Corrosion in passivated materials
Passivation is extremely useful in alleviating corrosion damage, but care must be taken not to trust it too thoroughly. Even a high-quality alloy will corrode if its ability to form a passivating film is compromised. Because the resulting modes of corrosion are more exotic and their immediate results are less visible than rust and other bulk corrosion, they often escape notice and cause problems among those who are not familiar with them.
Pitting corrosion
Certain conditions, such as low availability of oxygen or high concentrations of species such as chloride which compete as anions, can interfere with a given alloy's ability to re-form a passivating film. In the worst case, almost all of the surface will remain protected, but tiny local fluctuations will degrade the oxide film in a few critical points. Corrosion at these points will be greatly amplified, and can cause corrosion pits of several types, depending upon conditions. While the corrosion pits only nucleate under fairly extreme circumstances, they can continue to grow even when conditions return to normal, since the interior of a pit is naturally deprived of oxygen. In extreme cases, the sharp tips of extremely long and narrow pits can cause stress concentration to the point that otherwise tough alloys can shatter, or a thin film pierced by an invisibly small hole can hide a thumb sized pit from view. These problems are especially dangerous because they are difficult to detect before a part or structure fails. Pitting remains among the most common and damaging forms of corrosion in passivated alloys, but it can be prevented by control of the alloy's environment, which often includes ensuring that the material is exposed to oxygen uniformly (i.e., eliminating crevices).
Fretting
Many useful passivating oxides are also effective abrasives, particularly TiO2 and Al2O3. Frettingcorrosion occurs when particles of corrosion product continuously abrade away the passivating film as two metal surfaces are rubbed together. While this process does often damage the frets of musical instruments, they were named separately.
Weld decay and knifeline attack
Stainless steel can pose special corrosion challenges, since its passivating behavior relies on the presence of a minor alloying component (Chromium, typically only 18%). Due to the elevated temperatures of welding or during improper heat treatment, chromium carbides can form in the grain boundaries of stainless alloys. This chemical reaction robs the material of chromium in the zone near the grain boundary, making those areas much less resistant to corrosion. This creates a galvanic couple with the well-protected alloy nearby, which leads to weld decay (corrosion of the grain boundaries near welds) in highly corrosive environments. Special alloys, either with low carbon content or with added carbon "getters" such as titanium and niobium (in types 321 and 347, respectively), can prevent this effect, but the latter require special heat treatment after welding to prevent the similar phenomenon of knifeline attack. As its name applies, this is limited to a small zone, often only a few micrometres across, which causes it to proceed more rapidly. This zone is very near the weld, making it even less noticeable.
|
|
Microbial corrosion
Microbial corrosion, or bacterial corrosion, is a corrosion caused or promoted by microorganisms, usually chemoautotrophs. It can apply to both metals and non-metallic materials, in both the presence and lack of oxygen. Sulfate-reducing bacteria are common in lack of oxygen; they produce hydrogen sulfide, causing sulfide stress cracking. In presence of oxygen, some bacteria directly oxidize iron to iron oxides and hydroxides, other bacteria oxidize sulfur and produce sulfuric acid. Concentration cells can form in the deposits of corrosion products, causing and enhancing galvanic corrosion.
High temperature corrosion
The chemical deterioration of of typically a metal under very high temperature conditions. This non-galvanic form of corrosion can occur when a metal is subject to a high temperature atmosphere containing oxygen, sulphur or other compounds capable of oxidising (or assisting the oxidation of) the material concerned. For example, materials used in aerospace, power generation and even in car engines have to resist sustained periods at high temperature in which they may be exposed to an atmosphere containing potentially highly corrosive products of combustion.
The products of high temperature corrosion can potentially be turned to the advantage of the engineer. The formation of oxides on stainless steels, for example, can provide a protective layer preventing further atmospheric attack, allowing for a material to be used for sustained periods at both room and high temperature in hostile conditions. Such high temperature corrosion products in the form of compacted oxide layer glazes have also been shown to prevent or reduce wear during high temperature sliding contact of metallic (or metallic and ceramic) surfaces.
|
|
Pipeline corrosion
Corrosion of steel pipelines is a natural process and steel pipes, when buried, invariably suffer from external corrosion unless adequately protected. Pipelines are usually coated to protect the external surfaces of the steel pipe against corrosion.
