Термическая обработка стали и чугуна.
Предыдущая21222324252627282930313233343536Следующая
Термической обработкой называется тепловая обработка, в результате которой изменяется структура и физико-механические свойства металлических сплавов.
Термической обработке подвергаются как заготовки, так и готовые детали. Заготовки обычно подвергаются термической обработке для улучшения структуры, снижения твердости, а обрабатываемые детали – для придания им требуемых свойств: твердости, прочности, износостойкости, упругости и др. В результате термической обработки свойства сплавов могут быть изменены в широких пределах. Возможность значительного повышения механических свойств после термической обработки деталей машин и изделий позволяет увеличить допускаемые напряжения, уменьшить размеры и вес деталей и механизмов, повысить надежность и срок службы изделий.
Научные основы термической обработки были заложены исследованиями выдающегося русского ученого Дмитрия Константиновича Чернова в середине XIX века. В результате коллективного труда многих ученых, развивающих идеи Д.К.Чернова, мы имеем весьма точную диаграмму состояния железоуглеродистых сплавов (см. Диаграмма состояния системы «железо – углерод» (Рис.37.)).
Цель термической обработки заключается в том, чтобы нагревом до определенной температуры и последующим охлаждением получить требуемое изменение строения металла.
На результат термической обработки оказывают влияние следующие факторы: скорость нагрева, температура нагрева, продолжительность выдержки, скорость охлаждения.Таким образом, основными факторами термической обработки являются температура и время.
|
|
Основными операциями термической обработки, общими как для стали и чугуна, так и для цветных металлов, являются отжиг, нормализация, закалка и отпуск.
Термическая обработка, может быть, простой и состоять только из одной операции и сложной, состоящей из нескольких операций.
Превращения в стали при нагреве и охлаждении.
Нагрев стали при термической обработке в большинстве случаев имеет целью перевод ее структуры в аустенит. Структура доэвтектоидной стали при нагреве до точки Ас, состоит из зерен феррита и перлита.
В точке Ас1 начинается фазовая перекристаллизация перлита, который превращается в мелкозернистый аустенит. При нагреве стали от температуры Ас1 до температуры Ас3 феррит растворяется в аустените. В заэвтектоидной стали при нагреве выше точки Ас1 перлит превращается в аустенит, а при дальнейшем нагреве цементит растворяется в аустените. Выше точки Асm сталь состоит только из аустенита, неоднородного по химическому составу. В тех местах где был цементит, аустенит богача углеродом, а там, где был феррит, - беднее. Поэтому при термической обработке для выравнивания химического состава аустенита сталь нагревают до температуры немного выше верхней критической точки Ас3 мелкие зерна аустенита соединяются между собой, размеры их увеличиваются. Величину зерен определяют путем сравнения микроструктуры стали (при увеличении в 100 раз) со стандартной шкалой. Зерна с номера 1 по 4-й считаются крупными, а с 5-го по 10-й – мелкими (Рис.49.).
|
|
.
Аустенит устойчив только при температурах выше 727º С. При охлаждении стали, нагретой до аустенитного состояния, ниже точки Аr1 начинается распад аустенита. Как уже было
сказано (см. Диаграмма состояния системы «железо – углерод»), при медленном охлаждении эвтектоидной углеродистой стали (0,81 %углерода) при температуре, соответствующей линии PSK, происходит превращение аустенита в перлит. Кристаллическая решетка - железа перестраивается в
- железо, выделяется цементит.
Рис.50. Диаграмма изотермического превращения аустенита стали, содержащей 0,8% углерода
Для изучения изотермического превращения аустенита небольшие образцы стали нагревают до температур, соответствующих существованию стабильного аустенита, т.е. выше критической точки, а затем быстро охлаждают, например до 700, 600, 500, 400, 300ºС и т.д., и выдерживают при этих температурах до полного распада аустенита. Изотермическое превращение аустенита эвтектоидной стали происходит в интервале температур от 727 до 250ºС (температура начала мартенситного превращения - Мн).
|
|
На диаграмме (см. диаграмму изотермического превращения (Рис.50.)) видны две С-образные кривые. Кривая I указывает время начала превращения, кривая II- время конца превращения переохлажденного аустенита. Период времени до начала распада аустенита называют инкубационным. При 700ºС превращение аустенита начинается в точке а и заканчивается в точке в, в результате этого процесса образуется перлит. При 650ºС распад аустенита происходит между точками а1 и в1 . в этом случае образуется сорбит.
