РТК на основе металлорежущих станков.
РТК металлообработки применяются для следующих направлений:
1) Выполнение вспомогательных операций, таких как смена обрабатываемых деталей, инструмента, оснастки.
2) Выполнение контрольно-измерительных операций над обрабатываемой деталью.
Контрольно-измерительные операции могут выполняться как во время технологических операций, так и в технологических паузах.
Для обрабатываемой детали -линейные размеры, шероховатость, температуру.
Различают системы активного и пассивного контроля. Системы активного контроля осуществляют замеры во время обработки детали, что не приводит к увеличению технологического времени. Такие системы имеют непосредственную связь с системами числового программного управления технологического оборудования. Однако такие системы являются более дорогими, т.к должны обладать помехоустойчивостью, надежностью и т.д
Системы пассивного контроля осуществляют измерения после окончания процесса обработки. Измерительная система активных либо пассивных систем контроля может быть с прямым либо с косвенным измерением параметров.
РТК кузнечно-штамповочного производства.
В кузнечно-штамповочном производстве используется около 45% промышленных роботов.
В кузнечно-штамповочном производстве промышленные роботы применяются на разгрузочно-загрузочных операциях.
В отличии от механообработки кузнечно-штамповочное производство требует большее быстродействии от промышленных роботов, что связано с коротки циклом обработки, цикл от единиц секунд.
|
|
M1, M2 – магазины (накопители)
С - стол
ВД – видео датчик
УПО – устройство предварительной обработки видеоданных
АПР – адаптивный промышленный робот
ЦПР – цикловой промышленный робот
УП – устройство подсветки
СТЗ – система технического зрения
В общем случае заготовки подаются в неориентированном виде, что затрудняет процесс загрузки и выгрузки. Для решения данной проблемы могут применяться специальные устройства – ориентаторы, которые оснащаются системой технического зрения СТЗ, состоящая из видео датчика и устройства предварительной обработки сигнала позволяющая идентифицировать объект и определить его положение в пространстве.
В следствие этого ЭВМ осуществляет сопоставление текущего положения объекта с заданным и формирует требуемое управляемое воздействие на исполнительные механизмы промышленного робота, который ориентирует заготовку или объект, который ориентирует заготовку или объект, после ориентации объекта его захват и перемещение к технологическому оборудованию возможно с помощью стандартных цикловых промышленных роботов, который для повышения быстродействия могут снабжаться 2-мя и более захватными устройствами.
|
|
44.РТК сборочного производства. На сборочном производстве в машиностроении применяется до 20% промышленных роботов, а в приборостроении 50-60% от общего числа.
Основными требованиями предъявляемыми к промышленным роботам являются:
1)высокая точность позиционирования 0,05 мм-0,001 мм
2)высокое быстродействие ϑ ≥1 м/с
3)большое число степеней подвижности n>6
4)захватные устройства должны быть достаточной грузоподъемности для манипулирования деталями различной массы.
m=1-20 кг – 40%
m< 1 кг -50%
m> 20 кг – 10%
5)универсальность захватных устройств
6)система управления промышленных роботов должна обеспечивать быструю и частую переналадку
Для обеспечения функционирования системы сборки необходимо наличие следующих подсистем:
1)автоматизированная транспортно-складская система – система взаимосвязанных транспортных и складских устройств, предназначенных для укладки, хранения, временного накопления и доставки предметов труда и технологической оснастки.
2) автоматизированная система инструментального обеспечения – система взаимосвязанных элементов предназначенных для подготовки инструмента, его накопления и транспортировки к месту сборки.
|
|
3)автоматизированного контроля – система включающая в себя элементы предназначенные для контроля качества выполненных сборочных работ.
4)автоматизированная система управления.
Сборочный процесс можно разделить на несколько этапов:
1этап)ориентация и подача деталей к месту сборки
2этап)сопряжение собираемых деталей. Данный этап является наиболее сложным и трудоемким.
3этап) Закрепление соединения путем завинчивания, сварки, либо пресса.
4этап) Контроль качества выполненных работ.
Дата добавления: 2018-08-06; просмотров: 433; Мы поможем в написании вашей работы! |
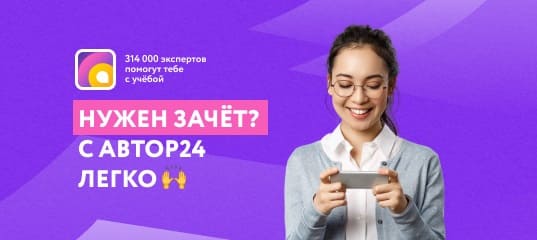
Мы поможем в написании ваших работ!