Получение стали в электрических печах.
Предыдущая15161718192021222324252627282930Следующая
Для производства стали наиболее часто применяют трехфазные дуговые электрические печи (Рис.48) с вертикальными графитовыми или угольными электродами и непроводящим подом. Ток, нагревающий ванну в этих печах, проходит по цепи электрод – дуга – шлак – металл – шлак – дуга – электрод. Печь состоит из металлического кожуха цилиндрической формы и сферического или плоского дна. Внутри печь футерована огнеупорным материалом. Подобно мартеновским, дуговые печи могут быть кислыми и основными. В основных печах подина выкладывается из магнезитового кирпича, сверху которого делается набивной слой из магнезита или доломита толщиной 150 – 200 мм. В кислых печах применяют динасовый кирпич и набивку из кварцита на жидком стекле.
В цилиндрической части печи имеется рабочее окно и выпускное отверстие с желобом. Электрические печи имеют механизмы для наклона печи в сторону выпускного отверстия на 40 - 45º для слива металла и на 10 – 15º в сторону рабочего окна для скачивания шлака. Свод печи обычно сферический и через него опускают в печь три электрода. Рядом с печью помещены механизмы для подъема электродов и понижающий трансформатор, питающий печь электроэнергией. Небольшие печи загружают через окно (с помощью мульд и завалочной машины), а печи вместимостью более пяти тонн – через свод (с помощью бадьи или сетки). В этом случаи свод с электродами делают съемным и в период загрузки его поднимают, печь отводят в сторону и мостовым краном загружают полную садку печи. После этого сводом быстро накрывают печь.
|
|
Рассмотрим плавку стали с окислением в основной дуговой печи. После загрузки печи электроды опускают на металлическую шихту, предварительно засыпав ее сверху известью в количестве 2-3 % от массы загруженного в печь металла. Известь способствует ровному горению дуги, предохраняет металлы от поглощения газов и быстрее образует шлак. Плавление ведут при наибольшей мощности печи, чтобы быстрее создать жидкую фазу. Еще до полного расплавления шихты в печь засыпают известь и железную руду для получения в первом периоде плавки окисленного шлака. Через 10-15 мин после загрузки руды из печи скачивают 60-70 % шлака – с ним удаляется большая часть фосфора, преимущественно в виде фосфатов железа, как и при плавке в мартеновской печи.
После скачивания шлака в печь опять засыпают известь (1 -1,5 % от массы металла), полностью расплавляют металл и порциями засыпают железную руду и известь. В период кипения для полного удаления фосфора из металла несколько раз скачивают шлак. В это время при высокой температуре и большем количестве извести фосфор связывается в фосфат извести
|
|
4CaO P2O5.
После того как соединение углерода в металле достигает нижнего предела для заданной марки, а содержание фосфора снижается до 0.015 %, шлак опять удаляют и дают ванне «прокипеть» 25 мин, без присадки руды. После этого начинают восстановительный период плавки. В печь загружают смесь извести, плавикового шпата и мелкого кокса для образования восстановительного шлака. Имеющаяся в металле закись железа и марганца при этом начинает переходить в шлак и восстанавливаться имеющимся в шлаке углеродом кокса. После побеления шлака в него вводят еще более сильные восстановители – молотый ферросилиций или алюминий. Активное раскисление шлака приводит к диффузионному раскислению металла, непрерывно отдающему растворенный в нем кислород в восстановительный шлак.
Высокая температура, низкое содержание в шлаке закиси железа и высокое содержание извести способствуют в дуговой электропечи более полному удалению серы из металла в виде CaS:
Fe + S + CaO = CaS + FeO .
Продолжительность выплавки стали в дуговой печи составляет 3-6 часов в зависимости от мощности, выплавляемой марки стали, а также характера исходного сырья.
|
|
Иногда плавку ведут без окислительного периода, если переплавке подлежат отходы легированной стали и содержание фосфора в них меньше, чем допускается заданной маркой стали. Продолжительность такой плавки обычно меньше на 1-2 часа из-за отсутствия окислительного периода и сокращения восстановительного.
Углеродистые стали.
