Коррозионно-стойкие (нержавеющие) стали.
Хромистые коррозионно-стойкие стали.Содержание хрома в стали должно быть не менее 12 % . При меньшем содержании хрома сталь не способна сопротивляться коррозии, так как ее электродный потенциал становится отрицательным. Широко применяют стали марок 12Х13, 40Х13, 12Х17, 08Х17Т.
Наибольшей коррозионной стойкость сталь 12Х13 (мартенситно-ферритного класса) обладает после закалки в масле с температуры 1000-1100º С и отпуска при температуре 700-750º С с последующей полировкой. Структура после термической обработки феррит и карбиды хрома. Твердость НВ 200-250. Эта сталь противостоит действию слабоагрессивных сред (воздуха, воды, пара).
Детали из стали 40Х13 (мартенситного класса) применяют после закалки в масле с температуры 1000-1050º С и отпуска при температуре 180-200º С, шлифования и полирования поверхности. После термической обработки сталь обладает высокой твердостью (HRC 52-55), структурой мартенсита; применяется для хирургических инструментов, пружин, предметов домашнего обихода и др.
Более коррозионностойкая сталь ферритного класса 12Х17, применяется (в отожженном состоянии) для химического и пищевого оборудования.
Хромоникелевые коррозионно-стойкие сталисодержат большое количество хрома и никеля, мало углерода и относятся к аустенитному классу. Кроме аустенита в этих сталях находятся карбиды хрома. (12Х18Н9, 12Х18Н9Т, 04Х18Н10)
Эти стали имеют большую коррозионную стойкость, чем хромистые и их широко применяют в химической , нефтяной и пищевой промышленности, в авиастроении, транспортном машиностроении, а также в строительстве.
|
|
Цветные металлы и сплавы.
К цветным металлам относятся все металлы, кроме железа и сплавов на его основе. Широкое применение цветных металлов и их сплавов обусловлено их ценными свойствами: высокими электро- и теплопроводностью, коррозионной стойкостью, хорошими пластичностью и вязкостью. Они хорошо поддаются штамповке, отливке и обработке резанием, что обеспечивает возможность изготовления деталей машин различными высокопроизводительными методами.
Медь (Cu) и ее сплавы.
Медь и ее сплавы находят широкое применение в электротехнике, электронике, приборостроении, литейном производстве, двигателестроении.
Читая медь - металл красного цвета. Ее кристаллическая решетка – гранецентрированный куб.
Температура плавления меди 1083º С, температура кипения 2360 º С, плотность 8,94 Мг/м3. Медь диамагнитна и не имеет полиморфизма. Механические свойства технической меди в отожженном состоянии: В = 25 кг/мм2,
= 45 %, НВ = 60 кг/мм2 (средние значения). Имея наименьшее (после серебра) удельное электрическое сопротивление (0,0178 мкОм
м), медь широко применяется в электротехнике в качестве проводников электрического тока. На воздухе медь окисляется – поверхность покрывается налетом углекислой меди. Промышленностью выпускается 11 марок меди с различным содержанием примесей. В электронике применяют бескислородную (б) медь марок М00б (99,99 % Cu) и М0б (99,97 % Cu), в электротехнике и металлургии М0 (99,95 % Cu), М1 (99,9 % Cu), М2 (99,7 % Cu) и др.
|
|
Обладая замечательными свойствами, медь в тоже время как конструкционный материал не удовлетворяет требованиям машиностроения, поэтому ее легируют , т.е. вводят в состав такие металлы как цинк, олово, алюминий и др., за счет чего улучшают ее механические и технологические свойства. По химическому составу медные сплавы подразделяют на латуни и бронзы, по технологическому назначению – на деформируемые, используемые для производства полуфабрикатов (проволоки, листа, полос, профиля), и литейные , применяемые для литья деталей.
Сплавы меди с цинком называют латунями, томпаками (до 10 % Zn) или полутомпаками (от 10 до 20 % Zn); все другие сплавы называют бронзами.
Латуни.
