Особенности подготовки под сварку поверхностей алюминиевых и титановых сплавов.
При сварке деталей из алюминия и его сплавов предъявляются особые требования к подготовке деталей, материалов и оборудования. Среди сварщиков, занимающихся изготовлением конструкций из алюминия, бытует выражение: "Хорошо подготовлено — наполовину сварено".
Имеется ряд рекомендаций по подготовке поверхностей алюминиевых деталей и проволоки, которые отличаются от рекомендаций для стали. Например, не допускается зачищать поверхность под сварку абразивами, наждачной бумагой, дробеструйной обработкой и т. п. Помимо механической обработки кромок свариваемых деталей для придания им рациональной формы, облегчающей выполнение соединений, подготовка деталей под сварку и подготовка проволоки к сварке включает очистку их поверхности от загрязнений и оксидов.
Имеется большое количество рецептов подготовки поверхности под дуговую (лучевую); под точечную (шовную) сварку; для получения клеесварных соединений. Однако различия в подготовке невелики.
1. Прежде всего их поверхность очищают от консервирующей смазки и загрязнений, протирая ее ветошью, смоченной в бензине, уайт-спирите или других органических растворителях. В серийном производстве свариваемые детали обычно обезжиривают в негорячем водном растворе, содержащем 10 г/л NaOH, 40—50 г/л тринатрийфосфата Na3PO4 - 12Н2O, 5 г/л натриевого жидкого стекла Na2SiO3. Продолжительность процесса обезжиривания зависит от степени загрязненности поверхности металла и от температуры. При температуре раствора 60—70°С длительность обезжиривания обычно не превышает 3—5 мин.
|
|
2. После обезжиривания детали или проволоку погружают в 5%-ный водный раствор щелочи (NaOH или КОН), нагретый до 60—70°С. В результате взаимодействия со щелочью оксидная пленка стравливается с поверхности в течение 2—3 мин. После этого остатки щелочи и продукты реакции смывают с поверхности деталей сначала горячей, а затем холодной водой, одновременно протирая их волосяными щетками.
3. Сразу же после промывки детали пассивируют в 20%-ной азотной кислоте (HNO3), нагретой до 60—70°С. За 5—7 мин пребывания в растворе поверхность деталей покрывается новым, более плотным слоем оксида алюминия. Извлеченные из азотной кислоты детали промывают в холодной
Технические требования, предъявляемые к сборке конструкций под сварку и НТД, в соответствии с которыми определяются эти требования. Фиксация деталей при сборке.
Технические условия на сборку
На всех, поступающих на монтажную площадку деталях, до начала сборки, мастером (или другим ответственным лицом) должно бать проверено наличие клейм, маркировки, а также сертификатов завода-изготовтиеля, подтверждающих соответствие деталей их назначению. При отсутствии клейм, маркировки или сертификатов детали к дальнейшей обработке не допускаются. При подготовке стыковых соединений под сварку необходимо проверить их соответствие чертежам и требованиям НТД.
|
|
Непосредственно перед сборкой изготовленные под сварку кромки и прилегающие к ним участки поверхностей деталей должны быть зачищены до металлического блеска и обезжирены, а так же необходимо проконтролировать зазор сварного соединения в зависимости от толщины металла и в соответствии с ГОСТ. Ширина зачищенных участков, считая от кромки разделки, должна быть не менее 20 мм. При сборке стыка необходимо предусмотреть возможность свободной усадки металла шва в процессе сварки; не допускается выполнять сборку стыка с натягом. Технические условия на сварку
Сварку конструкций должны производить сварщики, прошедшие теоретическую и практическую подготовку и имеющие удостоверения, устанавливающие их квалификацию и характер работ, к которым они допущены.Производить ее можно только после приемки ОТК сборки под сварку. Поверхности, подлежащие сварке, должны быть тщательно очищены от ржавчины, грязи, масла, влаги. Способ сварки зависит от условий производства, технологических и технико-экономических данных.
|
|
Сварка конструкций должна производиться в соответствии с технологическим процессом, устанавливающим последовательность сборочно-сварочных работ, способ сварки, сварочную аппаратуру, источник питания, приспособления и вспомогательное оборудование, сварочные материалы, порядок наложения сварных швов, режимы сварки и т.д.
ФИКСАЦИЯ
Любая машина состоит из отдельных частей, простейшей из которых является деталь, т.е. изделие изготовленное из однородного по наименованию и марке материала без применения сборочных операций. Изделие- любой предмет или набор предметов производства, изготовляемых на предприятии.