There are essentially two methods: impressed current method and sacrificial anode method. For onshore pipelines it is common to use an impressed current method. In this system, a DC (direct current) is supplied to the pipeline and is made to flow between the pipe and an anode ground bed via the soil. The current is adjusted to generate higher driving potentials in the pipe than those existing naturally in the corrosion cell. This neutralizes or reverses the effects of corrosion. This system requires transformer stations and is usually monitored by output voltage readings. A sacrificial anode method, on the other hand, relies upon the installation of anodes on or near the pipeline. The pipeline becomes the cathode of the system and the anodes, which corrode are sacrificed to arrest corrosion of the pipeline. When water is present on the transported fluid, corrosion of the internal pipe surfaces can also occur. Water may be present, either alone, or in combination with CO2, H2O, O2 or other salts. The severity of corrosion depends upon the operating temperature, pressure, conductivity, soil condition, pH and fluid velocity and composition. Corrosion control measures include water removal and drying, chemical injection and corrosion allowance on wall thickness. Wall thickness – the most important element in pipeline mechanical design is the determination of pipeline wall thickness. Wall thickness is a function of the pipeline maximum allowable operating pressure and the yield strength of the steel pipe used. Operating pressure and wall thickness determine the number and locations of pump or compressor stations along the pipeline. If a higher pipeline operating pressure is chosen, the power at each station can be greater, and the stations can be farther apart.
|
|
Corrosion | |
To suffer | |
External corrosion | |
To coat | |
External surface | |
Impressed current method | |
Sacrificial anode method | |
DC (direct current) | |
To supply | |
Anode ground bed | |
Via | |
Soil | |
Driving potentials | |
Corrosion cell | |
To neutralize | |
To reverse | |
Transformer station | |
Monitor (by) | |
Output voltage | |
Readings | |
Rely on | |
Installation | |
Anode | |
To corrode | |
To be sacrificed | |
To arrest | |
Transported fluid | |
Severity | |
Conductivity | |
Soil condition | |
pH | |
Fluid velocity | |
Water removal | |
Water drying | |
Chemical injection | |
Corrosion allowance | |
Wall thickness | |
Determination | |
Allowable operating pressure | |
Yield strength |
Сплошная поверхностная коррозия
Сплошная поверхностная коррозия
![]() | |||
![]() |
ЯЗВЕННАЯ КОРРОЗИЯ
ПИТТИНГОВАЯ КОРРОЗИЯ
Pipeline Coatings
Applied coatings
|
|
Plating, painting, and the application of enamel are the most common anti-corrosion treatments. They work by providing a barrier of corrosion-resistant material between the damaging environment and the (often cheaper, tougher, and/or easier-to-process) structural material. Platings usually fail only in small sections, and if the plating is more noble than the substrate (for example, chromium on steel), a galvanic couple will cause any exposed area to corrode much more rapidly than an unplated surface would. For this reason, it is often wise to plate with a more active metal such as zinc or cadmium.
The corrosion control system for an oil and gas pipeline consists of two parts: the external coating on the pipeline and the cathodic protection. The primary purpose of the coating is to protect the pipe surface from its external environment. Coatings are also increasingly used to protect the internal surface of pipelines. Over the years the pipeline has been protected by various polymeric coatings. In the 1950s and 1960s, coal tar or asphalt coatings were applied. In the mid-1950s, mill-applied extruded polyethylene coatings were introduced (primarily on small-diameter pipes). From the early 1960s to the early 1980s, polyethylene tape coatings were field applied.