Латуни – сплавы меди с цинком, и другими компонентами. При содержании цинка менее 39 % латунь имеет структуру однофазного твердого раствора цинка в меди, называемую - латунью. Количество цинка свыше 39 % приводит к выделению из твердого раствора электронного соединения CuZn (
- фаза) и латуни имеют структуру
+
- латуни. При дальнейшем увеличении и цинка в сплаве прочность латуни уменьшается, а хрупкость увеличивается. Максимальную пластичность имеет латунь, содержащая около 32 % цинка (
= 55 %), а максимальную прочность – латунь, содержащая около 45 % цинка (
В =35 кг/мм2). Если латунь подвергается наклепу, механические свойства ее меняются: прочность на разрыв повышается (до 60 кг/мм2), относительное удлинение снижается (до 1 %).
|
|
Для снятия внутренних напряжений латунные изделия, полученные холодной обработкой давлением, необходимо подвергнуть отжигу при температуре 400º С.
По сравнению с медью латунь обладает большей прочностью, твердостью, коррозионной стойкостью и жидкотекучестью.
При практическом использовании следует иметь в виду, что повышенное процентное содержание меди в составе латуни улучшает ее пластичность, теплопроводность, электропроводность и коррозионную стойкость. Относительное повышение содержания цинка улучшает обрабатываемость латуни резанием, прирабатываемость, повышает износостойкость, снижает себестоимость латуни. Наличие в латуни олова, марганца, кремния, железа повышает ее прочность и способствует улучшению антикоррозионных свойств.
|
|
Деформируемые латуниобозначают (по ГОСТ 15527-70) буквой Л и цифрой, указывающей массовое содержание меди в сплаве в процентах (Л96, Л63). Если латунь легирована наряду с цинком другими элементами, то после буквы Л ставят обозначение этих элементов: С – свинец, О – олово, Ж – железо, А – алюминий, К – кремний, Мц – марганец, Н – никель. Числа после букв показывают массовое содержание меди и последующих (согласно буквам) легирующих элементов, кроме цинка (ЛАН59-3-2 содержит ~59 % Cu, 3 % Al, 2 % Ni, Zn – остальное).
Литейные латунииспользуют для фасонного литья. Маркировка литейных латуней (по ГОСТ 17711-93) начинается с буквы Л. После буквенного обозначения основного легирующего элемента (цинк) и каждого последующего ставятся цифра, указывающая его усредненное содержание в сплаве. Например, латунь ЛЦ23А6Ж3Мц2 содержит 23 % Zn, 6 % Al, 3 % Fe и 2 % Mn.
Бронзы.
Бронзами называют сплавы на основе меди с оловом, алюминием, свинцом, кремнием и другими элементами. В зависимости от состава бронзы делятся на оловянные и безоловянные (специальные).
Деформируемые бронзы маркируют (по ГОСТ 5017-74, 18175-78) буквами Бр; затем буквами последовательно указывают легирующие элементы и в конце их содержание в сплаве. Например, БрОФ6,5-0,4 содержит 6,5 % Sn и 0,4 % P, Cu – остальное. Обозначение элементов в бронзах то же, что и при маркировке латуней. Кроме того, фосфор обозначают буквой Ф, цинк – Ц, хром – Х, бериллий – Б, цирконий – Цр. Маркировка литейных бронз (по ГОСТ 613-79, 493-79) начинается также с букв Бр, а дальше производиться аналогично обозначению литейных латуней. Например, БрО3Ц12С5 содержит 3 % Sn, 12 % Zn и 5 % Pb.
Оловянные бронзы по структуре бывают однофазными ( - твердый раствор олова в меди) и двухфазными, состоящими из
- и
(Cu31Sn8)-фаз. Обычно
- фаза выделяется при содержании олова, больше 7-9 %. Она повышает твердость и хрупкость бронз.
Деформируемые оловянные бронзы (БрОФ6,5-0,4, БрОЦ4-3, БрОЦС4-4-2,5) имеют однофазную структуру ( - твердый раствор), поскольку содержат до 7 % Sn. Деформируемые оловянные бронзы изготавливают в виде листа, прутков, проволоки, трубок, ленты и др.- главным образом штамповкой и прессованием. По сравнению с литейными деформируемые бронзы характеризуются более высокой прочностью, вязкостью, пластичностью (в отожженном состоянии) и сопротивлением усталости.
Литейные оловянные бронзы (БрО3Ц12С5, БрО3Ц7С5Н1, БрО5Ц5С5, БрО5С25, БрО10Ф1) имеют двухфазную структуру ( и
).