Рис.51. Микроструктуры.
Сорбит– механическая смесь феррита и цементита, отличающаяся от перлита более тонким строением. Магнитен. Образуется при ускоренном охлаждении при распаде аустенита в интервале температур 600-700ºС или при отпуске мартенсита. НВ 270-320 (30-40 HRC) (Рис.51.). Такая сталь обладает высокой прочностью и пластичностью. При охлаждении стали до 550ºС (точка начала и конча распада а2 и в2 соответственно) аустенит превращается в троостит.
|
|
Троостит – механическая смесь феррита и цементита, отличающаяся от сорбита еще более высокой степенью дисперсности. Магнитен. Образуется при ускоренном охлаждении при распаде аустенита в интервале температур 400 - 600ºС , а также при отпуске мартенсита. НВ 330-400 (40-45 HRC) (Рис.51.). Обладает достаточной прочностью, умеренной вязкостью и пластичностью.
Ниже температуры 550ºС в результате промежуточного превращения аустенита (в температурном интервале, расположенном ниже перлитного но, выше мартенситного превращения) образуется структура бейнита, состоящая из смеси перенасыщенного углеродом феррита и карбидов (цементита).
Различают верхний бейнит (перистого строения), появляющийся при 500-350ºС, и нижний (пластинчатого, игольчатого строения), образующийся при 350-250ºС.
Верхний бейнит имеет пониженную прочность, невысокую пластичность и вязкость, твердость его 43-46 HRC. У нижнего бейнита показатели прочности, пластичности и вязкости более высокие, твердость 52-55 HRC. Превращение аустенита при температурах Аr - 550ºС называют перлитными, при температурах 550ºС – Мн – промежуточными и при температурах Мн – Мк – мартенситными.
При медленном охлаждении аустенит превращается в перлит. При большей скорости охлаждения переохлажденный аустенит полностью перейдет в сорбит. При еще больших скоростях охлаждения образуется новая структура – троостит. При очень больших скоростях охлаждения образуется мартенсит.
Мартенсит – перенасыщенный твердый раствор углерода в - железе (Рис.52.), полученный из аустенита в результате бездиффузионного превращения (перестройки кристаллической решетки
- железа без изменения концентрации углерода). Микроструктура игольчатого вида. Образуется в процессе быстрого охлаждения при температуре ниже 250 -200ºС. НВ 500-700.
При образовании мартенсита происходит перестройка гранецентрированной решетки аустенита в объемно-центрированную решетку - железа. Избыточное содержание углерода находящегося в
- железе, искажает эту решетку и превращает ее в тетрагональную, в которой отношение параметров с/а не равно единице, как у куба.
Рис.52.Элементарная ячейка кристаллической решетки мартенсита
Степень тетрагональности тем выше, чем больше углерода в стали. Скорость охлаждения, при которой из аустенита образуется только мартенсит, называют критической скоростью закалки. При закалке стали ее охлаждают со скоростью больше критической.
Мартенситные превращения протекают при непрерывном охлаждении аустенита ниже точки Мн. по достижении определенной температуры (точка Мк) превращение аустенита в мартенсит заканчивается. Температуры в точках Мн и Мк зависят от химического состава стали. Углерод и легирующие элементы (за исключением алюминия и кобальта) понижают эти температуры.
Мартенсит обладает самой высокой твердостью, наряду со значительной хрупкостью. Он имеет пластинчатое строение, но в плоскости микрошлифа пластинки приобретают вид игл, поэтому мартенсит часто называют игольчатым (Рис.53.).
Рис.53.
