Оборудование и технологическая оснастка
Наиболее часто в мелкосерийном производстве применяются следующие типы металлорежущих станков: токарные, фрезерные, сверлильные, шлифовальные станки с ручным управлением, автоматы фасонно-продольного точения, токарно-револьверные автоматы, станки с ЧПУ.
На токарных станках выполняют следующие виды работ: подрезка торца, точение цилиндрических и конических поверхностей; точение канавок на торце детали и на цилиндре; растачивание конических и цилиндрических поверхностей; центрование, сверление, зенкерование, развертывание отверстий; нарезание наружной резьбы резцом и плашкой; нарезание внутренней резьбы резцом и метчиком; накатывание рифлений. Применяется стандартный режущий инструмент [49]: различные типы резцов, сверла, зенкеры, развертки, метчики, плашки.
На токарных автоматах фасонно-продольного точения обрабатывают детали с наружным диаметром до 16 мм. Получают из прутка цилиндрические и конические наружные поверхности, центральное гладкое и резьбовое отверстие. Режущий инструмент – резцы различных типов, сверла, метчики.
На токарно-револьверных автоматах из прутка круглого (диаметром до 40 мм) или шестигранного сечения получают наружные цилиндрические поверхности резцами (в том числе фасонными), центральное отверстие – сверлами.
На фрезерных станках выполняют следующие виды работ: фрезерование плоскостей, уступов, колодцев, пазов. Обработка производится фрезами различных типов.
|
|
На сверлильных станках выполняют следующие виды работ: сверление, зенкерование, развертывание, нарезание резьбы метчиком. Режущий инструмент – сверла, зенкеры, развертки, метчики.
На круглошлифовальных станках шлифуют наружные цилиндрические и конические поверхности, и наружные цилиндрические поверхности с подшлифовкой торца различными типами шлифовальных кругов для обработки наружных поверхностей.
На внутришлифовальных станках производится шлифование внутренних поверхностей или внутренних поверхностей с подшлифовкой торца шлифовальными кругами для обработки отверстий (диаметр круга меньше диаметра отверстия).
На плоскошлифовальных станках выполняют шлифование плоских наружных поверхностей шлифовальными кругами для обработки плоских поверхностей.
Выбор оборудования для заданной операции производится с учетом габаритов обрабатываемой заготовки и достигаемой точности.
Необходимые данные по отечественному оборудованию классов точности Н (нормальной точности) и П (повышенной точности) можно найти в справочнике технолога-машиностроителя [51]. Характеристики оборудования других классов точности определяют по табл. 3.9.
|
|
Таблица 3.9
Характеристика металлорежущего оборудования [59]
Класс точности станков | Группа | Погрешность, % | Трудоемкость, % |
нормальной повышенной высокой особо высокой особоточные станки | Н П В К С | 100 60 40 25 16 | 100 140 200 280 450 |
При выборе оборудования для конкретного вида обработки необходимо представлять возможности оборудования различной степени точности при получении допусков взаимного расположения поверхностей, эксцентриситета, торцового биения.
Торцовое биение определяется относительно осей цилиндрических поверхностей, обработанных за одну установку с торцовой поверхностью на токарных и координатно-расточных станках (табл. 3.10)
Таблица 3.10
Торцовое биение в зависимости от класса точности станка
Контроли-руемый параметр | Классы точности станков | ||||||
токарных | координатно-расточных | ||||||
П | В | А | С | В | А | С | |
Торцовое биение, мм | 0,008 и более | 0,005 … 0,008 | 0,003 … 0,005 | 0,002 … 0,003 | 0,006 и более | 0,004 … 0,006 | 0,003 … 0,004 |
Эксцентриситет цилиндрических поверхностей, обработанных за одну установку на токарных и координатно-расточных станках (табл. 3.11).
|
|
Эксцентриситет цилиндрических поверхностей, обработанных за одну установку на координатно-расточных станках (с разворотом универсального стола на 180°) на приведенной длине l = 100 мм (табл. 3.12).
Таблица 3.11
Эксцентриситет цилиндрических поверхностей
в зависимости от класса точности станка
Контроли-руемый параметр | Классы точности станков | ||||||
токарных | координатно-расточных | ||||||
П | В | А | С | В | А | С | |
Эксцентриситет, мм | 0,004 и более | 0,0025 … 0,004 | 0,0016 … 0,0025 | 0,001 … 0,0015 | 0,004 и более | 0,0025 … 0,004 | 0,0015 … 0,0025 |
Приведенная длина l равняется удвоенному расстоянию от торца одного из растачиваемых отверстий до оси вращения универсального стола. При разработке техпроцесса конкретной детали для правильного выбора координатно-расточного станка требуемого класса точности, кроме таблиц 3.9…3.11 технолог должен руководствоваться следующим: величина допустимого эксцентриситета, указанного в табл. 3.11,
состоит из 2-х слагаемых (табл. 3.13):
· постоянного слагаемого, не зависящего от величины расстояния от торца растачиваемого отверстия до оси вращения стола (оно является следствием всех погрешностей станка и стола, кроме погрешности установки угла поворота);
|
|
· переменного слагаемого, зависящего прямо пропорционально от величины расстояния от торца растачиваемого отверстия до оси вращения стола (оно является следствием погрешности установки угла поворота при развороте стола на 180°).