Оловянные бронзы характеризуются достаточной прочностью, высокими антифрикционными качествами, коррозионной стойкостью, хорошей теплопроводностью. Повышение содержания олова в оловянных бронзах увеличивает их прочность и твердость, но уменьшает пластичность и ударную вязкость.
В качестве легирующих добавок в оловянные бронзы вводят цинк, свинец, никель, фосфор. Цинк и никель улучшают механические свойства бронзы, причем никель способствует измельчению зерна и улучшению структуры сплава; свинец и фосфор улучшают антифрикционные свойства и, кроме того, обрабатываемость резанием (фосфор) и износостойкость (свинец).
Специальные бронзы (не содержащие олова) обладают высокими механическими свойствами, отличаются высокой пластичность, коррозионной стойкостью и хорошими технологическими свойствами, в связи, с чем не только полностью заменяют оловянные бронзы, но и в ряде случаев превосходят их.
К специальным относятся бронзы: марганцовистые, алюминиевые, свинцовистые, кремниевые, бериллиевые и др.
Алюминиевые бронзы могут быть как двойными (БрА5), так и дополнительно легированными никелем, марганцем, железом и др. содержащие до 4-5 % Al бронзы характеризуются высокой пластичностью. При ускоренном охлаждении сплавов с 6-7 % Al в структуре наряду с - твердым раствором алюминия в меди появляется твердая, хрупкая
-фаза (Cu32Al19). Поэтому двухфазные сплавы обладают высокой прочностью, но пониженной пластичностью по сравнению с однофазными. Никель и железо повышают механические свойства бронз и их износостойкость. Алюминиевые бронзы хорошо пластически деформируются как в холодном , так и горячем состоянии, коррозионностойки, обладают высокими механическими свойствами.
Кремнистые бронзы (БрКМц3-1) характеризуются хорошей прочность и пластичностью. Они немагнитны, морозостойки. Никель и марганец повышают механические и коррозионные свойства кремнистых бронз. Сплавы свариваются, подвергаются пайке.
Бериллиевые бронзы обладают высокими механическими свойствами, стойкостью против коррозии и удовлетворительной тепло- и электропроводностью, хорошо свариваются.
Хромовые бронзы (БрХ0,5) обладают высокими механическими свойствами, хорошей электро- и теплопроводностью.
Свинцовистые бронзы имеют высокие антифрикционные свойства и применяются для высоконагруженных подшипников с большим удельным давлением, заменяя не только оловянную бронзу, но и дорогой высокооловянистый баббит, применяемый для вкладышей подшипников.
Циркониевые бронзы сочетают в себе высокую тепло- и электропроводность, близкую к меди, и жаропрочность.
Марганцовистые бронзы имеют сравнительно невысокие механические свойства, но обладают высокой сопротивляемостью коррозии и высокой пластичностью, а также сохраняют механические свойства при повышенных температурах.
Области применения меди и ее сплавов.
Чистая медь широко используется в электротехнике и различного вида теплообменниках. Из высокотехнологичных латуней получают изделия глубокой вытяжки (радиаторные и конденсаторные трубки, гибкие шланги). Латуни, содержащие свинец, используют при работе в условиях трения (в часовом производстве, в типографских машинах).
Оловянные бронзы применяют для литья художественных изделий. При дополнительном легировании фосфором их используют для изготовления деталей, работающих на трение в коррозионной среде: подпятники, подшипники, уплотняющие втулки, пояски поршневых колец, клапаны. Алюминиевые бронзы, прежде всего, используют в качестве заменителей оловянных. Высокопрочные алюминиевые бронзы идут на изготовление шестерен, втулок, подшипников, пружин, деталей электрооборудования. Из бериллиевой бронзы делают детали точного приборостроения, упругие элементы электронных приборов и устройств, мембраны. Для менее ответственных деталей используют кремнистые бронзы. Хромовые и циркониевые бронзы применяют в двигателестроении.
Магний (Mg) и его сплавы.