У многих сталей температура в точке Мк ниже комнатной, поэтому распад аустенита не заканчивается, если сталь охлаждается только до комнатной температуры. Аустенит, который сохраняется в структуре стали при комнатной температуре, наряду с мартенситом, называют остаточным. Закаленные высоколегированные стали содержат остаточный аустенит в больших количествах, а низкоуглеродистые его почти не имеют.
Мартенсит, получаемый при закалке стали, представляет собой неустойчивую структуру, стремящуюся к превращению в более равновесное состояние. Нагрев ускоряет этот переход, так как подвижность атомов при этом сильно возрастает.
Отжиг стали.
Отжигомназывается операция термической обработки, при которой путем нагрева, выдержки при установленных температурах и последующего медленного охлаждения в стали получают устойчивую (равновесную) структуру, свободную от остаточных напряжений.
Отжиг стальных изделий имеет целью снятие внутренних напряжений, устранение структурной неоднородности, улучшение обрабатываемости резанием и подготовку к последующей термической обработке.
Отжиг первого рода. Это отжиг, при котором, как правило, не происходит фазовых превращений (перекристаллизации), а если они имеют место, то не оказывают влияния на конечные результаты.
Различают следующие разновидности отжига первого рода: гомогенизационный (диффузионный), низкий и рекристаллизационный.
Гомогенизационный отжиг, или гомогенизация, применяется для выравнивания химической неоднородности (за счет диффузии) зерен твердого раствора, т.е. уменьшения микроликвации в фасонных отливках и в слитках главным образом из легированной стали.
В процессе гомогенизации слитки нагревают до 1100–1200 ºС, выдерживают при этой температуре 8 -15 часов, а затем медленно охлаждают до 200-250 ºС. Продолжительность отжига 80-110 часов.
Рекристаллизационному отжигу подвергают сталь, деформированную в холодном состоянии. Наклеп может оказаться столь большим, что сталь становиться мало пластичной и дальнейшая деформация становится невозможной. (После ковки холодного металла заметно возрастает его прочность и твердость. В то же время он становится хрупким. Это явление получило название «наклеп». Наклепом называют как сам процесс изменения внутреннего строения металла при холодной пластической деформации, так и получающийся при этом результат, т.е. повышение прочности и твердости, сопровождающееся уменьшением пластичности.) Для возвращения стали пластичности, и возможности дальнейшей деформации изделия проводят рекристаллизационный отжиг.
При нагреве холоднодеформированной стали до температуры 400-450 ºС изменений в строении стали не происходит, механические свойства изменяются незначительно и только снимается большая часть внутренних напряжений. При дальнейшем нагреве механические свойства стали резко изменяются: твердость и прочность понижаются, а пластичность повышается (Рис.54.).
.
Рис.54. Влияние температуры отжига на механические свойства деформированного металла
Это происходит в результате изменения строения стали. Вытянутые в результате деформации зерна становятся равноосными.
Рекристаллизация начинается с появления зародышей на границах деформированных зерен. В дальнейшем зародыши растут за счет деформированных зерен, в связи с чем происходит образование новых зерен, пока деформированных зерен совсем не останется.
Под температурой рекристаллизации подразумевается та температура, при которой в металлах, подвергнутых деформации в холодном состоянии, начинается образование новых зерен. Для ускорения процесса рекристаллизации, холоднодеформированные металлы и сплавы, нагревают до более высоких температур, например углеродистую сталь до 600-700 ºС.
Низкий отжиг. Если структура стали после горячей механической обработки хорошая и нет необходимости в перекристаллизации, внутренние напряжения, то нагревают сталь ниже Ас1 . Нагрев осуществляется со скоростью 100-150 град/час, а после выдержки - охлаждение на воздухе. Углеродистые и легированные стали подвергают низкому отжигу перед обработкой резанием, волочением и т.д.
Отжиг второго рода. Это отжиг, при котором фазовые превращения (перекристаллизация) определяют его целевое назначение.
Различают следующие разновидности отжига второго рода: полный отжиг, неполный отжиг, изотермический отжиг.
