Выбор заготовки и метода ее получения
Выбор заготовки оказывает непосредственное влияние на возможность рационального построения технологического процесса изготовления как отдельных деталей, так и машины в целом, способствует снижению удельной металлоемкости и уменьшению отходов. Исходя из необходимости максимального приближения формы и размеров заготовки к параметрам готовой детали, следует применять прогрессивные методы и способы получения заготовок, такие как литье по выплавляемым моделям, литье в оболочковые формы, литье под давлением, штамповка в закрытых штампах, поэлементная штамповка, периодический прокат и др.
Оптимальный вариант при выборе заготовки для изготовления конкретной детали определяется сравнительным технико-экономи-ческим анализом. Чем больше заготовка приближена к форме и размерам готовой детали, тем дороже обходится заготовка. Такие заготовки экономически выгодны только в крупносерийном и массовом производстве.
В крупносерийном и массовом производстве, для снижения доли механообработки и повышения производительности, применяют специальное оборудование – деталепрокатные станки. Этот тип оборудования получает распространение в последние годы для снижения удельного веса механообработки и замены ее, например, способами холодного давления (прокатка валов, зубчатых колес, втулок, сверл).
Методы порошковой металлургии позволяют в ряде случаев исключить механическую обработку или выполнять ее в малом объеме. Для реализации этого метода необходимо специальное производство.
|
|
В качестве заготовок для деталей в мелкосерийном производстве обычно применяется недорогой полуфабрикат – прокат: круг, пруток, труба, лист, уголок, швеллер. В случае если диаметр круга недостаточен для получения детали, то применяют поковки. Если материал круга позволяет выполнять ковку, то можно отрезать заготовку от круга, а затем подвергнуть ковке.
Иногда в чертеже заранее оговаривается способ получения заготовки – литье. В этом случае заготовку обычно отливают. Но при несложной форме детали возможен другой вариант – изготовление детали механообработкой из сортового проката. При этом необходимо получить согласие заказчика на замену способа получения заготовки.
Если размеры или форма проката и поковки не позволяют получить деталь, то применяют литье в землю, литье по выплавляемым моделям или другие, не требующие дорогостоящего оборудования.
Довольно часто в мелкосерийном производстве в качестве заготовки используется сварная конструкция, позволяющая экономить дорогостоящий материал.
Прокат, полученный с завода-изготовителя, имеет большие габариты. Установить такие заготовки на обычные станки не представляется возможным.
|
|
Максимальные размеры заготовки, устанавливаемой на станке, зависят от размера детали, величины изготавливаемой партии деталей, размеров рабочего пространства конкретного станка (табл. 3.6).
Разрезка крупногабаритного проката производится на специальном оборудовании. Разрезка прутка, круга, трубы, уголка, швеллера с максимальным размером в сечении 80…100 мм производится на механических ножовках, размером от 100 мм – на круглопильных станках. Разрезка листа толщиной до 10…15 мм производится на гильотинах, толщиной свыше 10…15 мм – на специальном оборудовании (иногда заготовки разрезают газовой резкой, на продольно-фрезерных станках дисковыми фрезами). Для разрезки или отрезки заготовок вводят специальные операции – заготовительные.
Таблица 3.6
Размеры заготовок для металлорежущих станков
Тип оборудования | Прокат | Размеры заготовки максимальные, мм | ||
Токарный станок: – пруток – единичная заготовка | Круг, пруток, труба Круг, пруток, труба | Ød x l ØD x M | ||
Фрезерный станок | Лист, швеллер, уголок, круг, пруток, труба | L x M; ØD x M | ||
Сверлильный станок | Лист, швеллер, уголок, круг, пруток, труба | L x M; ØD x M | ||
Шлифовальный станок: – круглошлифовальный – бесцентрово-шлифовальн – внутришлифовальный – плоскошлифовальный | Круг, пруток, труба Круг, пруток, труба Труба Лист, швеллер, круг | ØD x M Ød x l, ØD x M ØD x M L x M; ØD x M | ||
Токарные автоматы | пруток | Ød x l | ||
Примечание: размеры Ød x l зависят от диаметра внутреннего отверстия шпинделя и длины шпинделя (подающей трубы для автоматов); размеры ØD x M и L x M определяются размерами рабочей зоны конкретного станка
|
Точность отрезки заготовок зависит от применяемого способа и оборудования (табл. 3.7).
