Oil and natural gas pipelines
Nbsp; History The oil industry began over five thousand years ago. In the Middle East, oil seeping up through the ground was used in waterproofing boats and baskets, in paints, lighting and even for medication. However, commercial petroleum production began in the United States in the mid 1800’s with the completion and operation of an oil well near Titusville, in Northwest Pennsylvania. Titusville is located in the area of Oil Creek. This well produced about 20 barrels of crude oil each day. Additional wells were drilled and shortly thereafter an oil refinery complex was near Pittsburgh. Getting the crude oil from the field to the refineries was a major problem and one that needed to be resolved quickly. Since the first oil was located adjacent to a waterway, Oil Creek; water transport was the most immediate solution. Boats of various types and sizes (steamers, passenger boats, towboats) were hired and used to transport the crude oil down Oil Creek to Oil City, PA. From there the oil was transferred to larger boats and transported down the Allegheny River to the refinery complex in Pittsburgh. Some “runs” could transport as much as 20.000 barrels downstream from the production area to the refinery. However, boating and related accidents resulted in the loss of large amounts of oil by spillage. Such losses had significant impacts on the environment as well as the economics of oil production. As a result, it was realized that moving oil by boats on inland waterways was too expensive and hazardous. Railroads were looked upon as the next solution to transporting oil from the field to the refineries. Around 1861, railroad tracks were laid to Titusville and other nearby Pennsylvania communities close to the Oil City oil production areas. From there the crude oil could now be transported to larger markets such as New York. The rail cars designed to transport the oil consisted of two large tanks mounted on a flatcar. These tanks were originally constructed of wood but were later fabricated from steel. Each tank held about 40 barrels of crude oil. To move the oil from the production area to the railheads in Titusville and other communities still required an initial trip by horse-drawn wagon. The wagons were loaded with from 1.800 to 2.500 pounds of crude oil contained in barrels. Up to 2.000 wagon trips were required daily to get the oil to the railheads and the cost, paid to the wagon drivers (teamsters) varied depending on the distance and road conditions. This method of transportation still involved many hazards, congestion and delays and high costs, as the wagons had to travel over inadequate roads and through unpredictable weather conditions. Those problems provided incentives to find safer and more economic methods of transporting the crude oil to the refineries. Pipelines were proposed as the solution. Early efforts to construct pipelines to transport crude oil were met with concerted and sometimes violent resistance by the teamsters. After all, if the oil was moved through pipelines fewer teamsters would be needed to drive the horse-drawn wagons that were used. Additionally, the viability of earl pipelines was challenged by the railroads. The railroads effectively established a transportation monopoly that controlled the shipment of oil and dictated prices to the oil producers and shippers. The railroads constructed their own pipelines but refused to allow privately owned pipelines to cross the railroad rights-of-ways. These difficulties were later overcome by legislative and judicial actions around 1875 that granted the power of eminent domain to common carrier pipelines. These actions led the way to the establishment of oil trunk line systems that could connect production areas in the field directly to the refineries. This led to more economical transportation of the oil by helping to assure predictable, consistent and cost-effective delivery. The first attempts to construct oil pipelines were made using wooden pipe with flow accomplished by gravity alone. In 1863 a pipeline was constructed from a Pennsylvania oil field to a nearby refinery over a distance of two and one-half miles. It was constructed of two-inch cast iron pipe and three pumps were used to force the oil over a 400-foot ridge. However, the pumps proved inadequate for the job and combined with excessive leakage from the pipe to cause the project to be abandoned. Around 1865, wrought iron pipe was employed to overcome the leakage problems encountered in cast iron pipe. Initially used to move petroleum distillates about three miles from a refinery at Clumer, PA, to the Allegheny River, wrought iron pipe was subsequently used to transport crude oil from a production area to a railroad at Miller Farm, PA. This line consisted of 32.000feet of two-inch pipe. The pipe was manufactured in 15-foot sections that were lap-welded together and pressure tested to 900 pounds per square inch (psi). Installed partially above ground and partially below ground, the pipeline made use of three pumps installed along the route and provided a throughout of about 81 barrels of crude oil per day. This line also had the distinction of having the beginnings of a flow data system – a telegraph line was used to relay data on the oil shipments. By 1867 the cost to transport a barrel of oil was down from $ 2.50 to about 50¢ as a result of competition brought on with the construction and operation of additional pipelines. Oil gathering and storage early oil production was accomplished by extracting the oil from the well and storing I temporarily in tanks. Teamsters were used to gather the oil from the well tanks and haul it to large dump tanks at the pipeline. In 1866 the Accommodation Pipeline Company constructed a two-inch line across the Pit ole production area, connecting the well tanks directly to the pipeline dump tank The cost for “gathering” the oil into the pipeline dump tank dropped from $1.00 to 25¢ per barrel. This method of gathering was quickly adopted by other established pipeline companies. To smooth out the up and down fluctuations between oil production and shipments, the early pipeline companies began constructing tanks to provide oil storage. The tanks were originally built from wood and had a capacity of about 1.200 barrels. Later the wooden tanks were replaced with tanks manufactured from wrought iron that were bigger and stronger and had a capacity of about 15.000 barrels. The companies had a combined storage capacity of about 1 million barrels by 1870.
|
|
|
|
Pipeline transport
An elevated section of the Alaska Pipeline.