Reactive coatings
If the environment is controlled (especially in recirculating systems), corrosion inhibitors can often be added to it. These form an electrically insulating and/or chemically impermeable coating on exposed metal surfaces, to suppress electrochemical reactions. Such methods obviously make the system less sensitive to scratches or defects in the coating, since extra inhibitors can be made available wherever metal becomes exposed. Chemicals that inhibit corrosion include some of the salts in hard water (Roman water systems are famous for their mineral deposits), chromates, phosphates, and a wide range of specially-designed chemicals that resemble surfactants (i.e. long-chain organic molecules with ionic end groups).
Anodization
Aluminium alloys often undergo a surface treatment known as anodization in a chemical bath near the end of their manufacture. Electrochemical conditions in the bath are carefully adjusted so that uniform pores several nanometers wide appear in the metal's oxide film. These pores allow the oxide to grow much thicker than passivating conditions would allow. At the end of the treatment, the pores are allowed to close (sealed), forming a harder-than-usual (and therefore more protective) surface layer. If this coating is scratched, normal passivation processes take over to protect the damaged area.
Cathodic protection
Cathodic protection (CP) is a technique to control the corrosion of a metal surface by making that surface the cathode of an electrochemical cell.It is a method used to protect metal structures from corrosion. Cathodic protection systems are most commonly used to protect steel, water, and fuel pipelines and tanks; steel pier piles, ships, and offshore oil platforms.
The application of cathodic protection (CP) for steel gas pipelines started in the 1930s. This technology was rapidly adopted by the oil and gas pipeline industry to protect the pipeline by applying -8,50 mV vs. Cu/CuSO4 in conjunction with polymeric coatings. Protecting the external surface of oil and gas pipelines by the application of cathodic protection is one of the main requirements. For effective CP, the potential of the steel surface is polarized (pushed) more negative until the metal surface has a uniform potential. With a uniform potential, the driving force for the corrosion reaction is halted. For galvanic CP systems, the anode material corrodes under the influence of the steel, and eventually it must be replaced. The polarization is caused by the current flow from the anode to the cathode, driven by the difference in electrochemical potential between the anode and the cathode.
Oil Storage
Types of Storage Tanks
Every facility involved in the production of petroleum and related products requires some type of storage. Manufacturers also should be consulted for specific design information on a particular type of storage. During the early days of oil production, the method of storing was almost exclusively white-pine wooden tanks, which were followed by cypress tanks, and then redwood tanks. However, because of the constant and steep rise in the cost of redwood lumber and the diminution of skilled erectors required, the installation of new wooden tanks is nearly non-existent. The bolted-steel tank was developed next and virtually replaced the wooden tank.
Bolted-steel tanks
Bolted tanks are designed and furnished as segmental elements assembled on location to provide complete vertical, cylindrical, above-ground, closed and open-top steel storage tanks. Standard API bolted tanks are available in nominal capacities of 100to 10.000bbl, and are designed for approximately atmospheric internal pressures. Bolted tanks offer the advantage of being easily transported to desired locations and erected by hand. To meet changing requirements for capacity of storage, bolted tanks can be easily dismantled and re-erected at new locations. If a tank develops a hole from corrosion or becomes damaged, a single sheet or more ma be replaced. A complete tank bottom may be replaced in the field without dismantling the tank. Also, a section may be removed from the tank, a new connection installed in the sheet and the section replaced without danger. No special equipment is required for the erection of bolted tanks. These tanks are erected b non-specialized crews using had tools and usually an impact wrench. Bolted tanks are available with painted, galvanized ad special coatings, including factory-baked coatings. Painting on both sides of the sheets during fabrication gives the inside of the tank some corrosion protection. Galvanizing the sheets and all tank parts by the “hot-dip” process or applying a factory-baked coating affords high corrosion protection. Generally, bolted tanks are fabricated from 12- or 10-gauge steel, and if not galvanized or furnished with a protective coating for corrosion protection, the do not have the expected life of the welded – steel tanks, which are usually constructed of heavier steel.