Изделие, составные части которого подлежат соединению между собой на предприятии-изготовителе посредством сборочных операций \свинчиванием, сочленением, клепкой, сваркой, пайкой, опрессовкой, развальцовкой, склеиванием и т.д. \, называется сборочной единицей. Комплекс - несколько специфицированных изделий, служащих для выполнения взаимосвязанных эксплуатационных основных или вспомогательных функций, но не соединенных между собой предприятием-изготовителем \ например, поточная линия станков, корабль и т.д. \. Комплект - не соединенные на предприятии-изготовителе несколько изделий, которые предназначены для совместной эксплуатации при выполнении вспомогательных функций, например, комплект запасных частей, комплект тары и т.д.
|
|
34.Основвные схемы сборки: сборка по разметке, сборка по сборочным отверстиям, сборка при помощи накладных шаблонов, сборка с применением универсальных и специализированных приспособлений. Фиксация деталей при сборке. (Слышь, про фиксацию в 33 вопросе найдешь)
Сборка по разметке(Рис.7.) – процесс, при котором взаимное положение деталей, входящих в узел, определяют непосредственно измерением расстояний между ними и по рискам, нанесенным на детали при разметке.
Сборка по разметке производится при помощи универсальных слесарных инструментов и приспособлений (струбцин, чертилки, керна, метра, циркуля, ручных и настольных тисков и т.п.). Детали, поступившие на сборку, размечают вручную или фотоконтактным методом (по специальным шаблонам из винипроза). Процесс сборки по разметке включает много переходов, связанных с разметкой центров отверстий в каждой детали, кернением положения центров, измерением расстояния между деталями, установкой и снятием струбцин и т.д. Установка деталей в сборочное положение по разметке – операция трудоемкая и длительная. Взаимозаменяемость при сборке с разметкой практически невозможна.
Рис. 7. Лючок и сборка его по разметке
1 – петля; 2 – диск; 3 – замок; 4 - струбцина
Метод сборки по разметке характеризуется, по сравнению со сборкой по сборочным отверстиям, более высокой производительностью, низкой точностью и взаимозаменяемостью подсборок. При применении этого метода нет необходимости изготовлять комплект шаблонов для увязки сборочных отверстий в деталях. Небольшие затраты на оснастку и сравнительно малый цикл подготовки производства позволяют применять указанный метод в опытном и мелкосерийном производствах для сборки плоских узлов и цилиндрических
Сборка по сборочным отверстиям (СО)(Рис.6.) – процесс, при котором сборка осуществляется путем совмещения взаимосогласованных отверстий, выполненных при изготовлении сопрягаемых деталей. В эти отверстия на период сборки вставляются фиксаторы, технологические болты или технологические заклепки с последующим окончательным соединением деталей.
Рис.6. Образование обводов агрегата при сборке с базированием по СО
1 и 3 – профили; 2 – стенка; 4 – фиксаторы; 5 - обшивка
Сборочные отверстия располагаются в местах установки заклепок или болтов. Места расположения СО наносят на чертеж или указывают в специальных схемах. Для установки детали в сборочное положение должно быть не менее двух СО.
В соответствии с технологическим процессом сборки-клепки на схематических чертежах, помимо СО, наносят места расположения направляющих отверстий (НО) и установочно-базовых отверстий (УБО). В соответствии со схемой расположения СО, НО, УБО на эскизах узлов, панелей им отсеков составляют схемы расположения СО, НО, УБО на деталях. При сборке с образованием обвода агрегата размер внешнего обвода
Универсальные приспособления (УП) применяют для установки и закрепления заготовок разных по форме и габаритным размерам, обрабатываемых на различных металлорежущих станках, в единичном и мелкосерийном производствах. К ним относятся различные патроны, машинные тиски, делительные головки и т.д.
Универсальные безналадочные приспособления (УБП) - используют для закрепления заготовок широкой номенклатуры и различной конфигурации. К ним относятся: универсальные патроны с неразъемными кулачками, универсальные фрезерные и слесарные тиски.
Универсально-наладочные приспособления (УНП) применяют для установки и закрепления определенной группы схожих по форме заготовок деталей, обрабатываемых на токарных, фрезерных, сверлильных и других станках. Универсально-наладочные приспособления состоят из двух частей: универсальной (постоянной) и наладочной (сменной). Универсальная часть включает в себя корпус, силовой привод и базовые элементы для установки сменных наладок. Наладочная часть состоит из сменных наладок, изготавливаемых в соответствии с формой и габаритными размерами обрабатываемых деталей.
Специализированные безналадочные приспособления (СБП) - используют дня закрепления заготовок, близких по конструктивно-технологическим признакам, с одинаковыми базовыми поверхностями, требующих одинаковой обработки. При осуществлении однотипных операций на этих приспособлениях необходимо осуществлять регулировку отдельных элементов. К таким приспособлениям относятся: приспособления для групповой обработки деталей типа валиков, втулок, фланцев, дисков, кронштейнов, корпусных деталей и т.п.
