего момента и упора, что может вызвать повреждение зубчатой передачи и гл. упорного подшипника. При эксплуатации ГТУ в таких условиях необходимы постоянный контроль, аннализ и ограничение ее нагруз. мощности. В судовых условиях это осуществляется путем наблюдения за величинами развиваемых част.вращ. турбокомпрессорным блоком высок. давления, силовой турбины, винтом и скоростью судна.
БИЛЕТ
Дата добавления: 2019-07-15; просмотров: 913; Мы поможем в написании вашей работы! |
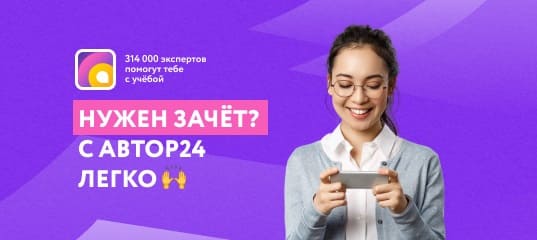
Мы поможем в написании ваших работ!