Полный отжиг. При полном отжиге доэвтектоидная сталь нагревается выше Ас3 на 30-50 ºС (Рис.55.), выдерживается при этой температуре до полного прогрева и медленно охлаждается. В этом случае ферритно-перлитная структура переходит при нагреве в аустенитную, а затем при медленном охлаждении превращается обратно в феррит и перлит. Происходит полная перекристаллизация.
На практике скорость нагрева обычно близка к 100 град/час, а продолжительность выдержки колеблется от 0,5 до 1 часа на тонну нагреваемого металла. Чрезмерное повышение температуры нагрева металла над точкой Ас3 вызывает рост зерна аустенита, что ухудшает свойства стали.
Основные цели полного отжига: устранение пороков структуры, возникших при предыдущей обработке металла (сварка, литье, горячая деформация, термообработка), смягчение стали перед обработкой резанием и снятие внутренних напряжений.
Неполный отжиг. Неполный отжиг заключается в нагреве выше Ас1 (Рис.55.) и медленном охлаждении. При этом происходит частичная перекристаллизация перлитной составляющей.
Неполному отжигу подвергают доэвтектоидные стали с целью снятия внутренних напряжений и улучшения обрабатываемости резанием в том случае, если предварительная горячая обработка не привела к образованию крупного зерна.
Неполный отжиг заэвтектоидных сталей называется также отжигом сфероидизации. В результате отжига сфероидизации получают структуру – зернистый перлит. Охлаждение при сфероидизации должно быть медленным, чтобы обеспечить распад аустенита на ферритно-карбидную смесь.
Стали со структурой зернистый перлит менее склонны к перегреву, образованию трещин и деформации при последующей закалке, а также хорошо обрабатываются резанием.
Изотермический отжиг. На практике с целью экономии времени часто проводят изотермический отжиг. В этом случае сталь нагревают, а затем быстро охлаждают (чаще переносом в другую печь) до температуры лежащей ниже Ас1 на 50-100 ºС. При этой температуре сталь выдерживается до полного распада аустенита, после чего охлаждается на воздухе. Изотермический отжиг часто применяют для легированных сталей, так как он сокращает продолжительность процесса.
Светлый отжиг осуществляется по режимам полного и неполного отжига с применением защитных атмосфер или в печах с частичным вакуумом.
Светлый отжиг применяется для холоднокатаной ленты, проволоки и т.д., а также для деталей, подвергаемых гальваническим покрытиям с целью защиты поверхности металла от окисления и обезуглероживания.
Рис.55.
Нормализация.
Нормализацией называется нагрев доэвтектоидной стали до температуры выше Ас3 (Рис.55.) , а заэвтектоидной – выше Асm на 50-60 ºС с последующем охлаждением на воздухе. При нормализации происходит перекристаллизация стали, устраняющая крупнозернистую структуру, полученную при литье или ковке.
В результате охлаждения на воздухе распад аустенита на ферритно-цементитную смесь происходит при более низких температурах, а следовательно, повышается дисперсность смеси.
Назначение нормализации различно в зависимости от состава стали. Вместо отжига низкоуглеродистые стали подвергают нормализации. В результате твердость немного возрастает, но улучшается качество поверхности при резании.
Для среднеуглеродистых сталей нормализацию применяют вместо закалки и высокого отпуска (улучшения). Механические свойства при этом понижаются, но уменьшается деформация изделия по сравнению с получаемой при закалке.
Высокоуглеродистые (заэвтектоидные) стали подвергают нормализации с целью устранения цементитной сетки.
Нормализацию с последующим высоким отпуском применяют вместо отжига для исправления структуры легированных сталей.
Закалка.
Закалкой называется операция термической обработки, состоящая в нагреве до температур выше (Рис.56.) верхней критической точки Ас3 доэвтектоидной стали и выше нижней критической точки Ас1 заэвтектоидной стали и выдержки при данной температуре с последующим быстрым охлаждением (в воде, масле, водных растворах солей и пр.).