Специализированные наладочные приспособления (СНП) - состоят из двух частей. Первая часть - базовый агрегат и, вторая часть - специальная сменная наладка. Базовый агрегат, как правило, несет основную базовую поверхность, на которую устанавливают специальные сменные наладки под обрабатываемые заготовки. Во многих случаях базовый агрегат имеет одну или несколько вспомогательных базовых поверхностей для установки на них специальных сменных наладок, предназначенных для направления режущего инструмента, механизма зажима заготовки и других деталей и сборочных единиц.
Универсально-сборные приспособления (УСП) - собирают из нормализованных деталей и узлов, входящих в комплект УСП. Этот комплект состоит из базовых, корпусных, установочных, направляющих, прижимных, крепежных и других деталей и нормализованных узлов, различных по конструкциям и назначению.
Изготовление приспособления из деталей УСП включает в себя:
- Разработку схемы сборки приспособления в соответствии с видом технологической операции обработки детали и станка;
- Сборку приспособления из нормализованных деталей;
- Использование собранного приспособления для изготовления детали на соответствующем станке;
- Разборку приспособления;
- Раскладку деталей УСП для хранения.
Применение системы УСП в 2-3 раза сокращает сроки технологической подготовки производства к выпуску нового изделия. Затраты на восстановление комплекта деталей УСП за год составляют 3,5% от всей себестоимости комплекта.
Основой комплекта являются гидравлические блоки. Конструктивно они выполнены в виде прямоугольных плит УСП, в корпус которых встроены гидроцилиндры двустороннего действия. Компоновки механизированных приспособлений, собранные на их базе, обладают важным достоинством по сравнению с компоновками, механизация которых осуществляется с помощью отдельно стоящих гидрофицированныхприжимов.Срок использования комплекта деталей и узлов УСП примерно 25 лет. УСП применяют в единичном, мелкосерийном и частично в среднесерийных типах производства.
Последовательность сборки и сварки конструкций: последовательная сборка и сварка, полная сборка с последующей сваркой, параллельно-последовательная сборка и сварка. Фиксация деталей при сборке.(Слышь, про фиксацию в 33 вопросе найдешь)
Последовательная схема (рисунок 33, а) целесообразна при сборке конструкций, не расчлененных на сборочные узлы, когда сварка полностью собранной конструкции невозможна, а другими схемами нельзя обеспечить необходимую точность из-за особенностей конструкции, например, из-за недостаточной ее жесткости. Ее выполняют последовательным наращиванием отдельных элементов. Требуемая точность может быть достигнута применением промежуточных операций правки. Сборка и сварка при такой организации процесса менее производительны, так как при их последовательном выполнении ограничивается фронт работ и уменьшается число работающих, Ц увеличивается.
Схему полной сборки конструкции с последующей сваркой (рисунок 33, б) обычно используют для сравнительно простых изделий или изделий средней сложности, состоящих из небольшого числа деталей с легкодоступными для выполнения соединениями. По этой схеме конструкцию сначала полностью собирают, закрепляя элементы струбцинами, фиксаторами, прихваточнымн соединениями и т. п., после чего собранную конструкцию передают на сварочный участок для выполнения сварки всех соединений. Фронт работ при этом расширяется, Ц уменьшается. Схема используется при различных типах производства. Технологический процесс сборки и сварки в зависимости от программы выпуска, массы и конфигурации изделий может быть механизирован или полностью автоматизирован.
Параллельно-последовательную схему (рисунок 33, в) используют при изготовлении сложных конструкций, расчлененных на укрупненные сборочные единицы. Сначала на параллельных технологических линиях собирают и сваривают укрупненные сборочные единицы. Затем из готовых узлов собирают и сваривают конструкции в целом. При такой схеме число одновременно занятых рабочих или фронт сборочных работ значительно больше, поэтому Ц минимален. Практика показывает, что такая схема позволяет сократить цикл в 3—4 раза по сравнению с последовательной схемой. Это подтверждает большие преимущества расчлененных конструкций.
Дата добавления: 2018-08-06; просмотров: 554; Мы поможем в написании вашей работы! |
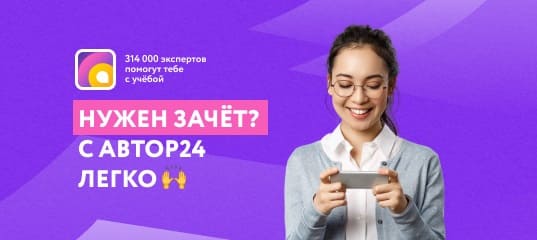
Мы поможем в написании ваших работ!