Поверхностная закалка при нагреве пламенем.
( газопламенный нагрев)
При этом способе закалки для нагрева наиболее часто используют ацетиленокислородное пламя с температурой 3100-3200º С.
При пламенной закалке применяют следующие способы (Рис.62.): одновременная закалка – стационарный и вращательный способы; непрерывная закалка – поступательный и комбинированный способы.
Рис.62.
Стационарный и вращательный способы относятся к закалке, выполняемой за две операции: сначала одновременно нагревается вся закаливаемая поверхность, а затем проводится охлаждение всей нагретой поверхности.
Поступательный и комбинированный способы относят к непрерывной закалке, при которой закаливаемая поверхность подвергается закалке непрерывным перемещением через зону нагрева и охлаждения. Толщина закаленного слоя обычно составляет 2-5 мм.
Поверхностная закалка при контактном нагреве.
Этот метод заключается в том, что ток из сети через понижающей трансформатор подводится к медным роликам , которые перекатываются по поверхности изделия и нагревают его. Изделие при этом служит как бы сопротивлением, включенным в цепь. Вслед за роликами движется душевое устройство; в качестве охлаждающей жидкости обычно применяется вода (Рис.63.).
Рис.63.
Поверхностная закалка при нагреве в электролите.
Этот способ заключается в том, что изделие погружают в ванну с электролитом (например, 5-процентным раствором Na2CO3), через который пропускают постоянный ток напряжением 220-380 В. ванна служит анодом, а деталь- катодом, вокруг которого образуется плотный слой водорода с очень высоким сопротивлением, вследствие чего водородная рубашка быстро нагревается до температуры 1800-2000º С и в течении нескольких секунд нагревает поверхность детали до температуры выше точки Ас3. нагретую деталь закаливают в том же электролите после выключения тока или сбрасывают в закалочный бак (Рис.64.).
|
|
Рис.64.
Стали с особыми свойствами.
Предыдущая24252627282930313233343536373839Следующая
Цементуемые легированные стали.
Целесообразно применять для крупных и тяжело нагруженных деталей и в том числе для деталей, у которых необходимо иметь высокую твердость поверхностного слоя и достаточно прочную вязкую сердцевину.
Хромистые стали (15Х, 20Х) применяют для деталей небольших и средних размеров, работающих на износ при повышенных нагрузках (поршневые пальцы, распределительные валы, толкатели клапанов и др.). после цементации и закалки в масле сердцевина деталей имеет структуру бейнита и заметно упрочняется ( В = 700-800 МПа).
Хромоникелевые стали (20ХН, 12ХН3А, 12Х2Н4А, 20Х2Н4А) применяют для крупных, ответственного назначения деталей, работающих на износ при высоких нагрузках (шестерни, шлицевые валы и др.). После цементации и закалки в масле сердцевина деталей имеет структуру низкоуглеродистого мартенсита или нижнего бейнита, что обеспечивает сочетание повышенной прочности сердцевины ( В = 800-1300 МПа) и вязкости.
|
|
Хромомарганцевые стали с титаном, содержат до 0,15 % титана (18ХГТ, 25ХГТ, 30ХГТ), являются заменителями хромоникелевых сталей. Эти стали имеют одинаковое количество легирующих примесей и отличаются только по содержанию углерода, что влияет на прокаливаемость. Поэтому сталь 18ХГТ применяют для деталей средних размеров (сечением до 20 мм), а сталь 30ХГТ – для крупных деталей (сечением до 100 мм). Предел прочности сердцевины деталей из стали 18ХГТ В = 1000 МПа; из стали 30ХГТ
В = 1500 МПа.
Хромоникелевые стали с молибденом (18Х2Н4МА) и с вольфрамом (18Х2Н4ВА) применяют для ответственных крупных и тяжело нагруженных деталей, работающих в условиях вибрации, скручивающих напряжений, при наличии концентрации напряжений (зубчатые колеса авиадвигателей, судовых редукторов и др.).
Дата добавления: 2019-02-26; просмотров: 317; Мы поможем в написании вашей работы! |
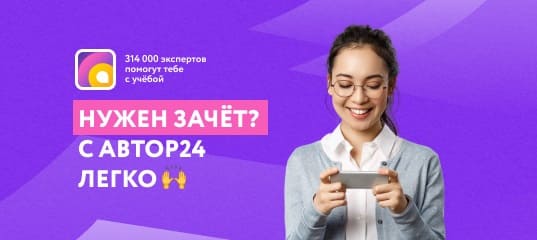
Мы поможем в написании ваших работ!