Магний открыт в XIX веке. Он широко распространен в природе, но в свободном виде не встречается. Мощные скопления образуют карбонаты магния – магнезит и доломит. Магний – пластичный металл серебристо-белого цвета. Это один из наиболее легких цветных металлов, его плотность составляет 1,74 Мг/м3. Температура плавления магния 651º С. Магний имеет компактную гексагональную кристаллическую решетку. Магний является химически активным металлом: образующаяся на воздухе оксидная пленка MgO в силу более высокой плотности, чем у самого магния, растрескивается и не обладает защитными свойствами; магний в виде порошка, пыли или стружки легко воспламеняется; при контакте расплавленного или горячего магния с водой происходит взрыв.
В промышленности магний используется в виде сплавов с алюминием, марганцем, цинком и другими элементами. Все магниевые сплавы хорошо обрабатываются резанием и имеют сравнительно высокую прочность. Они удовлетворительно свариваются аргонодуговой и контактной сваркой. Основными легирующими элементами в магниевых сплавах являются марганец, алюминий и цинк. Марганец повышает коррозионную стойкость и свариваемость сплавов магния. Алюминий и цинк оказывают большое влияние на прочность и пластичность магниевых сплавов: максимальное значение механических характеристик достигается при введении в сплав6-7 % алюминия или 4-6 % цинка. Цирконий (Zr), титан(Ti), щелочноземельные (Са – кальций) и редкоземельные (La-лантан, Ce-церий, Nd-неодим) металлы и торий (Th) измельчают зерно, раскисляют сплав, повышают его жаропрочность.
По технологии изготовления изделий магниевые сплавы разделяют на литейные (маркировка «МЛ») и деформируемые («МА»).
Литейные сплавы обладают следующими механическими свойствами: В = 115 МПа,
= 8 %, 30 НВ (кгс/мм2). В литых магниевых сплавах повышения механических свойств добиваются измельчением зерна посредствам перегрева расплава или его модифицирования добавками мела или магнезита. При этом в расплаве образуются твердые частицы, становящиеся центрами кристаллизации. Для предотвращения возгорания магниевых сплавов их плавку ведут в железных тиглях под слоем флюса, а разливку - в парах сернистого газа, образующегося при введении серы в струю металла.
Деформируемые сплавы. Деформированный (прессованный) магний обладает более высоким комплексом механических свойств, чем литой: В = 200 МПа,
= 11,5 %, 40 НВ (кгс/мм2). Деформируемые сплавы производят в виде поковок, штамповых заготовок, горячекатаных полос, прутков и профилей.
Повышение механических свойств магниевых сплавов (отливок) достигают применением термической обработки: закалки и последующего искусственного старения. При этом отливки нагревают до температуры 380-415º С, длительно выдерживают при этой температуре (10-16 ч), затем охлаждают на воздухе. Старение производят при температуре 175º С на протяжении 15-16 ч. С этой же целью применяют также модифицирование сплавов хлорным железом и углесодержащими веществами. Для защиты от коррозии изделия из магниевых сплавов подвергают оксидированию (воронению), а также покрытию лакокрасочными материалами.
Применение магниевых сплавов. Из сплавов магния изготавливают корпуса ракет, насосов, приборов, топливные и кислородные баки, рамы двигателя. Сплавы МЛ5 и МЛ6 (цифра показывает порядковый номер сплава) используют для литья тормозных барабанов, штурвалов, коробок передач, МЛ10 – деталей приборов высокой герметичности. Деформируемые сплавы МА1 применяют для изготовления арматуры, бензо- и маслосистем, а также сварных деталей, МА14 – для высоконагруженных деталей.
Алюминий и его сплавы.( Al )
Алюминий – легкий металл серебристо-белого цвета с голубоватым оттенком. Алюминий отличает очень низкая плотность – 2, 72 Мг/м3, высокие тепло- и электропроводность, хорошая коррозионная стойкость во многих средах за счет образования на поверхности металла плотной оксидной пленки Al2O4. температура плавления 658,7º С, температура кипения 2500º С. Алюминий имеет кристаллическую решетку гранецентрированного куба (ГЦК). Алюминий высокопластичен и легко обрабатывается давлением, однако при обработке резанием возникают осложнения, одной из причин которого является налипание металла на инструмент. Алюминий хорошо сваривается, имеет большую литейную усадку – 1,8 %.
Основные легирующие элементы в алюминиевых сплавах.Cu, Zn, Mg, Fe, Mn - элементы, формирующие упрочняющие зоны и фазы. Марганец одновременно повышает коррозионную стойкость. Кремний является основным легирующим элементом в ряде литейных алюминиевых сплавов (силуминов), поскольку он участвует в образовании эвтектики.
