ВЛИЯНИЕ СПОСОБА ИЗГОТОВЛЕНИЯ АППАРАТА
НА ЕГО КОНСТРУКЦИЮ
Технологические свойства конструкционного материала предопределяют способ изготовления из него частей аппаратов. Чугунные аппараты изготавливаются с помощью литья; стальные также могут быть получены литьем, но чаще изготавливаются из заготовок листового проката, готовых труб и др. заготовок при помощи их сварки, штамповки, гибки. Изготовленные разными способами аппараты, предназначенные для проведения одного и того же процесса, будут конструктивно отличаться друг от друга.
На рис. 1 изображены узлы греющих камер двух выпарных аппаратов – стального (а) и чугунного (б). Трубная доска стального аппарата приварена к корпусу, а трубки развальцованы в трубной доске. Трубная доска чугунного аппарата соединяется с корпусом болтами, а трубки привернуты специальными фасонными гайками. Такое конструктивное решение обусловлено несвариваемостью чугуна и его хрупкостью.
Аппараты, изготовленные из одного и того же материала, но разными способами, также будут отличаться друг от друга. В качестве примера можно рассмотреть клепаное и сварное соединения днища с обечайкой стального ресивера (рис. 2 а, б). Клепаные соединения днища с обечайкой применялись в 50-60-х годах, при этом днище имеет вогнутую форму, для того, чтобы иметь возможность поддерживать головки заклепок во время клепки. Сварка позволяет соединять обечайку с днищами встык, что улучшает и облегчает конструкцию.
|
|
Конструирование литой аппаратуры
Литье является одним из основных способов изготовления элементов аппаратов, что объясняется возможностью получать отливки сложных форм. Применение литья особенно выгодно при массовом производстве одинаковых отливок.
При конструировании учитываются: свойства материала; простота изготовления модели; удобство последующей обработки отливки.
Механические свойства литых изделий зависят не только от химического состава этих материалов, но и от их структуры, зависящей от скорости остывания отливки.
Одним из важнейших принципов конструирования литых деталей является обеспечение одинаковой скорости остывания всех частей отливки. Поэтому все наружные стенки отливки следует стараться сделать одинаковой толщины. Внутренние стенки, перегородки и ребра находятся в худших условиях в отношении их охлаждения. Для выравнивания скоростей охлаждения толщину внутренних стенок принимают меньше толщины наружной стенки
.
Неравномерное остывание наружных стенок отливки приводит к возникновению термических напряжений и образованию усадочных раковин и трещин. На рис. 3 показана деформация неравностенной отливки, при остывании которой затвердевший раньше металл тонкой стенки будет мешать свободной усадке со стороны утолщенной стенки. В результате в отливке возникают изгибающие напряжения, причем, если эти напряжения превысят предел прочности, произойдет разрушение отливки во время охлаждения.
|
|
При конструировании оливок желательно назначать наименьшую толщину стенок, определяемую условиями прочности. Это необходимо для получения хорошей структуры металла, и его экономии.
Для уменьшения веса литых аппаратов и увеличения их прочности и жесткости следует не утолщать стенки, а применять ребристые и коробчатые конструкции (рис. 4). Ребристые конструкции лучше заливаются и условия их охлаждения более благоприятны. Коробчатые конструкции более жестки, имеют плавные и обтекаемые формы. Чугунные конструкции рекомендуется выполнять коробчатыми, а стальные – ребристыми.
При конструировании химической аппаратуры не всегда удается выдерживать принцип равностенности. Если части аппарата находятся под разными нагрузками, то согласно принципу равнопрочности, должны иметь стенки разной толщины. Поэтому при конструировании литых изделий необходимо стремиться к тому, чтобы разница в толщине сопрягаемых стенок была наименьшей, сопряжение – плавным. (рис. 5, 6).
|
|
Нежелательно, чтобы отношение толщин сопрягаемых стенок превышало 2.
.
Сопряжение стенок разной толщины осуществляется с помощью клиновидного перехода с соотношением
,
с помощью углового перехода с радиусом
или комбинацией этих двух способов (рис. 7).
Выбор радиуса перехода обоснован тем, что с одной стороны, при малых r в местах сопряжения концентрируются повышенные напряжения, с другой стороны, при больших r возникает вероятность образования усадочных раковин. Радиусы переходов регламентированы ГОСТами, например, для отливок из СЧ – ГОСТ 1412-86.
Вдоль границ сопряжения массивных частей с более тонкими частями рекомендуется размещать ребра (рис. 8). Они улучшают теплоотвод от массивной части и способствуют более равномерному распределению нагрузки.