The component parts of a typical bolted tank are shown in Fig. .
|

Fig. Typical bolted tank
Welded – steel Tanks Shop-fabricated welded, cylindrical-shape tanks are available in a large variety of sizes as shop-fabricated items. Shop-welded tanks fabricated to API specifications provide the oil production industry with tanks of adequate safety and reasonable economy for use in the storage of crude petroleum and other liquids commonly handled and stored by the production segment of the industry. Shop-welded tanks are usually fabricated from 3\16-in. or heavier steel and will permit internal pressure up to 16oz. Shop fabrication permits testing in the shop for leaks and also provides immediate storage. Tanks are merely up-ended from a truck on the location.
Field-welded Tanks provide large storage capacities in a single unit. Large field-welded tanks providing storage capacities of 150.000bbl or more have become prevalent for use in the storage of oil and petroleum products. Field-welded tanks are designed and erected in accordance with API Standard, which covers material, design, fabrication, erection and testing requirements for welded-steel storage tanks. It also includes an alternative basis for shell design, as well as one for calculating tank-shell thickness.
Fixed Roof are permanently attached to the tank shell. Welded tanks of 50bbl capacity and larger may be provided with a frangible roof (designed for safety release of the welded deck-to-shell joint in the event excess internal pressure occurs). In this case, the design pressure should not exceed the equivalent pressure of the dead weight of the roof including rafters, if external.
Floating Roof storage tanks may be tank type is used primarily for storage near atmosphere pressure. Floating roofs are designed to move vertically within the tank shell to provide a constant minimum void between the surface of the stored product and the roof. Floating roofs normally are designed to provide a constant seal between the periphery of the floating roof and the tank shell. They can be fabricated in a type that is exposed to the weather or a type that is under a fixed roof. Internal floating-roof tanks, with an external fixed roof, are used in areas of heavy snowfall since accumulations of snow or water on the floating roof affect the operating buoyancy. These can be installed in existing tanks as well as new tanks. Both floating roofs and internal floating roofs are used to reduce vapour losses and to aid in conservation programs. Fig. is a schematic of a typical internal floating roof tank.
Fig. Typical arrangement of internal floating roof
|
Cone-Bottom Tanks The cone-bottom in either the bolted or the welded tank offer a means of draining and removing water or water-cut oil, from only the bottom of the tank, leaving the marketable oil above. The drain line from a sump-equipped cone bottom must be equipped with a vortex breaker to drain off most of the water without coning oil into the drain. With a flat-bottom tank, some of the marketable oil must be removed if all the water is removed from the tank. Corrosion o the tank bottom is kept to a minimum by keeping all water removed. A cone bottom can be kept clean without having to open the tank if 1 or 2bbl are drained off once or twice weekly and pumped back through the treating system. If this is not done and the bottom solidifies, the tank must be opened. The cone- bottom tank can be cleaned without entering. A water hose, handled just outside the cleanout opening, can be used to flush the solids to the centre of the cone and drain connection.
Coating types Many types of internal coatings are available for numerous protection requirements. Because of the unlimited types and applications, only a few are described here:
Coal tar – among the oldest and most reliable coatings, coal tar has extremely low permeability, protects the surface by the mechanical exclusion of moisture and air, is extremely water resistant and resists weak mineral acids, alkalis, salts, brine solutions and other aggressive chemicals as well.
Epoxy resin- gives an excellent adhesion, toughness, abrasion resistance, flexibility, high gloss and durability and good chemical and moisture resistance. Typical applications include linings for sour-crude tanks, floating roof tanks, solvent storage tanks, drilling mud tanks and pipelines.
Rubber lining is used as internal lining for storage tanks that are subjected to severe service, such as elevated temperatures or for protection from extremely corrosive contents such as concentrated chlorides and various acids (chromic, sulphuric, hydrochloric and phosphoric).
Galvanized (zinc coating) – is highly resistant to most types of corrosion. Bolted steel tanks are ideally suited for galvanizing since all component parts are galvanized by the hot-dip process after fabrication but before erection. Galvanized bolted tanks are recommended where sulphur oil is produced and associated with hydrogen sulphide gas. Galvanizing is also very effectiveagainst corrosion in seacoast areas where atmospheric conditions present difficulties in maintaining tank life.