Закалкой можно считать такую термообработку, при которой сталь приобретает неравновесную структуру (сорбит, троостит, бейнит, мартенсит) что, прежде всего, выражается в повышении твердости стали.
Закалкой достигается повышение прочности конструкционных сталей и придание режущей способности инструментальной стали. Температура нагрева стали перед закалкой зависит в основном от химического состава стали. При закалке доэвтектоидных сталей нагрев следует вести до температуры, лежащей на 30-50 ºС выше точки Ас3. В этом случае сталь имеет структуру однородного аустенита, который при последующем охлаждении со скоростью, превышающей критическую скорость закалки, превращается в мартенсит. Такая закалка называется полной.
Максимальная скорость охлаждения, при которой аустенит превращается в мартенсит без структур перлитного типа, называется критической скоростью закалки.
Рис.56. Интервал закалочных температур углеродистой стали
При нагреве доэвтектоидной стали до температур, лежащих в интервале Ас1- Ас3, в структуре мартенсита сохраняется некоторое количество феррита, снижающего твердость закаленной стали. Такая закалка называется неполной. Для заэвтектоидной стали наилучшая температура закалки – на 29-30 ºС выше Ас1, т.е.неполная закалка. В этом случае сохранение цементита при нагреве и охлаждении будет способствовать повышению твердости, так как твердость цементита больше твердости мартенсита. Нагрев заэвтектоидной стали до температур выше Асm излишен, так как твердость получается меньшей, чем при закалки с температуры Ас1, за счет растворения цементита и увеличения количества остаточного аустенита. Кроме того, при охлаждении с более высоких температур могут возникнуть большие внутренние напряжения.
Скорость охлаждения оказывает решающее влияние на результаты закалки.
Для каждой стали существует критическая скорость закалки, чем ниже эта скорость, тем легче закалить сталь. Фактическая скорость охлаждения при закалке должна быть меньше критической, иначе мартенсит в структуре стали либо не образуется совсем, либо образуется частично, тогда структура стали будет состоять в основном из троостита или сорбита. Однако не следует охлаждать сталь со скоростью, значительно превышающей критическую. При таком охлаждении сталь будет иметь структуру мартенсита, но чрезмерно резкая закалка может привести к весьма значительным внутренним напряжениям и трещинам.
Различна скорость охлаждения изделий при закалке достигается за счет применения охлаждающих жидкостей: воды, масла, растворов солей в воде и др. При охлаждении в жидкости изделие отдает часть своей теплоты соприкасающейся с ним жидкости, превращающейся в пар. Теплота, расходуемая на образование пара, называется скрытой теплотой парообразования. Чем выше теплота парообразования, тем выше закаливающая способность жидкости, так как изделие, отдавая большое количество тепла на образование пара, будет быстрее охлаждаться.
Самая распространенная закалочная среда – вода. Ее охлаждающая способность зависит от температуры. Чем выше температура воды, тем меньше ее закалочная способность. Обычно при закалке применяется вода с температурой 20-30 ºС.
Так же в качестве закалочной жидкости используют 5-10-процентный раствор едкого натра или поваренной соли в воде. Вода, в которой растворены хлористый натрий или едкий натр, имеет более высокую скрытую теплоту парообразования. Частицы соли, соприкасаясь с раскаленным металлом, взрываются и разрушают паровую рубашку, тем самым, увеличивая закаливающую способность воды.
Широкое распространение в качестве охлаждающей среды получило минеральное масло, преимущественно индустриальное. Масло, подогретое до 50-60 ºС, обладает более высокой закаливающей способностью, чем холодное. Это объясняется тем, что при нагреве масло становится менее вязким, его паровая рубашка разрушается быстрее.
Закалочная способность масла при 550-650 ºС в 4 - 5 раз меньше, чем холодной воды, однако при 200-300 ºС масло охлаждает изделие в 10 раз медленнее, чем вода, поэтому при закалке изделий в масле значительно уменьшается опасность их коробления и появления трещин.
Виды закалки стали.