Ni, Ti, Cr, Fe повышают жаропрочность сплавов, затормаживая процессы диффузии и образуя стабильные сложнолегированные упрочняющие фазы. Литий в сплавах способствует возрастанию их модуля упругости. Вместе с тем магний и марганец снижают тепло- и электропроводность алюминия, а железо - его коррозионную стойкость.
Маркировка алюминиевых сплавов. В настоящее время одновременно «существуют» две маркировки сплавов: буквенно-цифровая (Таблица.5.) и цифровая (Рис.65.)
Рис.65.
Таблица.5.Буквенно-цифровая маркировка алюминиевых сплавов.
Принцип классификации | Название сплава | обозначение |
По химическому составу | - | AMr, AМц |
По названию сплава | Дуралюмин | Д1, Д6 |
По технологическому назначению | Ковочный | АК6, АК8 |
По свойствам | Высокопрочный | В95, В96 |
По методу получения полуфабрикатов и изделий | спеченный литейный | САП, САС АЛ2 |
По виду полуфабрикатов | Проволочный | Амr5П |
Таблица.6.Классификация алюминиевых сплавов.
Технология получения и обработки | Основные характеристики группы сплавов | Основные химические элементы и компоненты сплава | Примеры сплавов |
Деформируемые | Коррозионностойкие, повышенной пластичности | Al-Mn Al-Mg Al-Mg-Si | АМц АМ6 АВ, АД31, АД33 |
Пластичные при комнатной температуре | Al-Cu-Mg | Д18, В65 | |
Среднепрочные | Al-Cu-Mg | Д1, Д16 | |
Высокопрочные | Al-Zn-Mg-Cu | В95, В96Ц1 | |
Малой плотности, высокомодульные | Al-Mg-Li-Zr | ||
Ковочные, пластичные при повышенной температуре | Al-Mg-Si-Cu | АК6, АК8 | |
Жаропрочные | Al-Cu-Mg-Fe-Ni Al-Cu-Mn | АК4-1 Д20, Д21 | |
Спеченные | Жаропрочные | Al-Al2O3 Al-Cu-Mg-Al2O3 Al-Cr-Zr | САП-1, САП-2 СПАК-4 |
Высокомодульные с пониженной плотность | Al-Mg-Li-Zr | ||
Сплавы с низким коэффициентом линейного расширения | Al-Si-Ni Al-Si-Fe | САС1-50 САС-2 | |
Высокопрочные | Al-Zn-Mg-Cu | ПВ90 | |
Литейные | Герметичные | Al-Si Al-Si-Mg Al-Si-Cu-Mg | АЛ2, АЛ4, АЛ9 АЛ34 АЛ4М, АЛ32 |
Высокопрочные и жаропрочные | Al-Cu-Mn Al-Cu-Mn-Ni Al-Si-Cu-Mg | АЛ19 АЛ33 АЛ3,АЛ5 | |
Коррозионностойкие | AL-Mg Al-Mg-Zn | АЛ8, АЛ27 АЛ24 | |
Композиционные | Волокнистые: армированные борным волокном (Б.В.) | АД1-Б.В. АД33-Б.В. | ВКА-1 ВКА-2 |
Сплавы, армированные стальной проволокой | Матрица: АД1, АВ; Проволока 18Х15Н5АМ3 | КАС-1, КАС-1А |
Алюминиевые сплавы подразделяются на деформируемые и литейные, также их разделяют по способности упрочняться термической обработкой на упрочняемые (закалка с 435-545º С, естественное старение при 20º С или искусственное – при 75-225º С, 3-48 ч)и не упрочняемые ей.
Дата добавления: 2019-02-26; просмотров: 294; Мы поможем в написании вашей работы! |
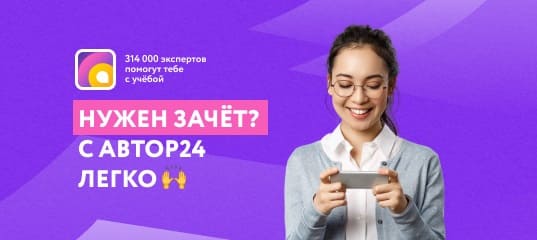
Мы поможем в написании ваших работ!