Предыдущая16171819202122232425262728293031Следующая
Согласно действующей по ГОСТ классификации, сталь по химическому составу делится на две группы: углеродистую и легированную.
Углеродистой сталью называется сплав железа с углеродом (содержание углерода до 2 %) с примесями кремния, серы и фосфора, причем главной составляющей, определяющей свойства стали, является углерод. Процентное содержание элементов в стали примерно следующее: Fe – до 99,0; С – 0,05 – 2,0; Si – 0,15 – 0,35; Mn – 0,3 – 0,8; S – до 0,06, Р – до 0,07.
Классификация углеродистых сталей. Углеродистые стали, классифицируют по содержанию углерода, назначению, качеству, степени раскисления и структуре в равновесном состоянии.
По содержанию углерода стали подразделяются на низкоуглеродистые (менее 0,3 % С), среднеуглеродистые (0,3 – 0,7 % С) и высокоуглеродистые (более 0,7 % С).
|
|
По назначению стали классифицируют на конструкционные и инструментальные. Конструкционные стали предназначены для изготовления строительных сооружений, деталей машин и приборов. К этим сталям относят цементуемые, улучшаемые, высокопрочные и рессорно-пружинные. Инструментальные стали, подразделяют на стали для режущего, измерительного инструмента, штампов холодного и горячего (до 200º С) деформирования.
По качеству стали классифицируют на обыкновенного качества, качественные, высококачественные. Под качеством стали понимается совокупность свойств, определяемых металлургическим процессом ее производства. Нормы содержания вредных примесей служат основными показателями для разделения сталей по качеству. Стали обыкновенного качества содержат до 0,06 % S и 0,07 %P, качественные - не более 0,04 % S и 0,035 % P, высококачественные – не более 0,025 % S и 0,025 %P.
Стали обыкновенного качества бывают только углеродистыми (до 0,5 %С), качественные и высококачественные – углеродистыми и легированными.
По степени раскисления и характеру затвердевания стали классифицируют на спокойные, полуспокойные и кипящие.
По структуре в равновесном состоянии стали делятся на: 1) доэвтектоидные, имеющие в структуре феррит и перлит; 2) эвтектоидные, структура которых состоит из перлита; 3) заэвтектоидные, имеющие в структуре перлит и цементит вторичный.
Влияние примесей стали на ее свойства.
Кремний – увеличивает прочность, износостойкость и придает упругие и антифрикционные качества. При содержании более 2 % снижает пластичность. Повышает прокаливаемость, но увеличивает температуру закалки, нормализации и отжига.
Марганец– повышает прокаливаемость и механические, в особенности упругие, свойства. При содержании более 1,5 % сообщает склонность к отпускной хрупкости. При содержании около 13 % и выше придает стали аустенитную структуру, противоударную стойкость, высокую износостойкость при сухом трении. При нагреве способствует росту зерна.
Сера является вредной примесью. Сера находится в стали главным образом в виде FeS. Это соединение сообщает, стали хрупкость при высоких температурах (красноломкость). Сера увеличивает истираемость стали, понижает сопротивление усталости и уменьшает коррозионную стойкость.
Увеличение хрупкости стали при повышенном содержании серы используется иногда для улучшения обрабатываемости на станках.
Фосфор является вредной примесью. Он образует с железом соединение Fe3P, которое растворяется в железе. Кристаллы этого химического соединения очень хрупки. Обычно они располагаются по границам зерен стали, резко ослабляя связь между ними, вследствие чего сталь приобретает очень высокую хрупкость в холодном состоянии (хладноломкость).
Дата добавления: 2019-02-26; просмотров: 298; Мы поможем в написании вашей работы! |
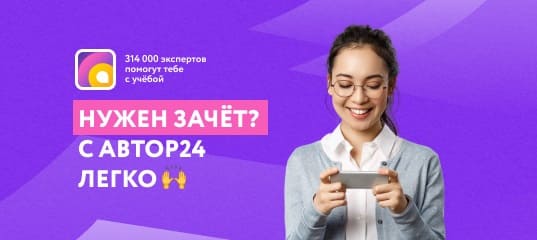
Мы поможем в написании ваших работ!