Конструирование алюминиевых аппаратов
Особенности конструирования аппаратов из алюминия обусловлены такими его свойствами, как легкоплавкость, малая механическая прочность, быстрая окисляемость.
Из-за быстрой окисляемости пайка алюминия практически невозможна, поэтому используется в основном сварка.
Низкая температура плавления (657°С) и малая вязкость расплавленного металла требуют одновременного расплавления соединяемых частей. В этой связи сварка производится только встык и при одинаковой толщине соединяемых частей.
Т.е. принципы конструирования сварных узлов аппаратов из алюминиевых сплавов и высоколегированных сталей аналогичны.
Штуцера привариваются к отбортовке корпуса. Фланцы выполняют из углеродистой стали свободными на отбортовке. Вследствие мягкости алюминия выполнять фланцы на приварном кольце нет необходимости. Внутренний диаметр фланца скругляется во избежание повреждения отбортовки.
Опоры алюминиевых аппаратов выполняются обычно из стали и привариваются к разъемному стальному кольцу, которое, обжимая аппарат, стягивается болтами.
На рис. 81 приведен пример исполнения узла алюминиевого аппарата со смотровым стеклом.
Конструирование эмалированных аппаратов
Высокая стойкость эмали против агрессивных сред обуславливает перспективность применения эмалированных аппаратов в производствах, требующих высокой чистоты продукта.
|
|
Качество эмалевого покрытия зависит в основном от двух причин: правильным выбором и качеством металла под эмалевое покрытие; рациональным конструированием аппарата.
Рекомендуемый состав чугуна, идущего на изготовление эмалированной аппаратуры: С = 3,35-3,5 %, Si = 1,4-1,8%, Mn = 0,55-0,65%, P = 0,3-0,38%, S = 0,10-0,12%.
Рекомендуемый состав стали: С = 0,005-0,09%, Mn = 0,35-0,4%, P = 0,01-0,02%, S = 0,03-0,04%.
Коэффициент линейного расширения материала должен быть близок к коэффициенту расширения эмали. Материал должен быть свободен от шлаковых включений, т.к. из них могут выделяться газы, приводящие к образованию пузырей в эмали.
Конструктивные особенности аппаратов, подлежащих эмалированию:
- Для подготовки аппарата по эмалевое покрытие.
Все внутренние поверхности должны иметь плавные очертания и быть доступными для обработки слесарным инструментом. Острые углы, края, впадины не допускаются. В местных впадинах может скапливаться эмаль, которая после охлаждения из-за термических напряжений может растрескаться.
- Для сохранения качества покрытия во время обжига и остывания.
Одинаковая скорость нагревания и охлаждения всех частей аппарата обеспечивается при его равностенности. Поэтому необходимо не допускать наличия массивных деталей и других скоплений металла. Наибольшую трудность в этом отношении возникают при разработке фланцевых соединений. На рис. 82 показана конструкция аппарата с фланцем. А сами фланцы, могут быть выполнены фигурными, как показано на рис. 83. Это усложняет конструкцию, но ведет к снижению брака.
|
|
- Для недопущения опасных для целостности покрытия напряжений.
Другой особенностью фланцевых соединений, является применение более тонких болтов или шпилек (но в большем количестве). Такое решение позволяет уменьшить расстояние между наружным диаметром прокладки и диаметром болтовой окружности, что ведет к снижению изгибающих моментов. Прокладки применяются мягкие – полиэтилен, фторопласт, резина.
Для уменьшения остаточных напряжений штуцера выполняют конической формы и приваривают их встык на отбортовке (рис. 84).
- Для исключения возможности появления пузырей при обжиге.
Главной причиной появления пузырей в эмали является выделение газов из сварных швов при обжиге. По этой причине лапы и стойки привариваются к аппарату прерывистым швом и без усиливающих листов (последнее также для того, чтобы избежать скопления металла) – рис. 85 а,б. В таких аппаратах применяются также трубчатые стойки, которые привариваются к отрезкам труб, предварительно приваренным к аппарату до эмалирования – рис. 85 в.
|
|
При конструировании эмалированных аппаратов следует учитывать то обстоятельство, что после обжига эмали возможно изменение формы аппарата за счет коробления, которое исправлено впоследствии быть не может. Поэтому необходимо предусматривать достаточные зазоры между стенками аппарата и устройствами, размещаемыми внутри него.
Для уменьшения брака при эмалировании, все мелкие детали и узлы (сальники, стаканы для термометра, устройства для отбора проб и т. п.) следует делать отъемными.
Дата добавления: 2018-09-23; просмотров: 215; Мы поможем в написании вашей работы! |
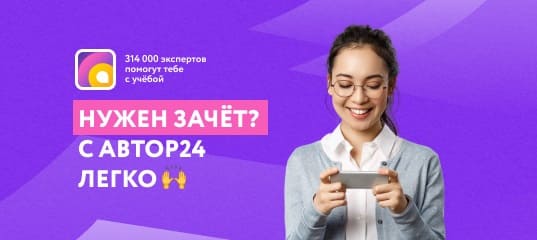
Мы поможем в написании ваших работ!