External are for protection against weathering exposure and appearance. Many types of external coatings are available, ranging from basic one-coat primers to primers with one or more top coats. Environmental conditions usually dictate the extent of coating applied. Offshore and coastal installations require more extensive coatings compared with inland locations.
oil storage | нефтехранилище |
storage tank | резервуар для хранения нефтепродуктов |
facility | оборудования |
production | добыча |
white-pine | сосна |
redwood | красное дерево |
diminution | уменьшение \ снижение |
erector | монтажник |
installation | монтаж \ установка |
non-existent | несуществующее |
bolted-steel tank | сборный резервуар |
welded tank | сварной резервуар |
nominal capacity | номинальная мощность |
internal pressure | внутреннее давление |
dismantle | разборка |
desired location | |
erected by hand | установить ручной |
meet requirements | отвечать требования |
sheet | лист |
bottom | дно |
replace | заменить |
factory-baked | |
connection | соединение |
impact wrench | гайковерт |
galvanized | оцинковывать |
coating | покрытие \ грунтовка |
corrosion protection | |
fabrication be fabricated) | изготовление |
gauge steel | толщина (калибр размер) |
deck | крыша |
bolt | болт |
dome | купол |
rafter | балка \ стропила |
channel | канал |
ladder | висячая лестница |
leak | утечка |
up-ended | опрокидывать |
hot-dip process | пропитка |
be furnished | снабжать |
cleanout | очистное отверстие |
centre plate | плита |
slave | планка |
flat-sided | плоский |
cell | камера |
atmospheric-type storage | хранение при атмосферного давления |
field-welded tank | |
capacity | вместимость |
shell | корпус |
shop-welded | заводской |
fixed roof | фиксированная крыша |
frangible | |
joint | шарнир |
design pressure | расчетное давление |
dead weight | собственный вес |
Pipeline Repair Considerations
It is very important to properly determine if a defect discovered in a steel pipe should be repaired or a section of the pipe replaced. Operators utilize bother external and internal surveys to evaluate the condition of the pipelines. Common practice is to consider the results of cathodic protection potential surveys to evaluate the effectiveness of external corrosion control systems installed in pipelines. Low potentials recorded during these surveys often are an indication of coating damage. Often the next step after a cathodic protection survey is to run an external coating analysis survey over areas identified as low potential points on the pipeline. An external coating analysis survey pinpoints areas of coating damage on the pipeline. Coating damage combined with low potentials can be identifications of a high risk for active corrosion in those areas. Once the areas are identified, bell hole excavations are conducted to allow for an examination of defects. The common method used to further evaluate pipelines and pinpoint wall loss is by the use of internal tool data. The tool utilized for this type of pipeline inspection is commonly identified as an intelligent pig. A pig is considered intelligent when it is used to measure and record wall thickness and is used to assess pipeline integrity.
Defect Identification intelligent pigging surveys can provide pipeline information on welds, branch connections, valves and wall thickness changes along with information about the wall loss and delamination or defects that the pig was designed to find. The two types of intelligent pigs utilized to detect metal loss in a steel pipeline fro corrosion are the magnetic flux leakage (MFL) and the ultrasonic (UT). The two goals of a pipeline inspection are the detection of defects and the sizing of defects. Pigs are usually used to find a particular type of defect.
Defect Assessment the purpose of measuring and characterizing corrosion is to determine the remaining wall thickness of the steel pipe. It is possible if an ultrasonic thickness gauge is used. Ultrasonic thickness gauges are used for measuring either internal or external corrosion. The latest development in defect assessment is the laser profilometer. Pit gauges can provide a quick and reasonably accurate measurement of the depth of single isolated pits. However, they provide limited benefit for measuring corrosion near a long seam or girth weld.