Таблица 3.7
Точность резки по длине заготовки различными способами
Способ резки | Величина отклонения по длине, мм |
Горячая резка на пилах | ± 0,5…± 1,5 |
Резка на механических ножовках | (± 1,0…± 1,5) / 100 мм диаметра |
Резка дисковыми пилами | (± 0,75…± 1,0) / 100 мм диаметра |
Резка на ножницах | ± 1,0…± 5,0 |
Газоплазменная резка | ± 1,0…± 3,0 |
Газовая (кислородная) резка: – ручная – машинная | ± 1,0…± 5,0 ± 0,5…± 2,5 |
Электроискровая резка | ± 0,1…± 0,25 |
Анодно-механическая резка | ± 0,1…± 0,5 |
Расчет припусков
|
|
При проектировании технологических процессов механической обработки заготовок необходимо установить оптимальные припуски, которые обеспечили бы заданную точность и качество обрабатываемых поверхностей.
Припуском называется слой материала, удаляемый с поверхности заготовки в целях достижения заданных свойств обрабатываемой поверхности.
Припуски могут быть операционные и промежуточные.
Припуск, удаляемый при выполнении одной технологической операции, называется операционным.
Промежуточный припуск – это припуск, удаляемый при выполнении одного технологического перехода.
Общий припуск, который удаляют в процессе механической обработки заданной поверхности для получения чертежных размеров, определяется разностью размеров исходной заготовки и детали.
На припуск устанавливается допуск, который является разностью между наибольшим и наименьшим значениями припуска.
При определении минимального припуска необходимо учитывать, что при обработке заготовки надо снять не только слой заготовки, имеющий геометрические отклонения 1 (рис. 3.3, а). В ряде случаев необходимо учесть способ получения заготовки и связанный с этим дополнительный дефектный слой. При получении заготовки методом литья некоторые металлы дают прочную литейную корку, которую надо полностью удалить (рис. 3.3, б). При получении заготовок спеканием (например, материал САС) дефектный слой распространяется на значительную глубину (до 7 мм на сторону на диаметре 100 мм), который также необходимо удалять (рис. 3.3, в).
Имеется два основных метода определения припусков на механическую обработку: опытно-статистический и расчетно-аналитический. В первом случае припуск устанавливается по стандартам и таблицам, составленным на основе обобщения и систематизации производственных данных передовых предприятий. Метод применяется в основном при изготовлении единичных деталей.
В расчетно-аналитическом методе минимальный припуск рассчитывают на основе анализа факторов, влияющих на формирование припуска, с использованием нормативных материалов. Припуски на обработку определяют таким образом, чтобы на выполняемом технологическом переходе были устранены погрешности изготовления детали, которые остались на предшествующем переходе. При расчетах учитывается величина А срезаемого дефектного слоя, состоящая из величины высоты микронеровностей Rzi-1, которая характеризует шероховатость поверхности и глубину дефектного слоя hi-1 (рис. 3.4).
Поверхностный слой Б, имеющий измененную структуру материала (наклепанный слой), обычно не удаляют из-за его повышенной износостойкости. Этот слой способствует и получению меньшей шероховатости. Ниже слоя Б расположен слой В, имеющий исходную структуру материала.
Качество обработанной поверхности заготовки характеризуется параметром шероховатости, состоянием и глубиной поверхностного слоя. При расчетах припуска исходят из того, что шероховатость поверхности и дефекты поверхностного слоя, сформированные на предшествующем переходе (i–1), должны быть удалены на выполняемом переходе. При этом надо учитывать глубину не всего поверхностного слоя, а лишь его дефектной части. Необходимо стремиться оставить наклепанный поверхностный слой – более износостойкий, чем нижележащие слои исходной структуры, к тому же способствующий получению меньшей шероховатости поверхности при ее обработке в зоне этого слоя.
При расчете припусков отклонения формы поверхности отдельно не учитывают. Принимают, что эти отклонения (овальность, бочкообразность, седлообразность, конусность, вогнутость, выпуклость и др.) не должны превышать допуска на размер и, как правило, должны составлять некоторую ее часть.