Вогнутая форма ребер (рис. 8 а) более благоприятна с точки зрения распределения напряжений. Ребра прямолинейной формы (рис. 8 б) более дешевые. Доводить ребра до края не рекомендуется (рис. 8 в).
Толщина наружных ребер по отношению к минимальной толщине сопрягаемой стенки отливки
|
|
,
высота ребра .
Конструируя литые детали с ребрами необходимо учитывать, что чугуны хорошо работают на сжатие и плохо на изгиб и растяжение. Поэтому располагать ребра следует так, чтобы они находились со стороны сжатых волокон (рис. 9 а, б).
Для уменьшения скопления металла, иногда напротив ребра в стенке делается вмятина (рис. 10).
Крестообразное сопряжение ребер менее благоприятны, чем «Т» – образное или «V» – образное. Если крестообразное расположение ребер необходимо, то лучше соединить их с помощью дополнительного кольцевого ребра (рис. 11).
Плавность сопряжения проверяется методом вписанных окружностей (рис. 12). Отношение диаметров соседних окружностей не должно превышать . Чем меньше это отношение, тем качественнее отливка.
Для уменьшения напряжений и скопления металла при отливке ребер внутри аппаратов, рекомендуется в месте соединения трех стенок в каждом ребре оставлять отверстие (рис. 13).
Получать отверстия при литье рекомендуется только при диаметрах отверстия > 50 мм. Отверстия меньшего диаметра выгоднее сверлить в готовой отливке. Край отверстия, для компенсации ослабления, укрепляют литым бортом (рис. 14). Причем наружный борт (рис. 14 а) более удобен, чем внутренний (рис. 14 б) или двухсторонний (рис. 14 в) борт, потому что последние две конструкции затрудняют формование.
Прямоугольные отверстия, например фонарные отверстия в станинах компрессоров (рис. 15), должны иметь достаточно большой радиус скруглений углов и усилены бортами. Слишком маленький радиус закруглений вызывает концентрацию напряжений, особенно при знакопеременных нагрузках, характерных для поршневых компрессоров.
Для удешевления литья и уменьшения брака необходимо стремиться к максимальной простоте форм отливаемой детали, хотя литьем можно получить детали сложных конфигураций. Например, изготовление детали с двумя радиусами закругления (рис. 16 а) проще, чем детали с четырьмя радиусами кривизны (рис. 16. б).
Большие плоские поверхности неблагоприятны для отливки, их лучше выполнять с небольшими ребрами или углублениями. При конструировании литых круглых днищ следует избегать плоских отливок, а выполнять их в виде конуса с большим центральным углом (рис. 17).
Литая деталь должна иметь очертания, обеспечивающие беспрепятственное удаление ее из формы (рис. 18, 19). Нежелательно внутри отливки предусматривать ребра, перегородки, выступы, подрезки, затрудняющих формовку и мешающих удалению детали из формы.
Для облегчения удаления детали из формы, все поверхности, перпендикулярные к плоскости разъема, необходимо делать с уклоном (рис. 20).
В заключение раздела о конструировании литой аппаратуры, приведем несколько общих выводов.
При конструировании литой аппаратуры необходимо учитывать себестоимость отливки. Выгоднее применять по возможности самый дешевый материал – серый чугун. Без необходимости не следует применять более дорогое стальное литье.
При конструировании литой аппаратуры необходимо добиваться наиболее простых очертаний, плавности переходов и максимального приближения к равностенности.
Следует также учитывать, что отливки, в результате деформирования модели, никогда в точности не соответствуют чертежу. Допускаемые отклонения размеров отливок регламентированы ГОСТ 1855-86. На чертежах необходимо отмечать базовые поверхности, относительно которых будет обрабатываться отливка или собираться с другими деталями.
Спорным является вопрос, что является предпочтительным, изготовление крупных и сложных отливок, или разделение их на несколько мелких и простых, собирая их после отливки в узлы. В результате такого дробления улучшается качество литья, уменьшается вероятность брака, можно уменьшить толщину стенок некоторых частей. При этом несколько возрастает стоимость обработки после литья и сборки.
Дата добавления: 2018-09-23; просмотров: 445; Мы поможем в написании вашей работы! |
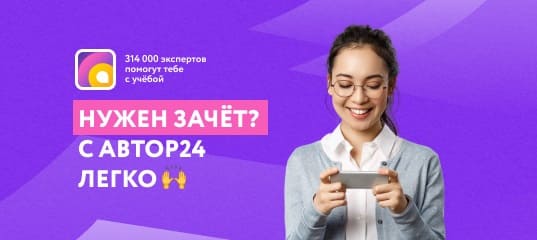
Мы поможем в написании ваших работ!