Pipeline inspection gauge
A pipeline inspection gauge or pig in the pipeline industry is a tool that is sent down a pipeline and propelled by the pressure of the product in the pipeline itself. Also known as an Inline Inspection (ILI) tool, it is the chief device used in pigging.
The original pigs were made from straw wrapped in wire used for cleaning. They made a squealing noise while traveling down the pipe that sounded to some like a pig squealing; the term "pipeline inspection gauge" was later created as a backronym.
One kind of pig is a soft, bullet shaped polyurethane plug that is forced through pipelines to separate products to reduce mixing. There are several types of pigs for cleaning. Some have tungsten studs or abrasive wire mesh on the outside to cut rust, calcium, or paraffin deposits off the inside of the pipe; others are plain plastic covered polyurethane.
Inline inspection pigs use various methods for inspecting the condition of a pipeline. A sizing pig uses one (or more) notched round metal plates that are used as gauges. The notches allow different parts of the plate to bend when a bore restriction is encountered. More complex systems exist for inspecting various aspects of the pipeline. Intelligent pigs, also called smart pigs, are used to inspect the pipeline with various sensors and record the data for later analysis. These pigs use technologies such as MFL (Magnetic Flux Leakage) and ultrasonics to detect the various aspects of the pipeline. 'Intelligent' or 'smart' pigs may also use calipers to measure the inside geometry of the pipeline.
The first smart pig was run in 1964. This inspection tool used MFL technology to inspect the bottom portion of the pipeline. The recording system used a flight data recorder black box to store the information.
Magnetic flux leakage
Magnetic flux leakage (MFL) is a magnetic method of nondestructive testing that is used to detect corrosion and pitting in steel structures, most commonly pipelines and storage tanks. The basic principle is that a powerful magnet is used to magnetize the steel. At areas where there is corrosion or missing metal, the magnetic field "leaks" from the steel. In an MFL tool, a magnetic detector is placed between the poles of the magnet to detect the leakage field. Analysts interpret the chart recording of the leakage field to identify damaged areas and hopefully to estimate the depth of metal loss.
Introduction to Pipeline Examination
There are many methods of assessing the integrity of a pipeline. In-line-Inspection (ILI) tools are built to travel inside a pipeline and collect data as they go. The type of ILI that has been in use the longest for pipeline inspection, is the magnetic flux leakage inline inspection tool (MFL-ILI). MFL-ILIs detect and assess areas where the pipe wall may be damaged by corrosion. The more advanced versions are referred to as "high-resolution" because they have a large number of sensors. The high-resolution MFL-ILIs allow more reliable and accurate identification of anomalies in a pipeline, thus, minimizing the need for expensive verification excavations (i.e. digging up the pipe to verify what the problem is).
The reliable supply and transportation of product in a safe and cost-effective manner is a primary goal of most pipeline operating companies and managing the integrity of the pipeline is paramount in maintaining this objective. In-line-inspection programs are one of the most effective means of obtaining data that can be used as a fundamental base for an Integrity Management Program. There are many types of ILI tools that detect various pipeline defects, but high-resolution MFL tools are becoming more prevalent as its applications are surpassing those to which it was originally designed. Originally designed for detecting areas of metal loss, the modern High Resolution MFL tool is proving to be able to accurately assess the severity of corrosion features, define dents, wrinkles, buckles, and, in some cases, cracks. Having a device that can perform simultaneous tasks reliably is more efficient and ultimately provides cost saving benefits.
Дата добавления: 2019-01-14; просмотров: 159; Мы поможем в написании вашей работы! |
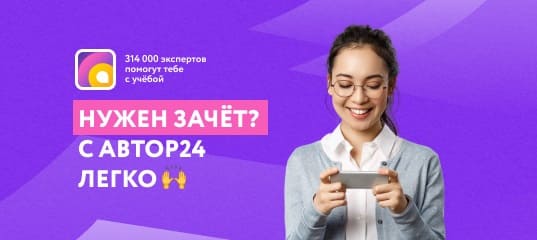
Мы поможем в написании ваших работ!