Таблица 3.12
Эксцентриситет цилиндрических поверхностей
с разворотом стола на 180° в зависимости от класса точности станка
Контролируемый параметр | Классы точности координатно-расточных станков | |||
В | А | С | ||
Эксцентриситет, мм (на 100 мм длины) | 0,015 и более | 0,010 … 0,015 | 0,006 … 0,010 |
Суммарный эксцентриситет определится как сумма постоянной и переменной составляющих:
εΣ = εпост + εпер .
Например, необходимо определить класс точности станка при расточке двух соосных отверстий с разворотом стола на 180°. Длина детали 70 мм, допустимый эксцентриситет по чертежу εдоп = 0,008 мм.
Так как ось поворота заготовки будет находиться в середине детали, то приведенная длина равна 70 мм (35 х 2).
Табл. 3.13
Составляющие эксцентриситета
Составляющая | Классы точности станков | ||
В | А | С | |
Постоянная Переменная | 0,010 0,005 | 0,007 0,003 | 0,004 0,002 |
Определим суммарную погрешность для станка класса точности А:
εΣ = εпост + εпер = 0,007 + 0,003 (70/100) = 0,009 мм.
Класс точности А не подходит, так как εΣ = 0,009 мм > εдоп .
Выбираем класс точности С:
εΣ = εпост + εпер = 0,004 + 0,002 (70/100) ≈ 0,006 мм. εΣ < εдоп .
Технологическая оснастка
По ГОСТ 31.0000.01–87 к технологической оснастке относят: приспособления к металлорежущим станкам; приспособления и инструмент сварочный, термический, для обработки давлением, литейный; вспомогательный к металлорежущим станкам, для измерения и контроля линейных и угловых величин; инструмент для обработки резанием и др.
Приспособления к металлорежущим станкам подразделяют на универсальные, специализированные и специальные. В единичном и мелкосерийном производстве рекомендуется применять универсальные приспособления. Они предназначены для использования при обработке большой номенклатуры различных заготовок. К ним относятся тиски, трех- и четырехкулачковые патроны, зажимные цанги, делительные головки, поворотные столы и др.
Применение приспособлений при обработке заготовок позволяет:
· производить установку заготовок на станках без выверки их положения;
· повышать производительность труда;
· расширять технологические возможности оборудования.
Применение приспособлений для установки заготовок устраняет
дорогостоящую и трудоемкую операцию разметки, исключает выверку обрабатываемой заготовки на станке, обеспечивает возможность автоматического получения размеров требуемой точности.
Повышение производительности труда обеспечивается применением высокопроизводительного оборудования и высокоэффективных приспособлений.
Приспособления, расширяющие технологические возможности станков, позволяют осуществить крепление инструмента, использование которого на данном станке не предусмотрено; дополнительные перемещения обрабатываемой заготовки и инструмента; перемещение инструмента относительно заготовки в требуемой последовательности. При этом возможно крепление заготовок и инструментов на не предназначенных для этих целей поверхностях станков; повышение точности положения и перемещения инструмента; становятся возможными виды обработки, для которых данный станок не предназначен. Например,
с помощью специальных приспособлений обработку шлифованием, протягиванием и фрезерованием можно производить на токарно-винторезном станке; растачивание, долбление – на фрезерном; обработку точных отверстий на сверлильных станках и др.
Приспособления подразделяют по следующим признакам [54]: целевому назначению, степени специализации и функциональному назначению элементов приспособлений.
По целевому назначению приспособления различают:
· для установки заготовок на станке;
· для крепления рабочих инструментов;
· сборочные приспособления;
· контрольные;
· транспортно-кантовательные для захвата, перемещений и перевертывания обрабатываемых заготовок.
По степени специализации приспособления делят на универсальные, специализированные и специальные.
По функциональному назначению элементы приспособления подразделяют на:
· установочные;
· зажимные;
· силовые приводы;
· элементы для определения положения
и направления инструментов;
· корпуса;
· вспомогательные механизмы
(делительные, фиксирующие и др.);
· вспомогательные и крепежные детали (рукоятки, сухари, шпонки и т.п.).
Совокупность всех систем приспособления представляет единый
комплекс технологической оснастки, применяемой для обработки заготовок во всех типах производства.
Для крепления инструмента применяются резцедержатели, оправки, переходные втулки.
Для измерений применяются стандартный измерительный инструмент и приборы: штангенциркули различных типов, штангенглубиномеры, микрометры, индикаторы часового типа.
При выборе измерительного инструмента учитывают погрешность измерения данным инструментом, пределы измерений и способ измерения (см. раздел «Контрольные операции»).
Дата добавления: 2019-02-12; просмотров: 243; Мы поможем в написании вашей работы! |
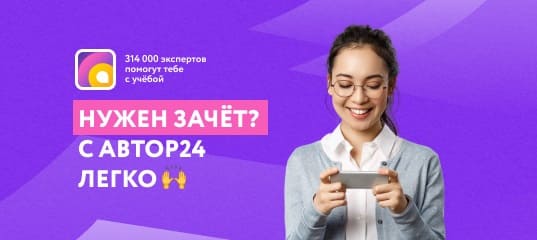
Мы поможем в написании ваших работ!