Выбор способа закалки зависит от, состава стали из которой изготовлена деталь, ее размеров и формы.
Закалка в одном охладители. (кривая охлаждения 1) (Рис.57.) деталь нагретую до закалочной температуры погружают в закалочную среду, где она остается до полного охлаждения. Данный вид закалки применяют для деталей простой формы из углеродистой и легированной стали. В качестве охлаждающей жидкости для углеродистых сталей применяют воду, легированные стали охлаждают в масле.
Рис.57.
Закалка в двух средах (кривая охлаждения 2) (Рис.57.) широко применяется для инструмента из высокоуглеродистой стали. Сущность способа состоит в то, что деталь вначале охлаждают в воде, до температуры немного выше Мн (температура начала мартенситного превращении), а затем переносят в масло или другую охлаждающую среду, где оставляют до полного охлаждения.
Ступенчатая закалка (кривая охлаждения 3) (Рис.57.) выполняется путем быстрого охлаждения деталей в соляной ванне температура которой немного выше температуры мартенситного превращения (240-250 ºС). Выдержка при этой температуре должна обеспечить выравнивание температур по всему сечению детали. Затем детали охлаждают до комнатной температуры в масле или на спокойном воздухе, устраняя тем самым термические внутренние напряжения.
Изотермическая закалка (кривая охлаждения 4) (Рис.57.) проводится так же, как ступенчатая, но с более длительной выдержкой при температуре горячей ванны – для обеспечения полного распада аустенита. В результате такой закалки сталь приобретает структуру игольчатого троостита, с твердостью НRС 45-55 и с сохранением небольшой пластичности. В основном изотермической закалке подвергают легированные стали. В качестве охлаждающей среды используют расплавленные соли: 55 % KNO3 + 45 % NaNO2 (температура плавления 137 ºС), и 55 % KNO3 + 45 % NaNO3 (температура плавления 218 ºС).
Светлая закалка стальных деталей производится в специально оборудованных печах с защитной атмосферой.
Так же для получения чистой и светлой поверхности применяют ступенчатую закалку с охлаждением в расплавленной едкой щелочи. Деталь нагревают в соляной ванне из хлористого натрия при температуре на 30-50 ºС выше точки Ас1 и охлаждают при температуре 180-200 ºС в ванне, состоящей из 75 % едкого калия и 25 % едкого натра с добавлением 6-8 % воды (от веса всей соли). Такая смесь имеет температуру плавления 145 ºС и благодаря наличию воды обладает очень высокой закаливающей способностью.
Закалка с самоотпуском. Детали выдерживают в охлаждающей среде не до полного охлаждения, а в определенный момент извлекают из нее с целью сохранения в сердцевине изделия некоторого количества тепла, за счет которого производится последующий отпуск. После достижения требуемой температуры отпуска за счет внутреннего тепла деталь окончательно охлаждают в закалочной жидкости. Закалка с самоотпуском применяется для различного инструмента, требующего высокой твердости на поверхности и сохранения вязкой сердцевины.
Отпуск стали.
Отпуском называется операция термической обработки, состоящая в нагреве закаленной стали до температуры ниже критической точки Ас1, выдержке при этой температуре и последующем медленном или быстром охлаждении.
Отпуск имеет целью устранение или уменьшение напряжений в стали, повышение вязкости и понижение твердости.
Отпуск является заключительной операцией термической обработки.
В зависимости от температуры нагрева различают низкий, средний и высокий отпуск.
Низкий отпуск характеризуется нагревом в интервале 80-200 ºС, выдержки при этой температуре и последующем охлаждении на воздухе. Этот отпуск снижает внутренние напряжение в стали при сохранении высокой твердости (58-63 HRC). Он применяется преимущественно для инструмента из углеродистой и низколегированной стали, а также для деталей, подвергаемых поверхностной закалке, цементации и нитроцементации, к которым предъявляются высокие требования по твердости и износостойкости.
