Конструирование сварной аппаратуры
При конструировании сварной аппаратуры должен быть назначен способ сварки, тип шва, подготовка кромок.
Способ сварки (электродуговая автоматическая, полуавтоматическая, ручная дуговая) выбирается в зависимости от материала, геометрических размеров свариваемых частей и оснащенности завода.
Тип сварного шва (встык, втавр, внахлест) зависит от расположения листов и способа сварки.
Подготовка кромок листов перед сваркой зависит от способа сварки и толщины листов. Подготовка кромок под ручную электродуговую сварку показана на рис. 21, под автоматическую сварку под флюсом – на рис. 22.
Наименьшая длина катета сварных швов К min зависит от толщины листа s (тадл. 1).
Таблица 1
s, мм | < 4 | 4 - 8 | 9 - 15 | 16 - 25 | 25 |
Kmin , мм | 3 | 4 | 6 | 8 | 10 |
Но при этом величина катета на должна превышать
К£ 1,2×smin ,
где smin – наименьшая толщина соединяемых листов.
Следует избегать излишней обработки кромок, например, при соединении обечаек с трубными досками (рис. 23) не следует скашивать кромки (рис. 23 б) или протачивать канавку (рис. 23 в).ё
Листы или обечайки, соединяемые стыковой сваркой, должны быть по возможности, одинаковой толщины. Если же толщина отличается больше чем на 20-25 %, для их соединения необходимо выполнить скос с уклоном 1:5 (рис. 24).
Место шва должно быть доступно для сварки (рис. 25)
Соединение аппаратов из труб малого диаметра поперечным швом, когда подрубка и подварка шва невозможны, необходимо устанавливать подкладные кольца или предусматривать соединение в замок (рис. 26). Толщину подкладных колец берут в пределах (0,3-0,5)×s ,а их ширину (4×s+5 мм), но не менее 20 мм.
|
|
Для того чтобы не перегревать швы и не подвергать металл повторному расплавлению, следует разносить швы, как показано на рис. 27. Расстояние между швами а должно быть не менее 3×s или 40 мм. Также не следует несколько деталей соединять одним швом (рис. 28).
Для обеспечения осмотра сварных швов, что особенно важно в химической аппаратуре, необходимо лапы и опоры располагать так, чтобы они не перекрывали сварные швы (рис. 29).
Концы ребер жесткости при односторонней приварке следует закреплять сваркой с обеих сторон (рис. 30).
Операции клепки, развальцовки, чеканки, обработка резанием и др. должны производиться после сварки, т.к. возникающие термические деформации и коробление нарушат прочность и плотность соединений. Если приходится сваривать обработанные детали, то место сварки необходимо относить дальше от обработанной поверхности (рис. 31).
Рекомендуется выносить сварной шов из зоны действия изгибающих напряжений, или избегать конструкций, в которых возникают такие напряжения (рис. 32).
|
|
Рекомендуется снижать до минимума объем сварочных работ путем совместного применения гибки и штамповки со сваркой (рис. 33).
Конструирование деталей, подвергающихся механической обработке
Проектируемым заготовкам должна придаваться форма, удобная для установки на обрабатывающие станки. Иногда приходиться в литых заготовках предусматривать специальные выступы для закрепления на планшайбе станка (рис. 34). После обработки, эти выступы могут быть удалены.
На чертежах деталей требуется правильно назначить черновую и чистовую базы, относительно которых ведется обработка и закрепление детали на станке. В чугунных аппаратах за базу принимают обычно привалочные поверхности фланцев, в стальных аппаратах – торцовые края обечайки.
Поверхность, предназначенная для обработки, должна четко отделяться от необрабатываемой, или обрабатываемой по другому классу чистоты (рис. 35). Толщина таких приливов должна быть больше, чем допуск на литье.
Желательно, чтобы обрабатываемые поверхности были взаимно перпендикулярны, параллельны, или располагались под углами 30°, 45°, 60° (рис. 36).
|
|
Обработку опорной поверхности фланцев лучше производить частичной цековкой (рис. 37).
Поверхность под центрирующий пояс крышки также должна обрабатываться по другому классу чистоты и в этой связи должна отличаться от основной поверхности (рис. 38).
Деталь должна быть доступна и удобна для обработки. Например, чтобы просверлить отверстие для винта в ступице шкива, следует просверлить отверстие в ободе во избежание сверления под углом (рис. 39). При сверлении поверхность детали должна быть по возможности перпендикулярна оси сверла, как в месте входа, так и в месте выхода (рис. 40).
Рекомендуется, чтобы длина сверления была минимальной (рис. 41), она не должна быть больше 6-8 диаметров сверла.
Длина отверстия под резьбу должна быть на 3-4 витка больше самой резьбы (рис. 42). Длина резьбы под шпильки, завинчиваемые в сталь равна диаметру резьбы dн , для шпилек, завинчиваемых в чугун – 1,3×dн , в медь или бронзу – 1,5×dн .
Недопустимо центрировать детали по резьбе, т.к. точность изготовления резьбы значительно ниже точности изготовления гладких поверхностей. Для этого предусматривают специальные центрирующие пояски (рис. 43).
При проектировании валов или других деталей вращения необходимо учитывать то, чтобы соседние диаметры не отличались более чем на 3-5 мм.
Следует избегать валов с квадратными концами, предпочитая для передачи крутящего момента использовать шпонки.
Дата добавления: 2018-09-23; просмотров: 238; Мы поможем в написании вашей работы! |
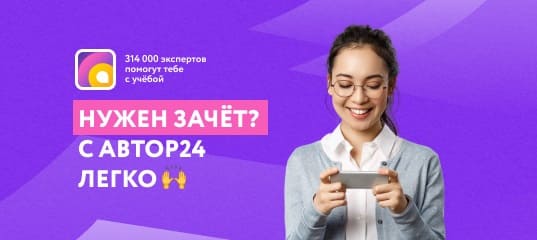
Мы поможем в написании ваших работ!