Pipeline transport is a transportation of goods through a pipe. Most commonly, liquid and gases are sent, but pneumatic tubes that transport solid capsules using compressed air have also been used.
|
|
As for gases and liquids, any chemically stable substance can be sent through a pipeline. Therefore sewage, slurry, water, or even beer pipelines exist; but arguably the most important are those transporting oil and natural gas.
Oil and natural gas pipelines
There is some argument as to when the first real oil pipeline was constructed. Some say pipeline transport was pioneered by Vladimir Shukhov and the Branobel company in the late 19th century. Others say oil pipelines originated when the Oil Transport Association first constructed a 2-inch wrought iron pipeline over a 6-mile track from an oil field to Pennsylvania to a rail road station in Oil Creek, in the 1860s. No matter, piplines are generally the most economical way to transport large quantities of oil or natural gas over land. Compared to railroad, they have lower cost per unit and also higher capacity. Although pipelines can be built even under the sea, that process is both economically and technically very demanding, so the majority of oil at sea is transported by tanker ships.
Oil pipelines are made from steel or plastic tubes with inner diameter from 30 to 120 cm (about 12 to 47 inches). Where possible, they are built above the surface. However, in more developed, urban, environmentally sensitive or potentially dangerous areas they are buried underground at a typical depth of about 1.3 - 1.6 meters (about 3 feet). The oil is kept in motion by a system of pump stations built along the pipeline and usually flows at speed of about 1 to 6 m/s. Multi-product pipelines are used to transport two or more different products in sequence in the same pipeline. Usually in multi-product pipelines there is no physical separation between the different products. Some mixing of adjacent products occurs, producing interface. This interface is removed from the pipeline at receiving facilities and segregated to prevent contamination.
Crude oil contains varying amounts of wax, or paraffin, and in colder climates wax buildup may occur within a pipeline. To clear wax deposition, mechanical pigs may be sent along the line periodically.
|
|
For natural gas, smaller feeder lines are used to distribute the fuel to homes and businesses downstream of larger transportation pipelines, similarly constructed of carbon steel and varying in size from 12 inches in diameter to 48 inches in diameter. The gas is pressurized by compressor stations spaced approximately every 70–100 miles and is odorless unless mixed with a mercaptan odorant where identified by the proper regulating body.
In the U.S. pipelines are regulated by the Pipeline and Hazardous Materials Safety Administration (PHMSA); offshore pipelines are regulated by the Minerals Management Service (MMS). In Canada pipelines are regulated by either the provincial regulators or, if they cross provincial boundaries or the Canada / US border, by the National Energy Board (NEB). Government regulations in Canada and the United States require that buried fuel pipelines must be protected from corrosion. Often, the most economical method of corrosion control is by use of pipeline coating in conjunction with cathodic protection and technology to monitor the pipeline system.
Fluid Mechanics
The transport of a fluid (liquid or gas) in a closed conduit (commonly called a pip, if it is of round cross section) or duct (if it is not round) is extremely important.
Some of the basic components of a typical pipe system are depicted in Fig. . They include the pipes themselves perhaps more than one diameter), various fittings used to connect the individual pipes to form the desired system, the flowrate control devices (valves), and pumps (turbines) that add energy to or remove energy from the fluid.
Fig. Typical pipe system components
In general, fluids have a well-known tendency to move or flow. It is very difficult to restrain fluid from moving. The slightest shear stress will cause fluid to move. Similarly, appropriate imbalance of normal stresses (pressure) will cause fluid motion.
Дата добавления: 2019-01-14; просмотров: 266; Мы поможем в написании вашей работы! |
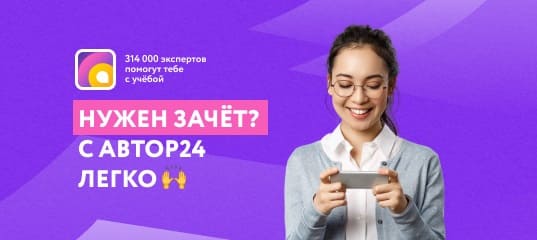
Мы поможем в написании ваших работ!