Well fluids and their characteristics
Some of the physical characteristics of well fluids handled by oil and gas separators are:
Crude oil is a complex mixture of hydrocarbons produced in liquid form. The API gravity of crude oil can range from 6 to 500 and viscosity from 5.0 to 90.000cp at average operating conditions. Color varies through shades of green, yellow, brown and black.
Condensate is a hydrocarbon that may exist in the producing formation either as a liquid or as a condensable vapor. Liquefaction of gaseous components of the condensate usually occurs with reduction of well-fluid temperature to surface operating conditions. Gravities of the condensed liquids may range from 50 to 1200 API and viscosities from 2.0 to 6.0cp at standard conditions. Color may be water- white, light yellow or light-blue.
Natural gas may be defined as a substance that has no shape or volume of its own. It will completely fill any container in which it is placed and will take the shape of the container. Hydrocarbon gas associated with crude oil is referred to as natural gas and may be found as “free” gas or as “solution” gas. Specific gravity of natural gas may vary from 0.55 to 0.90 and viscosity from 0.011 to 0.024cp at standard conditions.
Free gas is a hydrocarbon that exists in the gaseous phase at operating pressure and temperature. Free gas may refer to any gas at any pressure that is not in solution or mechanically held in the liquid hydrocarbon.
Solution gas is homogeneously contained in oil at a given pressure and temperature. A reduction in pressure and\or increase in temperature may cause the gas to be emitted from the oil, whereupon it assumes the characteristics of free gas.
Condensable vapors these hydrocarbons exist as vapor at certain pressures and temperatures and as liquid at other pressures and temperatures. In the vapor phase, they assume the general characteristics of a gas. In the vapor phase, condensable vapors vary in specific gravity from 0.55 to 4.91 and in viscosity from 0.006 to 0.011cp at standard conditions.
Waterproduced with crude oil and natural gas may be in the form of vapor or liquid. The liquid water may be free or emulsified. Free water reaches the surface separated from the liquid hydrocarbon. Emulsified water is dispersed as droplets in the liquid hydrocarbon.
Impurities and extraneous materials produced well fluids may contain such gaseous impurities as nitrogen, carbon dioxide, hydrogen sulfide and other gases that are not hydrocarbon in nature or origin. Well fluids may contain liquid or semiliquid impurities (water and paraffin). They may also contain solid impurities (drilling mud, sand, silt, salt).
|
|
Primary functions of oil and gas separators
Separation of oil from gas may begin as the fluid flows through the producing formation into the wellbore and may progressively increase through the tubing flowlines and surface handling equipment. Under certain conditions, the fluid may be completely separated into liquid and gas before it reaches the oil and gas separator. In such cases, the separator vessel affords only an “enlargement” to permit gas to ascend to one outlet and liquid to descend to another.
1. removal of oil from gas;
2. removal of gas from oil;
3. separation of water from oil
Oil and gas separation
Separators are the primary field treating units used to separate gas from liquid, gas from oil, oil from water and to break down emulsions. Separators may be classified in several ways:
(1) by their configuration- almost all separators are classified by configuration as either horizontal or vertical. Horizontal separators are generally used for high gas-oil ratios. They have a greater capacity and a greater gas\liquid interface which permits higher velocity fluids than vertical separators. They are also easier to transport and connect. Vertical separators are used on low to intermediate gas-oil ratio wells. They handle more sand and impurities and are easier to clean due to the small bottom area.
(2) by what they are designed to handle (high or low pressure);
(3) by the number of fluids separated.
The selection is based on the anticipated fluid and gas rates of flow, their specific gravities, temperature, pressure, required retention time and the amount and type of impurities carried.
How a separator operates
The specific operation of a separator will vary depending on its design. A typical separator operation is described below:
The mixture of produced enters the separator through the inlet where a swirling motion is created as the fluid is forced against an inlet diverter. The swirling motion facilitates the escape of gas. The liquids collect on the inside of the separator and the effects of gravity cause separation to occur, as the liquids migrate downward and accumulate at the bottom of the vessel. Additional separation occurs as liquids collect on the deflector cone, and gas and vapor rise upward through the primary mist extractor into the gas separation section of the vessel. The secondary mist extractor removes additional vapor from the gas as it passes out the gas outlet into the gas line. The remaining oil is then removed from the separator by way of the oil outlet.
|
|
Дата добавления: 2019-01-14; просмотров: 99; Мы поможем в написании вашей работы! |
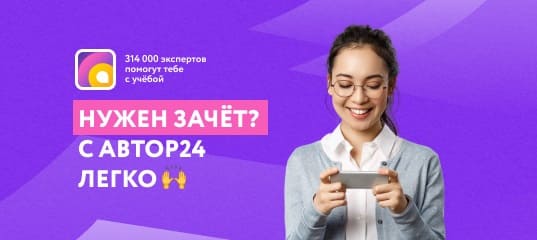
Мы поможем в написании ваших работ!