Major products of oil refineries
Most products of oil processing are usually grouped into three categories: light distillates (LPG, gasoline, naptha), middle distillates (kerosene, diesel), heavy distillates and residuum (fuel oil, lubricating oils, wax, tar). This classification is based on the way crude oil is distilled and separated into fractions (called distillates and residuum) as can be seen in the above drawing.
- Asphalt
- Diesel fuel
- Naphtha
- Fuel oils
- Gasoline
- Kerosene and related jet aircraft fuels
- Liquid petroleum gas (LPG)
- Lubricating oils
- Paraffin wax
- Tar
Common process units found in a refinery
- Desalter Unit (washes out salt from the crude oil before it goes into the atmospheric distillation unit)
- Atmospheric Distillation Unit (distills crude oil into fractions)..
- Vacuum Distillation Unit (further distills residual bottoms after atmospheric distillation)
- Naphtha Hydrotreater Unit (uses hydrogen to desulfurize naphtha from atmospheric distillation. Must hydrotreat the naphtha before sending to a Catalytic Reformer Unit.)
- Catalytic Reformer Unit (contains catalyst used to convert the naphtha-boiling range molecules into higher octane reformate (reformer product). The reformate has higher content of aromatics, olefins, and cyclic hydrocarbons). An important byproduct of a reformer is hydrogen released during the catalyst reaction. The hydrogen is used either in the hydrotreaters and hydrocracker.)
- Distillate Hydrotreater Unit (desulfurizes distillate (diesel) after atmospheric distillation)
- Fluid Catalytic Cracking (FCC) Unit (upgrades heavier fractions into lighter, more valuable products)
- Hydrocracker Unit (uses hydrogen to upgrade heavier fractions into lighter, more valuable products)
- Merox treater - In certain cases such as for jet fuel or kerosene treatment, a Merox process unit may be used to oxidize mercaptans to organic disulfides.
- Coking unit (processes asphalt into gasoline and diesel fuel, leaving coke as a residual product)
- Alkylation unit (produces high octane component for gasoline blending)
- Dimerization Unit
- Isomerization Unit (converts linear molecules to higher octane branched molecules for blending into gasoline or feed to alkylation units)
- Steam reforming Unit (produces hydrogen for the hydrotreaters or hydrocracker)
- Liquified gas storage units for propane and similar gaseous fuels at pressure sufficient to maintain in liquid form - these are usually spherical or bullets (horizontal cylinder with rounded ends).
- Storage tanks for crude oil and finished products, usually cylindrical, with some sort of vapor enclosure and surrounded by an earth berm to contain spills
- Amine gas treater, Claus unit, and tail gas treatment for processing hydrogen sulfide from hydrodesulfurization
- Utility units such as cooling towers for circulating cooling water, boiler plants for steam generation, instrument air systems for pneumatically operated control valves and an electrical substation.
- Wastewater collection and treating systems consisting of API separators, dissolved air flotation (DAF) units and some type of further treatment to make such water suitable for reuse or for disposal.
Flow diagram of typical refinery
|
|
The image below is a schematic flow diagram of a typical oil refinery that depicts the various unit processes and the flow of intermediate product streams that occurs between the inlet crude oil feedstock and the final end products. The diagram depicts only one of the literally hundreds of different oil refinery configurations. The diagram also does not include any of the usual refinery facilities providing utilities such as steam, cooling water, and electric power as well as storage tanks for crude oil feedstock and for intermediate products and end products.
Schematic flow diagram of a typical oil refinery
Specialty end products
These will blend various feedstocks, mix appropriate additives, provide short term storage, and prepare for bulk loading to trucks, barges, product ships, and railcars.
- Gaseous fuels such as propane, stored and shipped in liquid form under pressure in specialized railcars to distributors.
- Liquid fuels blending (producing automotive and aviation grades of gasoline, kerosene, various aviation turbine fuels, and diesel fuels, adding dyes, detergents, antiknock additives, oxygenates, and anti-fungal compounds as required). Shipped by barge, rail, and tanker ship. May be shipped regionally in dedicated pipelines to point consumers, particularly aviation jet fuel to major airports, or piped to distributors in multi-product pipelines using product separators called pipeline inspection gauges ("pigs").
- Lubricants (produces light machine oils, motor oils, and greases, adding viscosity stabilizers as required), usually shipped in bulk to an offsite packaging plant.
- Wax (paraffin), used in the packaging of frozen foods, among others. May be shipped in bulk to a site to prepare as packaged blocks.
- Sulfur (or sulfuric acid), byproducts of sulfur removal from petroleum which may have up to a couple percent sulfur as organic sulfur-containing compounds. Sulfur and sulfuric acid are useful industrial materials. Sulfuric acid is usually prepared and shipped as the acid precursor oleum.
- Bulk tar shipping for offsite unit packaging for use in tar-and-gravel roofing.
- Asphalt unit. Prepares bulk asphalt for shipment.
- Petroleum coke, used in specialty carbon products or as solid fuel.
- Petrochemicals or petrochemical feedstocks, which are often sent to petrochemical plants for further processing in a variety of ways. The petrochemicals may be olefins or their precursors, or various types of aromatic petrochemicals.
|
|
Oil and Gas Separators
The term “oil and gas separator” in oilfield terminology designates a pressure vessel used for separating well fluids produced from oil and gas wells into gaseous and liquid components. A separating vessel may be referred to in the following ways:
1. oil and gas separator;
2. separator;
3. stage separator;
4. trap;
5. knockout vessel, knockout drum, knockout trap, water knockout, or liquid knockout;
6. flash chamber, flash vessel or flash trap;
7. expansion separator or expansion vessel;
8. scrubber (gas scrubber), dry or wet type;
9. filter (gas filter), dry or wet type;
10. filter \ separator.
