Конструирование деталей из пластических материалов
Как известно, все пластмассы делятся на термореактивные (реактопласты) и термопластические (термопласты).
Процесс изготовления аппаратов из термореактивных материалов (фаолит) состоит в формировании деталей из мягкого листа и отверждаются термической обработкой при 100-160°С.
Изделия из термопластических материалов (винипласт, акрипласт) производятся формовкой из листов, предварительно нагретых до температуры размягчения (80-100°С), после чего подвергаются холодной обработке, в случае необходимости склеиваются и свариваются.
Изготовление деталей из пластических материалов может осуществляться прессованием в специальных пресс-формах. Такая технология накладывает определенные требования к конструкции прессованных деталей.
Требования к толщине стенок.
Излишняя толщина стенок приводит к перерасходу материала и увеличению времени выдержки изделия в прессе. Наиболее оптимальная толщина стенок составляет 2-4 мм. Наибольшая толщина стенок не должна превышать 10-12 мм. Желательно выдерживать толщину стенок одинаковой по всему изделию. В местах скопления материала он полностью не затвердевает даже при длительной выдержке в прессе, что приводит к снижению прочности изделия. Переходы от одной толщины стенки к другой должны быть по возможности плавными.
Требования к радиусам закруглений.
Следует избегать острых углов на стенках изделий, т.к. это приводит к образованию концентрации напряжений.
|
|
Рекомендуемые радиусы закруглений (рис. 86):
- внутренние и наружные в вертикальных проекциях и внутренние в горизонтальных проекциях: R³0,5-1,5 мм;
- наружные в горизонтальных проекциях: Rн = 5-10 мм.
Требования к жесткости конструкции.
Ребра жесткости позволяют уменьшать толщину изделия и экономить тем самым пластический материал (рис. 87). Высота ребер жесткости не должна мешать механической обработке изделия, для этого их немного не доводят до поверхности обработки. Толщина ребер принимается равной толщине стенок.
Повышение жесткости достигается также заменой плоских поверхностей сферическими (рис. 88).
Обеспечение выемки деталей из формы.
Для облегчения удаления изделия из формы и пуансона из изделия делается уклон (1:100 или 1:200). Уклон внутренних стенок рекомендуется делать больше уклона наружных (рис. 88, 89).
Оформление края изделия.
Если требуется расположение по краю изделия буртика, то он должен быть не слишком тонким или толстым (рис. 90) и идти воль всего периметра детали (рис. 91).
Требования к выполнению отверстий.
Отверстия в прессованных изделиях можно выполнить тремя способами:
|
|
- отформовать сквозное отверстие при прессовании;
- отформовать отверстие не до конца с последующим сквозным сверлением;
- сверлить отверстие после прессования.
Вертикальные сквозные отверстия можно отпрессовать длиной L < 10 d .
Вертикальные несквозные отверстия длиной L < 7,5 d .
Требования к технологичности прессования.
Для упрощения устройства пресс-форм и повышения производительности прессования в конструкциях изделий необходимо избегать поднутрений (рис. 92); избегать отверстий в боковых стенках (рис. 93).
Доведение отверстий до верхнего края изделия значительно упрощает формовку.
Неизбежное поднутрение можно исключить изготовлением детали из двух частей (рис 94).
Выполнение резьбы в деталях из пластических материалов.
Резьба диаметром более 5 мм выполняется путем прессования. Наиболее часто применяется метрическая резьба, реже – круглая резьба. Если в отверстие с резьбой должен ввинчиваться металлический винт, в пластмассовую деталь запрессовывают металлическую втулку с резьбой.
Запрессовка металлических деталей.
Арматуре, запрессовываемой в пластмассу желательно придавать округленную форму и размещать не слишком близко к краю, чтобы избежать растрескивания пластмассы, причем сечение металлической арматуры должно быть намного меньше сечения пластмассы.
|
|
Запрессованная арматура должна иметь накатку или выточки, исключающие ее проворачивание или вытаскивание.
Диаметр накатки запрессованных шпилек должен быть: D ³ d + 1 мм (рис. 95), т.е. расстояние от буртика до стержня должно быть не менее 0,5 мм на сторону.
Расположение грата.
Грат – заусенец, получающийся в местах соприкосновения матрицы с пуансоном или по линии разъема формы. Вертикальный грат, образующийся вдоль движения пуансона удаляется наждачным кругом. Горизонтальный грат (перпендикулярный движению пуансона) срезается на токарном станке.
Следует учитывать, что обточка грата на токарном станке не портит вид изделия, но обходится дороже, чем шлифование.
Дата добавления: 2018-09-23; просмотров: 385; Мы поможем в написании вашей работы! |
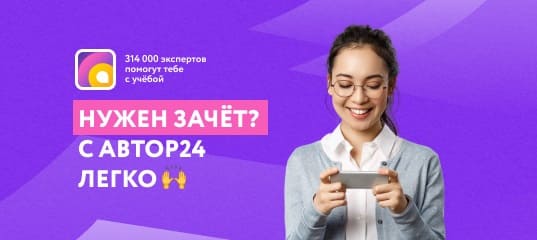
Мы поможем в написании ваших работ!