Дефекты термической обработки и меры их предупреждения.
Дефекты при отжиге могут возникать вследствие неправильного хода нагрева, применения слишком высоких или слишком низких температур, чрезмерной продолжительности нагрева, из-за неподходящей атмосферы в печи и неправильного режима охлаждения.
Недогрев– дефект, образующийся при нагревании стали до температуры ниже критической, что приводит к снижению ее прочности, твердости и пластических свойств. Этот дефект устраняется отжигом или нормализацией с последующей повторной термической обработкой.
Перегрев – дефект, являющийся следствием нагревания стали до температуры намного выше критической или чрезмерно большой выдержки при заданной температуре. Из-за перегрева получается крупноигольчатый мартенсит, механические свойства которого ниже мелкоигольчатого. Перегретую сталь отжигают и вновь подвергают закалке.
Окисление и обезуглероживание – дефекты, являющиеся результатом химических реакций, происходящих при нагреве стали между поверхностным слоем металла и кислородом окружающей среды. Эти процессы оказывают отрицательное влияние на конструктивную прочность изделий, приводят к потерям металла на угар, обуславливают необходимость увеличение припусков для последующей механической обработки. Применяют ряд способов предохранения стальных изделий от окисления и обезуглероживания при нагреве (нагрев в печах с контролируемой атмосферой, нагрев в расплавленных солях, нагрев в ящиках наполненных чугунной стружкой и т.п.).
|
|
Коробление и образование трещин – наиболее распространенные дефекты, являющиеся следствием возникновения в деталях больших внутренних напряжений, связанных с изменением их объема при закалке. Объемные изменения и сопровождающее их внутренние напряжения обусловлены двумя причинами. Первая причина – быстрое и резкое охлаждение изделий при закалке, в результате чего объем их различных слоев изменяется неравномерно. Другая причина появления закалочных трещин и коробления – изменение объема изделий при превращении аустенита в мартенсит. Из всех структурных составляющих стали, аустенит имеет наименьший объем, а мартенсит - наибольший. Так как при закалке аустенит переходит в мартенсит не одновременно по всему сечению изделия, в нем возникают внутренние напряжения. В тех местах изделия, где внутренние напряжения выше предела прочности стали, появляются трещины. Если внутренние напряжения значительны, но не достигают предела прочности стали, происходит коробление изделия.
Одним из способов уменьшения внутренних напряжений при закалке является предварительная подготовка изделия путем – отжига, нормализации или высокого отпуска. Весьма эффективный способ уменьшения внутренних напряжений – медленное охлаждение изделий при температурах превращения аустенита в мартенсит.
|
|
Недостаточная твердость – такой дефект получается в результате недогрева или недостаточно быстрого охлаждения изделия при закалке. Этот дефект исправляется правильной повторной закалкой, перед которой отжигом, нормализацией или высоким отпуском снимаются внутренние напряжения.
Термическая обработка чугуна.
Предыдущая22232425262728293031323334353637Следующая
Термическую обработку чугунов производят с целью снятия внутренних напряжений, возникающих при литье и вызывающих с течением времени изменением размеров и формы оливки, снижения твердости и улучшения обрабатываемости резанием, повышения механических свойств.
Отжиг чугуна.
Отжиг для снятия внутренних напряжений. Этому отжигу подвергают чугуны при следующих температурах: серый чугун с пластинчатым графитом 500-570 ºС; высокопрочный чугун с шаровидным графитом 550-650 ºС; низколегированный чугун 570-600 ºС; высоколегированный чугун 620-650 ºС. Скорость нагрева составляет примерно 70-100 град/час, выдержка при температуре нагрева зависит от массы и конструкции отливки составляет от 1 до 8 часов. Охлаждение до 200 ºС (для предупреждения возникновения термических напряжений) медленное, со скоростью 20-50 град/час, что достигается охлаждением отливки вместе с печью. Далее отливки охлаждают на воздухе. Результатом этого вида отжига является снятие внутренних напряжений, повышение вязкости, исключается коробление и образование трещин в процессе эксплуатации.
|
|
Смягчающий отжиг (отжиг графитизирующий низкотемпературный) проводят для повышения обрабатываемости резанием и повышения пластичности. Его осуществляют длительной выдержкой при 680-700 ºС (ниже точки А1). Время выдержки для серых чугунов 1-4 часа, для ковких чугунов до 60 часов. Охлаждение медленное для деталей сложной конфигурации и ускоренное для деталей простой формы. В результате этого отжига в чугуне увеличивается количество феррита.
Отжиг графитизирующий, в результате которого из белого чугуна получают ковкий чугун.
Нормализация(серого и ковкого чугуна) при температуре 850-950 ºС. Время выдержки должно быть достаточным для насыщения аустенита углеродом (1 -3 часа). Охлаждение ускоренное, чтобы аустенит смог превратится в перлит и чаще всего осуществляется на воздухе. В результате нормализации получается структура перлит + графит и повышается прочность и износостойкость. После нормализации для снятия внутренних напряжений применяется высокий отпуск при 650-680 ºС с выдержкой 1-1,5 часа.
|
|
Закалка и отпуск чугуна.
Для закалки чугун нагревают до температуры 850-950 ºС. Время нагрева обычно составляет от 1 до 3 часов (полное растворение углерода в - железе). Охлаждение осуществляется в воде или масле. При закалке аустенит превращается в мартенсит или троостит + графит. После закалки проводят отпуск при температуре 200-600 ºС. В результате повышается твердость, прочность и износостойкость чугуна.
При изотермической закалке чугун нагревают и выдерживают от 10 до 90 минут, после чего охлаждают в расплавленной соли при 200-400 ºС. В результате этого аустенит распадается с образованием структуры игольчатого троостита + графит. Изотермическая закалка позволяет повысить твердость и прочность, сохраняя пластичность.
Поверхностная закалка с нагревом поверхностного слоя кислородо-ацетиленовым пламенем, ТВЧ или в электролите. Нагрев до 900-1000 ºС. Охлаждение в воде, масле или масляной эмульсии. При поверхностной закалке в поверхностном слое образуется мартенсит + графит или троостомартенсит + графит. Отпуск при 200-600 ºС, охлаждение на воздухе. В результате повышается твердость, прочность и износостойкость поверхностного слоя при наличии мягкой сердцевины.
Старение чугуна.
Для стабилизации размеров литых чугунных деталей, предотвращения коробления и снятия внутренних напряжений применяют старение.
Различают два вида старения: естественное и искусственное. Естественное старение осуществляется на открытом воздухе или в помещении склада. Изделия после литья выдерживаются в течении 6-15 месяцев. При естественном старении снижение напряжений в отливках составляет 3-10 %.
Искусственное старение осуществляется при повышенных температурах; длительность несколько часов.
Нагрев до температуры 550-570 ºС со скоростью 30-60 ºС в час, выдержка при этой температуре 3-5 ч и охлаждение вместе с печью до 150-200 ºС, с последующим охлаждением на воздухе.
Дата добавления: 2019-02-26; просмотров: 2608; Мы поможем в написании вашей работы! |
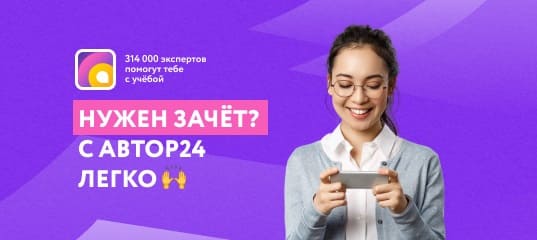
Мы поможем в написании ваших работ!