The terms “oil and gas separator”, “separator”, “stage gas separator” and “trap” refer to a conventional oil and gas separator. These separating vessels are normally used on a producing lease or platform near the wellhead, manifold or tank battery to separate fluids produced from oil and gas wells into oil and gas or liquid and gas. .They must be capable of handling “slugs” or “heads” of well fluids. Therefore, they are usually sized to handle the highest instantaneous rates of flow.
|
|
A knockout vessel, drum or trap may be used to remove only water from the well fluid or to remove all liquid, oil plus water, from the gas. In the case of a water knockout for use near the wellhead, the gas and liquid petroleum are usually discharged together, and the free water is separated and discharged from the bottom of the vessel.
A liquid knockout is used to remove all liquid, oil plus water, from the gas. The water and liquid hydrocarbons are discharged together from the bottom of the vessel, and the gas is discharged from the top.
A flash chamber (trap or vessel) normally refers to a conventional oil and gas separator operated at low pressure, with the liquid from a higher-pressure separator being “flashed” into it. This flash chamber is quite often the second or third stage of separation, with the liquid being discharged from the flash chamber to storage.
An expansion vessel is the first-stage separator vessel on a low-temperature or cold-separation unit. This vessel may be equipped with a heating coil to melt hydrates, or a hydrate-preventive liquid (such as glycol) may be injected into the well fluid just before expansion into this vessel.
A gas scrubber may be similar to an oil and gas separator. Usually it handles fluid that contains les liquid that that produced from oil and gas wells. Gas scrubbers are normally used in gas gathering, sales and distribution lines, where they are not required to handle slugs or heads of liquid, as is often the case with oil and gas separators. The dry-type gas scrubber uses mist extractors and other internals similar to oil and gas separators. The wet-type gas scrubber passes the stream of gas through a bath of oil or other liquid that washes dust and other impurities from the gas. The gas s flowed through a mist extractor where all removable liquid is separated from it. A “scrubber” can refer to a vessel used upstream from any gas-processing vessel or unit or protect the down-stream vessel or unit from liquid hydrocarbons and \or water.
|
|
The “filter” (gas filter \ filter separator) refers to a dry-type gas scrubber, especially if the unit is being used primarily to remove dust from the as stream. A filtering medium is used in the vessel to remove dust, line scale, rust and other foreign material fro the gas. Such units will normally remove liquid from the gas.
An oil and gas separator generally includes the following essential components and features:
1. a vessel that includes (a) primary separation device and\or section; (b) secondary “gravity” settling (separating) section; (c) mist extractor to remove small liquid particles from the gas; (d) gas outlet; (e) liquid settling (separating) section to remove gas or vapor from oil (on a three-phase unit, this section also separates water from oil); (f) oil outlet; (g) water outlet (three-phase unit).
2. adequate volumetric liquid capacity to handle liquid surges (slugs) from the wells and\or flowlines.
3. adequate vessel diameter and height or length to allow most of the liquid to separate from the gas so that the mist extractor will not be flooded.
4. a means of controlling an oil level in the separator, which usually includes a liquid-level controller and a diaphragm motor valve on the oil outlet. For three-phase operation, the separator must include and oil\water interface liquid-level controller and a water- discharge control valve.
5. a backpressure valve on the gas outlet to maintain a steady pressure in the vessel.
6. pressure relief devices.
In most oil and gas surface production equipment systems, the oil and gas separator is the first vessel the well fluid flows through after it leaves the producing well. However, other equipment – such as heaters and water knockouts, may be installed upstream of the separator. Fig. shows a typical surface production equipment system for handling crude oil using an oil and gas separator along with related equipment.
Vessel internals
Gas outlet is the point at which gas leaves the separator into the gas line.
Primary mist extractor is the initial baffle arrangement used to separate the small liquid particles swept upward with the gas stream.
Secondary mist extractor is the final baffle arrangement of a wire mesh used to separate small liquid particles from the gas flow out of the separator.
Deflector cone. Is a device used to restrict liquid flow into the gas separation section and facilitate the separation of free gas vapor into the gas separator section.
Inlet diverter is a device placed opposite the inlet inside the vessel, which causes the incoming fluid to swirl in a centrifugal motion. The friction facilitates separation.
Swirl chamber is the area above and below the inlet and diverter where fluids are thrown against the inside wall of the separator.
Deflector is an additional device used to change direction of the accumulating fluids at the bottom of the vessel.
Oil outlet is the point at which the accumulated oil is removed from the separator.
Drain is located at the bottom of the separator and is used to remove mud, sand, salt, etc.
Pressure gauge is a device that indicates the pressure within the separator
Thermometer is used to indicate temperature within the separator.
Дата добавления: 2019-01-14; просмотров: 201; Мы поможем в написании вашей работы! |
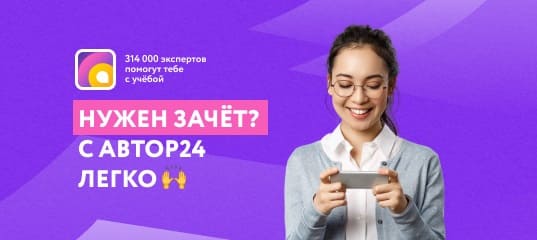
Мы поможем в написании ваших работ!