Пространственные отклонения ΔΣ (кривизна и коробление заготовки, эксцентричность отверстия относительно наружной поверхности, увод оси отверстия, отклонения от параллельности, перпендикулярности, плоскостности и т.п.) следует учитывать отдельно при расчете припусков на обработку.
Перечисленные отклонения проявляются в результате предшествующей обработки. На выполняемом переходе может возникнуть погрешность установки εi.
С учетом изложенного можно определить в общем виде минимальный промежуточный припуск на выполняемом переходе по формулам [35]:
· для асимметричных припусков при последовательной обработке плоских поверхностей
zi min = (Rz i-1 + hi-1) + | ΔΣ i-1 + εi |;
· для симметричных припусков при обработке наружных и внутренних поверхностей вращения
2zi min = 2[(Rz i-1 + hi-1) + | ΔΣ i-1 + εi |].
Здесь Rz i-1 – высота неровностей на предшествующем переходе; hi-1 – глубина дефектного поверхностного слоя на предшествующем переходе (обезуглероженный или отбеленный слой); ΔΣ i-1 – суммарные отклонения расположения поверхности (отклонения от параллельности, перпендикулярности, соосности, симметричности, пересечения осей, позиционное) и в некоторых случаях отклонения формы поверхности (отклонения от плоскостности, прямолинейности на предшествующем переходе); εi – погрешность установки заготовки на выполняемом переходе.
Нормативные материалы для значений Rz i-1, hi-1, ΔΣ i-1, εi даны в справочнике [50]. Выборочно значения Rz i-1, hi-1, εi представлены в табл. 3.8. Расчет минимальных промежуточных припусков на обработку производят для определения расчетных размеров обрабатываемой поверхности по всем технологическим переходам от готовой детали до исходной заготовки.
На расчетных схемах указывается черновая, чистовая и отделочная обработка с указанием допусков на обрабатываемые поверхности (рис. 3.5).
Таблица 3.8
Значения Rz i-1 (Hmax) hi-1 (Tmax), εi (δп),
соответствующие среднеэкономической точности
Вид обраба-тываемой поверхности |
Стадии обработки | Rz i-1 | hi-1 | εi | ||
мкм | ||||||
Наружные цилиндри-ческие, конические и фасонные поверхности вращения | Притирка Тонкое точение Шлифование Чистовое точение Черновое точение Холодная обработка давлением Прокатка Штамповка горячая | 0,05–0,5 1–5 1,7–15 5–45 15–100 25–100
100–225 100–225 | 3–5 15–20 15–25 30–40 40–60 80–100 300 500 | 4–11 8–25 10–40 50–200 100–400 70–340
500–1600 400–1000 | ||
Отверстия цилиндри-ческие | Притирка Тонкое точение Дорнование Протягивание Шлифование Чистовое растачивание Чистовое развертывание Черновое растачивание Рассверливание Сверление по кондуктору Сверление без кондуктора Штамповка горячая | 0,05–0,5 1–5 1–5 1,7–8,5 1,7–15 3–25 25–100 25–225 25–225 45–225 45–225 100–225 | 3–5 15–20 20–25 10–20 20–30 30–40 25–30 30–50 40–60 50–60 50–60 500 | 4–13 15–25 12–18 18–30 15–35 100–200 40–150 200–350 140–300 70–300 120–350 600–1000 | ||
Плоскости | Притирка Шлифование Чистовое фрезерование Черновое фрезерование Строгание Прокатка Штамповка горячая | 0,05–0,5 1,7–15 5–45 15–100 15–100 100–225 100–225 | 3–5 15–25 25–50 40–60 40–50 300 500 | 4–15 10–50 25–100 70–200 80–200 500–1600 300–1000 | ||
Дата добавления: 2019-02-12; просмотров: 445; Мы поможем в написании вашей работы! |
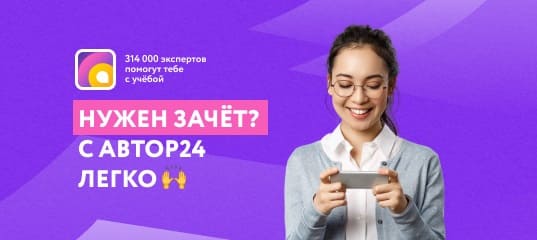
Мы поможем в написании ваших работ!