Средний отпуск осуществляется при температурах 350-500 ºС. Целью этого отпуска является получение структуры троостита. Твердость стали заметно понижается (40-50 HRC), предел упругости достигает максимальной величины. Средний отпуск применяют для пружин, рессор, а также инструмента, который должен иметь значительную прочность и упругость при средней твердости.
Высокий отпуск производится при температурах 550-680 ºС.
Сталь при этом приобретает структуру сорбита. Твердость закаленной стали снижается до 250-350 НВ, прочность уменьшается в 1,5-2 раза, пластичность и вязкость увеличиваются в несколько раз, внутренние напряжения полностью снимаются. Закалка с высоким отпуском называется улучшением. Улучшенная сталь по сравнению с отожженной или нормализованной имеет более высокие показатели прочности, пластичности и вязкости.
Старение – это процесс изменения свойств сплавов без заметного изменения микроструктуры. В результате старения прочность и твердость повышаются, а пластичность и вязкость снижаются. Старение приводит к изменению размеров и короблению изделий. Если старение протекает при комнатной температуре, его называют естественным, если при повышенной температуре – искусственным. Известны два вида старения: термическое и деформационное. Термическое старение происходит в результате изменения растворимости углерода в - железе в зависимости от температуры. Деформационное строение протекает в сплаве, подвергнутом пластической деформации при температуре ниже температуры рекристаллизации. Процесс этого старения длится 15 суток и более при комнатной температуре и всего несколько минут при температурах 200-350 ºС.
Искусственное старение закаленных и отпущенных при низкой температуре изделий производится после предварительной механической обработки при 100-180 ºС с выдержкой в течении 18-35 часов и медленным охлаждением. Естественное старение осуществляется на открытом воздухе под навесом, где на изделия воздействуют температурные изменения, влажность и давление воздуха. Оно длится от 3 месяцев до 2 лет. Результатом естественного старения является снижение внутреннего напряжения, стабилизация размеров и геометрической формы изделия.
Обработка стали холодом.
В некоторых сталях – углеродистых (при содержании более 0,4-0,5 % углерода) и легированных – в закаленном состоянии содержится повышенное количество остаточного аустенита – 3-12 %, а в быстрорежущих – 35 % и более. Это объясняется тем, что температура конца мартенситного превращения (Мк) указанных сталей ниже нуля градусов, а при закалке охлаждение производится только до комнатной температуры. Остаточный аустенит в стали снижает ее твердость и при постепенном самопроизвольном распаде вызывает изменение размеров детали из этой стали. Закаленные стали, в структуре которых имеется остаточный аустенит, подвергают охлаждению до температур ниже нуля градусов. Под действием отрицательных температур остаточный аустенит перестраивается в мартенсит, что способствует повышению твердости, улучшению магнитных характеристик, стабилизации размеров, повышению стойкости и усталостной прочности изделий. Твердость после обработки холодом возрастает на 1-5 HRC и более.
Необходимую температуру получают с помощью сухого льда (твердая углекислота), жидкого кислорода или жидкого воздуха. Термообработку с применением холода осуществляют по схеме: закалка – обработка холодом – низкий отпуск.
Термомеханическая обработка стали.
Термомеханической обработкой называется процесс, при котором термическая обработка совмещается с обработкой давлением. При такой обработке сталь нагревают до температуры выше критической точки Ас3 и выдерживают при этой температуре с последующей пластической деформацией аустенита для получения в нем особой мартенситной структуры.
Термомеханическая обработка способствует повышению механических свойств стали.
Дата добавления: 2019-02-26; просмотров: 420; Мы поможем в написании вашей работы! |
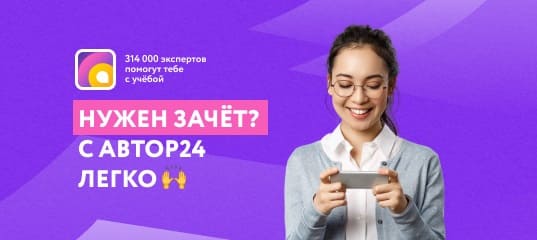
Мы поможем в написании ваших работ!